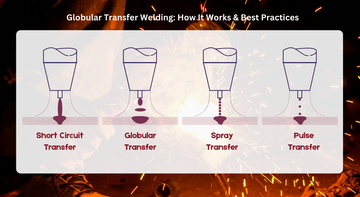
Globular transfer welding is a fascinating technique used in Gas Metal Arc Welding (GMAW), especially for thicker materials.
In this method, metal droplets form and move across the arc, creating strong welds.
It's an important part of MIG welding, but getting the best results depends on setting the right current and positioning the materials correctly.
Understanding how these metal droplets affect weld quality can help improve your skills and make your projects even better.
But how exactly does globular transfer welding work, and what are the best practices for success? Keep reading to learn more.
What Is Globular Transfer Welding?
Globular transfer welding is a process where molten metal droplets are moved from the electrode to the weld pool.
These droplets form large, irregular globules. This method commonly uses both MIG (Metal Inert Gas) and GMAW (Gas Metal Arc Welding).
Characteristics
-
Less Controlled: Compared to other methods, globular transfer is less controlled. The size and shape of the droplets can be irregular, leading to splatter. This makes it less ideal for precision work.
- Applications: While not commonly used for detailed tasks, globular transfer can be effective for heavy or thick materials. It may be chosen when high deposition rates are needed.
How Globular Transfer Welding Works
Globular transfer welding is a process that moves molten metal from the electrode to the workpiece in large, irregular droplets. Here’s a breakdown of how it works:
1. Voltage and Current Control
- Uses medium-to-high voltage and current settings.
- The high heat melts the electrode, forming large droplets of molten metal.
- These droplets are bigger than the electrode wire and transfer across the arc.
2. Metal Droplet Transfer
- The molten metal falls across the arc in an uneven pattern.
- Because the droplets are large and heavy, they drop due to gravity, leading to irregular weld deposition.
- This process results in high spatter, making the weld area messy.
3. Role of Shielding Gas
- 100% CO₂ is commonly used as it increases arc stability but also causes more spatter.
- CO₂-Argon mixtures help reduce spatter and improve control over the arc.
- The gas selection affects the droplet size, arc shape, and weld bead appearance.
4. Welding Position and Weld Pool Stability
- Best performed in a flat or horizontal position to control the weld pool.
- The unstable nature of globular transfer makes it difficult for overhead or vertical welding.
- A steady weld pool helps manage weld shape, penetration, and bead width.
5. Key Challenges and Solutions
- Excessive spatter – Can be reduced by adjusting voltage and using a CO₂-Argon mix.
- Irregular droplet transfer – Keeping a steady arc and proper gas flow helps.
- Undercutting risks – Controlling heat input prevents the weakening of the weld edges.
By understanding how globular transfer welding works, you can adjust settings, choose the right gas, and improve overall weld quality.
Applications of Globular Transfer Welding
1. Structural Fabrication
In large-scale projects, where you are working with thick steel structures, globular transfer welding is often used. The process is ideal in situations where the quality of spatter and bead appearance is not a primary concern.
2. Heavy-Duty Welding
For tasks involving thick materials, usually above 5 mm, you’ll find globular transfer particularly effective. The large molten droplets and high heat input are beneficial in welding these substantial materials.
3. Cost-Sensitive Projects
If cost efficiency is your primary goal, this method may be suitable. Although precision and aesthetic quality may be compromised, globular transfer offers a lower-cost option for creating strong joints.
However, globular transfer is rarely chosen for thin materials or precision welds. The large droplets and higher risk of spatter can harm thin materials and reduce the quality of precise welds.
The process is also less stable, which can lead to issues with controlling the arc and maintaining a clean finish.
Advantages and Disadvantages of Globular Transfer Welding
Globular transfer welding can be a viable option in some welding scenarios. It uses large drops of molten metal that transfer across the welding arc.
Understanding both its strengths and weaknesses can help you decide if it's right for your project.
Advantages
-
Cost-effective: You can save money by using 100% CO₂ shielding gas, which is cheaper than other gas mixtures.
-
High deposition rates: It's great for heavy-duty welding because of its ability to deposit a lot of material quickly. This makes it useful for projects where you need to cover large areas.
-
Simpler setup: Compared to other methods like spray or pulse transfer, globular transfer welding requires a simpler setup. This can make it more user-friendly, especially if you’re just starting out.
Disadvantages
-
Excessive spatter: One of the major downsides is that it creates a lot of spatter, leading to more cleanup and inefficiency. This can increase the time and effort you need after welding.
-
Limited control: It offers less control over the weld pool. This can make it harder to achieve precision, which is crucial in fine or detailed work.
-
Not suitable for thin materials: The high heat input can cause burn-through, making it unsuitable for thin metal welding.
- Poor aesthetics: Compared to other methods, the weld bead often looks less neat. This might not be suitable for projects where appearance is important.
