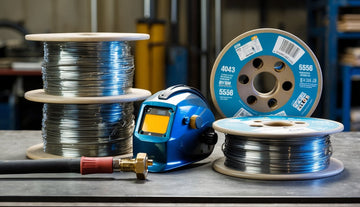
Choosing between 4043 vs. 5356 aluminum welding filler metals can be tricky. These two options have different strengths that make each better for specific projects.
5356 delivers higher strength (18 KSI vs 11 KSI shear strength), making it superior for structural and marine applications.
Meanwhile, 4043 offers better flowability with its lower melting point—ideal for beginners and high-temperature environments above 150°F. 5356 works better for projects requiring post-weld anodizing, while 4043 provides smoother welds with less spatter.
Consider your specific requirements—strength needs, environment, and your welding experience—to select the perfect aluminum filler metal. Read on for detailed insights!
4043 vs 5356: Choosing the Right Aluminum Filler Metal

Selecting between 4043 and 5356 aluminum filler metals depends on your specific welding project needs.
These two fillers make up about 85% of aluminum welding applications, but they have different properties that make each better for certain jobs.
What's the Difference Between 4043 and 5356 Aluminum Filler?
4043 is an aluminum-silicon filler with about 5% silicon content. It flows easily during welding and creates smooth, clean welds.
5356 is an aluminum-magnesium filler with approximately 5% magnesium. It's stronger than 4043 and resists corrosion better.
The main differences show up in how they work and what they're good for. 4043 melts at a lower temperature, making it easier to use for beginners.
5356 creates stronger welds but can be harder to work with.
Your choice depends on what you're welding and what properties you need in the finished product.
Chemical Composition: 4043 vs 5356
4043 Composition:
- 5% Silicon (main alloying element)
- Very low magnesium content
- Remainder mostly aluminum
5356 Composition:
- 5% Magnesium (main alloying element)
- Low silicon content
- Small amounts of manganese and chromium
- Remainder mostly aluminum
The silicon in 4043 gives it good fluidity when melted. This helps it flow into joint gaps easily.
The magnesium in 5356 increases strength and corrosion resistance. This makes it ideal for marine applications where salt exposure is common.
When working with 5xxx series aluminum alloys (which contain magnesium), 5356 filler is usually better. For 6xxx series alloys, either filler can work well.
Mechanical Properties Comparison
Strength Comparison:
- 4043: Approximately 11 KSI shear strength
- 5356: Approximately 18 KSI shear strength
5356 creates stronger welds, making it better for structural parts that need to hold heavy loads. Its higher tensile strength means it can handle more stress before failing.
4043 produces slightly more ductile welds. This means they can bend more before breaking, which can be good for parts that need to flex.
For color matching after anodizing, 5356 works better. 4043 welds often turn dark gray or black after anodizing while 5356 maintains a closer match to the base metal.
Temperature performance differs too. 4043 performs better in high heat applications, while 5356 maintains strength better at lower temperatures.
Weldability and Flow Characteristics
4043 has excellent fluidity when melted. This makes it easier to:
- Fill gaps in poorly fitted joints
- Create smooth, attractive weld beads
- Prevent hot cracking in certain alloys
4043 is more forgiving for beginners because it flows better and has a lower melting point. You'll find it easier to work with when you're learning.
5356 has a higher melting temperature and doesn't flow as easily. It can be harder to get smooth welds, especially for new welders. However, 5356 wire feeds better in wire-feed welding machines.
Crack sensitivity is another factor. 4043 works better for crack-sensitive alloys like 6061. The silicon content helps prevent hot cracking during solidification.
When working with dirty or oxidized aluminum, 5356 often performs better because of its cleaning action.
Whether you choose 4043 or 5356 filler, proper technique matters. Perfect your wire welding skills today. Check out our guide How To Weld With a Wire Welder: Basics for Quality Joining for expert tips on getting flawless results with either alloy.
When To Use 4043 Aluminum Filler Metal
4043 aluminum filler metal is one of the most popular choices for welding aluminum materials. It contains about 5% silicon, which gives it special properties that work well for certain jobs.
Compatible Base Materials for 4043
4043 filler metal works best with specific types of aluminum. You should use it when welding:
- 6xxx series alloys (like 6061)
- 3xxx series alloys
- 4xxx series alloys
- Cast aluminum containing silicon
4043 is perfect for welding aluminum castings to wrought aluminum. When you need to join different kinds of aluminum, 4043 often makes a good choice because of its versatility.
The silicon in 4043 helps prevent cracking in materials that are crack-sensitive. This makes it especially useful for automotive parts and structural components.
