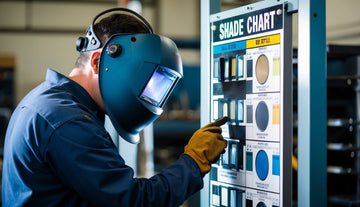
A welding helmet shade chart is essential for selecting the right lens for your specific welding tasks.
Proper lens shading protects your eyes from harmful light and ensures you can see clearly to make accurate welds. Choosing the wrong shade can cause eye strain or damage, so it's crucial to match the shade with your welding process.
Techniques like MIG or TIG require different lens shades based on their intensity. The right shade impacts both your safety and welding performance.
By exploring the various options, you can find the perfect match for your needs. Ready to learn how to pick the right shade for your next project? Read on to discover tips, charts, and everything you need to know about welding helmet shades.
What Is a Welding Helmet Shade Chart?

A welding helmet shade chart is a guide that helps you choose the right lens shade for your welding tasks. The shade number indicates how dark the lens is, affecting how much light gets through.
Shade Numbers:
- Shade numbers typically range from 4 to 14.
- A higher number means a darker lens, which protects your eyes from intense light and radiation.
Using the correct shade is crucial for comfort and safety. If the shade is too light, harmful rays can reach your eyes. If it is too dark, you may struggle to see your work.
Welding Helmet Shade Table
You will find that different welding processes require different shade levels. A good shade chart not only enhances visibility but also complies with safety regulations.
Welding Process |
Current (Amperes) |
Shade Number |
Shielded Metal Arc Welding (SMAW) |
< 60 A |
7 |
60 - 160 A |
8 |
|
160 - 250 A |
10 |
|
250 - 550 A |
11 |
|
Gas Metal Arc Welding (GMAW) |
< 60 A |
7 |
60 - 160 A |
10 |
|
160 - 250 A |
10 |
|
250 - 550 A |
12 |
|
Gas Tungsten Arc Welding (GTAW) |
< 50 A |
8 |
50 - 150 A |
8 |
|
150 - 500 A |
10 |
|
Flux-Cored Arc Welding (FCAW) |
< 60 A |
10 |
60 - 160 A |
10 |
|
160 - 250 A |
10 |
|
250 - 550 A |
12 |
|
Plasma Arc Welding |
< 20 A |
6 |
20 - 100 A |
8 |
|
100 - 400 A |
10 |
|
Plasma Arc Cutting |
< 20 A |
4 |
20 - 40 A |
5 |
|
40 - 60 A |
6 |
|
60 - 80 A |
8 |
|
80 - 300 A |
8 |
|
300 - 400 A |
9 |
|
Gas Welding |
< 1/8 inch |
4 |
1/8 - 1/2 inch |
5 |
|
> 1/2 inch |
6 |
|
Oxygen Cutting |
< 1 inch |
3 |
1 - 6 inches |
4 |
|
> 6 inches |
5 |
Always select your helmet’s shade based on the type of welding and the amperage you are using. This ensures optimal protection for your eyes during work.
What Are Welding Lens Shades?

Welding lens shades are special filters in welding helmets that protect your eyes from the bright light and harmful radiation produced during welding. These shades are essential for both safety and clear visibility. They reduce the amount of visible light, infrared (IR), and ultraviolet (UV) radiation that reaches your eyes, preventing eye strain, burns, and long-term damage.
Lens shades are categorized by numbers, usually ranging from 3 to 14. Higher numbers mean darker shades that block more light. The right shade number depends on the welding process and the intensity of the welding arc.
For example, more intense processes like Shielded Metal Arc Welding (SMAW) and Gas Metal Arc Welding (GMAW) need darker shades compared to less intense processes like oxy-fuel welding and cutting.
Choosing the correct lens shade is crucial. A lens that is too light won't protect your eyes adequately, while one that is too dark can make it hard to see your work clearly. Understanding how to pick the right shade for your specific welding task ensures both your safety and the quality of your welds.
Importance of Using the Correct Shade

