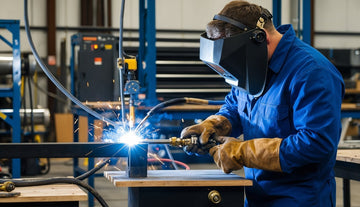
Can you weld A356 aluminum? Yes, this popular casting alloy can be successfully welded using several common techniques including Gas Tungsten Arc Welding (GTAW/TIG), Gas Metal Arc Welding (GMAW/MIG), and Friction Stir Welding (FSW).
With proper preparation and the right filler metal—typically ER4043 or ER4047—you can achieve strong, quality welds on A356 components. However, be aware that welding will affect the mechanical properties of heat-treated A356-T6, as the process creates an over-aged heat-affected zone regardless of your filler choice.
Read on to discover essential preparation steps, filler metal selection tips, and techniques to achieve the best results when welding this versatile aluminum alloy.
What Makes A356 Aluminum Different For Welding
A356 aluminum stands out in the welding world because of its unique composition and properties as a casting alloy. The silicon and magnesium content affects how it responds to heat and filler materials during the welding process.
Properties Of A356 Cast Aluminum That Affect Weldability
A356 is a popular casting alloy containing 7% silicon and 0.3% magnesium. This composition gives it good fluidity when melted, making it perfect for sand casting and die casting parts.
The silicon in A356 helps reduce cracking during welding. This is a big advantage compared to some other aluminum alloys.
However, A356 has higher thermal conductivity than steel. This means heat travels away from your weld area quickly. You need more heat input when welding A356.
The T6 heat treatment that makes A356 stronger can be affected by welding. The heat-affected zone (HAZ) loses some strength after welding. This happens because the heat changes the material's microstructure.
Comparing A356 To Other Aluminum Alloys For Welding
A356 welds similarly to 6061-T6 aluminum. Both alloys lose strength in the heat-affected zone during welding.
When choosing filler metals, A356 works well with 4043 and 5356 fillers. The 4043 filler (with silicon) gives better flow. The 5356 filler (with magnesium) provides better strength and ductility.
Unlike 7xxx series alloys, A356 has good weldability with less risk of hot cracking. This makes your welding job easier.
A356 offers better corrosion resistance than many wrought aluminum alloys. This is important for parts that will be exposed to harsh environments.
The casting process creates a different grain structure than wrought alloys. This can sometimes lead to porosity issues that affect weld quality.
Why People Ask If A356 Aluminum Can Be Welded
People question A356 weldability because it's primarily a casting alloy. Many assume cast aluminum is difficult or impossible to weld.
The T6 heat treatment of A356 causes concern. Welders worry about losing the material's strength after welding. This is a valid concern since welding does affect the mechanical properties.
Repair welding on cast parts often prompts questions. Engine components or structural parts made from A356 sometimes need repair.
DIY welders find A356 challenging due to its high thermal conductivity. It requires proper preheating and cooling techniques to avoid problems.
The different fillers available for A356 create confusion. Many don't know whether to select silicon-based or magnesium-based fillers for their specific application.
Successful A356 aluminum welding requires the right equipment for precise heat control. Explore our collection of premium welding torches to find the perfect tool for your aluminum welding projects.
Yes, You Can Weld A356 Aluminum - Best Methods
A356 aluminum is a common casting alloy that can be welded successfully with proper preparation and technique. The right welding method depends on your equipment, skill level, and the specific requirements of your project.
TIG Welding A356 Aluminum: Step-By-Step Process
TIG welding (GTAW) offers precise control for A356 aluminum. First, clean your workpiece thoroughly with a wire brush and acetone to remove all contaminants. This prevents porosity in your weld.
Set up your TIG welder with AC current and high frequency start. Use pure argon as your shielding gas at 15-20 CFH. Choose a 4043 filler rod for most A356 welds.
Preheat the A356 component to about 200°F to reduce cracking risks. This is especially important for thicker castings.
Use a larger tungsten electrode (1/8") with a ball end for better cleaning action. Keep your arc length short and maintain steady travel speed. Too much heat can damage the T6 temper in the heat-affected zone.
Let the weld cool slowly after completion. Remember that welding will affect the mechanical properties regardless of filler metal used.
MIG Welding Techniques For A356 Aluminum Castings
MIG welding (GMAW) works well for A356 when speed matters more than appearance. You'll need a spool gun or push-pull system for aluminum wire feeding.
Use ER4043 wire for most A356 applications. Set your machine to spray transfer mode with 100% argon shielding gas at 20-25 CFH.