Advantages of 4043 in Specific Applications
4043 offers several benefits that make it ideal for certain jobs:
- Better flow characteristics - It flows smoothly and creates less spatter
- Lower melting point than 5356, making it easier to work with
- Reduced risk of hot cracking in welds
- Cleaner welds with less oxide formation
You'll find 4043 works great for thin materials because it's less likely to burn through. It also produces cleaner, more attractive welds that may need less finishing work.
It's a top choice for radiators, heat exchangers, and other components where appearance matters. 4043 also works well with automatic welding machines because of its consistent flow.
Limitations of 4043 Filler Alloy
Despite its benefits, 4043 isn't perfect for every job:
- Lower tensile strength compared to 5356 filler
- Not recommended for welding 5xxx series alloys
- Poor color match after anodizing (turns dark gray)
- Less corrosion resistance in marine environments
You should avoid using 4043 when your project requires high strength or will be exposed to saltwater. It's also not the best choice when you need the weld to match the base material after anodizing treatment.
When working with alloys containing more than 2% magnesium, 4043 can form brittle compounds at the weld interface. This can lead to poor mechanical properties and potential weld failures.
Also, learn how your current type affects aluminum welding performance. Discover critical insights in our article AC and DC Welding: Understanding the Differences.
When To Use 5356 Aluminum Filler Metal

5356 filler metal is a popular choice for many aluminum welding applications due to its strength and corrosion resistance. This aluminum-magnesium alloy contains about 5% magnesium and performs exceptionally well in specific situations.
Compatible Base Materials for 5356
5356 filler metal works best with specific aluminum alloys. You should use it when welding:
- 5xxx series alloys (5052, 5083, 5086)
- 6xxx series alloys (6061, 6063)
- 7xxx series alloys (when proper procedures are followed)
5356 creates strong welds when joining similar metals. For example, when you're welding 5052 to 5052 or 6061 to 6061, 5356 is often the best choice.
The high magnesium content in 5356 filler alloy makes it compatible with base metals that also contain magnesium. This creates a better metallurgical match and stronger welds.
You should not use 5356 with 2xxx series or cast alloys that contain copper, as this can lead to cracking.
Advantages of 5356 in Specific Applications
5356 filler metal shines in several key applications:
Marine environments: The high magnesium content gives excellent corrosion resistance in saltwater.
Structural applications: When you need higher strength welds, 5356 delivers better mechanical properties than 4043.
Color matching: 5356 creates welds that better match the color of 5xxx series alloys after anodizing.
5356 also offers:
- Higher tensile strength (38,000 psi vs 27,000 psi for 4043)
- Better feeding through wire feeders due to its stiffer nature
- Less sensitivity to cracking when welding 5xxx series alloys
You'll find 5356 commonly used in boat building, truck bodies, and railcars where strength matters.
Limitations of 5356 Filler Alloy
Despite its advantages, 5356 filler alloy isn't ideal for every job. You should be aware of these limitations:
5356 doesn't flow as smoothly as 4043. This makes it slightly harder to work with, especially for beginners. The weld bead tends to be more rounded and less flat.
Temperature considerations are important. 5356 shouldn't be used for applications with service temperatures above 150°F (65°C) or below -320°F (-196°C) as it can become susceptible to stress corrosion.
5356 costs more than 4043, which may affect your choice for large projects where cost matters.
The higher magnesium content means 5356 produces more spatter during MIG welding. You'll need to clean your work more thoroughly when using this filler metal.
Working with 4043 or 5356 aluminum filler requires proper hand protection. Aluminum welding generates intense heat and UV radiation. Explore our leather welding gloves collection for comfort and safety during your next aluminum project.
4043 vs. 5356 Performance in Different Welding Methods
The performance of 4043 and 5356 aluminum filler wires varies significantly across different welding processes. Each wire type responds uniquely to specific welding techniques and requires different handling approaches to achieve optimal results.
TIG Welding Comparison (GTAW)
When TIG welding with 4043, you'll notice it has a lower melting point, making it more fluid in the weld pool. This creates smoother welds with less spatter.
The silicon content helps the filler flow better, which is perfect for detailed work on 6061-T6 components.
4043 performs well in groove welds and butt joints where appearance matters. You'll need less heat input compared to 5356.
5356 requires more heat during TIG welding but offers better strength in fillet welds. It doesn't flow as smoothly as 4043, but this can be an advantage when building up material.
For welding aluminum with TIG, 5356 creates a brighter, whiter weld bead while 4043 tends to produce a darker finish. Many fabricators prefer 5356 for TIG when working with visible components that need anodizing.
MIG Welding Comparison (GMAW)
In MIG applications, 4043 shines with superior feedability through wire-feed systems. It's less rigid and causes less wear on contact tips and liners.
