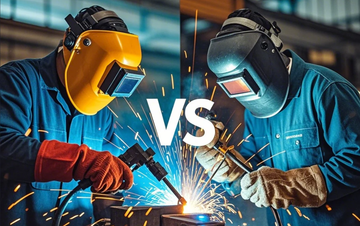
Arc welding and laser welding are two important methods in the welding field. This article will discuss their working principles, advantages and disadvantages, and application scenarios. By exploring these three aspects, you will gain a comprehensive understanding of the differences between arc welding and laser welding, providing valuable insights for your purchasing decisions.
I. Working Principles of Arc Welding and Laser Welding
- Arc Welding: Arc welding is a widely used method for joining metals by generating heat from an electric arc between an electrode and the base material, melting them to form a strong bond upon cooling. Electrodes can be consumable, adding filler material, or non-consumable. Shielded Metal Arc Welding (SMAW) uses inert gases to protect the weld from contamination, while Gas Tungsten Arc Welding (GTAW) employs semi-inert gases. Its adaptability to various equipment and settings makes arc welding a versatile choice across many industries.
- Laser Welding: Laser welding employs a focused laser beam to precisely join materials by quickly melting a small area to form a weld. This contactless process minimizes material distortion and enhances accuracy, making it ideal for detailed welding tasks. Its key advantage is the ability to adjust the laser's intensity and duration, allowing it to work with various materials and handle intricate jobs efficiently.
II. Advantages and Disadvantages of Arc Welding and Laser Welding
Arc Welding’s Advantage:
- Cost-Effectiveness: Arc welding equipment is generally more affordable compared to other welding methods. This affordability extends to both the initial investment and the ongoing operating costs.
- Versatility: It can be used on a variety of metals and alloys, making it suitable for a wide range of applications in different industries.
- Portability: Arc welding equipment is often portable, allowing for welding tasks to be performed in various locations, including outdoors.
- Robust Welds: Arc welding is known for producing strong and durable welds, which is particularly important in heavy-duty applications like construction and shipbuilding.
Arc Welding’s Disadvantage:
- Safety Concerns: The process generates intense heat, sparks, and UV radiation, posing safety risks that require strict protective measures.
- Limited Precision: Compared to methods like laser welding, arc welding is less precise, making it less suitable for applications requiring high accuracy.
- Environmental Impact: Arc welding can produce fumes and gases that may be harmful if not properly ventilated, raising concerns about its environmental and health impacts.
Laser Welding’s Advantage:
- High Precision: Laser welding offers superior precision, especially beneficial for delicate and intricate welding tasks.
- Speed: The process is typically faster than traditional welding methods, increasing productivity.
- Low Heat Input: Laser welding minimizes the heat-affected zone, reducing material distortion and allowing for the welding of heat-sensitive components.
- Versatility: It can be used on a wide range of materials, including metals, plastics, and composites.
- Automated Operations: Laser welding can be easily automated, enhancing consistency and reducing labor costs.
Laser Welding’s Disadvantage:
- High Initial Cost: The equipment for laser welding is generally more expensive than traditional welding setups.
- Technical Expertise Required: Operating and maintaining laser welding equipment requires specialized knowledge and training.
- Limited Thickness Range: It is less effective on very thick materials compared to methods like arc welding.
- Safety Concerns: The intense laser beam can be hazardous, requiring strict safety protocols and specialized equipment.
- Limited Joint Accessibility: Due to the nature of the laser beam, welding certain joint configurations can be challenging.
III. The Application Scenarios of Arc Welding and Laser Welding
Arc Welding’s Application:
To fully appreciate the contrasts with arc welding, it is essential to delve into the realm of laser welding and its unique attributes.
- Construction: Used in building structures and bridges.
- Automotive: Essential for assembling vehicle frames and body parts.
- Industrial Repair and Fabrication: Ideal for repairing and creating metal equipment and pipelines.
-
Metal DIY Project: Widely used for constructing metal DIY projects for hobbyists.
Its adaptability to different metals and alloys makes arc welding a preferred choice in many industrial applications.
Laser Welding’s Application:
Laser welding’s precision and versatility allow it to be employed in a variety of industries, some of which include:
- Electronics and Microfabrication: Ideal for joining small components in electronic devices and micro-assemblies.
- Automotive Industry: Used for high-precision welding of engine components and intricate automobile parts.
- Aerospace Industry: Crucial for fabricating and repairing critical aerospace components with high precision.
- Medical Equipment Manufacturing: Applied in producing surgical tools and medical devices requiring exact welds.
The non-contact nature and precision of laser welding make it an indispensable tool in fields requiring detailed and precise welding work.
Conclusion:
In summary, both arc welding and laser welding have unique strengths and applications. Arc welding is cost-effective and versatile for heavy-duty tasks, while laser welding offers precision and speed for high-tech projects.
The choice between them depends on factors like budget, material type, and project complexity. The key is to align the welding method with your specific project needs and resources, ensuring optimal quality and efficiency.
Compared with Laser Welding, Arc Welding is relatively new in the welding field. In the Arc Welding Field, there are many reliable brands, like Lincoln, Miller and Arccaptain. These brands, especially Arccaptain, continuously combine technology with welding, introducing high-quality welding machines like the MIG200, MIG205Pro, and MIG205MP, empowering numerous welding enthusiasts.
- 4043 vs. 5356,
- Aluminum,
- ARC welding machine,
- aws welding certification,
- Braze Brass,
- contact tips,
- Cool Welding Projects,
- deposition rate in welding,
- Electrode,
- Flux-Cored Weld,
- Fusion Welding,
- Globular Transfer Welding,
- guide,
- highest paying welding jobs,
- Interpass Temperature,
- inverter vs transformer welder,
- Laser Welding,
- mig welding machine,
- military grade aluminum,
- mma welding,
- multi-process welders