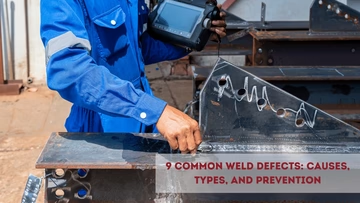
Si trabaja en la industria de la soldadura, sabrá que los defectos de soldadura pueden ser un problema grave. La soldadura es un proceso complejo que implica fusionar dos piezas de metal, e incluso el error más pequeño puede provocar un defecto. Estos defectos pueden debilitar la soldadura y comprometer la integridad de toda la estructura. Por eso es fundamental comprender qué son los defectos de soldadura y cómo prevenirlos.
Los defectos de soldadura pueden adoptar muchas formas, desde porosidad y grietas hasta falta de fusión y penetración incompleta. Cada tipo de defecto tiene sus propias características y causas únicas, y comprender estos factores es esencial para producir soldaduras de alta calidad.
En este artículo, exploraremos los tipos más comunes de defectos de soldadura y sus causas principales. También discutiremos cómo verificar defectos y evitar que ocurran en primer lugar. Al final de este artículo, tendrá un conocimiento sólido de los defectos de soldadura y estará mejor equipado para producir soldaduras fuertes y confiables.
Conclusiones clave
-
Los defectos de soldadura pueden comprometer la integridad de una estructura y deben evitarse.
-
Existen muchos tipos de defectos de soldadura, cada uno con sus propias características y causas únicas.
-
Comprender cómo prevenir y comprobar defectos de soldadura es esencial para producir soldaduras de alta calidad.
¿Qué son los defectos de soldadura?
Los defectos de soldadura se refieren a imperfecciones o irregularidades que ocurren durante el proceso de soldadura. Estos defectos pueden ocurrir debido a diversas razones, como técnicas de soldadura inadecuadas, materiales de mala calidad o capacitación inadecuada.
Abordar los defectos de soldadura es crucial para garantizar la seguridad y la calidad en los proyectos de soldadura. Los defectos de soldadura pueden comprometer la integridad estructural de la unión soldada y aumentar el riesgo de falla. Esto puede provocar accidentes, lesiones e incluso la muerte en algunos casos. Además, los defectos de soldadura también pueden afectar la calidad de la soldadura, lo que genera problemas como fugas, corrosión y una vida útil reducida.
Tipos de defectos de soldadura
Pueden ocurrir varios tipos de defectos de soldadura, que incluyen:
-
Porosidad
-
Grietas
-
Falta de fusión
-
Grietas
-
Penetración incompleta
-
Inclusión de escoria
-
Vender a menor precio que
-
Superposición
-
Quemar
La soldadura es un proceso complejo que requiere una cuidadosa atención a los detalles para garantizar un resultado exitoso. Desafortunadamente, incluso los soldadores más hábiles pueden encontrar defectos de soldadura. Estos defectos pueden comprometer la resistencia y la integridad de la soldadura, provocando reparaciones costosas o incluso fallas catastróficas.
Porosidad
La porosidad es un defecto de soldadura común que ocurre cuando las burbujas de gas quedan atrapadas en el metal de soldadura. Estas burbujas pueden debilitar la soldadura y hacerla más susceptible al agrietamiento y la corrosión. La porosidad puede ser causada por una variedad de factores, incluido un gas de protección inadecuado, metal de aportación contaminado o una técnica de soldadura deficiente.
Cómo prevenir la porosidad
Prevenir la porosidad requiere una cuidadosa atención a la técnica y las condiciones de soldadura. Aquí hay algunos pasos que puede seguir para prevenir la porosidad:
-
Asegure una cobertura adecuada de gas de protección: asegúrese de que el área de soldadura esté cubierta adecuadamente por gas de protección para evitar la exposición al aire y la humedad.
-
Utilice metal de aportación seco: la humedad puede provocar porosidad, por lo que es importante utilizar metal de aportación seco.
-
Limpiar el metal base: asegúrese de que el metal base esté libre de contaminantes que puedan causar porosidad.
-
Utilice una técnica de soldadura adecuada: siga las técnicas y pautas de soldadura adecuadas para garantizar una soldadura fuerte y estable.
Causas de la porosidad en la soldadura
La porosidad puede ser causada por una variedad de factores, que incluyen:
-
Cobertura inadecuada del gas de protección
-
Contaminación por humedad
-
Mala técnica de soldadura.
