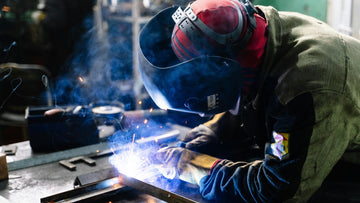
Spray transfer welding stands as one of the most efficient methods in metal fabrication, delivering high-quality, clean welds that industrial professionals rely on daily. If you've seen those perfect, smooth welds on aluminum or stainless steel and wondered how professionals achieve them, you're about to discover one of their secrets.
This beginner's guide breaks down spray transfer welding into simple, actionable information that both novices and intermediate welders can apply immediately. You'll learn not only what makes this technique different from other MIG welding methods but also why it might be the missing piece in your welding toolkit.
Whether you're looking to advance your career or simply improve your workshop projects, understanding spray transfer could revolutionize your welding results. Let’s begin!
Ready for spray transfer welding? Upgrade your setup with our high-performance GMAW welding machines designed for consistent, professional results.
What Is Spray Transfer Welding?

Spray transfer welding is a process where metal droplets are sprayed from a welding wire into the weld puddle. This technique is known for creating clean welds with minimal spatter, especially on thicker materials. It is an efficient method that offers deep penetration and high deposition rates.
Comparing Methods
In welding, different transfer methods have unique advantages. Spray transfer welds without touching the weld pool, unlike short-circuiting where the wire tip creates a short circuit. This contact-free process produces smoother welds.
Spray transfer requires higher current settings and uses an argon-rich gas mix. This configuration suits thicker metals, while short-circuiting is better for thin materials due to its controlled heat input.
Each method has its place, but spray transfer excels at delivering strong and clean results.
Transfer Physics
The physics behind spray transfer involves the continuous transfer of molten droplets across the arc. At high temperatures and currents, metal flows evenly from the electrode. The use of argon-rich shielding gas stabilizes the arc, improving droplet transfer.
Droplets in spray transfer are smaller and more uniform. This leads to less spatter and waste. The axial spray transfer mode ensures that the weld pool is more controlled, making it ideal for precision welding tasks. This method provides strong, consistent results with good penetration for robust welds.
Required Equipment
Spray transfer welding needs specific equipment to work well. This includes the right power source, proper wires and feeders, suitable shielding gases, and essential safety gear.
Power Sources
For spray transfer welding, you need a power source capable of providing high amperage. A machine that can deliver at least 200 amps in MIG mode is necessary. This power level helps create the consistent arc needed for this welding process.
Adjustable voltage settings are also important to fine-tune the arc characteristics. Machines from reliable brands from ArcCaptain are commonly used due to their durability. Make sure your power source can handle the demands of your specific welding projects, including thickness and material type.
Wires and Feeders
Welding wires must be chosen carefully for spray transfer. The wire diameter plays a key role.
Typically, wires of 1.0mm or thicker are used for this process. These wires must be combined with a high-quality feeder that maintains a steady wire feed rate. A good feeder ensures that the wire is fed consistently into the weld puddle, preventing any disruptions that could affect weld quality.
Look for wire made from materials like mild steel, stainless steel, or aluminum, depending on what you're working on.
Shielding Gases
Use an 80% Argon and 20% CO2 gas mixture for spray transfer. This blend helps create a stable arc and reduces spatter, which is ideal for clean welds.
In some cases, a mix with up to 90% Argon is preferred if you need greater control over the weld pool. The right gas flow rate is also crucial, typically between 20 to 25 cubic feet per hour (CFH). Ensure your gas cylinder or tank is compatible with your setup.
Safety Gear
Safety gear is crucial in spray transfer welding.
Welding helmets with auto-darkening features protect your eyes from bright arcs and UV rays. Fire-resistant clothing, gloves, and a welding jacket shield your skin from burns and sparks. Don't forget welding boots to protect your feet from falling objects. Ear protection can also be vital in loud environments.
Always ensure equipment fits properly and is in good condition to maintain safety standards.
Protect your hands without sacrificing dexterity. Shop our best welding gloves for comfort and safety during precise spray transfer work.
Process Breakdown
Getting comfortable with spray transfer welding requires understanding the fundamental process steps and technical parameters. Let's break down how this welding method works in practice.
Step-by-Step Guide
Follow these six critical steps to achieve clean, professional spray transfer welds every time:
- Setup: Configure your welding machine with a compatible torch and electrode wire suitable for your material.
- Gas Selection: Use the proper gas mixture (typically 80%+ argon) for effective spray transfer.
- Arc Initiation: Strike an arc between the welding wire and base metal.
- Positioning: Hold the torch at a 10-15 degree angle for optimal metal droplet transfer.
- Arc Maintenance: Steadily maintain the arc to ensure consistent droplet movement to the weld pool.
- Movement Control: Make slow, deliberate movements along your intended path to prevent defects.
Voltage and Amperage
The power settings on your machine directly impact spray transfer quality. Getting these parameters right is essential for success:
-
Voltage Requirements: Set higher voltages (24-32 volts) than other welding modes to ensure continuous arc and smooth droplet transfer.
Amperage Factors:
- Wire diameter determines base amperage needs
- Material thickness affects required power
- Larger diameters and thicker materials need higher amperage
- Incorrect settings lead to spatter or weak welds
Arc Properties
Understanding arc behavior helps you maintain control over your weld quality and appearance:
- Stability: The spray transfer arc remains stable and continuous, creating clean, precise weld lines.
- Formation: Electric arc forms between wire electrode and base metal, generating heat to melt both materials.
- Droplet Transfer: Arc stability ensures fine, consistent metal spray to the weld pool.
