What Welding Rod Should You Use For Your Project? Factors to Consider
May 06, 2024
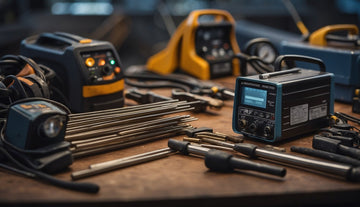
Picking the right welding rod is key to a strong and good-looking weld. It's the piece that melts to join two metals together. The kind of metal you're working with, where you're welding, and what you want the weld to handle play into which rod you should use.
There are loads of different rods, each made for certain jobs—some for everyday welding, others for really tough stuff, or special kinds of metal. Each rod has a code that tells you what it's best for.
Want to know which rod is right for your project? Keep reading to find out more about welding rods.
Electrode Classification and Usage
Selecting the right welding rod is crucial for project success, and understanding electrode classification and usage is pivotal. This section offers detailed guidance on decoding electrode labels, differentiating between electrode types, and matching electrodes to various metals for optimal performance.
Also read our guide:
Understanding Electrode Coding
The American Welding Society (AWS) classification system is a critical tool for identifying welding rods.
Each welding rod number holds specific information about the electrode's characteristics.
For example, a 6010 electrode means:
- 6: Tensile strength of 60,000 psi
- 1: All position welding capability
- 0: Type of coating and current used
The last two digits indicate usability and penetration.
Other common classifications like 6011, 6012, and 6013 adapt to different welding conditions and materials, such as mild steel or low carbon steel.
A 7018 rod, known for its high tensile strength and low hydrogen content, is crucial for welding components subjected to high stress.
Comparing Consumable and Non-Consumable Electrodes
In welding, electrodes are either consumable or non-consumable:
-
Consumable Electrodes are melted during the welding process to form a bond, commonly used in Shielded Metal Arc Welding (SMAW), or stick welding. Examples include the 6010 and 7018 rods.
-
Non-Consumable Electrodes do not melt and are primarily used in Tungsten Inert Gas (TIG) welding.
The Tungsten electrode color codes indicate various properties, such as:
- Green: Pure tungsten
- Red: Thoriated tungsten
Selecting Electrodes for Different Metals
Choosing the correct electrode for the base metal is fundamental:
-
Steel: 6010 and 7018 electrodes are suitable for welding steel, providing deep penetration or low hydrogen qualities accordingly.
-
Aluminum: Requires electrodes with specific coatings to manage its oxide layer and higher conductivity.
-
Cast Iron: Often welded using a nickel-based electrode to accommodate its brittle nature.
-
Stainless Steel Electrodes: Identified by the 'L' or 'H' in their classification, which stands for low or high carbon content. This is essential to match the electrode's composition with the stainless steel grade being welded.
Technical Aspects of Welding Rods
Choosing the right welding rod is crucial for achieving a strong and durable weld. This choice is influenced by technical aspects which include the welding current, rod coating, and the relationship between rod size and amperage.
Analyzing Arc Welding Current Types
Arc welding requires a specific type of current; either alternating current (AC) or direct current (DC).
Electrodes such as 6010 welding rods are designed for use with DC and deliver deep penetration.
In contrast, 6011 electrodes can be used with both AC and DC, offering greater versatility.
The choice impacts the stability of the arc and subsequent weld quality.
Examining Coating Types and Thickness
Electrode coatings play a vital role in stabilizing the arc and adding substances to improve the weld.
7018 electrodes are coated with low-hydrogen flux that prevents hydrogen cracking and is suitable for various welding positions.
Meanwhile, 7024 electrodes have a thicker flux coating, enhancing the deposition rate, especially in horizontal or flat welds.
Coatings may contain cellulose sodium for deep penetration or titania potassium for a cleaner weld surface.
Influence of Rod Size and Amperage on Welding
The size of the electrode diameter and the required amperage are interdependent.
Selecting the proper rod size is essential for achieving the desired heat and penetration levels:
- Electrode Diameter: Smaller diameters (e.g., 1/16 inch) require lower amperage and are suitable for thin metals, while larger diameters (e.g., 1/4 inch) need higher amperage for thicker materials.
- Amperage: Corresponds to the rod size, dictating the welding power source's setting to create an efficient weld. For example, a 1/8 inch 7018 rod typically operates between 90-150 amps.
Functional Considerations
When selecting a welding rod, consider how your choice affects the weld's functionality. Material compatibility, welding position, and environmental factors play pivotal roles in achieving a reliable and efficient weld.
Welding Positions and Rod Selection
Choosing the appropriate welding rod is essential for your project's success, as not all rods are suitable for every position.
- Flat Position: Most welding rods are compatible with the flat position, providing ease of use and control.
- Horizontal Position: Rods used here need to create a strong weld despite gravity's influence, like E7018.
- Vertical Position: Requires rods that produce a fast-freezing weld pool, such as E6011 rods, to prevent sagging.
