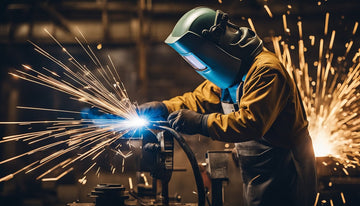
How many watts does a MIG welder use? It's a question that matters a lot for anyone using these tools, whether you're doing a quick repair at home or handling a big project at work. The power a MIG welder needs affects not just your electric bill but also how well it performs. Our blog is here to clear up the confusion about how much electricity these welders need and help you make smart choices about using and picking the right one.
Knowing the wattage of a MIG welder helps you do better work. In this post, we'll explain what you need to know about power and welding. You'll learn how choosing the right amount of power can mean the difference between a good weld and a great one. We're here to guide you through the specifics so you can weld confidently and cost-effectively. Let's get started and shed some light on the power needs of MIG welding.
Ready to power up your welding projects? Discover the perfect blend of performance and power in our MIG welder machine collection. Find your ideal MIG welder today!
Understanding MIG Welding and Power Basics
MIG welding, or Metal Inert Gas welding, relies on specific power requirements to function effectively. To achieve optimal results, understanding its principles and components is essential.
Principles of MIG Welding
MIG welding uses a continuous wire feed as an electrode, which melts and fuses the base materials upon electrical contact. This process operates through a combination of voltage and amperage.
- Voltage affects the arc length and heating capacity. Higher voltage typically results in a broader arc.
- Amperage controls the heat intensity. More amps provide deeper weld penetration.
The balance between these parameters is crucial for achieving strong, clean welds. Adjustments may be necessary depending on material thickness and type. Knowing how to manipulate these settings will enhance your welding performance and efficiency.
Components of a MIG Welder
A MIG welder consists of several key components that work together to deliver the necessary power for welding:
- Power Source: Supplies the required voltage and current.
- Wire Feed Mechanism: Provides a consistent flow of welding wire to the weld pool.
- Gun and Nozzle Assembly: Directs the arc and shielding gas to the weld area.
Additionally, shielding gas plays a vital role in protecting the weld from contamination. Common gases include argon and carbon dioxide. Your ability to configure these components will influence the overall effectiveness of your MIG welding setup.
Factors Influencing Power Usage
Power usage in a MIG welder is influenced by several critical factors, including the materials being welded and the settings you choose for voltage and amperage. Understanding these elements can help you optimize performance and efficiency.
Material and Thickness Impact
The type of material you are welding plays a significant role in power consumption. Different materials, such as steel, aluminum, and stainless steel, require varying energy levels for effective welding.
- Material Type: Softer metals may need less power compared to harder alloys.
- Thickness: Thicker materials demand higher heat input. For instance, welding a 1/4-inch steel plate requires more amperage than a 16-gauge sheet.
As the thickness of the material increases, you will likely adjust your welder's settings to ensure proper penetration. This change can significantly raise the wattage needed for effective welding.
Role of Voltage and Amperage Settings
Voltage and amperage settings are crucial parameters that dictate how much power your MIG welder will consume.
-
Voltage: Higher voltage settings can result in increased arc stability and penetration. A typical 240-volt MIG welder may draw significantly more power compared to a 120-volt model.
-
Amperage: The amperage settings directly impact heat generation. For example, running a welder at 200 amps draws about 4.6 kW, while a 150 amps setting uses around 3 kW.
In addition, selecting the appropriate wire size can also affect how much power you use. A larger diameter wire might require different settings, impacting both the voltage and amp consumption. Adjusting these parameters effectively ensures optimal performance while managing energy costs.
Determining the Power Requirements
Understanding the power requirements for your MIG welder is crucial for optimal performance. Factors such as the type of metal, its thickness, and the welder's settings will significantly influence the necessary wattage.
Using Charts and Guidelines
Using charts and guidelines helps you match the right amperage to your specific welding tasks. For example, consult amperage charts that often list appropriate settings for various materials:
Metal Type |
Thickness (inches) |
Amperage Range |
Steel |
0.030 - 0.125 |
30 - 200 amps |
Aluminum |
0.040 - 0.200 |
40 - 250 amps |
Stainless Steel |
0.030 - 0.125 |
40 - 180 amps |
You should ensure that your welder's output matches these requirements for effective results. Always consider using a safety margin for added voltage consistency.
Calculating For Different Materials
When calculating power requirements, consider the material you are working with. Each metal type demands different amperage, so proper calculations are vital.
For example, if welding mild steel at 0.125 inches thick, you may calculate:
- Amperage Needed: 150 amps (from the chart)
- Power Consumption: 150 amps x 220 volts = 33,000 watts.
For aluminum, if using 0.200 inches thickness at 200 amps, your calculation might look like this:
- Power Consumption: 200 amps x 220 volts = 44,000 watts.
Adapting settings based on the specific metal type and thickness will ensure efficient welding performance and minimize issues.
