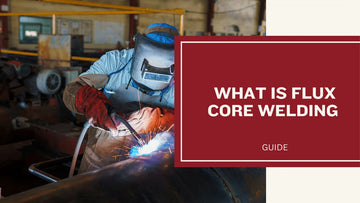
Are you interested in learning about a welding technique that is gaining popularity in the industry? Look no further than flux core welding. This process, also known as FCAW welding, is a type of welding that uses a continuously-fed electrode with a flux core to create a weld.
So, what is flux core welding? Essentially, it is a type of arc welding that uses a tubular wire filled with flux instead of a solid wire. The flux creates a shielding gas that protects the weld from impurities and contamination. This technique is commonly used in construction, shipbuilding, and other industries where welding is required.
Whether you're a seasoned professional looking to refine your skills or a curious newbie stepping into the world of metalwork, understanding Flux Core Welding is an exciting journey into a process that's reshaping how we join and create with metal. In this article, we'll dive deep into the world of Flux Core Welding, exploring its nuances, advantages, and why it's becoming a go-to method for welders worldwide.
What is Flux Core Welding (FCAW)
Flux Core Welding, also known as FCAW, is a welding process that uses a tubular wire electrode with a flux core. The flux core contains various materials that produce shielding gases and slag to protect the weld from atmospheric contamination. This process is similar to MIG welding, but the difference is that FCAW uses a tubular wire electrode instead of a solid wire electrode. It is commonly used in construction, shipbuilding, and pipeline welding due to its high deposition rates and ability to weld in all positions.
In summary, FCAW is a welding process that uses a tubular wire electrode with a flux core to produce a weld. It is a versatile process that can be used on a variety of materials and is commonly used in construction, shipbuilding, and pipeline welding.
How Does Flux Core Welding Work?
Flux core welding is a type of welding that uses a continuously fed electrode wire that is coated with a flux. The flux is a material that protects the weld puddle from the air and helps to create a strong weld. Here is a step-by-step guide on how flux core welding works:
-
First, you need to set up your welding machine. This involves selecting the right settings for the thickness of the metal you are welding and the type of flux core wire you are using.
-
Once your machine is set up, you need to prepare the metal you are welding. This involves cleaning the metal to remove any rust, paint, or other contaminants that could affect the quality of the weld.
-
Next, you need to position the metal in the right place for welding. This could involve clamping the metal in place or using a jig to hold it steady.
-
Now it's time to start welding. You will hold the welding gun at a specific angle and distance from the metal and pull the trigger to start the wire feed. As you move the gun along the joint, the wire will melt and create a weld puddle.
-
The flux in the wire will create a protective shield around the weld puddle, preventing it from being contaminated by the air. This shield also helps to create a strong, clean weld.
-
As you weld, you will need to move the gun at a steady pace to ensure that the weld is consistent and strong. You may need to adjust the angle and distance of the gun as you go to get the best results.
-
Once you have finished welding, you will need to clean up the weld by removing any excess flux and grinding down any rough spots. This will help to create a smooth, professional-looking weld.
In summary, flux core welding works by using a continuously fed electrode wire that is coated with a flux. The flux creates a protective shield around the weld puddle, preventing it from being contaminated by the air and helping to create a strong, clean weld. By following the steps above, you can learn how to use flux core welding to create high-quality welds on a variety of metals.
Equipment Used in FCAW Welding
To perform flux core welding, you will need a few pieces of equipment. Here are the most important ones:
-
Welding Gun: The welding gun is the tool that delivers the filler metal to the base metal. It is usually held in the dominant hand and controlled by the welder's trigger finger. The gun is connected to the flux core welder by a cable.
-
Flux Core Welder: The flux core welder is the machine that provides the electrical current to melt the filler metal and the base metal. It also regulates the wire feed rate and the voltage.
-
Drive Rolls: The drive rolls are the small wheels that pull the filler metal wire from the spool and feed it into the welding gun. They are usually made of steel or plastic, depending on the wire type.
-
Filler Metals: The filler metals are the wires that are melted to create the weld. They come in different types and sizes, depending on the base metal and the welding application. Some common filler metals for flux core welding are E71T-1, E71T-11, and E71T-GS.
-
Wire Type: The wire type is the composition of the filler metal wire. It can be either flux core or solid wire. Flux core wire has a hollow core that contains fluxing agents, which produce a shielding gas when heated. Solid wire requires a separate shielding gas to protect the weld from contamination.
-
Base Metal: The base metal is the material that is being welded. It can be steel, stainless steel, aluminum, or any other metal that can conduct electricity.
