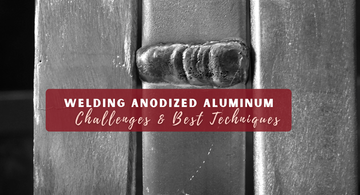
Welding anodized aluminum is challenging because the anodized layer acts as a barrier, making it harder for the weld to bond properly.
This protective oxide coating improves corrosion resistance and appearance but interferes with the welding process.
To get clean, strong welds, you must first remove the anodized coating from the areas you plan to weld.
If you're new to welding or looking to refine your technique, understanding the best methods for welding anodized aluminum is essential.
Keep reading to discover which techniques work best and how to achieve high-quality welds.
What Is Anodized Aluminum and Why Is It Difficult to Weld?
Anodized aluminum is created through a special process that makes it more resistant to corrosion and adds a hard, attractive surface. This process also makes the aluminum tricky to weld due to a non-conductive layer that forms.
How Anodization Affects Aluminum’s Properties
Anodization is a process that uses electricity to boost aluminum’s resistance to rust. This treatment results in a thick layer of aluminum oxide that does not conduct electricity.
This layer protects the aluminum but complicates welding. The non-conductive surface makes it hard to start and maintain an electric arc, which is needed for welding.
The oxide layer also creates a barrier that can weaken weld strength if chipped or broken.
Advantages & Disadvantages of Anodized Aluminum
Advantages:
- Corrosion Resistance: Anodized aluminum lasts longer against rust.
- Aesthetic Appeal: It has a uniform, attractive surface.
- Increased Surface Hardness: It's tougher, which prevents scratches.
Disadvantages:
- Harder to Weld: The oxide layer makes this more challenging.
- More Prone to Contamination: Dirt and oils can easily affect the welding area.
Why Welding Anodized Aluminum Is More Challenging Than Bare Aluminum
The oxide layer on anodized aluminum acts as a barrier during welding. This layer can hinder the initial arc needed to start welding.
Aluminum is sensitive to heat, so it must be carefully managed to avoid warping or uneven welds. If there is contamination, it can lead to weak welds that may have holes or be porous.
These issues make it more complex than welding bare aluminum.
How to Prepare Anodized Aluminum for Welding
Preparing anodized aluminum for welding demands careful attention to detail. You will need to remove the oxide layer, clean the surface thoroughly, and select the appropriate filler material for optimal results.
Step 1 – Removing the Oxide Layer Before Welding
Removing the oxide layer is essential because it has a higher melting point than aluminum, making welding challenging.
Start by using mechanical methods like a wire brush, flap disc, or sanding to grind off the anodized coating. These techniques are effective for large areas.
For more precise removal at the weld joint, consider chemical stripping using acid or alkaline solutions.
This method allows for targeted removal, ensuring only the necessary oxide is eliminated without affecting the surrounding metal.
Localized removal can be very advantageous when accuracy is crucial.
Step 2 – Cleaning the Surface to Avoid Contamination
Once the oxide layer is removed, cleaning the surface is vital to prevent contamination. Use acetone or alcohol-based solvents to wipe away any grease, oil, or dirt.
These substances can cause welding problems like porosity and weak welds.
Ensure that the aluminum surface is completely dry before starting the welding process.
Moisture can lead to defects, so double-check that no water is left after cleaning.
Proper cleaning sets the stage for a successful weld, free from impurities and defects.
Step 3 – Choosing the Right Filler Material
Choosing the right filler material is the last crucial step. For strength and a good color match, use a 5356 aluminum filler rod. This material is widely recommended for its reliability in welding anodized aluminum.
If you need better corrosion resistance, options like 4045 or 4047 aluminum fillers are suitable choices.
The correct filler material ensures that your weld is not only strong but also durable against environmental conditions.
Selecting the appropriate filler completes your preparation, paving the way for robust and effective welding.
Related Product:
ARCCAPTAIN ER4043 Aluminum Welding Wire 1 Pound Aluminum MIG Wire
ARCCAPTAIN ER4043 Aluminum Welding Wire offers a smooth and stable arc, ensuring easy control and an excellent weld bead appearance. This high-quality aluminum welding wire is perfect for both professionals and hobbyists seeking superior results.
|
Also Read: 🔗 What Welding Rod Should You Use For Your Project?
Best Welding Methods for Anodized Aluminum
When welding anodized aluminum, certain methods offer better precision and control. Choosing the right approach depends on factors like thickness, desired quality, and equipment.