Using the right lens shade is crucial for your safety while welding. The correct shade protects your eyes from harmful radiation, including ultraviolet (UV) and infrared (IR) light.
Key Reasons to Use the Correct Shade:
-
Eye Protection: The right shade reduces the risk of eye damage. This damage can result from bright arcs or sparks created during welding.
-
Visibility: A proper lens shade allows you to see the weld pool clearly. Good visibility helps you make more accurate welds.
- Comfort: Wearing the right shade prevents eye strain. If the shade is too dark or too light, you may become uncomfortable and fatigued during work.
Make sure to check manufacturer recommendations and follow standards, like ANSI and AWS, for selecting the right shade.
Always prioritize your eye safety by choosing the correct welding helmet lens shade.
Factors Influencing Lens Shade Selection
Choosing the right lens shade for your welding helmet is crucial for protecting your eyes from harmful radiation.
Several factors affect your decision, including the type of welding process, the environment where you're working, and your comfort level.
Type of Welding Process
Different welding processes produce varying amounts of bright light and radiation.
For example, Gas Metal Arc Welding (GMAW) typically requires a shade between #11 to #13, depending on the amperage used.
Conversely, Shielded Metal Arc Welding (SMAW) usually needs a darker lens due to higher radiation levels, often around shade #12 to #14.
Selecting the right lens shade also helps protect against infrared light and harmful UV radiation.
Make sure to consult the shade charts specific to the welding process you are using.
Welding Environment and Conditions
The environment where you weld significantly impacts the required lens shade.
In outdoor settings, bright sunlight can make it harder to see the weld. You might need a darker shade to counteract the effects of external light.
In contrast, indoor conditions with lower light levels may allow for a lighter shade.
Additionally, consider factors like sparks and spatter that can occur when welding.
A wider viewing area with the right shade can also help improve vision while ensuring optimal eye protection.
Personal Comfort and Safety
Comfort is key when selecting a lens shade.
A shade that is too dark can make it difficult to see your workspace, leading to mistakes.
You need a balance between sufficient protection and visual clarity.
If you wear prescription glasses, ensure your helmet accommodates them without compromising fit.
Lighter shades, like #5 to #9, can work well for tasks like tacking and positioning.
Your comfort affects your focus, which is essential for safety. Make sure the helmet is also lightweight for extended use.
Determining the Right Shade for Various Welding Processes

Choosing the correct lens shade for your welding helmet is crucial for eye protection.
Different welding processes require different shade levels based on amperage and brightness. Below are the recommendations for popular welding methods.
MIG Welding Shade Recommendations
For Gas Metal Arc Welding (GMAW), a common choice is shade 10 to shade 12.
This range is ideal for most MIG welding applications where the amperage typically runs between 130 to 300 amps.
Amperage Range |
Recommended Shade |
130 - 200 A |
Shade 10 |
200 - 300 A |
Shade 11 |
Above 300 A |
Shade 12 |
You may also prefer shade 13 for very bright conditions or higher amperage jobs.
For Flux Core Arc Welding (FCAW), similar shade numbers apply, ensuring proper visibility and safety while working.
TIG Welding Shade Recommendations
For Gas Tungsten Arc Welding (GTAW), light intensity from the arc is lower than in MIG welding, making it necessary to use lighter shades.
The recommended shade number is often shade 9 to shade 12.
Amperage Range |
Recommended Shade |
10 - 150 A |
Shade 9 |
150 - 250 A |
Shade 10 |
Above 250 A |
Shade 11 to 12 |
If you're working with materials like aluminum, a shade between shade 5 to shade 8 may be adequate for lower amperages.
It’s essential to adjust your shade based on the specific job.
Stick Welding Shade Recommendations
For Shielded Metal Arc Welding (SMAW), you generally need darker shades due to the higher brightness of electric arcs.
A good rule of thumb is to use shade 10 to shade 14.
Amperage Range |
Recommended Shade |
40 - 140 A |
Shade 10 |
140 - 200 A |
Shade 11 to 12 |
Above 200 A |
Shade 13 to 14 |
This range helps protect your eyes from ultraviolet (UV) and infrared (IR) rays emitted during the process.
Using a Welding Helmet Shade Chart Effectively
A welding helmet shade chart is a valuable tool for selecting the right lens shade based on your welding process and amperage.
Knowing how to read and use the chart properly ensures clear visibility and adequate protection for your eyes.
Step-by-Step Guide to Reading the Chart
-
Identify the Welding Process: Start by noting the type of welding you will be performing, such as MIG, TIG, or stick welding. Each process has different requirements for lens shades.
-
Check Amperage Levels: Find the amperage of your welding machine. The shade chart usually provides recommended shade numbers based on these levels.
-
Locate the Correct Shade: Match your welding process and amperage to the chart. For instance, if you're using MIG welding at 250 amps, you might need a shade between #11 and #12.
-
Consider Visibility: Keep in mind that lighting conditions can impact your choice. Daytime work may require a darker shade for clear visibility, while nighttime work can often use lighter shades.
-
Follow Manufacturer Recommendations: Always refer to your helmet manufacturer’s instructions for any specific guidance on shades, ensuring you meet safety standards.
Tips for Optimal Use and Safety
-
Use the Right Shade: Select the appropriate shade number corresponding to your welding method and amperage.
A common shade for general MIG welding is #11, but factors like time of day and environment can influence this.
-
Test Your Visibility: Before starting your work, ensure that you can see clearly through the chosen lens shade.
Good visibility is crucial for accuracy and safety.
-
Adjust as Needed: If your job conditions change, don’t hesitate to switch to a different lens shade.
For example, when moving from indoor to outdoor welding, adjust your shade accordingly.
-
Stay Informed: Keep yourself updated on any changes in safety regulations regarding lens shades.
The Occupational Safety and Health Administration (OSHA) provides guidelines that can aid in your decisions.
-
Practice Safe Handling: Ensure your welding helmet is in good condition.
Check for scratches or cracks on the lens, which can affect visibility and safety.
Advanced Features in Modern Welding Helmets

