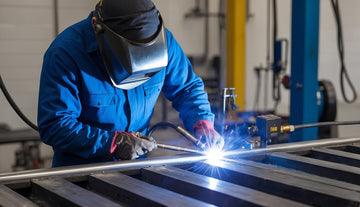
Interpass temperature is when you're welding metal pieces together, and the temperature between weld passes matters a lot. It's the heat level of your weld area before you start the next pass in a multi-pass weld.
Controlling interpass temperature is critical because it affects the quality, strength, and overall integrity of your finished weld joint.
Interpass temperature typically needs to stay below 300°C (572°F), though this varies by material. If the metal gets too hot between passes, you might face problems like distortion or weak spots.
Too cold, and the weld might crack or not fuse properly. You need to find that "just right" temperature zone for your specific project.
Welders use different methods to check and control this temperature. Some use temperature sticks, infrared thermometers, or thermal imaging cameras.
Proper interpass temperature management helps you create welds that will last and perform as needed. Read on to learn about interpass temperature and be come an expert in knowing the difference between a weld that fails and one that holds strong for years.
Interpass Temperature in Welding

Interpass temperature plays a crucial role in welding quality and outcomes. Proper management of this temperature affects everything from weld strength to crack prevention.
What Is Interpass Temperature and Why It Matters
Interpass temperature is the temperature of the weld area between successive weld passes in multi-pass welding. Think of it as the "waiting temperature" before you start your next weld pass. This temperature matters because it affects how your weld forms and how strong it will be.
When interpass temperature is too high, your weld might become weak or brittle.
If it's too low, you might get cracks or poor fusion.
Proper interpass temperature control prevents problems like:
- Hydrogen cracking (cold cracking)
- Excessive distortion
- Poor mechanical properties
- Residual stress buildup
Your weld's quality depends on keeping this temperature just right. Not too hot, not too cold—like Goldilocks of welding!
Measuring and Monitoring Interpass Temperature
You have several tools to check interpass temperature:
Contact Methods:
- Thermocouples (most accurate)
- Temperature-indicating crayons (melt at specific temperatures)
- Digital contact thermometers
Non-Contact Methods:
- Infrared thermometers (quick but affected by surface conditions)
- Thermal cameras (good for seeing the whole heat pattern)
Always measure in the area where you'll place your next weld pass.
Take readings about 1 inch (25mm) from the weld joint.
For critical welds, continuous monitoring with attached thermocouples gives the best results.
Remember to check your measuring tools regularly for accuracy. Even the best welders can't control what they can't measure correctly.
Interpass Temperature Requirements by Code
Different welding codes specify interpass temperature requirements based on safety and quality needs.
AWS D1.1 (Structural Welding Code):
- Usually specifies maximum interpass temperatures
- Often requires 550°F (290°C) maximum for structural steel
- May vary based on material thickness and grade
ASME Boiler and Pressure Vessel Code:
- Specifies both minimum and maximum temperatures
- For carbon steel: typically 50-350°F (10-175°C)
- For chrome-moly steels: often higher minimum temperatures
Your Welding Procedure Specification (WPS) must follow these codes. The WPS is your recipe for welding—follow it exactly!
Code requirements exist because they've been proven to produce safe, strong welds.
Always check the specific code that applies to your project. Requirements change based on the importance of the structure you're building.
Interpass Temperature for Different Metal Types
Each metal type has unique interpass temperature needs:
Carbon Steel:
- Generally 250-550°F (120-290°C)
- Higher carbon content = higher minimum temperature
- Prevents hydrogen cracking
Stainless Steel:
- Usually lower at 300-350°F (150-175°C) maximum
- Higher temperatures can reduce corrosion resistance
- May need minimum temperatures for thick sections
Aluminum:
- Very low interpass temperatures
- Often no preheat needed
- Control maximum to prevent weakness
Alloy Steels:
- Typically need higher minimums (300-400°F/150-200°C)
- Maximum often 550°F (290°C)
- Critical for preventing cracks in these sensitive materials
The metal's thickness also matters.
Thicker pieces usually need higher minimum temperatures but similar maximums.
Your WPS should spell out exactly what's needed for your specific material.
Controlling Interpass Temperature in Multi-Pass Welds
Keeping interpass temperature in range takes planning and skill.
When Temperature Is Too Low:
- Use gas torches for spot heating
- Increase ambient temperature in the work area
- Use electric heating blankets for large pieces
When Temperature Is Too High:
- Let the weld cool naturally (most common)
- Use compressed air (when allowed by procedure)
- Schedule your weld sequence to allow cooling time
Practical Tips:
- Work in a pattern that lets hot areas cool
- Use heat sinks on smaller pieces
- For big jobs, have multiple parts to work on while others cool
- Track temperature regularly between passes
Automated welding systems often include built-in cooling pauses and temperature monitoring.
For manual welding, you need to be disciplined about checking before each pass.