-
Presencia de impurezas en el metal base o metal de aporte.
-
Fusión incompleta entre el metal de soldadura y el metal base.
-
Velocidad de soldadura excesiva
-
Manipulación inadecuada de los electrodos.
-
Parámetros de soldadura incorrectos, como voltaje o amperaje.
Al comprender las causas de la porosidad y tomar medidas para prevenirla, se pueden producir soldaduras de alta calidad y libres de defectos.
Grietas
Las grietas son otro defecto de soldadura común que puede ocurrir tanto en el metal de soldadura como en la zona afectada por el calor. Las grietas pueden ser causadas por una variedad de factores, incluidos altos niveles de tensión, enfriamiento inadecuado o una técnica de soldadura deficiente. Las grietas pueden comprometer la resistencia y la integridad de la soldadura, provocando fallas catastróficas.
Tipos de grietas en la soldadura
Hay tres tipos principales de grietas:
- Grietas longitudinales – correr paralelo a la soldadura, debilitando toda su longitud.
- Grietas transversales – atraviesan el ancho de una cuenta, provocando debilidades localizadas pero graves.
- Grietas de cráter – a menudo forman marcas en forma de estrella al final de una soldadura cuando se termina el arco
Cómo prevenir grietas
Para evitar grietas en la soldadura, siga estos pasos:
-
Utilice la técnica de soldadura correcta para el tipo de material que se va a soldar.
-
Asegúrese de que los parámetros de soldadura estén configurados correctamente para el material que se está soldando.
-
Utilice técnicas adecuadas de tratamiento térmico de precalentamiento y possoldadura.
-
Mantenga una velocidad y técnica de soldadura consistentes.
-
Utilice el material de relleno correcto para el tipo de material que se va a soldar.
Causas de grietas en la soldadura
-
Alto estrés en la zona de soldadura.
-
Mala técnica de soldadura, como ángulo inadecuado del electrodo o penetración inadecuada.
-
Parámetros de soldadura incorrectos, como voltaje o amperaje incorrectos.
-
Tratamiento térmico de precalentamiento o post-soldadura inadecuado.
-
Uso de material de relleno incorrecto.
Al comprender las causas de las grietas y tomar las precauciones necesarias, puede prevenir este defecto de soldadura común y garantizar una soldadura fuerte y duradera.
Falta de fusión
La falta de fusión ocurre cuando el metal de soldadura no logra unirse adecuadamente con el metal base. Esto puede deberse a una variedad de factores, incluido un aporte de calor inadecuado, una técnica de soldadura deficiente o metal base contaminado. La falta de fusión puede comprometer la resistencia y la integridad de la soldadura, provocando reparaciones costosas o incluso fallas catastróficas.
Para identificar la falta de fusión, busque los siguientes signos:
-
Penetración incompleta
-
Falta de unión entre el metal de soldadura y el metal base o metal de soldadura previamente depositado.
-
Grietas o huecos en el cordón de soldadura.
Cómo prevenir la falta de fusión
Prevenir la falta de fusión requiere una cuidadosa atención a los parámetros y técnicas de soldadura. Aquí hay algunos pasos que puede seguir para evitar la falta de fusión:
-
Asegure una preparación y ajuste adecuados de la junta para permitir una penetración y fusión adecuadas.
-
Utilice la técnica de soldadura y los parámetros correctos para la configuración de la junta y el material que se va a soldar.
-
Mantenga una entrada de calor adecuada para garantizar una fusión y fusión adecuadas del metal de soldadura.
-
Utilice técnicas de soldadura adecuadas para garantizar una cobertura adecuada del gas de protección y evitar la contaminación del metal de soldadura.
Causas de la falta de fusión en la soldadura
Varios factores pueden contribuir a la falta de fusión en la soldadura. Aquí hay algunas causas comunes:
-
Preparación y ajuste inadecuados de las articulaciones.
-
Técnica o parámetros de soldadura incorrectos.
-
Aporte de calor insuficiente
-
Contaminación del metal de soldadura o del metal base.
-
Mala cobertura de gas de protección
Al comprender las causas de la falta de fusión y tomar medidas para evitarla, puede garantizar soldaduras fuertes y confiables que cumplan con las especificaciones requeridas.
