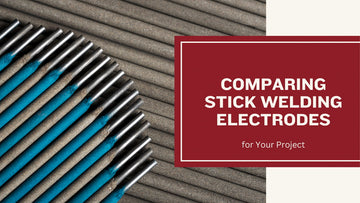
Stick welding is a welding process that is more difficult to master than MIG welding but less complex than TIG welding. One of the most challenging aspects of stick welding is electrode manipulation and application. However, with the right knowledge and practice, it can produce high-quality welds on a variety of materials, including carbon steel.
In this article, you will learn about the commonly used stick welding electrodes for carbon steel, their pros and cons, and which ones are more difficult to run. This knowledge will help you to choose the right electrode for your welding project and improve your stick welding skills.
Stick Welding Electrodes Comparison Chart
When it comes to stick welding electrodes, there are many types available with different characteristics. The American Welding Society (AWS) has a classification system that categorizes stick electrodes according to their intended use. Here is a comparison chart of some common stick welding electrodes:
Electrode |
Polarity |
Penetration |
Metal Deposition Rate |
Welding Thickness |
Overall Use Difficulty |
E6010 |
DCEP |
High |
High |
Medium to thick metal |
High |
E6011 |
AC or DCEP |
High |
High |
Medium to thick metal |
Medium to high* |
E6012 |
AC or DCEN |
Low/Medium |
Medium |
Thin to medium-thick metal |
Medium |
E6013 |
AC, DCEP, or DCEN |
Low/Medium |
Medium |
Thin to medium-thick metal |
Easy to medium* |
E7018 |
AC or DCEP |
Medium |
High |
Medium to thick metal |
Easy to medium* |
* Depending on the application
As you can see, each type of electrode has its own strengths and weaknesses. The classification system used by AWS makes it easy to select the right electrode for the job based on the welding procedure specification (WPS) and the requirements of the project. It is important to choose the right type of electrode to ensure a successful weld.
Stick Welding Rods Explained
E6010 - Digs Deep, Runs Hot, And Welds Fast
The E6010 stick welding electrode is known for its high penetration and fast welding capabilities. It is commonly used for pipeline and boiler welding due to its ability to dig deep into the metal, making it suitable for welding dirty, rusty metal. The E6010 electrode operates using DCEP and is ideal for welding low-carbon, non-alloyed steel. It releases hydrogen during the welding process, making it important to follow up with another electrode to remove excess hydrogen.
E6011 - Multi-Polarity Powerful Rod
Similar to the E6010, the E6011 electrode offers high penetration, making it suitable for various welding applications. It can be used with both DCEP and AC current, providing flexibility for welders, especially when only AC welding machines are available. While it works well with AC, the penetration may be slightly reduced compared to DCEP. The E6011 electrode is an excellent alternative for welders using machines that cannot run the E6010 effectively.
E6012 and E6013 - The Happy Medium And Beginner's Best Friend
The E6012 and E6013 electrodes are rutile electrodes, offering a balance between penetration and ease of use. The E6012, suitable for DCEN and AC polarity, is ideal for welding thin materials and light-duty repairs. On the other hand, the E6013, with its potassium content, provides better arc stability when used with AC. These electrodes are commonly used for hobby welding due to their stable arc, minimal smoke production, and easy slag removal.
E7018 - Low Hydrogen Electrode - Easy and Powerful
The E7018 electrode is highly versatile and commonly used for professional welding, including critical welds in structural steel. It can be used with both AC and DCEP polarity and offers a low-hydrogen environment in the weld area. The E7018 electrode is known for its smooth, stable arc and low spatter, making it suitable for various welding applications. It requires proper handling, including storage in a special oven and adherence to welding codes and standards for critical joints.
Check out the Best-Selling ArcCaptain Products:
Conclusion
In conclusion, stick welding rods E6010, E6013, and E7018 are excellent choices for welding different types of metal. E6010 is ideal for welding rusty, painted metal, while E6013 is suitable for welding thin sheet metal and most metal thicknesses. E7018 is an all-rounder for most hobbyist and professional welding jobs. However, it's crucial to keep it moisture-free to avoid porosity and cracking.
When welding with stick electrodes, it's essential to have the proper equipment such as a welding power source and a ground clamp. It's also crucial to practice and master basic stick welding skills before taking on critical applications such as pressure vessel and boiler fabrication.
The advantages of stick welding include its versatility, portability, and low cost. However, it's essential to consider service conditions, joint design, and electrode selection for a successful stick welding operation.
Frequently Asked Questions
What are the primary differences between 7018, 7014, and 6013 welding rods?
When comparing these three types of welding rods, there are a few key differences to consider. The 7018 electrode is known for its low hydrogen coating, which makes it an excellent choice for welding high-strength steel. On the other hand, the 7014 electrode is better suited for welding on thin or dirty surfaces, as it has a high iron powder content that allows it to penetrate rust and other contaminants. The 6013 electrode is a general-purpose electrode that can be used on a wide range of materials, but it does not offer the same level of penetration as the 7018 or 7014 electrodes.
How do I select the appropriate amperage for welding with a 6013 electrode?
When welding with a 6013 electrode, the appropriate amperage will depend on the thickness of the material you are welding. As a general rule of thumb, you should use 1 amp for every 0.001 inch of material thickness. For example, if you are welding a 1/8 inch thick piece of steel, you should use 125 amps.
What are the specific applications and uses for a 7018 welding electrode?
The 7018 welding electrode is commonly used for welding high-strength steel, as it produces a strong, clean weld. It is often used in applications such as structural welding, shipbuilding, and pipeline welding. It can also be used for welding low-alloy, high-tensile strength steel, as well as for welding joints that will be subjected to high stress.
In what scenarios should I use a 7014 welding rod over other types?
The 7014 welding rod is best suited for welding on thin or dirty surfaces, as it has a high iron powder content that allows it to penetrate rust and other contaminants. It is also a good choice for welding on materials that are not perfectly clean or flat. However, it is not recommended for use on high-strength steel or for welding joints that will be subjected to high stress.
What are the key specifications to consider when comparing different stick welding electrodes?
When comparing stick welding electrodes, there are several key specifications to consider. These include the type of coating, the diameter of the electrode, the amperage range, and the tensile strength. It is important to select an electrode that is appropriate for the material you will be welding and the specific application.
How does one determine the best electrode for welding various types of steel?
When selecting an electrode for welding various types of steel, it is important to consider the composition of the base metal and the specific application. Factors such as the thickness of the material, the welding position, and the required strength of the weld should also be taken into account.