Clean the surface meticulously before welding. Any oxide will cause serious weld problems. A stainless steel brush works best for this.
Keep your travel speed consistent but fairly quick. This helps reduce heat input to the base metal. Too slow a travel speed causes excessive heat that weakens the A356 material.
Hold the gun at a 10-15° push angle. This improves visibility and helps prevent burnthrough on thinner sections. Expect some strength reduction in the heat-affected zone after welding.
Is Friction Stir Welding Viable For A356 Components?
Friction Stir Welding (FSW) is an excellent option for A356 aluminum when weld quality is critical. This solid-state process doesn't melt the metal, which preserves more of the base material's properties.
FSW creates stronger, more ductile joints in A356 than traditional welding methods. The process introduces less heat, minimizing distortion and property changes in the heat-affected zone.
The downside is equipment cost and setup complexity. FSW requires specialized machinery not commonly available in small shops.
For high-volume production or critical aerospace/automotive applications, FSW offers significant advantages. The process works exceptionally well joining A356 to other aluminum alloys like 6061.
Consider FSW when weld appearance, strength retention, and minimal post-weld heat treatment are priorities. The process eliminates many common A356 welding issues like porosity and hot cracking.
Choosing The Right Filler Metal For A356 Aluminum

Selecting the proper filler metal is critical when welding A356 aluminum. Your choice affects weld strength, crack resistance, and final appearance.
Best Filler Alloys Compatible With A356 Aluminum
The 4xxx series fillers work best with A356 aluminum. ER4043 is the most commonly recommended filler metal for A356 welding projects. This silicon-based filler flows well and creates clean welds.
ER4047 (also called 4047) is another excellent option. It contains more silicon than 4043, which lowers the melting point and improves fluidity. This makes it perfect for applications where appearance matters.
Some welders also use ER4145 with A356. This filler contains both silicon and copper, offering good crack resistance.
Recommended Fillers for A356:
- ER4043 - Good all-purpose filler
- ER4047 - Better fluidity, shinier finish
- ER4145 - Added strength from copper content
Your project requirements will determine which of these works best for you.
Why 4043 Vs 4047 Matters When Welding A356
The choice between 4043 and 4047 filler metal affects your welding experience and results. 4043 contains about 5% silicon, while 4047 has nearly 12%.
This silicon difference changes how the metal behaves. 4047 flows better and wets the base metal more easily than 4043. This means less effort for you during welding.
4047 creates a shinier finish that many welders prefer for visible projects. But be careful - it solidifies faster than 4043, which can be tricky for beginners.
4043 offers better ductility after welding. This matters if your part will bend or flex in service. The weld becomes more brittle with 4047.
When welding thicker A356 sections, 4043 may help prevent hot cracking better than 4047. For thin sections, either filler works well.
Filler Metals To Avoid With A356 Aluminum
Not all aluminum fillers work well with A356. The 5xxx series fillers (like 5356) should generally be avoided with A356 aluminum. These magnesium-containing fillers can reduce corrosion resistance in your welds.
5356 filler metal doesn't match the chemistry of A356 well. This mismatch can lead to strength issues in the finished weld. It may work in non-critical applications, but isn't recommended for structural parts.
Filler materials with high copper content (except 4145) can cause galvanic corrosion problems with A356. This happens when dissimilar metals touch in a moist environment.
Fillers to avoid:
- 5356, 5183, 5556 (magnesium-based)
- 2xxx series (high copper)
- 7xxx series (zinc-based)
Common Problems When Welding A356 Aluminum

Welding A356 aluminum presents several challenges that can affect the quality of your finished project. Being aware of these issues ahead of time will help you achieve better results and stronger welds.
Preventing Porosity In A356 Aluminum Welds
Porosity is one of the biggest problems when welding A356 aluminum. These tiny holes form when gas gets trapped in the weld. To prevent this issue, you must clean the surface thoroughly. Remove all oil, grease, and oxides with a stainless steel brush or solvent before welding.
Your shielding gas matters too. Use pure argon or an argon-helium mix to protect the weld pool. Keep the gas flow rate between 15-20 CFM for best results.
Preheat your A356 parts to about 200-250°F to drive off moisture. This helps reduce hydrogen, a main cause of porosity. Also, check your filler rod for contamination. Store filler materials in a clean, dry place to keep them free from moisture.
Avoiding Hot Cracking In A356 Castings
Hot cracking happens when the weld cools and shrinks too quickly. A356 is especially prone to this problem because of its casting structure. To avoid cracks, use a proper filler metal like 4043 or 5356.
