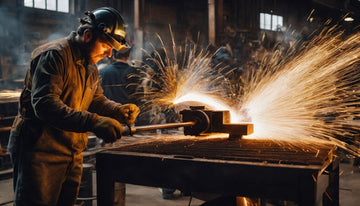
Gas Metal Arc Welding (GMAW), also known as MIG welding, is a versatile and efficient method for joining metals. This process uses an electric arc and a continuously fed wire electrode to create strong, durable welds quickly. Whether you're a beginner or looking to refine your skills, understanding GMAW can open up a world of possibilities in metalworking.
In this guide, we'll explore the ins and outs of GMAW, from basic principles to advanced techniques. You'll learn how to set up your equipment, choose the right materials, and troubleshoot common issues. We'll also share tips for achieving clean, professional-looking welds that stand the test of time.
Ready to spark your welding journey? Let's dive into the world of GMAW and discover how it can transform your projects!
Key Takeaways
- Gas Metal Arc Welding (GMAW) uses an electric arc and wire electrode to join metals.
- Equipment needed for GMAW includes a welding gun, wire feed unit, power supply, electrode, and shielding gas.
- There are different metal transfer modes in GMAW: globular, short-circuiting, spray, and pulsed-spray.
- GMAW can be used for high - speed welding and is easy to use for people of various skill levels.
- It’s important to use proper ventilation when doing GMAW because of the risk of harmful fumes.
What Is Gas Metal Arc Welding (GMAW)?
Gas Metal Arc Welding (GMAW) is a welding process that uses a consumable wire electrode and a shielding gas to create a strong bond between metal surfaces. This process requires equipment such as a welding gun, wire feed unit, power supply, electrode, and shielding gas.
As technology advances, GMAW has also been utilized in 3-D printing applications for metal fabrication.
Definition and process
Gas Metal Arc Welding (GMAW) is a powerful method to join metals. It uses an electric arc that forms between a consumable wire electrode and the metal workpiece. This process melts the materials together, creating strong joints when they cool and solidify.
The weld area is shielded by gas, which stops any contamination from the air.
A variety of metals like carbon steel, aluminum, or stainless steel can be welded using GMAW. Each material fuses well under proper welding parameters for high-quality results.
Equipment like a welding gun feeds the consumable wire into the arc as electricity heats it up to its melting point.
Next up, let's look at what equipment you need for GMAW.
Equipment You Need fo GMAW Welding
Gas Metal Arc Welding (GMAW) requires specific equipment to execute the process effectively. Here are the essential items needed:
- Welding gun: This tool is essential for directing the electrode wire and shielding gas to the welding area.
- Wire feed unit: This component feeds the electrode wire at a consistent rate, ensuring a stable weld.
- Power supply: The power supply provides the necessary electrical energy to create the arc between the electrode and workpiece.
- Electrode: The consumable wire electrode acts as a filler material that melts and joins the base metals during welding.
- Shielding gas: Using an appropriate shielding gas, such as argon or carbon dioxide, is crucial to protect the welding area from atmospheric contamination, ensuring a clean and strong weld joint.
GMAW-based 3-D printing
GMAW technology has expanded into 3-D printing, allowing for the fabrication of complex metal parts. This process involves layer-by-layer deposition of molten metal, creating intricate and durable components directly from digital models.
GMAW-based 3-D printing offers advantages such as high material utilization and precision in producing intricate designs while maintaining structural integrity.
The versatility of GMAW-based 3-D printing makes it suitable for a wide range of industries, including aerospace, automotive, and medical equipment manufacturing. The process enables the efficient production of custom metal parts with minimal material wastage, contributing to cost-effective and sustainable manufacturing practices.
How Does GMAW Work?
GMAW works by using a welding gun to create an electric arc between the electrode and the workpiece, resulting in the coalescence of metals. The process involves feeding a continuous solid wire electrode through the welding gun, along with shielding gas, to protect the weld from atmospheric contamination.
