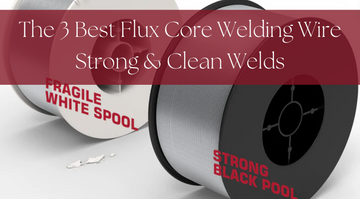
When it comes to welding, having the right materials is crucial. The best flux core welding wire can greatly enhance your weld quality and efficiency. Whether you're working with mild steel or stainless steel, the right wire ensures you achieve strong, durable joints.
Picking the right flux core wire isn’t just about choosing a brand; it’s about knowing what your project needs. Things like the wire size and whether it works with the materials you’re using are key to getting good results.
When looking at different options, think about how each type of flux core wire fits your project. With the right details, you can make a smart choice for better, more reliable welding.
Want to know which wire is best for your job? Keep reading to learn how to pick the perfect flux core wire for your next welding project!
What Is Flux Core Welding Wire and Why It Matters?
Flux core welding wire is a type of welding filler that contains a flux in its core. This core helps in the welding process by producing a shielding gas when heated. This feature makes it a great choice for various welding tasks.
Key Features:
-
Ease of Use: Flux core wire is easy to work with, especially for beginners. It allows for quicker welds since you don’t need a separate shielding gas.
-
Penetration Capabilities: This wire provides deeper penetration into metals. This is essential for strong welds, especially on thicker materials.
-
Outdoor Suitability: Flux core welding wire is effective in windy or outdoor conditions, where shielding gas might be blown away.
Flux Core vs. Solid Wire
-
Flux Core Wire: Contains a flux that helps shield the weld, making it suitable for dirty or rusty metals.
-
Solid Wire: Requires an external shielding gas, which can be less effective in challenging environments.
Choosing the right wire is crucial for achieving high-quality welds. Flux core welding wire is a reliable option for various applications, including construction and repairs. This makes it valuable for both hobbyists and professionals.
Key Features of Flux Core Wires
When choosing flux core wire, understanding its key features is vital. Important factors include wire diameter, spatter management, tensile strength, and material compatibility. Each feature affects your welding results and ease of use.
✅ Wire Diameter and Its Impact
Wire diameter is a crucial aspect that influences your welding performance. Common sizes range from 0.030 inches to 0.045 inches. Thinner wires, like 0.030 inches, are ideal for welding thin materials, ensuring better control and precision.
On the other hand, thicker wires, such as 0.035 inches, provide deeper penetration, making them suitable for heavier metals. The right diameter helps you achieve a cleaner weld, minimizing defects. Be sure your chosen wire works with your welding equipment for optimal results.
✅ Spatter and Slag Considerations
Spatter occurs when molten metal splatters during the welding process. Some flux core wires are designed to produce low spatter, making cleanup easier. Look for wires that emphasize easy slag removal to streamline your post-welding process.
For instance, ARCCAPTAIN E308LFC-O Flux Cored wires often have features that limit spatter, promoting a smoother finish. Managing spatter and slag not only saves you time but also enhances the quality of your weld. Always prioritize wires that offer a balance between minimal spatter and strong weld integrity.
✅ Tensile Strength and Material Compatibility
Tensile strength measures how much force a weld can withstand before breaking. Flux core wires vary in strength, so it's essential to choose one that suits the materials you'll be welding. Many wires are compatible with carbon steel, galvanized, and painted surfaces.
Check the specifications of flux core wires like E71T-11 or others designed for versatility. Their tensile strength ensures that your welds maintain integrity under pressure. Using the right wire for your specific project also enhances material compatibility, ensuring strong results across different applications.
How to Choose the Best Flux Core Welding Wire?

When selecting flux core welding wire, you should consider several key factors.
✔️ Wire Diameter:
The diameter of the wire affects your welding results. Common sizes include:
- 0.030 inches: Best for thin materials.
- 0.035 inches: Suitable for thicker materials.
✔️ Material Compatibility
Make sure the wire matches the material you are welding.
- Carbon Steel: Most common for general purpose.
- Stainless Steel: Use specific flux core wire designed for stainless.