In summary, to perform flux core welding, you will need a welding gun, a flux core welder, drive rolls, filler metals, wire type, and base metal. Each of these pieces of equipment plays a crucial role in creating a strong and durable weld.
Types of Flux Cored Arc Welding (FCAW)
There are two main types of Flux Cored Arc Welding (FCAW): self-shielded and gas-shielded.
Self-Shielded Flux-Cored Arc Welding
Self-shielded FCAW is a type of welding process that does not require an external shielding gas. The flux inside the electrode produces a shielding gas when it is heated, which protects the weld pool from atmospheric contamination. Self-shielded FCAW is ideal for outdoor welding applications, as it can be used in windy conditions.
Applications for Self-Shielded FCAW
Self-shielded FCAW is commonly used in the construction industry for welding structural steel and in the shipbuilding industry for welding offshore structures. It is also used for welding pipelines and in the repair and maintenance of heavy equipment.
Gas-Shielded Flux Core Welding
Gas-shielded FCAW is a type of welding process that uses an external shielding gas to protect the weld pool from atmospheric contamination. The shielding gas is typically a mixture of argon and carbon dioxide. Gas-shielded FCAW produces a higher quality weld than self-shielded FCAW but requires a clean work environment.
Applications for Gas-Shielded FCAW
Gas-shielded FCAW is commonly used in the automotive industry for welding sheet metal and in the manufacturing of heavy machinery. It is also used in the construction industry for welding structural steel and in the shipbuilding industry for welding ship hulls.
In conclusion, both self-shielded and gas-shielded FCAW have their own unique advantages and disadvantages. The choice of which type of FCAW to use depends on the specific welding application and the environment in which the welding is being performed.
Advantages of Flux Core Welding
Benefits of Flux Core Welding
Flux core welding is a popular welding technique that offers several advantages over other welding techniques. Here are some of the benefits of flux core welding:
-
High Welding Speed: Flux core welding is a high-speed welding technique that allows you to weld at a faster rate than other welding techniques. This is because the flux core wire melts faster than solid wire, which means you can cover more ground in less time.
-
Better Penetration: Flux core welding offers better penetration than other welding techniques. The flux core wire melts at a lower temperature, which allows it to penetrate deeper into the metal. This results in a stronger weld.
-
No Need for Gas: Flux core welding does not require a shielding gas, which makes it a more cost-effective option than other welding techniques. This also makes it a more portable option, as you don't need to carry around a gas cylinder.
-
Versatile: Flux core welding can be used on a variety of metals, including stainless steel, carbon steel, and aluminum. This makes it a versatile option for a range of welding projects.
Ideal Use Cases for Flux Core Welding
Flux core welding is an ideal option for several use cases, including:
-
Outdoor Welding: Flux core welding is a great option for outdoor welding projects because it does not require a shielding gas. This means you can weld in windy or breezy conditions without worrying about the gas blowing away.
-
Heavy Metal Welding: Flux core welding is a great option for heavy metal welding projects because it offers better penetration than other welding techniques. This means you can weld thicker pieces of metal with ease.
-
Welding in Tight Spaces: Flux core welding is a more compact option than other welding techniques because it does not require a gas cylinder. This makes it a great option for welding in tight spaces where there isn't much room to maneuver.
-
Cost-Effective Welding: Flux core welding is a more cost-effective option than other welding techniques because it does not require a shielding gas. This makes it a great option for DIY welding projects or for those on a tight budget.
Overall, flux core welding is a versatile, cost-effective, and efficient welding technique that offers several advantages over other welding techniques. Whether you're welding outdoors, working with heavy metal, or welding in tight spaces, flux core welding is a great option to consider.
Getting Started with Flux Core Welding
If you're interested in learning how to weld, flux core welding is a great place to start. This welding method is versatile, easy to learn, and produces strong welds. In this section, we'll cover the basic skills required for flux core welding, as well as some tips for beginners.
Basic Skills Required for Flux Core Welding
Before you start welding, there are a few basic skills you should master. These include:
- Safety: Always wear appropriate protective gear, such as a welding helmet, gloves, and clothing made of flame-resistant material.
- Preparation: Clean the surface of the metal you'll be welding to remove any rust, paint, or debris that could interfere with the weld.
- Positioning: Position the metal so that you can comfortably and safely weld it. This may require using clamps or supports.
- Speed and angle: Move the welding gun at a consistent speed and angle to produce a smooth, even weld.