You'll experience fewer feeding issues during long production runs.
5356 can be more challenging to feed in GMAW setups due to its stiffness. However, it excels in providing stronger welds on structural components.
The magnesium content in 5356 makes it better for welding thicker aluminum sections.
When MIG welding aluminum, 5356 typically handles the high-speed deposition better. You'll notice less porosity in your welds when properly set up.
For welded components that need to hold up under stress, 5356 often performs better in MIG applications.
Parameter Adjustments for Each Filler Type
For 4043, you should use:
- Voltage: 1-2 volts lower than 5356
- Wire feed speed: Can be set 5-10% higher
- Travel speed: Generally faster due to better fluidity
- Gas flow: 25-30 CFH of pure argon works best
5356 requires these adjustments:
- Amperage: Often needs 5-10% higher settings
- Voltage: Slightly higher to compensate for less fluidity
- Pulse settings: Benefits more from pulse techniques
- Weave technique: Works better with slight weaving motion
You'll need less pre-cleaning with 4043 since silicon helps break down surface oxides.
For both filler types, proper parameter settings are crucial for avoiding common defects like porosity or lack of fusion in aluminum welding.
Make sure to maximize the performance of your 4043 or 5356 filler with professional-grade equipment. Quality tools elevate your aluminum welding results. Discover our premium welding tools collection for precision and reliability.
Strength and Corrosion Considerations: 4043 vs. 5356
When choosing between 4043 and 5356 aluminum filler metals, their strength properties and resistance to corrosion play a big role in making the right choice for your project.
These two factors often determine which filler will perform best in your specific application.
Tensile Strength Differences
5356 filler metal offers much higher strength than 4043. The tensile strength of 5356 can reach up to 290 MPa, while 4043 typically provides around 186 MPa. This strength difference is important for projects that need to handle heavy loads.
Shear strength shows an even bigger gap. 5356 provides about 18 KSI (kilopounds per square inch), while 4043 offers only 11 KSI. This makes 5356 a better choice for structures built mainly with fillet welds.
For parts that will be heat-treated after welding, 4043 might work better because it's less likely to crack during treatment. But for parts that need to work well at high temperatures, 5356 keeps more of its strength when hot.
Corrosion Resistance in Various Environments
5356 stands out with superior corrosion resistance, especially in harsh conditions. It contains magnesium, which helps it fight corrosion in salty environments. This makes it perfect for marine applications like boats and offshore structures.
4043 still offers decent corrosion protection for normal indoor use. But when exposed to chemicals or saltwater, it doesn't perform as well as 5356.
For outdoor projects that face rain, sun, and changing temperatures, 5356 is usually the safer bet.
Its resistance to stress corrosion cracking is also better than 4043. Your environment should guide your choice:
- Marine/saltwater: Choose 5356
- Indoor/controlled: Either works, but 4043 is often cheaper
- Chemical exposure: 5356 offers better protection
Post-Weld Appearance and Finishing
After welding, 4043 tends to produce a shiny, smooth finish that many welders prefer. It flows better during welding, which helps create neater welds with less spatter. This can reduce the need for grinding and post-weld cleanup.
5356 welds often look duller with a frosty appearance. However, 5356 works much better if you plan to anodize your project after welding.
4043 contains silicon that can turn dark during anodizing, creating unsightly black streaks.
The ductility of each filler also affects finishing. 5356 is more ductile, meaning it can bend more before breaking.
This makes it better for projects that might flex or vibrate. 4043 is less ductile but easier to polish to a high shine if appearance is your top priority.
Common Problems and Solutions When Using 4043 vs. 5356

Both 4043 and 5356 aluminum welding wires have specific challenges that welders face. Understanding these issues can help you choose the right filler metal and achieve better results.
Preventing Cracking and Porosity
Crack sensitivity varies significantly between these two filler metals. 4043 contains silicon which gives it better crack resistance when welding 6xxx series alloys. However, it's more prone to hot cracking when used on 5xxx series aluminum.
For 4043, use these tips to prevent cracking:
- Preheat thick sections to 200-300°F
- Use stringer beads instead of weaving
- Control heat input to minimize distortion
5356 works better on 5xxx series alloys but may crack on 6xxx series. To reduce porosity with either wire:
- Clean the base metal thoroughly to remove oxides and oils
- Store filler wire properly to prevent moisture absorption
- Use proper shielding gas (usually pure argon)
- Keep a shorter arc length to minimize atmosphere contamination
Hydrogen is the main cause of porosity. Moisture on your base metal or filler wire turns to hydrogen during welding. Always wipe surfaces with acetone before welding.
