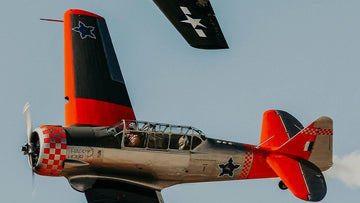
Military grade aluminum transformed the battlefield with vehicles that can absorb punishing impacts yet remain light enough for rapid deployment.
But why stop at defense applications? This extraordinary metal is now the secret weapon of welders who demand perfection in everything from aircraft components to high-performance boats. When properly welded, military grade aluminum creates joints so robust they can withstand stresses that would cause standard aluminum to fail catastrophically.
Here's the shocking truth most fabricators miss: apply your regular welding techniques to military grade aluminum and you'll actually weaken what should be its superior properties. The unique metallurgy demands specific approaches that many experienced welders have never learned.
Throughout this guide, we'll reveal the exact methods that preserve the exceptional characteristics of alloys like 7075 and 6061-T6, techniques previously known only to defense contractors and aerospace specialists. Master these approaches, and you'll create aluminum structures that perform in ways your competitors might consider impossible.
Ready to master military-grade aluminum? Our specialized aluminum welders deliver the precision control needed for defense-grade materials and professional results.
What Is Military Grade Aluminum?

Military grade aluminum refers to specific aluminum alloys that meet stringent military specifications for use in defense applications. These alloys are known for their durability, strength, and corrosion resistance, making them suitable for demanding environments.
Common Military Grade Aluminum Alloys
The defense industry relies on specific aluminum alloys that deliver exceptional performance under extreme conditions.
Let's examine the most crucial military-spec options:
- 7075 aluminum - The heavyweight champion of military alloys, offering extraordinary tensile strength thanks to its high zinc content and heat treatment capabilities
- 6061 aluminum - The versatile workhorse combining excellent corrosion resistance with superior machinability, making it ideal for components requiring complex fabrication
- 5083 aluminum - Preferred for marine military applications due to its exceptional saltwater corrosion resistance and good weldability characteristics
- 2024 aluminum - Widely used in aircraft structural components where fatigue resistance and damage tolerance are critical performance factors
- 7050 aluminum - Developed specifically for thick aerospace and defense components requiring superior stress corrosion cracking resistance
These specialized alloys deliver the optimal balance of strength, weight, and workability that make military grade aluminum the material of choice for mission-critical applications.
Military vs Commercial Aluminum Classifications
The distinction between military and commercial aluminum extends far beyond simple marketing terminology—it reflects fundamental differences in specifications, testing protocols, and performance requirements.
Military Aluminum Classifications:
- Rigorous Mil-Spec standards - Defense applications require adherence to precise military specifications that govern every aspect of the material's composition and performance
- Extensive quality testing - Military grade aluminum undergoes comprehensive evaluation for critical properties including brinell hardness, elongation at break, and specific density metrics
- Strict composition control - Chemical makeups are tightly regulated with minimal tolerance for variation, ensuring consistent performance under extreme conditions
- Enhanced performance requirements - Military specifications demand superior strength, corrosion resistance, and fatigue properties compared to commercial counterparts
Commercial Aluminum Classifications:
- Cost-optimization focus - Commercial grades often balance performance with economic considerations, allowing more flexibility in composition and processing
- Application-specific standards - Rather than universal military specifications, commercial grades follow industry-specific standards that vary by application
- Wider tolerance ranges - Composition and property specifications typically permit broader variation while maintaining acceptable performance for civilian applications
- Overlapping alloy designations - Many alloys like 6061 and 7075 exist in both sectors, but military versions undergo more stringent testing and may feature optimized heat treatments
Understanding these classification differences helps explain why seemingly identical alloy numbers can deliver significantly different welding and performance characteristics.
Key Properties That Make Military Grade Aluminum Exceptional
Military grade aluminum doesn't earn its prestigious status by accident—it delivers a unique combination of performance characteristics that make it indispensable for the most demanding applications.
- Superior strength profiles - Military aluminum alloys deliver impact resistance that can withstand ballistic forces while maintaining structural integrity in critical defense components
- Advanced corrosion resistance - These specialized alloys resist degradation in extreme environments from saltwater exposure to chemical warfare agents, ensuring reliable long-term performance
- Enhanced plasticity and formability - Despite their strength, military grade alloys maintain sufficient ductility to be formed into complex shapes required for sophisticated defense systems
- Extraordinary fatigue resistance - Particularly evident in 7000-series alloys, this property ensures components can endure repeated stress cycles without developing microfractures
- Specialized wear resistance - Alloys like 6082 aluminum feature hardened surfaces that minimize degradation from friction in mechanical systems and moving parts
- Precision-engineered compositions - Strategic addition of elements like copper and magnesium creates optimized microstructures that balance seemingly contradictory properties such as toughness and hardness
These exceptional characteristics explain why military grade aluminum commands premium pricing and requires specialized welding approaches to maintain its performance advantages.