Lower your welding speed to reduce stress during cooling. Fast welding creates more heat input and increases cracking risk. Try using an interpass temperature of 200°F between weld passes.
The T6 heat treatment of A356 makes it more likely to crack. Remember that welding will weaken the heat-affected zone no matter what filler you use. Using a backing plate can help control cooling rates and prevent cracks.
Dealing With Silicon Content In A356 During Welding
A356 contains about 7% silicon, which affects how you weld it. This silicon content gives it good fluidity when melted but can cause problems during welding.
Choose your filler metal wisely. 4043 (with 5% silicon) works well with A356's silicon content.
Your welding technique needs adjustment too. Use a slightly weaving motion rather than a straight line. This helps distribute heat more evenly across the high-silicon material.
Clean any silicon oxide that forms on the surface. It has a higher melting point than the base metal.
Use AC current with TIG welding to help break up these oxides. Set your machine to 60-70% electrode negative for better cleaning action during welding.
When welding A356 aluminum, protecting yourself from sparks and UV radiation is essential. Check out our stylish and protective welding caps collection to stay safe while maintaining comfort during long welding sessions.
How Heat Treatment Affects Welded A356 Aluminum
The welding process significantly changes the properties of A356 aluminum. When heat is applied during welding, it alters the carefully engineered T6 temper that gives this aluminum its strength.
Welding A356-T6: Strength Considerations
When you weld A356-T6 aluminum, the heat affects its strength in important ways. The high temperatures from welding cause over-aging in the heat-affected zone (HAZ). This means the area near the weld becomes weaker than the original material.
The welded area's properties become similar to aluminum in the annealed condition. This happens regardless of which filler metal you use.
The strength drop happens because welding disrupts the precipitation hardening that creates the T6 temper.
A356-T6 behaves similarly to 6061-T6 when welded. Both are heat-treatable alloys strengthened through precipitation hardening.
Expect a 30-40% reduction in strength in the HAZ compared to the base metal.
Post-Weld Heat Treatment Options For A356
After welding A356 aluminum, you have several heat treatment options to restore strength:
- Full Solution Heat Treatment: Heating the entire part to dissolve the precipitates, followed by quenching
- Artificial Aging: Heating at specific temperatures to form strengthening precipitates
- Room Temperature Aging: Allows some natural aging but won't fully restore T6 properties
The best approach depends on your part size and equipment. Full solution heat treatment gives the best results but requires careful temperature control.
You need to consult with heat treatment specialists to determine the right process for your specific application.
Large parts might warp during quenching, so proper fixturing is important.
Restoring Properties After Welding A356 Aluminum
You can restore much of the original strength to welded A356 aluminum with proper heat treatment. Using AMS4181 weld wire (which matches A356's composition) helps achieve the best results.
Full heat treatment includes:
- Solution treatment at about 1000°F (538°C)
- Water quenching
- Artificial aging at around 310°F (154°C) for several hours
This process can recover up to 90% of the original T6 properties in many cases. The success depends on your welding technique and heat treatment quality.
Without heat treatment, the weld and HAZ remain significantly weaker than the base metal.
Some natural aging happens at room temperature, but it won't reach T6 strength levels. For critical structural parts, post-weld heat treatment is usually necessary.
Alternative Joining Methods For A356 Aluminum

While A356 aluminum can be welded, there are situations where other joining methods might work better. These alternatives can help preserve the material's properties and provide strong connections without the heat-related challenges of welding.
When Welding A356 Aluminum Isn't Recommended
Welding A356 aluminum isn't always the best choice. The heat from welding can harm the heat-affected zone (HAZ) and reduce the mechanical properties of this casting alloy.
You should avoid welding A356 when:
- The parts need to maintain their full T6 heat-treated strength
- The components have thin sections that might warp
- The casting has internal porosity that could lead to weld defects
- High precision is required for the final assembly
The silicon and magnesium in A356 can also make welding tricky. These elements affect how the metal flows when heated and can lead to hot cracking if proper techniques aren't used.
For critical structural parts where strength is important, other joining methods might be safer.
Mechanical Fastening Vs. Welding For A356
Mechanical fastening offers several benefits over welding for A356 aluminum parts.