Color Matching Challenges
Color matching can be tricky with aluminum welds, especially after anodizing.
4043 produces darker welds that turn gray or black after anodizing. 5356 creates welds that better match the base metal color.
For better color matching:
- On 6061 aluminum that will be anodized, 5356 provides better color match
- For non-anodized parts, 4043 often blends better with 6xxx series alloys
- Test samples before committing to large projects
- Consider post-weld treatments
Some fabricators use 4643 filler wire instead of 4043 for improved color matching after anodizing. This specialty alloy costs more but maintains better appearance for decorative applications.
If color match is critical, discuss with your customer whether the part will be painted or otherwise finished after welding.
Troubleshooting Weld Quality Issues
Common quality issues include poor fusion, inconsistent bead appearance, and weak joints.
With 4043, you might notice these problems:
- Wire feeding issues due to its softer nature
- Excessive spatter at higher amperage
- Black sooty residue around the weld
For 5356, watch for:
- Weld stiffness making it harder to work in tight spots
- More feeding problems in older wire feeders
- Higher tendency for burn-through on thin materials
To improve weld quality with either wire:
- Adjust your technique based on the wire type
- For 4043, reduce wire feed speed and voltage slightly
- For 5356, you may need higher settings due to its higher melting point
When switching between wires, always clean your liner and drive rolls. Aluminum dust builds up and causes feeding problems.
Both 4043 and 5356 fillers require careful technique to avoid common defects. Prevent costly mistakes in your aluminum projects. Master proper welding technique by reading our guide: What Is Undercut in Welding? today.
Making the Final Decision: 4043 or 5356?
Your project needs should dictate your aluminum filler choice. For structural applications requiring strength, choose 5356 (18 KSI vs 4043's 11 KSI).
For appearance, consider that 5356 anodizes closer to base aluminum color, while 4043 offers smoother welds with less spatter—perfect for beginners.
Match your filler to your base metal: 4043 for 6XXX series alloys, 5356 for 5XXX and marine applications. Budget-conscious? 4043 typically costs less.
For quality aluminum welding wire, consider ArcCaptain's reliable options. For troubleshooting help, read our guide: Common Wire Feed Welding Issues and How To Solve Them.
Frequently Asked Questions on 4043 vs. 5356
Welders often have specific questions about aluminum filler metals. The following questions address key differences between 4043 and 5356 alloys to help you make the right choice for your projects.
What are the primary applications of 5356 aluminum welding wire?
5356 aluminum welding wire works best for marine applications. It contains about 5% magnesium, giving it excellent resistance to saltwater corrosion.
This wire is ideal for boats, docks, and offshore structures. It's also great for structural parts that need strong welds.
Projects that will be anodized after welding benefit from 5356 wire. The finish looks more uniform than with other filler metals.
In what scenarios is 4043 aluminum filler rod ideal for use?
4043 filler rod works best when welding 6xxx series alloys like 6061. The silicon content in 4043 creates smooth, fluid welds.
Automotive parts and bicycle frames often use 4043. It's good for projects where appearance matters.
4043 is easier to feed through welding machines. This makes it popular for production welding where speed counts.
How does the tensile strength of 4043 and 5356 welding wires compare?
5356 has significantly higher tensile strength than 4043. The minimum shear strength of 5356 is about 18 KSI (kilopounds per square inch).
4043 has a lower shear strength of around 11 KSI. This difference matters in structures built mainly with fillet welds.
If your project needs stronger welds, 5356 gives a clear advantage over 4043.
What distinguishes the 4000 series aluminum wire from the 5000 series?
The main difference is their primary alloying elements. 4000 series (like 4043) contains silicon as its main additive.
5000 series (like 5356) uses magnesium as its main alloying element. This gives it different properties and applications.
Silicon makes 4043 flow better during welding. Magnesium gives 5356 better strength and corrosion resistance.
Can you outline the key differences in melting temperature between 4043 and 5356 aluminum wires?
4043 has a lower melting temperature range than 5356. This makes 4043 easier to weld for beginners.
The silicon in 4043 creates a wider freezing range. This gives you more time to work with the puddle while welding.
5356 solidifies faster due to its higher melting point. This can be helpful in overhead or vertical welding positions.
What factors should be considered when choosing between 4043 and 5356 filler metals?
Consider the base metal you're welding. Some aluminum alloys work better with specific filler metals.
Think about your project's environment. For marine or high-moisture areas, 5356's corrosion resistance is important.
Evaluate strength requirements. If your project needs stronger welds, 5356 offers better mechanical properties than 4043.
Consider whether the finished project will be anodized. 5356 typically provides better color matching after anodizing.