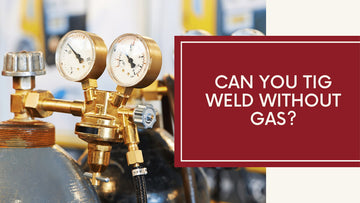
Can you TIG weld without gas? TIG welding’s famed precision relies on shielding gas to protect welds—but what if you skip it? Known for its precision and clean results, TIG welding traditionally relies on shielding gas to protect the weld pool from contamination. But what happens when gas isn’t an option?
In this article, we’ll explore the risks, limitations, and practicality of gasless TIG welding. From oxidation concerns to alternative methods, we’ll break down whether bypassing gas is truly viable—and what it means for your projects.
Basics of TIG Welding

Tungsten Inert Gas (TIG) welding, also known as Gas Tungsten Arc Welding (GTAW), is an electric arc welding process that uses a tungsten electrode to produce the weld. The weld pool is protected from atmospheric contamination by an inert gas, typically argon.
TIG welding is known for producing high-quality, precise welds with minimal distortion. It is commonly used in industries such as aerospace, automotive, and manufacturing.
The Role of Shielding Gas in TIG Welding
Shielding gas is a crucial component of TIG welding. It is used to protect the weld pool from contamination by atmospheric gases such as oxygen and nitrogen. This is important because these gases can cause porosity in the weld, reducing its strength and durability.
Argon is the most commonly used shielding gas in TIG welding. It is an inert gas, meaning it does not react with other elements. This makes it an ideal choice for protecting the weld pool from contamination.
TIG Welding Equipment
To perform TIG welding, you will need a few key pieces of equipment:
- Tungsten electrode: This is the electrode that produces the electric arc and melts the base metal.
- Power supply: This provides the electrical current needed to create the arc.
- Shielding gas supply: This provides the inert gas used to protect the weld pool.
- Welding torch: This is the tool used to hold the tungsten electrode and direct the arc onto the base metal.
In addition to these basic components, TIG welding also requires specialized equipment such as a high-frequency generator to start the arc and a foot pedal to control the amperage.
Need reliable gear instead? ArcCaptain delivers top-tier welders—like aluminum welders, MIG 110V, and compact TIG models—to nail flawless results. Gas or gasless, master your craft!
TIG Welding Without Gas
No, TIG welding cannot be performed without shielding gas without sacrificing weld quality, safety, and equipment longevity. Here’s why:
Shielding Gas Is Essential
TIG welding relies on inert gas (typically argon or argon-helium mixes) to:
- Protect the tungsten electrode and molten weld pool from oxygen, nitrogen, and airborne contaminants.
- Prevent oxidation, porosity, and weak welds.
- Cool the weld torch during operation.
Without gas, the weld becomes discolored, brittle, and prone to failure. The torch may also overheat and sustain damage.
What Gas Is Used for TIG Welding?
TIG (Tungsten Inert Gas) welding demands precision, and shielding gas is non-negotiable. Here’s a breakdown:
Primary Gas: Pure Argon
100% argon is preferred for its stability, density, and non-reactive properties. It shields welds effectively in flat positions, settling over the weld pool due to its weight.
- Argon is cost-effective and produces clean, precise welds without discoloration.
- Argon’s density shields the tungsten electrode and weld pool effectively, even at low flow rates. It also works for nearly all metals (steel, aluminum, titanium).
Argon-Helium Mixes
Adding helium improves heat input and penetration, ideal for thicker materials or automated processes. However, pure helium is rarely used manually due to arc instability.
- When to Use: For thicker materials (e.g., aluminum or copper) requiring higher heat input.
- Ratio: Common blends include 75% argon/25% helium or 50/50 mixes.
- Trade-off: Helium increases cost and requires higher flow rates.
Specialty Gases
- Hydrogen-Argon Mixes: Used for austenitic stainless steel to improve arc constriction and travel speed (e.g., 95% argon/5% hydrogen).
- Nitrogen-Argon: Rarely used for duplex stainless steels to preserve corrosion resistance.
Gas-free TIG welding is not viable—it risks contamination, equipment damage, and unsafe results. Always use high-purity shielding gas and ensure proper ventilation.
What Doesn’t Work for TIG?
- Oxygen or CO₂: Reactive gases oxidize tungsten and melt electrodes. Only used in MIG/MAG processes.
- Nitrogen Alone: Causes severe porosity and brittleness in most metals.