Length Control:
- Too short = harsh arc and spatter
- Too long = weakened control
- Proper technique maintains ideal arc length
Key Advantages

Spray transfer welding offers several benefits that can greatly improve your welding projects. This includes higher deposition rates, better penetration quality, and reduced spatter. Moreover, this method is well-suited for specific applications that demand precision and efficiency.
Deposition Rates
One of the most significant advantages of spray transfer welding is its ability to achieve high deposition rates. This means you can add more material to the weld pool in a shorter amount of time. It increases productivity, making it ideal for large-scale projects.
Since more metal is deposited quickly, the overall welding process is more efficient. This allows you to complete tasks more rapidly while maintaining consistency in weld quality. If you manage projects requiring swift turnaround times, this method is particularly beneficial.
Penetration Quality
Spray transfer welding provides excellent penetration quality, resulting in stronger and more durable welds. The metal droplets are consistently transferred in a steady, direct stream from the wire to the weld pool. This ensures deeper fusion with the base material.
Deeper penetration allows the weld to hold up well under stress and high loads. This quality is crucial for structural welds, as it reduces the likelihood of joint failure. Therefore, you can confidently use spray transfer welding in critical applications requiring robust connections.
Spatter Reduction
A notable benefit of spray transfer welding is the significant reduction in spatter. Spatter consists of small bits of molten metal that are thrown out of the weld pool. This process minimizes cleanup time after welding.
Less spatter also results in a cleaner work area and reduces the need for additional grinding or finishing work. This not only saves time but also results in better overall weld appearance. It's a key advantage if you prioritize precision and efficiency.
Best Applications
Spray transfer welding is particularly suited for welding thicker materials. It is highly effective on metals like steel and aluminum, commonly used in construction and heavy equipment industries. This mode is especially beneficial if you're working with materials that require high-quality welds.
The method is also ideal for flat and horizontal welding positions. Since it demands a stable workpiece, ensuring proper setups significantly enhances performance. Knowing where to apply this technique will allow you to maximize its strengths for your projects.
Challenges to Overcome
In spray transfer welding, some challenges include handling high heat levels, finding suitable positions for effective welding, and choosing appropriate materials. Additionally, consider quick fixes to common issues for better control and results. Knowing each of these can greatly improve your spray transfer welding projects.
Heat Management
Spray transfer welding involves high heat levels that can lead to warping and distortion if not carefully managed. You should monitor your travel speed to prevent too much heat from concentrating in one area. Faster travel minimizes burn-through and distortion.
Constantly check the thickness of the materials. Thicker materials absorb heat better, reducing the risk of damage. Consider using a heat sink or spreading the heat over a larger area if possible. These steps help you maintain the material's integrity.
Position Limits
Certain positions can be challenging, especially when welding overhead or vertically. These positions require more skill due to gravity's effect on the weld pool. Controlling the weld pool in these positions needs a steady hand and careful planning.
Try practicing on scrap materials to get used to different angles before tackling the main project. Employ smaller nozzle diameters to give you more control in awkward positions, allowing for more precise welds. This approach can make the process easier and less stressful.
Material Constraints
Spray transfer works best with specific materials, mostly with medium to thick materials such as steel or aluminum. Thin materials are at higher risk for burn-through due to the intense heat involved in spray transfer.
Ensure you select the right filler materials that match the base metal's properties. This choice reduces the chances of structural weaknesses. Coatings or finishes on materials complicate the process, so strip these areas clean to achieve a solid, uninterrupted weld.
Quick Fixes
Quick fixes can save you time when faced with unexpected challenges. For instance, adjusting your equipment settings is a simple yet effective quick fix. Tweaking your wire-feed speed or voltage can make a significant difference in controlling the weld pool.
If you're getting too much spatter, check your gas flow rate. Minor changes in the flow can eliminate excess spatter. Keep a spare set of essential tools and materials handy. That way you can rapidly address issues like changing worn-out nozzles or electrodes. This readiness helps maintain workflow efficiency.
Perfect your spray transfer technique with the right tools. Browse our essential welding accessories for enhanced performance and precision.
Conclusion on Spray Transfer Welding
Spray transfer welding represents a significant step up from basic welding techniques, offering professional-quality results that are difficult to achieve with other methods.
As you've learned, the combination of proper equipment setup, precise power settings, and careful technique creates those smooth, spatter-free welds that distinguish expert fabrication work. While it may take practice to master, the efficiency and quality improvements make it well worth the learning curve for both hobbyists and professionals.
Remember that successful spray transfer welding is as much about preparation as execution. Start with the right wire, gas mixture, and safety equipment before fine-tuning your technique. As you gain experience, you'll develop an instinctive feel for the proper arc length and torch angle.
For a deeper understanding of how power settings affect your welding results, check out our guide on Amperage in Welding to further enhance your welding skills.
Frequently Asked Questions about Spray Transfer Welding
Spray transfer welding is useful for its efficiency and high-quality results. Understanding the right gas, settings, and potential drawbacks helps you make the most of this technique.
Why use spray transfer?
Spray transfer is great for achieving clean and strong welds with less spatter. It’s often used in industrial settings and on thicker materials. It allows for faster welding speeds and reduces the need for post-weld cleanup.
What gas do you use for spray transfer?
A common choice for spray transfer welding is a gas mixture of 90% argon and 10% carbon dioxide. This blend helps achieve the desired arc characteristics and stability, which is essential for effective spray transfer.
What setting do you use for spray transfer?
You must use a constant voltage power source. Typically, higher voltage and current settings are required to maintain the spray arc. These settings help create a stable welding process, ensuring effective transfer and minimizing defects.
What are the disadvantages of spray welding?
Spray welding can be tricky to control and might lead to overheating if not monitored. Excessive spatter is also a concern if not done correctly. This process is better suited for flat or horizontal positions to avoid issues with gravity affecting the weld pool.