Benefits of mechanical fastening:
- Preserves the T6 heat treatment and full strength of the material
- Creates joints that can be taken apart later if needed
- Doesn't introduce thermal stress or distortion
- Works well for joining A356 to different metals
Common mechanical fasteners for A356 include:
- Bolts and nuts with lock washers
- Self-tapping screws designed for aluminum
- Rivets, including blind rivets for one-side access
- Press-fit pins for precise alignment
When using mechanical fasteners, you should consider galvanic corrosion if joining A356 to different metals. Using stainless steel fasteners or adding insulating washers can help prevent this problem.
Adhesive Bonding Options For A356 Components
Adhesive bonding provides a strong, lightweight way to join A356 aluminum without heat damage.
The best adhesives for A356 aluminum include:
- Epoxy systems: Offer excellent strength and resistance to chemicals
- Structural acrylics: Provide good impact resistance and faster curing
- Polyurethanes: Offer flexibility and good performance in varied temperatures
Before bonding A356, proper surface preparation is critical. You should:
- Clean the surface with acetone or alcohol
- Roughen with sandpaper (80-120 grit)
- Apply an aluminum primer if recommended by the adhesive manufacturer
Adhesive bonding works especially well for joining A356 to different materials like composites or plastics. It also creates a seal that prevents moisture and contaminants from reaching the joint.
For best results, follow the adhesive manufacturer's curing time and temperature recommendations.
A356 is a common cast aluminum alloy that requires specific approaches for successful joining. Dive deeper into specialized methods with our detailed article Welding Cast Aluminum: Tips and Techniques to overcome common challenges when working with cast materials.
Final Thoughts
Yes, you can definitely weld A356 aluminum with proper techniques and preparation. Success depends on thorough cleaning, selecting the right filler metal (typically 4043 or 4047), and understanding how welding affects the alloy's properties.
Whether using GTAW, GMAW, or friction stir welding, remember that the heat-affected zone will experience reduced mechanical properties. With practice and attention to detail, you can achieve strong, quality welds on A356 components.
While challenging for beginners, the workability of this popular casting alloy makes it an excellent choice for various applications requiring both casting and welding processes.
Also learn the science behind successful aluminum welding in our latest guide What Temperature Does Aluminum Melt: Welding Metal Tips to perfect your temperature control techniques.
Frequently Asked Questions
What are the challenges of welding A356 aluminum compared to other alloys?
A356 aluminum can be tricky to weld because it's a cast alloy. One big problem is the presence of pores and inclusions in the material. These defects can lead to weak welds.
Surface contamination is another challenge. A356 often has oils or oxides that must be removed before welding.
The alloy also loses strength in the heat-affected zone (HAZ). This happens because the heat from welding over-ages the material, similar to what happens with 6061-T6 aluminum.
Which welding method is most suitable for A356 aluminum?
Gas Tungsten Arc Welding (GTAW), also called TIG welding, works best for A356 aluminum. It gives you good control and clean welds.
Gas Metal Arc Welding (GMAW or MIG) can also be used for thicker pieces. It's faster but offers less precision.
Friction Stir Welding (FSW) is excellent for A356 because it creates strong joints without melting the material. This helps avoid many common welding defects.
How does the silicon content in A356 aluminum affect its weldability?
The silicon in A356 (about 7%) improves its weldability. Silicon lowers the melting point and improves fluidity of the molten metal.
This high silicon content helps reduce cracking during welding. The silicon also makes the weld pool flow better.
However, too much silicon can make the weld brittle. A356 has a good balance that makes it one of the most weldable aluminum casting alloys.
What pre-welding treatments are recommended for A356 aluminum?
Thorough cleaning is essential. Remove all oils, greases, and oxides from the surface with a degreaser and stainless steel brush.
Preheat the A356 parts to about 200-300°F (93-149°C). This reduces thermal shock and helps prevent cracking.
Check the quality of your cast material. X-ray or dye penetrant tests can find hidden pores or inclusions that might cause problems during welding.
Can A356 aluminum be welded without a filler material?
Yes, A356 can be welded without filler in some cases, especially for simple joints or repairs. This is called autogenous welding.
Most professionals recommend using filler material for best results. ER4043 is the preferred filler for A356 aluminum, while ER4047 is also suitable.
Avoid using 5356 filler with A356, even though it's common for other aluminum alloys. The welding handbook doesn't recommend this combination.
What post-welding processes can enhance the strength of welded A356 aluminum?
Heat treatment is needed to restore original strength after welding A356-T6. The welding process reduces strength in the heat-affected zone.
A full solution heat treatment (T4) followed by aging is required to get back to T6 properties. Room temperature aging alone won't restore full strength.
Stress relief treatments can help reduce distortion and cracking. These should be done before final machining of the welded parts.