Learn more about gas and TIG welding by reading our guide: What Gas Is Used for TIG Welding?
TIG Welding Safety Considerations
When TIG welding without gas, it is important to take safety precautions. It is important to work in a well-ventilated area and wear appropriate protective gear, including a welding helmet, gloves, and a respirator.
Metals Compatible with TIG Welding

TIG welding is a versatile welding process that can be used to weld a wide range of metals. The most commonly welded metals using TIG welding are steel, aluminum, and stainless steel. TIG welding is also suitable for welding other metals, such as copper, mild steel, ferrous metals, non-ferrous metals, carbon steel, cast iron, and brass.
Impact on Different Welding Materials
When TIG welding without gas, it is important to consider the impact on different materials. For instance, welding aluminum without gas can lead to porosity and contamination, which can weaken the weld.
Similarly, welding stainless steel without gas can lead to oxidation and discoloration, which can affect the appearance and strength of the weld.
To avoid these issues, it is recommended to use a shielding gas when welding aluminum and stainless steel. However, if you must TIG weld without gas, it is important to clean the surfaces of the materials thoroughly before welding to prevent contamination.
Perfect your TIG welding. Dive into advanced techniques, gas mixing ratios, and metal-specific best practices in our Ultimate TIG Welding Gas Guide.
Technical Aspects of TIG Welding
TIG welding, also known as Gas Tungsten Arc Welding (GTAW), is a welding process that uses a non-consumable tungsten electrode to produce a weld. The process is known for its high quality, versatility, and ability to weld a wide range of materials. In this section, we will discuss some of the technical aspects of TIG welding.
Controlling Heat Input
One of the most critical aspects of TIG welding is controlling the heat input. The heat input affects the weld quality, penetration, and strength. Too much heat can cause overheating, while too little heat can result in poor penetration and weak welds. It’s essential to maintain a stable and consistent heat input during the welding process.
Weld Penetration and Strength
TIG welding produces high-quality welds with excellent penetration and strength. The process allows for precise control of the heat input, resulting in deep penetration and strong welds.
TIG welding is also known for its ability to produce welds with low levels of porosity and impurities, which enhances the mechanical properties of the weld.
Dealing with Contamination and Impurities
TIG welding requires a clean and contaminant-free welding environment to produce high-quality welds. Contamination and impurities can cause oxidation, porosity, and weak welds. It’s crucial to remove any contaminants and impurities from the welding area before starting the welding process.
Additionally, using the right shielding gas can help prevent contamination and impurities from entering the weld.
Conclusion
TIG welding cannot be performed without shielding gas in standard practice. Gas (typically argon) is mandatory to protect the tungsten electrode and molten weld pool from atmospheric contamination.
Without it, the arc becomes erratic, welds suffer porosity/oxidation, and results are structurally unsound.
While experimental methods like flux-coated rods exist, these are niche, unreliable, and not true TIG welding. Always use inert gas for clean, durable welds compliant with industry standards.
Want to improve your TIG Skills? Unlock pro techniques for flawless results in our guide: Mastering TIG Welding Polarity: PRO Tips for Perfect Welds.
Frequently Asked Questions
Is gasless TIG welding any good?
No. True TIG welding requires shielding gas (like argon) to protect the weld from contamination. Without gas, the arc becomes unstable, the tungsten electrode degrades, and welds suffer severe porosity, oxidation, and weakness.
While "gasless TIG" is sometimes marketed (using flux-coated rods), these methods are unreliable, produce poor-quality welds, and deviate from standard TIG principles. For gas-free welding, consider stick welding (SMAW) or flux-core MIG instead.
Is it possible to TIG weld with a flux core wire?
No, TIG welding cannot be done with a flux core wire. TIG welding requires a filler rod to be added to the weld pool manually. Flux core wire is used in a different welding process called flux-cored arc welding (FCAW).
What are the consequences of TIG welding without using gas?
TIG welding without gas can result in poor quality welds with excessive porosity, lack of fusion, and contamination. The weld area will be exposed to air, which will cause oxidation and contamination of the weld pool. This can lead to weakened welds that are more likely to fail.
Can aluminum be TIG welded using a gasless method?
Aluminum cannot be TIG welded using a gasless method. Aluminum requires a high-purity shielding gas, such as argon, to protect the weld area from contamination and oxidation. Gasless TIG welding is not suitable for welding aluminum.