Troubleshooting Interpass Temperature Problems
When interpass temperature issues arise, here's how to fix them:
Problem: Cracking in Completed Welds
- Likely cause: Interpass temperature too low
- Solution: Increase minimum temperature, slow cooling rate
Problem: Weak, Soft Welds
- Likely cause: Interpass temperature too high
- Solution: Allow proper cooling between passes, monitor more frequently
Problem: Excessive Distortion
- Likely cause: Uneven heating/cooling cycles
- Solution: Better temperature control, balanced welding sequence
Problem: Inconsistent Temperature Readings
- Likely cause: Poor measurement technique or equipment
- Solution: Calibrate tools, standardize measurement locations
Document any problems and solutions in your welding logs.
This helps track what works and what doesn't.
Remember that temperature problems often show up as weld defects later, so catching them early saves time and money.
Advanced Interpass Temperature Considerations
Beyond the basics, these factors also affect interpass temperature needs:
Microstructure Development:
- Different cooling rates create different grain structures
- Finer grains (from controlled cooling) generally mean stronger welds
- The HAZ (Heat Affected Zone) quality depends heavily on temperature control
Environmental Factors:
- Ambient temperature affects cooling rates
- Wind can create uneven cooling
- Humidity can introduce hydrogen (increasing crack risk)
Joint Design Impact:
- Thicker joints hold heat longer
- Complex joint designs may trap heat in certain areas
- Heat sinks might be needed for small, thick parts
Shielding Gas Influence:
- Some gases conduct heat differently
- Gas flow can cool the weld area
- Preheated gas can help maintain interpass temperature
Final Thoughts
Getting your interpass temperature right isn't just about following rules—it's your secret weapon for creating welds that truly stand the test of time! When you master this critical variable, you'll see immediate improvements in your work: stronger joints, fewer defects, and welds that sail through inspection every time. The small effort of monitoring temperatures between passes pays massive dividends in quality and consistency.
Ready to level up your temperature control game? Check out ArcCaptain's premium welding equipment.
And while you're boosting your skills, don't miss our guide: The Best Way to Weld Cast Iron: Guide, Tips, & Recommendations—your next welding challenge solved!
Frequently Asked Questions
What factors determine the appropriate interpass temperature for welding different materials?
The base metal type is the most important factor. Different metals need different temperature ranges to weld properly.
The thickness of the material also matters. Thicker materials usually need higher interpass temperatures.
Your welding process (TIG, MIG, or stick) affects temperature needs too. Some processes put more heat into the metal than others.
The welding code or specification for your job may set strict limits. Always check what standards apply to your project.
How can one accurately measure the interpass temperature during the welding process?
Temperature crayons are a simple way to check. They melt at specific temperatures to show you when you've reached the right heat.
Digital thermometers with surface probes give more exact readings. They're fast and don't leave marks on your work.
Infrared thermometers let you measure from a distance. Make sure yours is adjusted for the metal's shine to get correct readings.
For critical work, attach thermocouples directly to the weld area. These give the most accurate measurements but take more setup time.
Why is maintaining the correct interpass temperature crucial for weld quality?
Correct temperatures prevent hydrogen cracking. Too cold and hydrogen can get trapped in the weld, causing cracks later.
The right temperature helps control the cooling rate. This directly affects the weld's strength and toughness.
Interpass temperature shapes the weld's microstructure. This determines many properties like hardness and how it handles stress.
It affects all passes after the first one, unlike preheat which only affects the first pass. This makes it even more important for multi-pass welds.
What are the recommended interpass temperature ranges for carbon steel and stainless steel?
For carbon steel, most codes recommend 250-550°F (120-290°C). Lower-carbon steels can often use the lower end of this range.
High-strength carbon steels usually need temperatures closer to 300-400°F (150-200°C) to avoid becoming too hard.
Stainless steel typically requires lower interpass temperatures, around 200-350°F (95-175°C). This helps maintain corrosion resistance.
Austenitic stainless steels (like 304 and 316) should stay under 350°F (175°C) to prevent chromium carbide formation.
At what point in the welding process should the interpass temperature be checked?
Check right before starting each new pass. This ensures the metal is at the correct temperature when you begin welding.
For long welds, you may need to check at multiple points. The temperature can vary along the joint.
After making adjustments to cool or heat the metal, check again.
Don't start the next pass until you confirm the temperature.
In production welding, establish a rhythm of checking. This might mean testing after specific time intervals between passes.
What implications does exceeding the maximum interpass temperature have on the integrity of the weld?
Excessive heat can reduce the weld's strength. The metal may become softer than needed for your application.
High temperatures can cause grain growth in the metal. This makes the weld more brittle and prone to cracking.
In stainless steel, too much heat promotes chromium carbide formation. This leads to reduced corrosion resistance near the weld.
Distortion and warping become more likely with higher temperatures. Your parts may not fit together correctly after welding.