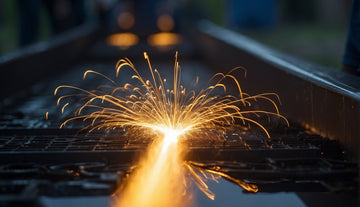
Curious about submerged arc welding? It's a method that's all about joining big pieces of metal really well and without any mess. Imagine welding with a special material called flux covering the work area—that's what keeps everything clean and strong.
This method is super useful for big projects like ships, trains, and huge pipes. It's a clean, reliable way to weld that pros use when they need to get a lot done without any fuss. Want to see how submerged arc welding can tackle big welding jobs? Keep reading, and we'll show you how it's done.
Fundamentals of Submerged Arc Welding
Submerged arc welding (SAW) is a fast and efficient method that produces deep and neat welds. It uses a special covering called flux to make sure the welding arc and the melted metal stay clean and stable during the process.
Submerged arc welding is a process in which the heat required to fuse the metal is generated by an electric arc between the workpiece and a consumable electrode.
The arc is submerged beneath a layer of flux, which helps to stabilize the arc, refine the weld metal chemistry, and protect the molten pool from contamination.
Historical Development
Introduced in the 1930s, submerged arc welding was developed to address the need for a method that could facilitate large-scale production and deliver consistent, high-quality welds.
This technique revolutionized the welding industry with its capacity to handle substantial weldments and high deposition rates.
Submerged Arc Welding Versus Other Arc Welding Processes
SAW differs from other arc welding processes by its use of a blanket of flux that shields the arc. This results in less spatter, no visible arc light, and minimal fume generation.
Compared to processes like MIG or TIG, sub arc welding is particularly suited for long, straight seams or heavy workpieces requiring thick joints.
Core Elements of the SAW Process
- Flux: A vital element that cleans the weld, shapes the profile, and prevents oxidation.
- Electrode: Continuous solid or cored wire fed into the weld pool.
- Arc: The heat source generated between the electrode and the metal.
- Electric Arc: Operates under the flux, making it invisible during welding.
In SAW, your control over these core elements influences the quality and efficiency of the welding process. Proper selection and handling are crucial for achieving optimal results.
Technical Insights Into Submerged Arc Welding
Explore the specifics of Submerged Arc Welding (SAW), where precision and understanding of the equipment, flux, mechanics, and operational settings play crucial roles in achieving quality welding outcomes.
Understanding the SAW Equipment
Your successful engagement with sub arc welding begins with comprehending the necessary equipment.
A typical SAW setup includes a power source, flux hopper, wire feed mechanism, and electrodes.
The power source must be capable of providing a constant current to produce the required heat for welding.
Electrodes are typically fed from a spool, and their diameters are chosen based on the specific welding application.
The Role of Flux in SAW
Flux controls the welding atmosphere and stabilizes the arc.
When you engage in SAW, the flux is delivered from the flux hopper and covers the weld area to prevent contamination from the surrounding environment.
In addition to protecting the weld pool, fluxes can also alter the chemical composition of the weld by transferring alloying elements.
Mechanics of the Welding Process
SAW is known for a high-deposition rate welding process involving the formation of an electric arc between the continuously-fed electrode and the workpiece.
As you operate, the wire feed mechanism efficiently delivers electrodes into the weld zone. This process ensures consistent quality by automating the feed rate, which is critical for maintaining a stable arc and smooth weld bead.
The Significance of Welding Current and Travel Speed
Two highly influential factors on the outcome of your SAW are the welding current and travel speed.
Adjusting the current modifies the heat input, affecting the penetration and bead profile. Travel speed, on the other hand, influences the weld bead's width and reinforcement.
A balance between these settings is paramount for the desired deposition rate and weld quality.
Materials and Applications of Sub Arc Welding
In the domain of sub arc welding (SAW), your choice of material and its intended application are crucial for the success of the welding process. Understanding their compatibility and the scope of their applications ensures optimal performance and longevity of the welded structures.
Metals Compatible with SAW
SAW is suited for a range of metals, where the productivity and efficiency of the process can be maximized. Notably, steels and stainless steels are frequently used materials. They accommodate a smooth welding experience due to their properties. Specifically:
- Carbon steels: Ideal for structural purposes, given their strength and versatility.
- Low alloy steels: Preferred for projects requiring higher strength and toughness.
- Stainless steels: Used for applications demanding resistance to corrosion.
Additionally, nickel-based alloys are also compatible with SAW, offering high performance in extreme conditions.
Also read: What Is Nickel Welding? Understanding the Process and Applications
Exploring the Spectrum of SAW Applications
Your projects may span various industries, and SAW is remarkably versatile in its applications. Here are a few specific uses:
- Pressure vessels: SAW’s capability to create strong, resilient joints makes it ideal for vessels that hold pressurized substances.
- Boilers and pipes: For these components, SAW provides durable welds that can withstand the demands of temperature and pressure fluctuation.
- Shipbuilding: The process is a staple in the shipbuilding industry due to its efficiency and the large-scale workpieces involved.
- Structural applications: SAW is often the preferred method for constructing large steel frameworks, supporting the integrity of the structure.
Performance and Characteristics of Sub Arc Welding
Submerged arc welding (SAW), commonly referred to as sub arc welding, is a highly efficient and controlled process. Below you’ll find a thorough investigation into its performance and how it behaves under various operational parameters.