✔️ Amperage Range
Check your welding machine's capabilities. The wire needs to fit the amperage you can operate at. For thicker materials, you will need a wire that handles higher amps.
✔️ Brand Reputation
Look for trusted brands known for quality, such as ArcCaptain, INETUB, and Lincoln Electric. Good brands often provide reliable performance and safety.
✔️ Flux Type
Consider whether you need gasless flux cored wire. This type can be useful for outdoor work, as it is less affected by wind.
Top 3 Best Flux Core Welding Wires in 2024
- Arccaptain E71T-GS Flux Core Wire 2 Lbs
- ARCCAPTAIN E308LFC-O Flux Cored Wire
- ARCCAPTAIN E71T-GS 10 Lbs Flux Core Welding
When choosing the right flux core welding wire, you should consider factors like material compatibility, diameter, and wire weight. The following top picks have proven to deliver great performance for various welding tasks.
1. Arccaptain E71T-GS Flux Core Wire 2 Lbs

The Arccaptain E71T-GS flux core wire is ideal for welding mild steel. This 2-pound spool features a .033-inch diameter, making it suitable for thinner materials.
Key Features:
- Precision Manufacturing: Offers reliable welds with minimal spatter.
- Versatile Use: Works well on both clean and slightly rusty metal.
- Easy Handling: Lightweight and user-friendly for beginners.
This wire is great for small to medium projects, providing strong penetration and a clean finish. It's perfect for those who are just starting out or tackling DIY repairs.
2. ARCCAPTAIN E308LFC-O Flux Cored Wire

👉 Buy 🛒: ARCCAPTAIN E308LFC-O Flux Cored Wire
For welding stainless steel, the ARCCAPTAIN E308LFC-O is an excellent choice. It is designed to handle challenging environments, ensuring high-quality welds.
Key Features:
- Corrosion Resistance: Ideal for outdoor and corrosive settings.
- Ductile Welds: Creates strong, flexible joints that withstand stress.
- Smooth Feed: Designed for seamless feeding into the welder.
This flux cored wire helps achieve clean and consistent welds on stainless steel. It's a reliable option for both automotive and construction applications.
3. ARCCAPTAIN E71T-GS 10 Lbs Flux Core Welding

If you need a larger spool, the ARCCAPTAIN E71T-GS 10 Lbs option is a great choice, giving you more welding time between changes. This wire also has a .033-inch diameter for versatility.
Key Features:
- Longer Run Time: Perfect for larger projects or continuous welding.
- High Penetration: Delivers strong welds even on thicker materials.
- Easy to Clean: Reduces post-weld cleanup time.
This option is excellent for professionals and hobbyists alike, making it ideal for fabrication work or extensive repairs. For more information, you can explore additional options for flux core welding wires.
Comparison Table of the Best Flux Core Welding Wires
Flux Welding Wires |
Wire Diameter |
Material Compatibility |
Price |
Price |
E71T-GS Flux Core Wire |
0.8 mm |
Carbon Steel Ideal for shaft buildup, tanks, truck bodies, and general shop tasks |
$39.9 |
![]() |
E71T-GS 10 Lbs Flux Core Wire |
0.8mm Spool - D100 |
Spool Gasless Carbon Steel
|
$15.99 |
![]() |
E308LFC-O Flux Cored Wire |
0.8 mm |
Stainless Steel
|
$29.99 |
![]() |
How to Use Flux Core Welding Wire Effectively?
Using flux core welding wire requires attention to detail for the best results.
- Adjust Your Settings:
- Polarity: Most flux core wires are DC+ (direct current electrode positive).
- Wire Feed Speed: Set it according to the thickness of the material. Use faster speeds for thicker materials and slower speeds for thinner ones.
- Choose the Right Stickout:
- Maintain a stickout of about ¾ inch for optimal performance. This length helps in getting a good arc.
- Maintain Your Work Angle:
- For flat welds, hold your gun at a 90-degree angle. Adjust your travel angle between 5 to 15 degrees to control the weld pool.
- Keep a Secure Ground:
- Ensure your ground connection is solid. This connection helps complete the welding circuit, which is critical for effective welding.