Penetración incompleta
La penetración es una medida de qué tan profundo penetra el metal de soldadura en el metal base. Una penetración insuficiente puede comprometer la resistencia y la integridad de la soldadura, provocando fallas catastróficas. La penetración excesiva también puede ser un problema, ya que puede debilitar el metal base y hacerlo más susceptible al agrietamiento y la corrosión.
Cómo prevenir la penetración incompleta
Para evitar una penetración incompleta, debes seguir estos pasos:
-
Utilice la técnica y el proceso de soldadura adecuados para el material y el diseño de la junta.
-
Asegúrese de que la junta esté adecuadamente limpia y preparada antes de soldar.
-
Utilice los parámetros de soldadura correctos, incluida la corriente, el voltaje y la velocidad de desplazamiento correctos.
-
Controlar el aporte de calor para evitar sobrecalentar o subcalentar la junta.
-
Utilice el material de relleno de soldadura correcto y asegúrese de que sea compatible con el material base.
Causas de la penetración incompleta
La penetración incompleta puede deberse a varios factores, entre ellos:
-
Aporte de calor insuficiente: si el aporte de calor es demasiado bajo, es posible que el metal de soldadura no penetre a través de la junta.
-
Diseño de unión incorrecto: Un diseño de unión deficiente puede provocar un acceso inadecuado para el metal de soldadura, lo que resulta en una penetración incompleta.
-
Mal ajuste: Si las piezas a soldar no están correctamente alineadas, pueden quedar huecos en la unión, provocando una penetración incompleta.
-
Limpieza inadecuada: Si la junta no se limpia adecuadamente de contaminantes, es posible que el metal de soldadura no penetre a través de la junta.
-
Parámetros de soldadura incorrectos: los parámetros de soldadura incorrectos, como la corriente, el voltaje y la velocidad de desplazamiento, pueden provocar una penetración incompleta.
Al comprender las causas de la penetración incompleta y seguir los pasos para prevenirla, puede asegurarse de que sus soldaduras sean fuertes y confiables.
Inclusión de escoria
La inclusión de escoria ocurre cuando la escoria queda atrapada en el metal de soldadura. La escoria es un subproducto del proceso de soldadura y puede ser causada por una variedad de factores, incluido un gas de protección inadecuado, metal de aportación contaminado o una técnica de soldadura deficiente. La inclusión de escoria puede comprometer la resistencia y la integridad de la soldadura, provocando reparaciones costosas o incluso fallas catastróficas.
Cómo prevenir las inclusiones de escoria
Prevenir las inclusiones de escoria es crucial para garantizar la calidad y resistencia de la soldadura. Aquí hay algunos pasos que puede seguir para prevenir inclusiones de escoria:
-
Limpie bien el metal base antes de soldar para eliminar óxido, aceite u otros contaminantes que puedan causar inclusiones de escoria.
-
Utilice la técnica y los parámetros de soldadura correctos, como la velocidad y la corriente de soldadura adecuadas, para garantizar una fusión adecuada y minimizar la formación de escoria.
-
Utilice el tamaño y tipo de electrodo correcto para la aplicación de soldadura para evitar la acumulación excesiva de escoria.
-
Mantenga una longitud y un ángulo de arco adecuados para evitar salpicaduras excesivas y acumulación de escoria.
Causas de las inclusiones de escoria
Existen varias causas de inclusiones de escoria en la soldadura, entre ellas:
-
Mala técnica de soldadura, como ángulo de electrodo inadecuado, longitud de arco incorrecta o velocidad de soldadura incorrecta.
-
Limpieza insuficiente del metal base, lo que puede dejar contaminantes que pueden provocar inclusiones de escoria.
-
Usar el tamaño o tipo de electrodo incorrecto para la aplicación de soldadura.
-
Salpicaduras excesivas, que pueden provocar que la escoria quede atrapada en el metal de soldadura.
-
Soldar en un lugar con viento o movimiento de aire excesivos, lo que puede provocar que la escoria entre en la soldadura.
Al comprender las causas de las inclusiones de escoria y tomar las medidas necesarias para prevenirlas, puede garantizar la calidad y resistencia de sus soldaduras y evitar posibles fallas.
Vender a menor precio que
El socavado es un defecto de soldadura común que ocurre cuando el metal de soldadura no llena completamente la junta, dejando una ranura o depresión en el metal base adyacente a la soldadura. El corte socavado puede debilitar la articulación y hacerla más susceptible a agrietarse y fallar.