Tips for Beginners
If you're new to flux core welding, here are a few tips to help you get started:
- Practice on scrap metal first: Before you start welding on your project, practice on scrap metal to get a feel for the welding gun and the welding process.
- Start with a low heat setting: Flux core welding requires a higher heat than other welding methods, but starting with a low heat setting will help you avoid burning through the metal.
- Keep the welding gun at a consistent angle: This will help you produce a smooth, even weld.
- Watch the weld pool: The weld pool is the molten metal that forms as you weld. Watching it will help you maintain the correct speed and angle as you weld.
- Clean up between passes: If you're welding multiple passes, be sure to clean up the weld area between passes to ensure a strong, clean weld.
With these basic skills and tips, you'll be well on your way to mastering flux core welding.
Safety Considerations in Flux Core Welding
When it comes to flux core welding, safety should always be a top priority. Here are some essential safety gear and practices, as well as common hazards and how to avoid them.
Essential Safety Gear and Practices
To protect yourself while flux core welding, you should always wear personal protective equipment (PPE) such as:
- Welding helmet with a filter lens shade
- Welding gloves
- Welding jacket or apron
- Safety glasses or goggles
- Respirator or face mask (if working in a poorly ventilated area)
It is also important to follow these practices:
- Keep your work area clean and free of clutter
- Make sure your welding machine is in good condition
- Use a welding table or workbench to hold your workpiece
- Keep your welding cables and hoses organized and out of the way
- Always have a fire extinguisher nearby
Common Hazards and How to Avoid Them
Flux core welding can expose you to a number of hazards, including:
- Electric shock
- Welding Burns
- Eye damage
- Fumes and gases
To avoid these hazards, follow these guidelines:
- Always wear your PPE, especially your welding helmet and gloves
- Keep your welding cables and hoses in good condition and away from water or other liquids
- Use a welding table or workbench to hold your workpiece steady
- Make sure you have adequate ventilation in your work area to avoid inhaling fumes and gases
- Use a respirator or face mask if working in a poorly ventilated area
By following these safety gear and practices, as well as avoiding common hazards, you can ensure a safe and successful flux core welding experience.
Flux Core Welding Applications
Flux-cored arc welding (FCAW) is a versatile welding process that is commonly used in many industries. This welding process is ideal for welding thicker materials and can be used on a variety of metals including stainless steel and mild steel. Here are some of the applications of flux core welding.
Industrial Uses of FCAW Welding
FCAW welding is widely used in the industrial sector due to its high deposition rate, which makes it ideal for welding thicker materials. This welding process is commonly used in shipbuilding, construction, and pipeline welding. It is also used in the manufacturing of heavy equipment, such as cranes and bulldozers.
One of the advantages of FCAW welding is that it can be used for multi-pass welds, which makes it ideal for welding thicker metals. This welding process is also suitable for welding metals with a higher melting point, such as stainless steel.
Flux-Cored Arc Welding in DIY and Home Projects
Flux-cored arc welding is not just limited to industrial applications, but it is also widely used in DIY and home projects. This welding process is ideal for welding metal thicknesses of 18 gauge and above.
One of the advantages of FCAW welding is that it can be used with a variety of welding machines, including portable welding machines. This makes it ideal for DIY and home projects, as you can easily transport the welding machine to your project site.
In conclusion, flux-cored arc welding is a versatile welding process that can be used in a variety of applications. Whether you are welding thicker materials in an industrial setting or working on a DIY project at home, FCAW welding is a reliable and efficient welding process.
Advanced Flux Core Welding
Dual Shield and Advanced Techniques
Dual shield welding is an advanced flux core welding technique that uses a combination of flux core wire and shielding gas to produce high-quality welds. This technique is ideal for welding heavy-duty materials such as structural steel, shipbuilding, and pipeline welding.
Dual shield welding offers several advantages over traditional flux core welding, including increased deposition rates, improved weld quality, and reduced spatter. The shielding gas used in dual shield welding helps to protect the weld from oxidation and contamination, resulting in a stronger, more durable weld.
To perform dual shield welding, you will need a specialized welding machine, a dual shield wire, and a shielding gas. The welding machine must be capable of providing a constant voltage output, and the dual shield wire must be compatible with the shielding gas used.
Advanced techniques such as pulse welding and waveform control can also be used to further improve the quality of the weld. Pulse welding allows for greater control over the heat input, resulting in less distortion and a more precise weld. Waveform control allows for greater control over the arc, resulting in a smoother, more stable arc and a better weld bead appearance.