Operation and technique
Gas Metal Arc Welding (GMAW) operates by using a constant voltage power supply to create an electric arc between the electrode and the workpiece. The wire electrode is continuously fed through the welding gun, forming the weld joint as it melts on contact with the workpiece.
Technique involves maintaining a consistent travel speed and distance from the workpiece, as well as ensuring proper shielding gas flow to protect the molten weld pool from contamination.
Additionally, adjusting voltage and wire feed speed according to material thickness and type enhances welding quality.
Quality and safety
Quality and safety are paramount in Gas Metal Arc Welding (GMAW). Proper training is crucial to ensure the highest quality welds and prevent accidents. Adhering to safety guidelines, such as wearing protective gear and ensuring proper ventilation, is essential for safeguarding against potential hazards like fumes and splatter.
Additionally, regular inspection of equipment and materials ensures that the welding process maintains high standards at all times.
For GMAW, selecting the appropriate shielding gas for specific materials is vital to maintain weld quality. It's important to note that different metals may require different types of shielding gases to achieve optimal results.
Furthermore, understanding the types of defects that can occur during GMAW, such as porosity or cracking, allows welders to take preventative measures for maintaining the integrity of their work.
Types of Metal Transfer Modes in GMAW Welding
GMAW offers several different metal transfer modes, including globular, short-circuiting, spray, and pulsed-spray. Each mode has its own unique characteristics and applications within the welding process.
Globular
In the globular transfer mode of GMAW, larger droplets of molten metal are transferred from the electrode to the weld pool. This method is suitable for welding thicker materials and typically produces more spatter compared to other transfer modes such as spray or short-circuiting.
In this mode, the electrode wire is not in close contact with the weld pool, leading to a less stable arc and increased spatter production, which can affect weld quality and efficiency.
Globular transfer can be used for welding carbon steel, stainless steel, and aluminum. However, it requires careful control of parameters such as voltage, current, and wire feed speed to ensure proper droplet size and deposition rate.
Short-circuiting
Short-circuiting is a metal transfer mode in Gas Metal Arc Welding (GMAW) where the electrode wire makes contact with the weld pool. This causes a short circuit that results in rapid melting of the wire, creating small droplets that transfer across the arc to the workpiece.
The process offers low heat input and minimal spatter, making it suitable for thin materials and out-of-position welding. Short-circuiting also provides good control over the weld puddle and reduces distortion, but it may not be ideal for high deposition rates or thick materials.
Moving on to "Spray" as another metal transfer mode in GMAW..
Spray
Moving from the metal transfer mode of "Short-circuiting" to "Spray," it's crucial to understand that in Gas Metal Arc Welding (GMAW), the spray transfer mode is characterized by a steady stream of tiny molten droplets.
This happens when using high welding currents and voltages, typically for thicker materials or in automated applications. The process involves propelling small, molten metal droplets across the arc into the weld joint at a rapid pace.
It results in a clean, precise weld with minimal spatter and excellent penetration. Spray transfer offers high deposition rates and efficient coverage on thicker materials such as aluminum and stainless steel.
The spray method used in GMAW ensures faster production speeds while maintaining quality welds. Moreover, this technique is well-suited for welding non-ferrous metals like aluminum due to its ability to provide deeper penetration without excessive heat input.
Pulsed-spray
Moving from the continuous stream of spray transfer, let's delve into pulsed-spray. In pulsed-spray GMAW, the power source rapidly switches between a high peak current for metal droplet projection and a low background current to maintain the arc.
This process creates controlled droplet transfer, reducing spatter and heat input while allowing welding in various positions. Pulsed-spray is advantageous for thin materials and out-of-position welding due to its ability to produce precise welds with minimal distortion.
Pulsed-spray GMAW also offers improved control over weld pool size and bead appearance. The technique is particularly effective when welding aluminum and stainless steel due to its ability to provide good fusion without excessive heat input.