Cómo prevenir socavaduras en la soldadura
Para evitar socavaduras en la soldadura, debe seguir estos pasos:
-
Utilice la técnica y el equipo de soldadura correctos para el trabajo.
-
Preparar adecuadamente la junta, incluyendo limpieza y biselado de los bordes.
-
Utilice los parámetros de soldadura correctos, como voltaje, amperaje y velocidad de desplazamiento.
-
Controle el aporte de calor para evitar el sobrecalentamiento del metal base.
-
Utilice una varilla o alambre de soldadura adecuado que sea compatible con el metal base.
Si sigue estos pasos, puede minimizar el riesgo de socavado y producir una soldadura fuerte y de alta calidad.
Causas del socavado en la soldadura.
Hay varias causas de socavado en la soldadura, que incluyen:
-
Preparación inadecuada de la junta, como limpieza inadecuada o ángulo de bisel incorrecto.
-
Técnica de soldadura inadecuada, como velocidad de desplazamiento o ángulo de soldadura incorrectos.
-
Parámetros de soldadura incorrectos, como voltaje o amperaje excesivo.
-
Mal ajuste de la articulación, como espacios o desalineación.
-
Cobertura inadecuada del gas de protección, que puede provocar oxidación y socavado.
Al comprender las causas del socavado, puede tomar medidas para prevenirlo y producir soldaduras de alta calidad.
Superposición
La superposición en la soldadura ocurre cuando el metal de soldadura se deposita sobre el metal base, pero no se fusiona con el metal base. Esto da como resultado una articulación débil y poco confiable. La superposición puede deberse a varios factores, como una técnica de soldadura inadecuada, parámetros de soldadura incorrectos y una mala preparación del metal base.
Cómo evitar la superposición en la soldadura
Se puede evitar la superposición en la soldadura siguiendo estos pasos:
-
Asegure la preparación adecuada del metal base limpiando y eliminando cualquier contaminante como óxido, aceite y grasa.
-
Utilice la técnica y los parámetros de soldadura correctos para la aplicación específica.
-
Mantenga la distancia correcta entre el electrodo y el metal base.
-
Utilice la velocidad de soldadura adecuada para garantizar la fusión adecuada del metal de soldadura y el metal base.
-
Inspeccione la soldadura una vez finalizada para asegurarse de que no haya superposiciones.
Causas de superposición en soldadura
Algunas de las causas de la superposición en la soldadura incluyen:
-
Técnica de soldadura incorrecta
-
Parámetros de soldadura incorrectos
-
Mala preparación del metal base.
-
Velocidad de soldadura inadecuada
-
Tamaño de electrodo incorrecto
-
Cobertura inadecuada del gas de protección
Si comprende las causas de la superposición en la soldadura y sigue los pasos para evitarla, podrá garantizar una unión fuerte y confiable.
Quemado
El quemado es un defecto de soldadura común que ocurre cuando el baño de soldadura penetra a través del metal base, lo que resulta en un agujero o cavidad. Este defecto puede debilitar la unión soldada y comprometer su integridad estructural.
El quemado puede ocurrir por varias razones, incluyendo un aporte excesivo de calor, una técnica de soldadura inadecuada y una preparación inadecuada de la junta. Es más probable que ocurra al soldar materiales delgados o en una posición vertical o por encima de la cabeza.
Cómo prevenir quemaduras en la soldadura
Para evitar quemaduras durante la soldadura, puede seguir los siguientes pasos:
-
Ajuste los parámetros de soldadura, como la corriente, el voltaje y la velocidad de desplazamiento, para garantizar que la entrada de calor esté dentro del rango aceptable.
-
Utilice la técnica de soldadura adecuada, como un movimiento de tejido o un paso atrás, para distribuir el calor de manera uniforme y evitar el sobrecalentamiento de un área en particular.
-
Prepare adecuadamente la junta limpiando y biselando los bordes para asegurar una adecuada penetración y fusión.
-
Utilice un ajuste de amperaje más bajo o un tamaño de electrodo más pequeño cuando suelde materiales delgados.
Causas del quemado en la soldadura
Las siguientes son las causas comunes de quemaduras en la soldadura:
-
Aporte de calor excesivo: cuando el aporte de calor es demasiado alto, el baño de soldadura puede penetrar a través del metal base y provocar quemaduras.
