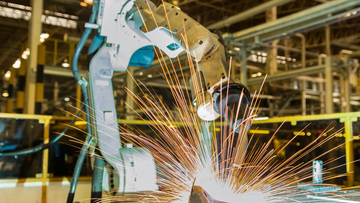
Cobot welding is emerging as a transformative trend in industrial automation. Collaborative robots, or cobots, are designed to work alongside humans, bringing a new level of efficiency, flexibility, and safety to welding processes.
This article will provide a comprehensive overview of cobot welding, exploring its benefits, applications, considerations, and future trends.
What is Cobot Welding?
Cobots are a class of robots designed to work in close collaboration with humans. Unlike traditional industrial robots that operate in isolated, guarded cells, cobots are equipped with advanced safety features such as force-torque sensors and vision systems.
These features allow them to detect and respond to human presence, ensuring safe and efficient cooperation.
How Cobot Welding Works
Cobot welding involves integrating a welding system comprising a welding power source, wire feeder, and torch with a cobot arm.
Safety sensors like force-torque sensors and vision systems enable safe human-robot interaction.
Programming methods for cobot welding include lead-through programming, where the operator physically guides the robot, and offline programming, which involves creating welding paths using specialized software.
Benefits of Cobot Welding
Enhanced Safety
Cobots are designed to work safely alongside humans, significantly reducing the risk of workplace accidents. Their built-in safety features ensure that they can detect and respond to human presence, making them ideal for collaborative tasks.
Increased Flexibility and Adaptability
Cobots can be easily reprogrammed and redeployed for different welding tasks, making them highly adaptable to various production needs. This flexibility is particularly beneficial for smaller batch sizes and high-mix, low-volume production.
Improved Efficiency and Productivity
By automating repetitive tasks, cobots can deliver consistent weld quality and faster cycle times. This leads to improved overall efficiency and productivity in welding operations.
Reduced Labor Costs
Cobots can augment human welders, reducing the need for a large welding workforce for certain tasks. This can lead to significant labor cost savings while maintaining high-quality welds.
Improved Weld Quality and Consistency
Cobots offer precision and repeatability in welding tasks, resulting in more consistent and higher-quality welds. This is crucial for industries where weld quality is of paramount importance.
Easier Programming and Deployment
Cobots are known for their user-friendly programming interfaces, making them easier to deploy compared to traditional industrial robots. This ease of use reduces the time and expertise required for setup and operation.
Space Savings
Cobots often have a smaller footprint and do not require large safety cages, saving valuable floor space in manufacturing facilities.
Applications of Cobot Welding
Cobot welding is being successfully implemented across various industries, including:
- Automotive: Small part welding, tack welding
- Aerospace: Precision welding of smaller components
- Metal Fabrication: General welding tasks, fixture welding
- Agriculture: Repair and manufacturing of equipment
- Consumer Goods: Welding of appliance parts, furniture frames
Cobots are particularly suitable for tasks requiring human-robot collaboration and high-mix, low-volume production.
Considerations and Challenges of Cobot Welding
Initial Investment Costs
The upfront costs of purchasing and integrating a cobot welding system can be significant. However, the long-term benefits often outweigh these initial expenses.
Integration Complexity
Proper integration with existing welding equipment and workflows is essential for successful cobot welding implementation. This may require specialized expertise and careful planning.
Skill Requirements for Programming and Maintenance
Personnel trained in cobot programming, operation, and maintenance are necessary to ensure smooth and efficient operation. While cobots are user-friendly, some level of training is still required.
Limitations in Reach and Payload
Cobots typically have smaller reach and payload capacities compared to traditional industrial robots. This may limit their suitability for certain tasks.
Suitability for Certain Welding Processes and Materials
Not all welding processes or materials may be ideal for cobot welding. It's important to assess the specific requirements of each application to determine suitability.
Safety Standards and Regulations
Adhering to relevant safety standards and conducting thorough risk assessments are crucial for safe cobot welding implementation. Compliance ensures the well-being of both human workers and the cobots themselves.
Safety in Cobot Welding
Cobots are equipped with various safety features, including force-torque sensors and speed and separation monitoring.
These features enable safe human-robot collaboration by detecting and responding to human presence. Proper training, risk assessment, and adherence to safety protocols are essential for successful and safe cobot welding implementation.
You May Also Like
The Future of Cobot Welding
Emerging trends and advancements in cobot welding technology include:
- Improved Sensor Technology and AI: Enhanced safety and adaptability
- Integration with Vision Systems: More complex tasks and quality control
- Greater Reach and Payload Capacities: Expanding the range of applications
- Simplified Programming Interfaces: Easier setup and operation
- Cloud-Based Platforms: Remote monitoring and control
- Increased Adoption Across Industries: Broader application of cobot welding
Conclusion
Cobot welding offers numerous benefits, including enhanced safety, increased flexibility, improved efficiency, and reduced labor costs.
By combining the strengths of humans and robots, cobot welding has the potential to transform welding processes across various industries.
Assessing specific needs and exploring cobot welding solutions can help businesses stay competitive in the ever-evolving landscape of industrial automation.
Frequently Asked Questions
How is cobot welding different from traditional robotic welding?
Cobot welding focuses on collaboration, safety, and ease of programming, allowing robots to work alongside humans seamlessly. Traditional robotic welding, on the other hand, typically involves robots operating in isolated, guarded cells to ensure safety. This isolation limits interaction and flexibility compared to cobot welding.
Is cobot welding safe?
Yes, cobot welding is designed to be safe, incorporating built-in safety measures such as force-torque sensors and vision systems. These features enable cobots to detect and respond to human presence, minimizing the risk of accidents. Proper implementation and strict adherence to safety protocols are essential to ensure a safe working environment.
What welding processes can be used with cobots?
Common welding processes for cobots include MIG and TIG welding, which are widely used in various industries. Cobots can be integrated with different welding systems to handle these processes efficiently. However, some specific processes and materials may have limitations that need to be assessed for each application.
How much does a cobot welding system cost?
The cost of a cobot welding system can vary widely depending on factors such as the cobot model, welding equipment, and integration complexity. While general price ranges can provide a rough estimate, obtaining specific quotes is recommended for accurate budgeting. These costs should be weighed against the long-term benefits of improved efficiency and safety.
Do I need specialized skills to program a cobot welder?
While cobots are designed to be user-friendly, some training is necessary for programming and operation. This training ensures that operators can effectively utilize the cobot's capabilities. Despite the need for training, the ease of use makes cobots accessible to a broader range of personnel, reducing the learning curve compared to traditional robots.
You May Also Like to Read:
Arc Welding VS Laser Welding | Which One Is Suitable for You
2 Beginner Farm Welding Projects with the Best Farm Welder