- Overhead Position: Choose a rod with a fast-freezing slag, like the E6010, to minimize spatter while welding overhead.
These positions correspond to specific electrode angles and directions of welding, calling for precise rod characteristics for optimal fusion.
Read more of this: 4 Basic Types of Welding Positions
Addressing Different Joining Applications
Welding rods must be selected based on the specific joining application to ensure proper fusion and strength.
- Fillet Weld: Calls for electrodes that guarantee sound joint geometry and thorough penetration.
- Pipe Welding: Often requires a rod capable of producing X-ray quality welds, like a low-hydrogen E7018.
- Pressure Vessel: High tensile strength rods are necessary to withstand extreme pressures.
- Joint Fit-Up: Requires rods that can handle variations in gap and alignment.
Ensure the welding rod's mechanical properties align with the application's demands to avoid failure.
Understanding Mechanical and Chemical Properties
The mechanical and chemical properties of welding rods are crucial for the durability and integrity of the weld.
- Tensile Strength: An electrode should match or exceed the base metal's tensile strength.
- Ductility: Electrodes must be flexible enough to allow for expansion and contraction without cracking.
- Base Metal Properties: The welding rod should complement the base metal chemically and mechanically.
Consider specific terms like penetration and heat input, as they directly affect the weld’s structural performance.
Managing External Factors and Contamination
To ensure a high-quality weld, it's vital to manage external factors and potential sources of contamination.
- Surface Preparation: Remove rust, oil, dirt, moisture, paint, and mill scale to prevent imperfections.
- Temperature: Use rods like low-hydrogen types in cool environments to prevent moisture absorption leading to hydrogen cracking.
- Contaminants: Magnetism and oxidation can adversely affect the weld quality, necessitating careful preparation and appropriate rod selection.
Proper selection of flux can help manage spatter and protect against contamination that could weaken the weld.
Rod and Material Storage
When storing your welding rods, there are specific conditions you must consider to ensure their longevity and readiness for future use:
- Moisture Control: Store your electrodes in a dry environment. Moisture is the enemy of welding rods as it can lead to hydrogen-induced cracking in your welds.
- Moisture Control: Use airtight containers with desiccants or invest in a rod oven if humidity is a concern.
- Temperature Regulation: Avoid extreme temperatures.
- Temperature Regulation: Welding rods should be stored at a consistent temperature to prevent the flux from becoming brittle or the rod from warping.
- Organization: Organize your rods by material and type. This prevents accidental use of the wrong electrode for a job, which can affect weld quality.
- Organization: Use labels or color-coding for easy identification.
- Inventory Management: Keep an inventory of your electrodes. Knowing what you have on hand can prevent wastage and unnecessary purchases, saving time and resources.
- Inventory Management: Update your inventory regularly.
- Manufacturer Guidelines: Always consult the manufacturer’s recommendations for specific storage instructions. Each type of electrode may have unique requirements.
Conclusion: How Do You Know Which Welding Rod To Use?
The right welding rod is essential for a strong and lasting weld. Factors like the base metal, weld position, and desired weld properties are key in choosing the best rod. Knowing the different rod types is crucial for any welding project.
Welding rods do more than fill gaps; they're pivotal for weld integrity. Each rod type is coded to help you make an informed choice, whether you're welding common materials or specialized alloys.
For those looking to source high-quality electrodes for their next welding endeavor, we recommend exploring the selection available from Arc Captain. Ready to gain deeper insights and find the ideal rod for your project? Explore Arc Captain's welding products today.
Frequently Asked Questions
What size of welding rod is for general use?
For general use, a welding rod with a diameter of 1/8 inch (3.2 mm) is commonly utilized due to its versatility. This size is suitable for a range of different welding tasks, including work on medium gauge metals. It offers a balance between ease of control for the welder and adequate filler metal for the joint.
How can you tell the difference between welding rods?
Welding rods can be distinguished by their AWS (American Welding Society) classification numbers, which are printed on the rod itself or its packaging. These numbers tell you about the rod's tensile strength, welding positions, type of flux coating, and suitable current types. For example, a 6011 rod would be different from a 7018 rod, with the first two digits indicating tensile strength and the last digit revealing the flux type and current usability.
What size rod is best for beginners?
Beginners often find that a 1/8 inch (3.2 mm) welding rod is a good starting point. This size is not too small or too large, making it easier to handle while still providing sufficient weld coverage on a variety of materials. Rods such as the 6013 are also beginner-friendly due to their smooth arc, easy slag removal, and all-position versatility.
What is the best welding rod for mild steel?
The 6010 and 6011 welding rods are typically recommended for mild steel. They provide deep penetration, which is great for creating strong welds on this type of metal. Additionally, for projects that require smoother welds with less penetration, a 6013 rod can be a good choice, offering an easier arc to control with a moderate penetration profile.