-
Técnica de soldadura inadecuada : utilizar una técnica de soldadura incorrecta o no distribuir el calor de manera uniforme puede provocar sobrecalentamiento y quemaduras.
-
Preparación inadecuada de la junta: Una mala preparación de la junta, como una limpieza o un biselado inadecuados, puede provocar una fusión incompleta y quemaduras.
-
Soldadura de materiales delgados: Los materiales delgados son más susceptibles a quemarse, especialmente cuando se sueldan en posición vertical o por encima de la cabeza.
Si sigue las técnicas de soldadura adecuadas y toma las precauciones necesarias, puede evitar quemaduras y garantizar una unión soldada fuerte y confiable.
Principales causas y soluciones de los defectos de soldadura
Los defectos de soldadura pueden ocurrir por diversas razones. Comprender las causas fundamentales de estos defectos puede ayudar a prevenir su aparición y garantizar un proceso de soldadura exitoso. Estas son algunas de las principales causas de los defectos de soldadura:
Contaminación de materiales
La contaminación del metal base, del metal de aportación o del gas protector puede provocar defectos de soldadura. La humedad, el aceite, la grasa y otros contaminantes pueden provocar porosidad, grietas y otros defectos. Es importante asegurarse de que todos los materiales estén limpios y secos antes de soldar.
Parámetros de soldadura inadecuados
Los parámetros de soldadura incorrectos, como voltaje, corriente, velocidad de desplazamiento y flujo de gas, pueden causar defectos de soldadura. Por ejemplo, un voltaje o corriente excesivos pueden provocar quemaduras, mientras que un voltaje o corriente insuficientes pueden provocar una fusión incompleta. Es importante establecer los parámetros correctos para cada aplicación de soldadura.
Técnicas de soldadura incorrectas
El uso de técnicas incorrectas de pistolas de soldar también puede causar defectos de soldadura. Por ejemplo, una preparación inadecuada de la unión, un ángulo incorrecto del electrodo y una técnica de tejido incorrecta pueden causar defectos como falta de fusión y socavado. Es importante utilizar la técnica de soldadura adecuada para cada unión y aplicación.
Mal funcionamiento del equipo
El mal funcionamiento del equipo, como fuentes de energía defectuosas, pistolas de soldar defectuosas y consumibles desgastados, pueden causar defectos de soldadura. Es importante inspeccionar y mantener periódicamente todos los equipos de soldadura para garantizar un rendimiento óptimo.
En conclusión, los defectos de soldadura pueden ocurrir debido a una variedad de razones, como contaminación del material, parámetros de soldadura inadecuados, técnicas de soldadura incorrectas y mal funcionamiento del equipo. Al comprender estas causas fundamentales, podrá tomar las medidas necesarias para evitar que ocurran y garantizar un proceso de soldadura exitoso.
Cómo comprobar los defectos de soldadura
La comprobación de defectos de soldadura es una parte esencial para garantizar la calidad de una soldadura. Aquí hay algunos pasos simples que puede seguir para verificar si hay defectos de soldadura:
-
Inspección Visual: El primer paso es realizar una inspección visual de la soldadura. Compruebe si hay grietas, porosidad, socavados o cualquier otro defecto visible. Utilice una lupa o un microscopio si es necesario.
-
Prueba de tintes penetrantes: La prueba de tintes penetrantes es un método de prueba no destructivo que se utiliza para detectar defectos de rotura de superficies. Aplique una solución de tinte penetrante a la superficie de la soldadura y déjela reposar durante un tiempo específico. Luego, retira el exceso de solución y aplica un revelador. Cualquier defecto será visible como una marca roja brillante.
-
Inspección de partículas magnéticas: la inspección de partículas magnéticas es otro método de prueba no destructivo que se utiliza para detectar defectos superficiales y ligeramente subsuperficiales. Aplique un campo magnético a la superficie de la soldadura y espolvoree partículas de hierro sobre la superficie. Cualquier defecto será visible como una línea oscura.
-
Pruebas ultrasónicas: las pruebas ultrasónicas son un método de prueba no destructivo que se utiliza para detectar defectos internos. Las ondas sonoras se envían a través de la soldadura y cualquier defecto las reflejará de regreso a la superficie.
-
Pruebas radiográficas : las pruebas radiográficas son un método de prueba no destructivo que se utiliza para detectar defectos internos. Los rayos X o gamma pasan a través de la soldadura y cualquier defecto aparecerá como puntos oscuros en la película.