Welding Advantages With Military Grade Aluminum
Ever wondered why defense contractors insist on military-grade aluminum? The welding benefits alone make it worth the premium price tag.
Superior Joint Integrity
Military aluminum creates welds that simply don't quit. These joints can withstand forces that would tear standard aluminum apart.
Imagine a weld that can take a direct .50-caliber impact without failing. That's the kind of toughness we're talking about.
Your most critical connections stay intact even under extreme stress, from battlefield conditions to aerospace applications where failure isn't an option.
Post-Weld Performance
Unlike regular aluminum that weakens after welding, military-grade alloys maintain their impressive properties even after intense heat exposure.
You won't face the typical strength degradation in the heat-affected zone. These alloys are engineered to bounce back after welding.
This means your finished projects maintain their performance specs even after multiple weld passes and heat cycles.
Reduced Warping and Distortion
Tired of fighting distortion? Military aluminum makes your life easier with excellent dimensional stability during welding.
The balanced thermal properties mean less fighting with warped parts. Your precision components stay true to spec without the usual headaches.
This translates to less rework, more accurate assemblies, and professional results that don't require extensive post-weld straightening.
Challenges When Welding Military Grade Aluminum
Welding military aluminum isn't a walk in the park. Here's what makes it tricky and how to tackle these challenges head-on.
Thermal Conductivity Considerations
Military aluminum steals heat faster than a pickpocket in a crowded subway. This incredible heat conductivity creates real headaches during welding.
Your weld pool cools almost instantly, making it tough to achieve proper fusion. Just when you think you've got enough heat, the aluminum whisks it away.
Cranking up your amperage helps combat this issue. Many welders also preheat their workpieces to slow down that rapid cooling that causes incomplete welds.
Oxide Layer Management
That invisible oxide layer is your biggest enemy when welding military aluminum. It melts at twice the temperature of the base metal!
Left intact, this stubborn layer prevents your weld from penetrating properly. The result? Weak joints that look good but fail under stress.
Aggressive cleaning just before welding is non-negotiable. Use a stainless steel brush dedicated only to aluminum, and clean in one direction to avoid pushing contaminants back into the surface.
Alloy-Specific Complications
Not all military aluminum behaves the same way under the torch. Each alloy throws its own unique tantrum during welding.
7075 might crack if you look at it wrong during welding, while 6061 is more forgiving but requires specific filler metals to maintain strength.
Learning the personality quirks of each alloy saves massive headaches. What works perfectly on one military grade aluminum might create a disaster on another.
Best Welding Processes for Military Grade Aluminum

Choosing the right welding method for military aluminum can make or break your project. Let's dive into which processes deliver the best results for these demanding alloys.
TIG Welding Applications
TIG welding is the gold standard for military aluminum—think of it as the precision scalpel in your welding arsenal.
The incredible control lets you dial in perfect beads even on those finicky 7075-T6 alloys. You'll get cleaner, stronger welds without the splatter mess of other methods.
Key advantages:
- Precision control allows consistent results even with variable material thickness
- Suitable for thin-walled sections and intricate designs where accuracy is critical
- Minimal contamination helps maintain material strength in the heat-affected zone
When working on critical components where failure isn't an option, TIG delivers the goods. Yes, it's slower, but that extra time buys you welds that pass the toughest inspection standards.
When precision matters and failure isn't an option, our aluminum TIG welders provide the pulse capabilities and fine control needed for aerospace-quality results.
MIG Welding Techniques
Need to crank out military-grade aluminum welds faster? MIG welding might be your best friend.
This process lets you lay down metal at triple the speed of TIG, making it perfect for those larger defense projects with tight deadlines. The continuous wire feed means fewer stops and starts that create weak points.
Benefits include:
- Quick setup and application speed—perfect when time matters
- Capable of welding thicker materials like t651 plate with better penetration
- Fewer stops required, reducing seams and potential failure points
While MIG sacrifices some precision, modern equipment has narrowed the quality gap considerably. For thicker sections over 1/4 inch, many defense contractors actually prefer MIG for its deeper penetration.
Create flawless joints in premium alloys with our professional MIG welders featuring the consistent wire feed and adjustable settings essential for military-grade aluminum.
Special Equipment Requirements
Don't expect to weld military aluminum with basic equipment from the hardware store. This stuff demands serious machinery.
You'll need high-frequency start capabilities, precision wire feeders, and pulse controls that standard welders just don't offer. The investment is significant, but so is the quality difference.
Necessary equipment:
- Precision CNC machines for accurate cuts and preparations
- Tooling designed specifically for high-strength aluminum alloys
- Proper shielding gases with precise flow control systems
The right shielding gas setup is non-negotiable—pure argon for TIG and helium mixes for thicker sections. Skimp here, and you'll create welds that look good but fail under stress testing.