Operational Efficiency and Techniques
Achieving operational efficiency with a MIG welder involves fine-tuning various parameters such as wire feed speed, voltage, and travel speed. By optimizing these factors, you can enhance performance and produce higher quality welds while managing energy consumption effectively.
Optimizing Wire Feed Speed and Voltage
Wire feed speed and voltage settings are crucial for the quality of your welds. If the wire feed speed is too low, the weld will be weak and may lack penetration. Conversely, an excessive speed can lead to burn-through or poor bead appearance.
Recommended Settings:
- Wire Feed Speed: Typically ranges from 300 to 600 inches per minute (IPM).
- Voltage Settings: Commonly between 18 to 26 volts, depending on the thickness of the material.
To find the right balance, conduct test welds. Adjust voltage as needed while maintaining an optimal wire feed speed. Use a consistent travel speed to ensure uniform weld beads.
Advanced Welding Techniques
Incorporating advanced techniques can significantly improve the efficiency and quality of your welding projects. Techniques such as weaving, stringer beads, and controlling travel speed can make a difference.
Key Techniques:
- Weaving: Helps distribute heat evenly over wider joints.
- Stringer Beads: Suitable for thinner materials; keeps heat input minimal.
- Controlled Travel Speed: Faster travel speeds reduce heat input, minimizing distortion.
Adjust your amperage settings based on the material's thickness. Lower amperage is ideal for thin materials, while thicker materials require higher settings to ensure proper penetration. By mastering these methods, you can achieve stronger, cleaner, and more efficient welds.
Precision and control are at your fingertips. Elevate your welding experience with our premium MIG welding guns. Upgrade your MIG gun now!
Maintenance and Safety Considerations
Proper maintenance and adherence to safety protocols are essential for maximizing the efficiency and lifespan of your MIG welder. These practices also ensure quality welds and protect you from potential hazards during operation.
Routine Welder Maintenance
To maintain your MIG welder at peak performance, develop a regular cleaning and maintenance schedule. Start by disconnecting the power supply to ensure safety. Clean the interior components by using a dry air hose to remove dust and debris, particularly from the power supply and wire drive mechanism.
Check and replace worn components such as the regulator and hoses, as these affect your duty cycle and weld quality. Ensure that your welding gun is free of obstructions and clean the nozzle regularly to promote strong welds. Keeping your equipment clean also helps prevent overheating and extends its operational life.
Safety Protocols and Best Practices
Safety should always be your top priority while using a MIG welder. Wear protective gear including flame-resistant clothing, gloves, and a welding helmet with the appropriate filter shade to shield your face and eyes from sparks and UV rays.
Always inspect your welder and cables for signs of wear before starting work to prevent electrical hazards. When operating the welder, monitor sparks closely to avoid fire risks. Use screens or barriers to protect others near your work area. Additionally, make sure your workspace is well-ventilated to reduce exposure to harmful fumes generated during welding. These steps will help mitigate risks associated with welding.
Take your welding wherever you go with our versatile portable MIG welders. Unmatched convenience without compromising on power—Shop for portable MIG welders now!
Conclusion
Understanding the wattage of a MIG welder is crucial for welders at all levels to ensure efficiency and produce high-quality work. Being aware of your machine's power needs is not only beneficial for performance but also for managing energy costs effectively. It's clear that having the right information helps in selecting a welder that meets your needs and contributes to a smoother welding experience, whether you're a beginner or a pro.
If you're looking to enhance your welding capabilities with a machine that fits your specific requirements, we invite you to explore a curated selection of top-notch equipment. Visit our best welding machines collection and power up your next metalworking project with confidence and precision. The perfect weld starts with the perfect welder, and your journey to excellence begins here.
Frequently Asked Questions
What size generator do I need to run a MIG welder?
To run a MIG welder, you typically need a generator that can provide at least 5,000 watts of continuous power. This ensures that the welder has enough capacity for its start-up requirements and can run smoothly during operation.
Will a 5000 watt inverter run a welder?
A 5,000 watt inverter can run smaller MIG welders, especially those with lower amperage ratings. However, if your welder draws close to or exceeds this wattage, it may not operate efficiently or safely.
How many watts is a 110v welder?
A 110V MIG welder generally consumes between 1,000 to 1,800 watts, depending on its amperage rating. For example, a welder running at 15 amps would utilize about 1,800 watts.
How much power do I need to weld?
The power needed to weld depends on the thickness of the material and the type of welding performed. For most MIG welding applications, a machine that uses between 3,000 to 5,000 watts should suffice for standard projects.
Can a welder damage a generator?
Yes, a welder can potentially damage a generator if the generator is not rated to handle the welder's power requirements. Always ensure your generator has an adequate wattage rating to avoid overloading.
Can we run a welding machine on solar power?
Running a welding machine on solar power is possible but requires a substantial solar setup. You need enough solar panels and an inverter with adequate capacity to handle the welder's peak and continuous wattage needs.