Siguiendo estos pasos, podrá asegurarse de que su soldadura esté libre de defectos y cumpla con los estándares de calidad necesarios.
Defectos de soldadura en soldadura MIG, TIG y STICK
Cuando se trata de soldadura MIG , TIG y electrodo revestido, existen varios tipos de defectos de soldadura que pueden ocurrir. Saber cuáles son estos defectos y cómo prevenirlos es crucial para producir soldaduras de alta calidad.
Estos son algunos de los defectos de soldadura más comunes en soldadura MIG, TIG y electrodo revestido:
-
Porosidad : Ocurre cuando quedan atrapadas bolsas de gas en la soldadura. La porosidad debilita la soldadura y puede provocar que falle bajo tensión.
-
Socavado : esto sucede cuando el metal base se funde lejos de la soldadura, dejando una ranura. El socavado puede debilitar la soldadura y hacerla más susceptible a agrietarse.
-
Fusión incompleta: esto ocurre cuando la soldadura no se fusiona completamente con el metal base. La fusión incompleta puede hacer que la soldadura se rompa bajo tensión.
-
Superposición: esto sucede cuando la soldadura se superpone, creando un punto débil en la soldadura.
-
Agrietamiento: esto ocurre cuando la soldadura se enfría demasiado rápido o cuando hay demasiada tensión sobre la soldadura. El agrietamiento puede hacer que la soldadura falle.
En general, es importante comprender los defectos de soldadura comunes en la soldadura MIG, TIG y electrodo revestido y cómo prevenirlos. Si sigue las técnicas de soldadura adecuadas y ajusta los parámetros de soldadura, puede minimizar la aparición de estos defectos y producir soldaduras de alta calidad.
Conclusión
En resumen, comprender los defectos de soldadura es crucial para garantizar la calidad y seguridad de las estructuras soldadas. Los defectos de soldadura pueden provocar fallos y accidentes, lo que puede resultar costoso tanto en términos de dinero como de vidas humanas.
Hay varios tipos de defectos de soldadura, incluyendo porosidad, falta de fusión, socavado y agrietamiento. Cada tipo de defecto tiene sus propias causas y características únicas, y es importante poder identificarlas y abordarlas para prevenir problemas futuros.
La porosidad es causada por el gas atrapado en la soldadura, mientras que la falta de fusión ocurre cuando el metal de soldadura no logra fusionarse con el metal base. El socavado ocurre cuando el metal base se funde lejos de la soldadura, y el agrietamiento puede ser causado por una variedad de factores, incluido el enfriamiento inadecuado y la tensión.
La prevención de defectos de soldadura requiere una cuidadosa atención a los detalles y el cumplimiento de las mejores prácticas. Esto incluye la preparación adecuada de la unión, la selección de materiales y técnicas de soldadura apropiados y una inspección y prueba cuidadosas de la soldadura terminada.
Al comprender las causas y características de los defectos de soldadura y tomar las medidas adecuadas para prevenirlos, puede asegurarse de que sus estructuras soldadas sean fuertes, seguras y confiables.
Preguntas frecuentes
¿Cuáles son los 7 defectos comunes de soldadura?
Los 7 defectos comunes de soldadura son:
-
Porosidad
-
Subcotización
-
Fusión incompleta
-
Grietas
-
superpuestas
-
Salpicar
-
Quemado
¿Cómo se identifican los defectos de soldadura?
Para identificar defectos de soldadura, es necesario inspeccionar la soldadura visualmente o con métodos de prueba no destructivos. La inspección visual incluye la verificación de irregularidades, grietas y porosidad de la superficie. Los métodos de prueba no destructivos incluyen radiografía, pruebas ultrasónicas, inspección con partículas magnéticas e inspección con tintes penetrantes.
¿Cómo identificaría una mala soldadura?
Una mala soldadura se puede identificar por su apariencia, que incluye grietas, porosidad, socavados y fusión incompleta. Una mala soldadura también puede fallar cuando se somete a tensión o presión.
¿Cuáles son los 3 defectos de soldadura que se encuentran en la soldadura MIG?
Los 3 defectos de soldadura comunes que se encuentran en la soldadura MIG son:
-
Quemado
-
Fusión incompleta
-
Porosidad
Es importante identificar y corregir estos defectos para garantizar la calidad y resistencia de la soldadura.