Modern welding helmets are equipped with advanced features that enhance safety and usability. Two key advancements are auto-darkening technology and variable shade options, which significantly improve the welding experience.
Auto-Darkening Technology
Auto-darkening helmets use sensors to detect the brightness of the welding arc.
When you start welding, the lens automatically shifts to a darker shade, protecting your eyes from harmful light.
Most auto-darkening welding helmets have 2 to 4 arc sensors that quickly respond to changes in brightness.
This allows you to see clearly while setting up and welding without flipping the helmet up and down.
The lens reaction time is essential; high-quality models react within 1/25,000 of a second, ensuring your eyes stay protected at all times.
Many helmets also come with battery or solar power options, providing longer usage.
Variable Shade Options
Variable shade options allow you to change the lens darkness to suit different welding tasks.
This feature is critical because different welding processes emit various intensities of light.
For example, you might use a fixed shade for MIG welding but need a different shade for TIG welding.
Auto-darkening helmets often have shade settings that range from 9 to 13 or higher, giving you the flexibility you need across multiple applications.
Variables can be selected manually or automatically, making it easier to adapt to different environments.
Helmets with this ability ensure that you can safely see your work without sacrificing comfort or safety.
Common Mistakes to Avoid
Choosing the right welding helmet shade is vital for your safety. Mistakes can reduce protection and lead to eye damage. Here are two common errors to watch out for.
Ignoring Manufacturer Guidelines
Many users overlook the recommendations from manufacturers. Each helmet has specific guidelines about the proper shade settings.
These guidelines align with safety standards from ANSI and AWS.
Using shades outside these recommendations can lead to insufficient eye protection.
For example, if the manufacturer suggests a shade number of 10 for a process, you should avoid using a shade of 5.
Always check the manual for your helmet to ensure you are following the correct information.
Using filters that do not meet these standards can expose your eyes to harmful rays.
Adhering to manufacturer guidelines ensures you comply with safety standards and effectively protect your vision.
Using Incorrect Shade Settings
Choosing the wrong shade number is a frequent mistake.
Shade numbers usually range from 4 to 14, depending on the welding type and amperage.
For tasks with higher heat, like TIG welding at high amperage, select a darker shade. For MIG welding at lower amperage, a lighter shade might be sufficient.
Using the right shade ensures you can see what you are working on while protecting your eyes.
Cross-reference your welding process with the shade chart often provided by manufacturers.
This can help you match the correct shade number to the work you are doing and meet ANSI and AWS standards to keep your eyes safe.
Conclusion
Getting the right shade for your welding helmet is key to protecting your eyes from harmful rays during welding. It's important to follow the helmet manufacturer's shade guidelines to ensure your eyes are well-protected and comfortable.
If you're looking to upgrade or buy new welding equipment, ArcCaptain has you covered. They offer auto-darkening welding helmets that adjust the shade automatically, so you stay safe without having to make manual changes.
Arccaptain also provides a variety of welding protection gear, including gloves and aprons to keep you safe from sparks and heat. Plus, their range of high-quality welding machines ensures you have the right tools for any welding project.
Frequently Asked Questions
How do I select the appropriate welding helmet shade for different welding processes?
To select the right shade, you need to consider the type of welding you are doing.
Different processes, like MIG, TIG, or stick welding, require different shades to protect your eyes effectively from harmful light and radiation.
What are the differences between shade levels on welding helmets?
Welding helmets come with various shade levels.
Lighter shades, like #4, are suitable for low-amp applications, while darker shades, like #14, are needed for high-amp processes. The level affects the amount of light that reaches your eyes during welding.
What do the shade numbers indicate on a welding lens?
Shade numbers indicate the amount of darkness of the lens.
For example, a shade #10 lens is darker than a #5 lens. This numbering helps you choose the right lens for the specific welding task and the visibility you need.
How can I determine the proper shade for varying amperage levels in welding?
You can use a shade chart that correlates lens shades with amperage levels.
Generally, higher amperage requires darker shades to protect your eyes from increased brightness. For example, a MIG welder at 100 amps might need a #10 shade.
In what context would I use the darkest welding helmet shades?
The darkest shades, typically #12 to #14, are used for processes like high-amperage arc welding.
These shades protect against intense light and radiation that can damage your eyes in heavy welding situations.
Can I find a chart that classifies welding helmet shades from lightest to darkest?
Yes, many resources provide shade charts that list appropriate lens shades from lightest to darkest.
These charts often include guidelines based on the specific welding processes and the amperage used.
You can refer to these charts to make informed decisions.