TIG (GTAW) Welding – The Best Option for Anodized Aluminum
TIG welding stands out due to its precision and ability to produce high-quality welds. It's preferred for anodized aluminum because it allows you to precisely control the heat, ensuring clean results.
🛒 Arccaptain TIG200P AC DC Multi Process Pulse TIG Aluminum Welder
Key settings include using AC mode with a high-frequency start, which helps maintain a stable arc. Opt for a pure tungsten or zirconiated tungsten electrode and set the balance control to enhance cleaning action. This setup helps remove aluminum oxide, yielding a smoother weld.
MIG (GMAW) Welding – Faster but Less Precise
MIG welding can be efficient for thicker anodized aluminum parts. It requires a spool gun and argon for shielding gas to minimize contamination.
🛒 Arccaptain MIG250 MIG TIG Stick Welder Aluminum Welding Machine
Important settings involve using the push technique, which helps reduce the risk of contamination in your weld. Spray transfer mode is recommended for better penetration and ensures a stronger bond. While faster, this method may lack the refined finish achievable with TIG welding.
Why Stick Welding (SMAW) & Laser Welding Are Not Ideal?
Stick welding generally leads to excessive contamination and poor weld quality on anodized aluminum. It lacks the precision required for a clean finish.
On the other hand, laser welding offers precision but is expensive and demands very precise control and setup.
Due to these drawbacks, both methods are less favorable compared to TIG and MIG for welding anodized aluminum effectively.
Common Mistakes and How to Avoid Them When Welding Anodized Aluminum
☓ Welding Over Anodized Coating: The anodized layer is an electrical insulator and can make it difficult to maintain a stable arc.
⋆ Solution: Remove the anodized coating in the welding area before starting. This ensures better conductivity and a smoother weld.
☓ Improper Surface Cleaning: Dirt and contaminants can ruin your welds.
⋆ Tip: Always clean the surface thoroughly with a suitable solvent. A clean surface helps prevent weak bonds and improves weld quality.
☓ Using Inappropriate Filler Material: Wrong filler materials might not bond well with anodized aluminum. Make sure to use a filler that is compatible with the aluminum alloy you are working on to avoid weld failure.
☓ Overheating: Overheating can warp the metal and crack the weld. Watch your heat levels and adjust welding parameters as needed to keep the temperature in check.
☓ Wrong Welding Techniques: Some techniques aren't ideal for anodized aluminum. Practice using techniques suited for this type of material to achieve better results. Using the right method reduces errors and improves the strength of your welds.
Key mistakes include failing to remove anodized layers and allowing contaminants to impact the weld. Adhering to these tips will help you avoid common errors. Adapt your process with these strategies to achieve a clean, durable weld.
FAQs About Welding Anodized Aluminum 💬
Welding anodized aluminum can be challenging but doable with the right techniques and tools. Understanding these can make a significant difference in the quality and durability of your weld.
Can you weld anodized aluminum without removing the anodized layer?
Welding anodized aluminum without removing the anodized layer is challenging and not recommended. The anodized layer is non-conductive and can cause poor weld quality and contamination. It is best to remove the anodized layer in the weld area to ensure a clean and strong weld.
What is the best welding method for anodized aluminum?
The best welding method for anodized aluminum is Tungsten Inert Gas (TIG) welding. TIG welding provides precise control over the heat and allows for clean, high-quality welds. It is especially effective when the anodized layer is removed before welding.
How do you restore the anodized finish after welding?
To restore the anodized finish after welding, you need to clean the welded area and then re-anodize it. This involves removing any contaminants, polishing the surface, and then applying an anodizing process. The re-anodizing will restore the protective and aesthetic properties of the aluminum.
Which type of tungsten is recommended for welding aluminum?
For welding aluminum, pure tungsten or zirconiated tungsten electrodes are recommended. These types of tungsten provide stable arc performance and are suitable for the alternating current (AC) used in aluminum welding. They help achieve clean and strong welds on aluminum materials.
Does anodizing weaken aluminum for welding?
Anodizing does not inherently weaken aluminum, but the anodized layer can complicate the welding process. The non-conductive anodized layer must be removed before welding to ensure a proper weld. Once the anodized layer is removed, the aluminum can be welded effectively without compromising its strength.
What is the best filler rod for anodized aluminum?
The best filler rod for welding anodized aluminum is typically a 4043 or 5356 aluminum filler rod. 4043 is known for its good flow characteristics and reduced cracking, while 5356 offers higher strength and better corrosion resistance. The choice depends on the specific requirements of the welding project.