Read more: What Is Weld Spatter?
Globular Transfer Welding vs. Short Circuit Transfer
Quick Overview:
Feature |
Globular Transfer |
Short Circuit Transfer |
How It Transfers Metal |
Large globules of molten metal fall into the weld pool |
Molten metal is deposited during repeated short circuits |
Speed |
Faster for depositing material on thick workpieces |
Slower but produces a cleaner weld finish |
Best for Material Thickness |
Works better for thicker materials |
Ideal for thin materials |
Precision & Control |
Less precise, can be messier with more spatter |
Offers better control and precision for detailed work |
Globular Transfer:
- Involves large droplets of metal.
- Operates at higher heat levels.
- Use for thicker materials where higher heat and spatter aren't issues.
Short Circuit Transfer:
- Electrode touches and creates a short circuit.
- More controlled and cleaner process.
- Lower deposition rates.
- Best for thin materials and when little spatter is desired.
Recommendations:
- Use globular transfer for projects needing high heat input and involving thicker materials.
- Opt for short circuit transfer in projects where cleanliness is crucial, and you're welding thin sections.
Understanding these differences helps you choose the right method for your welding project.
Globular Transfer Welding vs. Spray Transfer
When comparing globular transfer welding and spray transfer welding, it's important to look at their distinct features and applications. Below is a table that highlights the key differences:
Feature |
Globular Transfer |
Spray Transfer |
Metal Droplet Size |
Large droplets |
Small droplets |
Spatter |
More spatter |
Minimal spatter |
Shielding Gas |
Usually uses 100% CO₂ |
Requires at least 80% argon or helium |
Precision |
Less precise |
High precision |
Application |
Flat and horizontal positions |
Multiple positions |
Cost |
Lower cost |
Higher cost due to gas requirements |
Globular Transfer Welding
- Often used for welding carbon steel.
- Pros: Lower shielding gas cost and suitable for thicker materials.
- Recommended for less critical projects and when a higher level of spatter is not a concern.
Spray Transfer Welding
- Suitable for various metals and positions.
- Pros: Offers high precision with minimal spatter.
- Recommended for applications needing clean welds and greater control, despite higher gas costs.
These transfer modes each have their own strengths. Your choice depends on your specific project needs, budget, and desired weld quality.
Globular Transfer Welding vs. Pulsed Spray Transfer
Globular Transfer Welding involves large droplets of weld metal crossing the arc. This mode is generally straightforward but can create more spatter.
Pulsed Spray Transfer varies the current to mix spray and short-circuiting transfer, offering higher deposition with great control but needing advanced setup.
Feature |
Globular Transfer Welding |
Pulsed Spray Transfer |
Droplet Size |
Large, irregular droplets |
Small, consistent droplets |
Spatter |
High spatter levels |
Minimal spatter |
Equipment |
Basic equipment required |
Requires advanced pulsing equipment |
Deposition Rate |
Medium to high but less efficient due to spatter |
High deposition rate with better control |
Control |
Less control; suitable for fewer critical applications |
Excellent control, ideal for thin materials and critical projects |
Shielding Gas |
Can use argon-CO2 mixtures |
Often requires high levels of argon, sometimes mixed with a little CO2 or other inert gases |
Material Thickness |
Ideal for thicker sections where neat finish is less crucial |
Efficient with both thick and thin materials; best for applications requiring high precision and low heat distortion |
Expert Tips 📌
-
Use Globular Transfer for:
- Basic welding tasks.
- Projects where high spatter is acceptable.
- Situations with limited equipment budget.
-
Choose Pulsed Spray Transfer for:
- Precision welding on thin materials.
- Projects needing minimal post-weld cleanup.
- When investing in advanced equipment is feasible.
How to Reduce Spatter in Globular Transfer Welding
sing the right techniques and settings can help minimize spatter and improve weld quality. Here are some key tips:
✅ Use the Right Gas Blend
- Instead of pure CO₂, use a 75% argon / 25% CO₂ mix.
- This creates a smoother arc and reduces spatter.
✅ Adjust Wire Feed Speed & Voltage
- Too much wire speed or voltage makes droplets too big, causing more spatter.
- Find a balance where the wire feeds smoothly without forming large molten drops.
✅ Maintain a Steady Hand & Correct Angle
- Hold the welding torch at a consistent angle to control the spatter.
- Aim for about 15 degrees to direct the spatter away from your workpiece.
✅ Keep Your Work Area Clean
- Dirt, rust, and oil on the metal can increase spatter.
- Wipe down surfaces before welding for a cleaner weld.
✅ Practice & Adjust as Needed
- Welding takes practice—pay attention to how changes in settings affect the spatter.
- Experiment and fine-tune your technique for better results.
By following these tips, you can reduce spatter, improve weld quality, and make cleanup easier!