Welding with Various Metals and Alloys
Flux core welding can be used to weld a variety of metals and alloys, including stainless steel, aluminum, and nickel alloys. However, welding these materials requires specialized flux core wire and shielding gas.
When welding stainless steel, a flux core wire with a high nickel content is recommended. This helps to prevent cracking and improve the overall quality of the weld. When welding aluminum, a flux core wire with a high silicon content is recommended. This helps to improve the wetting action of the weld and prevent porosity.
When welding nickel alloys, a specialized flux core wire with a high nickel content is recommended. This helps to prevent cracking and improve the overall quality of the weld.
In conclusion, advanced flux core welding techniques such as dual shield welding and advanced waveform control can help to produce high-quality welds on heavy-duty materials. Additionally, specialized flux core wire and shielding gas can be used to weld a variety of metals and alloys, including stainless steel, aluminum, and nickel alloys.
Flux Core Welding Versus Other Methods
Comparison with MIG and TIG Welding
When it comes to welding methods, there are several options available, including MIG welding, TIG welding, and flux core welding. MIG welding, also known as gas metal arc welding (GMAW), uses a wire electrode and a shielding gas to create a strong weld. TIG welding, or gas tungsten arc welding (GTAW), uses a tungsten electrode and a separate filler material to create a precise, high-quality weld.
Welding Method | Description | Advantages | Ideal Usage |
---|---|---|---|
MIG Welding | Uses a wire electrode and shielding gas. | Preferred for precision and control. | Best for welding thin materials. |
TIG Welding | Uses a tungsten electrode and separate filler material. | High-quality, precise welds. | Ideal for strong welds on various materials. |
Flux Core Welding | Does not require external shielding gas. | Affordable, suitable for outdoor/windy conditions. | Good for environments where MIG and TIG may not be feasible. |
However, MIG and TIG welding are often preferred for their precision and control. MIG welding is especially useful for welding thin materials, while TIG welding is ideal for creating strong, high-quality welds on a variety of materials.
When to Choose Flux Core Welding
While MIG and TIG welding may be better suited for certain applications, there are many situations where flux core welding is the best choice. For example, if you need to weld thick materials or work in outdoor conditions, flux core welding may be the most practical option.
Flux core welding is also useful for creating strong, durable welds on materials like steel and stainless steel. It can be used for a variety of applications, including construction, automotive repair, and metal fabrication.
Overall, while MIG and TIG welding have their advantages, flux core welding is a reliable and affordable option that can be used in a variety of situations. Whether you are a professional welder or a DIY enthusiast, it is worth considering flux core welding as a viable option for your next project.
Conclusion
By now, you should have a good understanding of what Flux-cored Arc Welding (FCAW) is and how it differs from other welding methods. FCAW is a versatile and reliable welding method that can be used in a variety of applications, including construction, shipbuilding, and pipeline welding.
One of the key advantages of FCAW is that it is a relatively easy welding method to learn, making it a popular choice for both beginners and experienced welders. FCAW also allows for welding in outdoor environments, which can be difficult with other welding methods.
Another advantage of FCAW is that it produces a high-quality weld with good penetration, even on thick materials. This is due to the flux core wire that is used, which helps to protect the weld from contaminants and provides additional shielding.
Overall, FCAW is an important welding method that is widely used in many industries. Whether you are a beginner or an experienced welder, FCAW is a versatile and reliable welding method that can help you achieve high-quality welds on a variety of materials.
Frequently Asked Questions
What is flux core welding good for?
Flux core welding is a versatile process that can be used for a variety of welding applications. It is particularly useful for welding thick materials and for outdoor welding because it does not require a shielding gas. Flux core welding is also good for welding dirty or rusty materials because the flux helps to clean the metal as it welds.
What is the difference between flux core and MIG welding?
The main difference between flux core welding and MIG welding is that flux core welding uses a hollow wire electrode that is filled with flux, while MIG welding uses a solid wire electrode and a shielding gas. Flux core welding is also better suited for outdoor welding because it does not require a shielding gas, which can be blown away by wind.
Is flux core welding as strong as stick?
Flux core welding can produce welds that are just as strong as stick welding, but it depends on the specific application and the skill of the welder. Flux core welding can also produce welds with less spatter and a smoother appearance than stick welding.
Do you need gas for flux core welding?
Flux core welding does not require a shielding gas, but it does require a flux core wire. The flux in the wire creates a shielding gas when it is heated, which protects the weld from atmospheric contamination. However, some flux core wires can be used with a shielding gas to improve weld quality and reduce spatter.