Assessing the Strength and Thickness Parameters
In sub arc welding, you’ll find that deposition rates are exceptionally high due to the covered arc and continuous feed of filler material.
This allows for welding thick-section workpieces with ease. The process is capable of joining materials with a thickness typically ranging from about 1/8 inch (3mm) to several inches.
Advantages of Employing SAW
The benefits of using sub arc welding are numerous. The process is clean with a minimal amount of spatter, resulting in a superior finish.
Additionally, the blanket of flux not only produces slag that protects the molten weld from contaminants but also minimizes fumes, enhancing the safety and cleanliness of your working environment.
- High-quality welds
- Minimal spatter and fumes
- Suitable for thick materials
- Enhanced safety due to reduced fume emission
Recognizing the Limitations of SAW
Despite its advantages, sub arc welding also presents some constraints. Certain geometries may be challenging to weld, and the process is typically less versatile than others.
Overhead or vertical welding processes can be particularly complex with SAW because of the granular flux.
- Limited to flat or horizontal-fillet welds
- Complex slag removal process
- Reduced versatility for varying geometries
Cost-Effectiveness of SAW
Sub arc welding is economically advantageous, especially when dealing with large-scale production or thick materials.
Its automated nature leads to a decrease in labor costs and an increase in throughput. The high deposition rate of SAW means faster welding speed and therefore less time spent per weld.
- Reduced labor costs
- Increased welding speed
- Economical for large-scale projects
Ease of Learning and Mastering SAW
Learning sub arc welding is straightforward, given its automated process controls which streamline the welding operation.
You do not need to possess high manual dexterity as required with some other welding processes, making the transition into SAW easier for operators.
- Lesser manual skill required
- Automated control for consistent results
- Training focused on equipment setup and operation
Submerged Arc Welding SAW vs. Shielded Metal Arc Welding (SMAW)
Submerged Arc Welding (SAW) and Shielded Metal Arc Welding (SMAW) are distinct processes within the arc welding category.
SAW employs a continuously fed consumable electrode and utilizes a blanket of fusible granular flux to protect the weld zone from atmospheric contamination. This results in a smoother and more controlled weld that is commonly used for thicker materials.
- Operations: SAW is often automated or mechanized whereas SMAW is typically manual.
- Weld Appearance: SAW tends to provide a cleaner weld with less spatter compared to SMAW.
SMAW, also referred to as stick welding, involves a manual technique utilizing a consumable electrode coated in flux to lay the weld.
This process is versatile and can be used in various environments, but it yields a slower deposition rate than SAW.
- Versatility: SMAW can be performed in diverse conditions including outdoors and on rusty or dirty metals.
- Equipment Portability: SMAW equipment is more portable compared to the heavier and more complex setups required for SAW.
Applicability of SAW for Underwater Operations
Submerged arc welding is generally not suited for underwater welding applications due to the nature of its setup which requires a granular flux to cover the weld area.
Sub arc welding relies on a dry and controlled environment to maintain the integrity of the flux and ensure a high-quality weld.
- Environment: The necessity for a dry work area makes SAW impractical for underwater use.
- Control: The flux used in SAW must remain dry; exposure to water can contaminate the weld pool leading to poor quality welds.
In contrast, specialized underwater welding techniques are applied for underwater operations which deal with the unique challenges posed by the marine environment.
Conclusion
Submerged arc welding (SAW) stands out as a stealthy and sturdy contender in the world of welding, delivering top-notch welds beneath a protective flux layer. A key player in heavy industrial tasks, this method promises strong, clean, and reliable welds for large, thick materials.
If you're drawn to the robust quality that SAW provides, consider looking into Arc Captain's selection of welding products. Engineered for performance and durability,
Take the next step in your welding journey and embrace the strength Arc Captain brings to every weld. Check out Arc Captain's products and ensure your next project stands the test of time.
Frequently Asked Questions
What is the minimum thickness for sub arc welding?
The minimum thickness for submerged arc welding typically starts at around 1/8 inch (3 mm). This process is best suited for thicker materials because it offers deep penetration and a high deposition rate. While SAW can be adjusted for slightly thinner materials, other welding methods might be more effective and practical for sheets under 1/8 inch.
How fast is submerged arc welding?
Submerged arc welding is one of the fastest welding processes available. It's known for its high deposition rates, allowing it to lay down more weld metal in a given time than most other welding methods.
The actual speed will depend on the specifics of the project, including material thickness and the machine's capabilities, but SAW is generally chosen for projects where speed and productivity are crucial considerations.
Does submerged arc welding require gas?
Submerged arc welding does not require an external shielding gas because the process itself uses a granular flux to protect the weld pool.
The flux covers the arc and molten metal, preventing contamination from the atmosphere. This characteristic of SAW makes it different from welding processes that do rely on shielding gases, like MIG or TIG welding.
What is the difference between MMA and arc welding?
MMA, or Manual Metal Arc welding, which is often called stick welding, is actually a type of arc welding. Arc welding is a broad term that encompasses a variety of welding processes, including MMA, TIG (Tungsten Inert Gas), and MIG (Metal Inert Gas) welding, along with Submerged Arc Welding (SAW).
MMA specifically uses a consumable electrode coated in flux to lay the weld, and it can be performed in diverse conditions, including outdoors and on rusty or dirty metals. Arc welding refers to the general principle of using an electric arc to generate heat and melt metals to be joined.