Advantages and Disadvantages of GMAW
GMAW offers advantages such as high welding speeds, ease of use, and the ability to weld various metal types. However, it also comes with disadvantages like the potential for solidification cracking and the need for proper ventilation due to shielding gas usage.
Advantages
Gas Metal Arc Welding (GMAW) offers numerous advantages to welders. It provides high welding speeds, allowing for efficient completion of projects. Additionally, it is easy to use, making it accessible for welders of varying skill levels.
- GMAW's high welding speeds reduce project completion time, increasing overall productivity.
- The ease of use of GMAW makes it suitable for welders with different levels of experience and expertise.
- GMAW enables precise control over the welding process, resulting in high-quality welds.
- This method allows for welding in various positions, enhancing its versatility and applicability.
- It is adaptable to a wide range of materials including carbon steel, stainless steel, aluminum, and non-ferrous metals.
- GMAW produces minimal spatter during the welding process due to its controlled arc characteristics.
- The ease of automation in GMAW reduces labor costs and increases efficiency in large-scale projects.
Disadvantages
Solidification cracking can occur in GMAW due to the higher cooling rate of the welded metal.
- Solidification cracking happens due to rapid solidification of the weld metal.
- Proper filler metal and welding technique selection can help prevent solidification cracking.
- Ventilation is crucial for removing welding fumes and maintaining a safe work environment.
- Adequate ventilation reduces the risk of inhaling hazardous particles and gases during welding.
- Using proper personal protective equipment such as respirators and gloves is essential for safety.
- Training on identifying ventilation requirements and utilizing safety measures is critical for welders.
- Adhering to industry guidelines for ventilation standards minimizes health risks associated with welding activities.
Conclusion
In conclusion, Gas Metal Arc Welding (GMAW) is a widely used and versatile industrial welding process. It offers advantages such as high welding speed, better control of the weld, and the ability to weld in various positions.
GMAW requires the use of a shielding gas to protect the weld pool from atmospheric contamination. Proper training and adherence to safety guidelines are essential for performing GMAW effectively and safely.
This comprehensive guide provides valuable insights into the operation, techniques, and materials involved in GMAW.
FAQs on GMAW Welding
What is Gas Metal Arc Welding?
Gas Metal Arc Welding (GMAW), or MIG welding, uses an electric arc to melt and join metals. It employs a continuously fed wire electrode and shielding gas to protect the weld pool.
GMAW is known for its efficiency, versatility, and ability to produce clean, strong welds on various metals, making it popular in both industrial and DIY settings.
What do I need for Gas Metal Arc Welding?
For GMAW, you'll need a MIG welder (including power source, wire feeder, and welding gun), safety gear (welding helmet, gloves, flame-resistant clothing), welding wire, and shielding gas.
You'll also require the metal you plan to weld and basic tools like wire cutters and a wire brush. Proper training or instruction is essential to use the equipment safely and effectively.
Is Gas Metal Arc Welding safe?
Gas Metal Arc Welding can be safe when proper precautions are taken. It's crucial to wear appropriate personal protective equipment, ensure proper ventilation, and keep the work area free of flammable materials.
Understanding the equipment, following manufacturer guidelines, and being aware of potential hazards like electric shock and UV radiation are key to maintaining a safe welding environment.
Can anyone learn how to do Gas Metal Arc Welding?
Most people can learn Gas Metal Arc Welding with proper training and practice. It's often considered one of the easier welding processes to learn, making it accessible to beginners.
However, mastering GMAW requires dedication, patience, and consistent practice to develop the necessary skills and understand the nuances of different materials and techniques.
What is GMAW vs SMAW?
GMAW (Gas Metal Arc Welding) and SMAW (Shielded Metal Arc Welding) are two different welding processes. GMAW uses a continuously fed wire electrode and external shielding gas, making it faster and cleaner, ideal for both beginners and professionals.
SMAW, or stick welding, uses a flux-coated electrode that creates its own shielding, making it more versatile for outdoor use and on dirty metals, but it's generally slower and requires more skill to master.