- Practice Smooth Motion:
- Use short, side-to-side motions while welding. This technique helps direct the molten metal precisely into the joint.
- Clean Your Material:
- Remove any rust, paint, or contaminants before you start welding. Clean surfaces help achieve better penetration and bonding.
- Monitor Your Heat:
- Too much heat can cause burn-through, while too little can lead to weak welds. Adjust your welding current based on your material thickness.
Understanding Wire Specifications and Classifications
Wire specifications and classifications are essential to choosing the right flux-cored wire for your welding projects. Different types of wires serve specific purposes and requirements, affecting the overall quality and strength of your welds.
Overview of Common Wire Classifications
When selecting flux-cored wire, you'll encounter several classifications. The most common are E71T-1, E71T-11, E71T-GS, and E71T-8. Each code provides specific details about the wire.
- E71T-1: This is a gas-shielded wire used for a variety of applications. It provides good arc stability and minimal spatter.
- E71T-11: This self-shielded wire offers versatility for outdoor and indoor welding. It works well in windy conditions.
- E71T-GS: This is also self-shielded and is ideal for thin materials and general fabrication.
These classifications help you identify the wire's specific usage, such as tensile strength and shielding method.
Gas-Shielded vs Self-Shielded Wires
Gas-shielded and self-shielded wires differ mainly in their protection during the welding process.
-
Gas-Shielded Wires: These require an external gas supply, usually a mixture of argon and carbon dioxide (CO2). They produce less spatter and offer a cleaner weld. Examples include E71T-1C.
-
Self-Shielded Wires: These do not need any external gas. They generate their gas through a flux core, making them suitable for outdoor projects. E71T-11 is a popular choice for such tasks.
Selecting Wire for Structural Applications
When working on structural projects, the choice of wire is crucial for safety and strength.
- Use E71T-1 for robust applications requiring solid welds and structural integrity.
- For thin metals, E71T-GS may be appropriate as it allows for better control and minimizes heat distortion.
Check the thickness of the materials you will weld to select the proper wire size. Common sizes include .035 inches and .045 inches. Always consider the project requirements, as using the right wire enhances durability and performance.
Conclusion
To wrap up, choosing the right flux core welding wire is essential for creating strong and clean welds. The three options we discussed are some of the best on the market, each offering unique benefits to help you achieve great results in your welding projects. Remember, using high-quality wire can make a big difference in the strength and appearance of your welds.
If you’re ready to take your welding skills to the next level, check out ArcCaptain Welders. They offer a variety of MIG, TIG, and Stick welders along with high-quality flux core wire. Start your welding journey today and see the difference for yourself!
📖 Related Articles to Read:
- FCAW vs. GMAW: Understanding the Key Differences in Welding Techniques
- How to Get the Strongest Flux-Core Weld
- Can You Weld Aluminum with Flux Core?
Frequently Asked Questions
This section addresses common inquiries that can help you choose the right wire and application for your welding needs.
Which flux core welding wire is best?
The best flux core wire depends on your project. For general use, the PGN Flux Core E71T-11 is popular for its low splatter and efficiency. Arccaptain E71T-GS Flux Core Wire is also highly rated for providing neat beads.
What is the best use for flux core welding?
Flux core welding is ideal for outdoor projects and thicker materials. It works well on steel and can fill gaps effectively. Some types are also self-shielding, making them great for windy conditions.
What is the thickest flux core wire?
The thickest common flux core wire is typically .045 inches in diameter. This size is suitable for welding thicker metals and provides strong penetration. It is often used in industrial applications.
Does flux core make strong welds?
Yes, flux core welding can produce strong welds. The flux inside the wire helps shield the molten weld pool, creating a strong bond. Proper techniques and settings enhance the strength of your weld.
Is flux core stronger than MIG?
Flux core welding can be stronger than MIG in certain situations. It is better for thicker materials and outdoor conditions. However, MIG welding generally provides cleaner and more precise welds for thinner metals.
How thick can I weld with flux core?
Flux core wire allows you to weld materials up to half an inch thick. The thicker the wire diameter, the more penetration you'll get. Always choose the wire diameter based on the type of material and project requirements.