Military Grade Aluminum Guide for Different Projects
Choosing the right aluminum alloy can make or break your project. Here's where specific military-grade alloys truly shine.
Aerospace Applications
Aerospace demands the perfect balance between weight and strength - and military aluminum delivers both.
These specialized alloys help aircraft components shed pounds while handling extreme forces. Every ounce saved translates directly to increased range and payload capacity.
Look for heat-treatable alloys like 7075 in critical components where failure isn't an option. These materials withstand the brutal temperature cycles and vibration that would destroy lesser metals.
Marine Environments
Nothing kills ordinary aluminum faster than saltwater. Military-grade alloys laugh at conditions that destroy standard metals.
5083 aluminum has become the gold standard for naval applications. It resists the relentless corrosion that turns other metals into flaky rust in months.
The superior weldability of these marine-grade alloys means you can create watertight structures that maintain their integrity even after years of harsh saltwater exposure.
Tactical Equipment Construction
When soldiers' lives depend on equipment performance, only military-grade aluminum makes the cut.
These alloys create gear that absorbs punishment without adding weight that exhausts troops in the field. From weapon components to portable shelters, the right aluminum makes equipment both tougher and lighter.
The superior machinability allows for precision components with tight tolerances that operate flawlessly even in sandy, muddy conditions that would jam ordinary metals.
High-Stress Structural Components
Building structures that must not fail? Military aluminum handles stresses that would buckle standard materials.
These alloys maintain their integrity under loads that would permanently deform commercial grades. The exceptional fatigue resistance prevents microscopic cracks from developing into catastrophic failures.
Engineers choose these premium materials for bridges, critical infrastructure, and anywhere failure would be catastrophic rather than merely inconvenient.
Tips for Successful Military Grade Aluminum Welds
Creating perfect welds with military aluminum requires specialized techniques. Here are the critical practices that separate amateur attempts from professional results:
- Meticulous surface preparation – Remove all oxide layers with a dedicated stainless steel brush and acetone cleaning. This prevents the contamination that causes 90% of military aluminum weld failures.
- Correct filler metal matching – Pair 5356 filler with 5xxx series alloys and 4043 with 6xxx series. Using the wrong filler can reduce joint strength by up to 40% even when the weld looks perfect.
- Pre-weld baking – Heat materials to 200°F for 1-2 hours before welding to drive out hydrogen that causes porosity. This simple step can double the strength of your final weld.
- Pulse welding technique – Use pulsed current to reduce heat input by up to 30%, preventing the distortion that makes precision components unusable after welding.
- Post-weld heat treatment – Apply proper aging cycles to restore up to 80% of the original alloy strength that was lost during the welding process.
- Corrosion protection – Apply MIL-spec coatings immediately after welding while the metal is still warm for maximum penetration and adhesion to prevent galvanic corrosion.
Perfect technique requires perfect materials. Browse our premium welding consumables including specialized filler metals formulated specifically for high-strength aluminum alloys.
Conclusion on Military Grade Aluminum
Military grade aluminum isn't just another marketing term—it represents genuinely superior materials engineered to perform when failure isn't an option. The unique combination of strength, corrosion resistance, and weldability makes these specialized alloys worth the investment for serious fabricators. While they do present challenges, the techniques we've covered will help you achieve welds that maintain the exceptional properties these materials offer.
Whether you're building high-performance vehicles, marine equipment, or aerospace components, mastering military grade aluminum welding gives you capabilities that separate professional results from amateur attempts. The knowledge to properly select, prepare, and join these premium alloys opens doors to projects that would be impossible with standard materials.
Ready to put your new skills to work? Check out our collection of cool welding projects that showcase what's possible when expertise meets premium materials.
Frequently Asked Questions about Military Grade Aluminum
Military grade aluminum is known for its strength and durability, making it ideal for various demanding applications. Different grades offer unique properties that suit specific needs.
What is military grade aluminum?
Military grade aluminum typically refers to aluminum alloys that have been used in military applications for their durability and strength. These alloys often have enhanced properties like improved corrosion resistance and impact strength.
What are the three grades of aluminum?
The main grades or series of aluminum include 1XXX, 6XXX, and 7XXX series. Each series has its own characteristics. The 1XXX series is known for purity, the 6XXX series for good weldability, and the 7XXX series for high strength due to zinc as a primary alloying element.
What is the best grade of aluminum?
The best grade of aluminum depends on the intended use. For military applications requiring high strength and resistance, the 7XXX series is often favored. Each series offers a balance of strength, weight, and resistance based on specific alloying elements.
What type of aluminum is used in guns?
The 7XXX series, especially alloys like 7075, is commonly used in firearms. It provides excellent strength-to-weight ratios, making it suitable for components that must withstand high stress and pressure.
Is military grade aluminum stronger than steel?
Military grade aluminum can be very strong, but its strength compared to steel depends on the specific alloy and steel type. Some aluminum alloys can match or exceed the strength of certain steels, but steel often remains stronger overall but heavier.