Safety Tips for Globular Transfer Welding
Following proper safety measures is essential when using globular transfer welding. Here’s what you need to do to stay safe and improve your weld quality:
✅ Protect Your Eyes & Vision
- Wear an auto-darkening welding helmet to shield your eyes from the bright arc.
- This helps reduce eye strain and improves visibility while welding.
✅ Wear Flame-Resistant Gear
- Use flame-resistant clothing to protect your skin from hot spatter.
- Wear a welding apron, safety gloves, and safety glasses for extra protection.
✅ Follow Fire Safety Precautions
- Keep a fire extinguisher nearby in case of emergencies.
- Remove flammable materials from the work area.
- Make sure everyone knows emergency exits and procedures.
✅ Ensure Proper Ventilation
- CO₂ gas buildup can be dangerous—make sure your space has good airflow.
- Use fans or ventilation systems to reduce fume exposure.
✅ Maintain the Right Stick-Out Length
- Keep a consistent stick-out distance to prevent porosity and defects.
- A steady hand helps maintain a stable arc for better weld quality.
✅ Monitor Voltage Settings
- Avoid using excessively high voltage, as it can cause porosity and burn-through.
- Check and adjust your settings regularly to maintain smooth welding.
✅ Keep Your Work Surface Clean
- Dirt, rust, and oil can cause weld instability and defects.
- Always clean materials before welding to reduce contamination.
What is the Best Setting for Globular Transfer Welding
To get the best results with globular transfer welding, you need to adjust your voltage, wire feed speed, and shielding gas properly. Here are the key settings to follow:
✅ Voltage: Set the voltage between 22V and 30V, depending on the wire size and material thickness. Higher voltage helps transfer molten metal across the arc, but too much can cause excessive spatter.
✅ Wire Feed Speed: Adjust the speed to match the voltage. A too-high speed creates large, uncontrollable droplets, while too low can cause an unstable arc. Follow manufacturer recommendations for your wire diameter.
✅ Stick-Out Length: Keep a longer stick-out (about ½ inch to ¾ inch) compared to short-circuit welding. This helps control heat input and prevents excessive spatter.
By fine-tuning these settings, you can achieve better weld quality, reduce spatter, and improve arc stability when using globular transfer welding.
Final Thoughts
Globular transfer welding is a useful method for welding thicker materials, but it requires proper settings and techniques to control spatter and ensure strong welds.
By adjusting your voltage, wire speed, and shielding gas, you can improve weld quality and minimize common issues.
Safety is also key—wear protective gear, maintain good ventilation, and keep your work area clean. With the right equipment and practice, you can achieve better results.
If you’re looking for high-quality welding machines, check out Arccaptain—the No. 1 brand in the market! Upgrade your gear today and take your welding skills to the next level!
Frequently Asked Questions
Globular transfer welding is known for its unique droplet formation and transfer method. It’s important to understand its uses, voltage settings, and suitability for different positions and materials.
What is globular transfer welding used for?
Globular transfer welding is used for welding thicker materials where deep penetration is needed. It works well in heavy fabrication, structural welding, and industrial applications. This method is not ideal for thin metals because it produces large molten droplets and more spatter. However, it is a good choice when speed and material deposition are more important than precision.
What is the voltage for globular transfer welding?
The voltage for globular transfer welding is typically between 22V and 30V, depending on the material and wire size. Higher voltage helps the molten metal transfer across the arc in large droplets. However, too much voltage can cause excessive spatter and arc instability. Adjusting the voltage correctly helps achieve a more controlled weld.
Can globular transfer be used in all positions?
No, globular transfer welding works best in flat and horizontal positions. The large molten droplets fall due to gravity, making it difficult to control in vertical or overhead welding. Using this method in out-of-position welding can lead to poor penetration and excessive spatter. For better control in all positions, other transfer methods like short circuit or spray transfer are recommended.
What type of shielding gas is best for globular transfer?
The best shielding gas for globular transfer welding is 100% CO₂ or a 75% Argon / 25% CO₂ mix. Pure CO₂ provides deeper penetration but produces more spatter. A CO₂-Argon blend helps create a more stable arc with less spatter. Choosing the right gas affects weld quality, bead shape, and overall control.
Can globular transfer welding be used on thin metals?
No, globular transfer welding is not ideal for thin metals because the large molten droplets can cause burn-through and excess spatter. It works better on thicker materials where heat and deep penetration are needed. For thin metals, short circuit transfer is a better option since it provides better control and reduces the risk of damaging the material.
Which welding machine is best for globular transfer?
A MIG welding machine is the best choice for globular transfer welding. MIG welders provide the necessary voltage and current settings to handle this transfer method. For high-quality and reliable MIG welders, Arccaptain is the No. 1 brand in the market. Their machines offer stable arc performance, precise control, and durability for professional results.
Related Articles 📖: