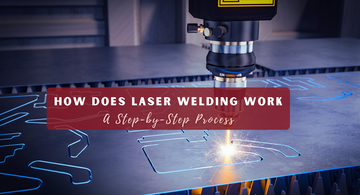
How does laser welding work? It’s a high-tech process that uses a focused laser beam to melt and fuse metal parts, creating strong, precise, and clean welds.
Popular in automotive, aerospace, and electronics, laser welding works faster than traditional methods with minimal heat distortion, making it ideal for delicate materials.
But what sets laser welding apart from other welding techniques?
In this article, we will break down the laser welding process, explore its various modes, and examine why it has become a preferred solution in modern manufacturing.
What Is Laser Welding?
Laser welding is a process that joins materials, usually metals, using a concentrated laser beam. This technique creates a precise and strong connection between pieces.
It is highly effective in industries needing accurate welds, like automotive and medical devices.
Key Features:
- Precision: Laser welding offers high accuracy, making it perfect for small parts.
- Strength: The welds can be as strong as or stronger than the original materials.
- Clean Process: It is non-contact, reducing contamination risks.
- High Temperatures: The laser can reach temperatures over 3,000°C, melting the metal quickly.
Laser welding is often used where quality and speed are crucial. It suits various industries, including aerospace and electronics, due to its efficiency and reliability.
Key Components of a Laser Welding System
A laser welding system is made up of several key components working together for precision and efficiency.
→ Laser Source: The laser source is crucial as it produces the laser beam. You can find different types like Fiber, CO₂, or Nd lasers. Each type has unique benefits and is chosen based on specific welding needs.
→ Beam Delivery System: This system uses optics, mirrors, and lenses to guide the laser beam to the exact spot on the workpiece. High precision is critical, making this component essential for accurate welding results.
→ Workpiece Fixture: Keeping materials steady is vital during welding. A workpiece fixture ensures that parts stay aligned and secure, leading to better weld quality and consistency.
→ Cooling System: The laser and associated equipment can generate a lot of heat. A cooling system helps regulate the laser's temperature, preventing overheating and equipment damage.
It's essential for maintaining performance and extending the lifespan of the system. Learn more about its importance in laser welding machines.
Understanding these components can help you appreciate how a laser welding system functions and why each part is vital for successful welding operations.
How Does Laser Welding Work? Step-by-Step Process
Laser welding is a fast and precise method that uses a concentrated laser beam to join metals.
Unlike traditional welding, it minimizes heat damage and often doesn’t require filler material.
Here’s a simple breakdown of how it works:
Step 1 - Positioning the Materials
Before welding begins, the metal pieces must be carefully positioned. This is done using fixtures or automated systems to ensure perfect alignment.
A laser welding machine then directs a highly focused beam onto the joint area with pinpoint accuracy.
Automated setups can control the laser’s path, speed, and intensity based on the material type and thickness.
Step 2 – Melting the Metal
When the laser beam hits the metal surface, it generates intense heat almost instantly, raising the temperature to the metal’s melting point.
Unlike traditional welding, which spreads heat over a larger area, laser welding keeps the heat focused, reducing warping and distortion in surrounding material.
Step 3 – Fusing the Materials
As the metal melts, a molten pool forms at the joint. The laser moves along the seam, continuing to melt the material and fusing the pieces together at a molecular level.
To prevent contamination, a shielding gas (such as argon or helium) is used to keep the molten metal clean and free from oxidation.
Step 4 – Solidification & Final Weld
Once the laser moves forward, the molten pool cools and solidifies quickly, creating a strong, smooth, and durable weld.
Since laser welding limits heat exposure, the surrounding material remains intact, making it ideal for precision jobs that require minimal distortion.
This highly efficient process allows for strong, clean welds, making laser welding a top choice in industries that demand accuracy and strength.
Types of Laser Welding & Their Applications
Laser welding encompasses two primary methods, each tailored to specific applications:
1. Conduction Mode Welding
- Best for: Thin materials and surface welding.
- How it works: The laser beam heats the material's surface, causing melting without deep penetration. This method is ideal for delicate tasks requiring precision, such as electronics assembly and welding thin metals. It produces smooth, aesthetically pleasing welds, often eliminating the need for additional finishing.
2. Keyhole (Deep Penetration) Welding
- Best for: Thick materials requiring robust, deep welds.
- How it works: The laser beam creates a small, vapor-filled cavity or "keyhole" in the material, allowing for deep penetration and the formation of strong joints. This technique is commonly employed in industries where material thickness is substantial, such as shipbuilding and automotive manufacturing. It enables deep, narrow welds essential for structural integrity.
Conduction Mode vs. Keyhole Welding
When using laser welding, you can select between conduction mode and keyhole welding. Each mode has its unique features and applications.
Conduction Mode
In conduction mode, the laser heats the surface, melting the material. This mode is optimal for thin materials because it ensures precision without deep penetration. The heat gradually spreads into the material, resulting in wider, shallow welds.
Keyhole Welding
Keyhole welding creates a small hole, or keyhole, in the material. The laser's high energy density causes the metal to vaporize, allowing for deep penetration. This method is perfect for thick, high-strength materials, providing strong and efficient welds.
Comparison Table
Feature |
Conduction Mode |
Keyhole Welding |
Heat Source |
Surface heating |
Vaporization and keyhole formation |
Depth |
Shallow |
Deep |
Material Suitability |
Thin materials |
Thick, high-strength materials |
Precision |
High |
Moderate |
Each mode has its advantages. Choose conduction mode for delicate and thin applications, like electronics. Opt for keyhole welding for robust, deep joints in heavy-duty jobs.
Understanding these modes helps you decide which method suits your project.
Both approaches offer unique benefits, ensuring you can achieve the desired weld quality for different applications.
Pulsed vs. Continuous Laser Modes
When it comes to laser welding, you can choose between pulsed and continuous laser modes. Each mode has its own strengths and is suited for different applications.
Pulsed Laser Mode
- Ideal for delicate and reflective materials.
- Works by creating bursts of energy, allowing you precise control.
- High peak power in each pulse helps to manage heat, reducing the risk of damage.
- Useful in small, intricate welding tasks where control is important.
Continuous Laser Mode
- Best for high-speed projects.
- Keeps the laser on continuously, producing deep welds.
- Suitable for thicker materials because it can maintain a steady heat flow.
- Commonly used when you need faster processing and larger weld areas.
Both modes play a vital role in different types of laser welding projects. Pulsed lasers are great for precision, whereas continuous lasers are better for speed and depth. Choose the mode that fits the materials and requirements of your project.
Advantages of Laser Welding
1. High Precision & Minimal Distortion
Laser welding provides high precision, which is especially useful for delicate parts. This method helps in minimizing warping and distortion. It's often used in micro-welding applications such as medical devices and electronics.
2. Faster Welding Speeds
Compared to methods like TIG or MIG welding, laser welding is significantly faster. The focused energy allows you to reduce production time and increase efficiency. This can greatly enhance your workflow and productivity.
3. Stronger Welds with Less Material Usage
Laser welds are known for being more durable due to their deep penetration capabilities. You can achieve strong joints while requiring minimal filler material. This not only ensures sturdy welds but also reduces costs related to material usage.
4. Automation & Robotics Compatibility
You can easily integrate laser welding into automated production lines. This makes the process compatible with robotics, reducing labor costs and improving consistency in production. Embracing this technology can streamline your operations.
Utilizing laser welding provides numerous benefits that improve both the quality and efficiency of your projects.
Common Challenges & How to Overcome Them in Laser Welding
1. Reflection & Absorption Issues
When welding highly reflective materials like aluminum, laser energy reflection can reduce efficiency. To tackle this, use fiber lasers with shorter wavelengths to improve absorption. This adjustment makes the process more effective.
2. Thermal Cracking & Porosity
Excessive heat during welding can lead to cracks or pores in the weld. You should optimize power settings and use proper shielding gas to prevent these issues. This helps maintain the integrity and strength of the weld. (Also Read: What is Porosity in Welding)
3. High Initial Investment Cost
The cost of laser welding machines is higher compared to traditional welders. Although the initial investment is significant, you can save on labor and material costs over time. This can make laser welding a worthwhile investment in the long run.
Table: Quick Solutions for Common Laser Welding Problems
Challenge |
Solution |
Reflection & Absorption Issues |
Use fiber lasers with shorter wavelengths |
Thermal Cracking & Porosity |
Optimize power and use proper shielding gas |
High Initial Investment Cost |
Consider long-term savings in costs |
These steps can help you tackle common challenges in laser welding effectively.
Final Thoughts
Laser welding is a powerful and precise technique that delivers high-quality, durable welds with minimal heat distortion. It is widely used in industries requiring accuracy, speed, and automation.
However, its advanced technology comes with a higher cost, making it less accessible for small-scale or DIY projects.
If laser welding is beyond your budget, traditional welding methods like MIG, TIG, or Stick welding offer reliable and cost-effective alternatives.
Explore our range of welding machines designed for DIY enthusiasts and professionals alike—perfect for achieving strong, clean welds without the high investment of laser technology.
Master Your Welding Craft with Our Professional Welding Machines
|
Arccaptain MIG200 Multi Process MIG Welder
The MIG200 is ARCCAPTAIN's best-selling multi-process All in 1 MIG Welder. Whether you're a beginner or a professional welder, this machine meets all your welding project needs.
|
Arccaptain TIG200P AC DC Multi Process Pulse TIG Aluminum Welder
The AC DC TIG200P is our most powerful, best-selling, and top-rated high-performance Pulse Aluminum TIG Welder, highly recognized for its exceptional performance in aluminum welding and thin plate welding projects.
|
|
Arccaptain MIG205 Pro Multi Process MIG Welder
The MIG205 Pro features enhanced welding capabilities, localized screen language options, and improved heat dissipation for a smoother, more efficient welding experience.
|
Frequently Asked Questions
You're likely curious about the technicalities of laser welding. From gas usage and material strength to cost and compatibility with various materials, this process has several aspects worth understanding.
Does Laser Welding Need Gas?
Yes, laser welding often requires a shielding gas to protect the weld area from contamination. Common gases used include argon, helium, and nitrogen. The shielding gas helps ensure a clean, high-quality weld by preventing oxidation and other impurities.
Is Laser Welding Stronger Than Traditional Welding?
Laser welding can be stronger than traditional welding methods due to its precision and control. It produces narrow, deep welds with minimal distortion and heat-affected zones. This results in high-strength joints, especially in materials that are difficult to weld using conventional methods.
How is Laser Welding Different From TIG Welding?
Laser welding uses a concentrated laser beam to melt and join materials, while TIG welding uses an electric arc and a tungsten electrode. Laser welding offers higher precision and speed, with less heat input and distortion. TIG welding, however, provides more control over the weld pool and is better suited for thicker materials and complex joints.
Is Laser Welding Expensive?
Yes, laser welding can be expensive due to the high cost of laser equipment and maintenance. However, its efficiency, precision, and ability to produce high-quality welds can justify the investment in certain applications. Over time, the benefits may outweigh the initial costs, especially in high-volume or specialized manufacturing.
What Materials Can Be Laser Welded?
Laser welding can be used on a wide range of materials, including steel, stainless steel, aluminum, titanium, and various alloys. It is also effective on dissimilar materials, making it versatile for many industrial applications. The ability to weld different materials with precision makes laser welding a valuable technique.
Does Laser Welding Require Filler Material?
Laser welding does not always require filler material. Many laser welding applications use autogenous welding, where the materials are fused directly without additional filler. However, filler material can be used if needed to fill gaps or add strength to the weld joint.