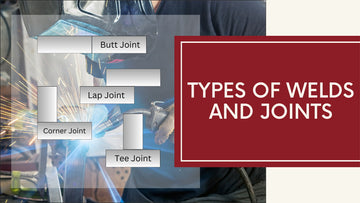
Welding is much more than simply joining metal; it's a skill in selecting the appropriate types of welds and joints for each task. Think of it as choosing the perfect tool for a specific job. Knowing which weld to use and when. Whether you're a beginner or a pro, understanding these different welds is crucial for making your metalwork strong and long-lasting. Let's dive into the different types and see how they're used in the world of welding.
What is Welding?
Welding is the process of joining two or more pieces of metal by heating the surfaces to their melting points and allowing them to cool and fuse together. The resulting bond is often as strong as the original metal. Welding is used in a wide range of applications, from construction and manufacturing to automotive and aerospace.
Understanding Welding Processes
There are many different welding processes, each with its own advantages and disadvantages. The most common types of welding include arc welding, gas welding, and resistance welding. Arc welding is the most widely used method, and it involves creating an electric arc between an electrode and the workpiece. This arc melts the metal and allows it to fuse together. Gas welding uses a flame to heat the metal, while resistance welding uses an electric current to heat the metal.
Types of Welds Joint and Their Applications
Understanding different types of welds is crucial for anyone in the welding field. Each weld type has unique characteristics and specific applications. Here, we detail some common types of welds, their features, and typical uses:
-
Butt Joint Weld
- Characteristics: This involves joining two pieces of metal end-to-end or edge-to-edge. The surfaces are often beveled to allow for deeper penetration of the weld.
- Applications: Commonly used in pipe welding and sheet metal work.
- Typical Use: Ideal for situations where a strong, flush joint is needed, like in pipelines or framework constructions.
-
Fillet Joint Weld
- Characteristics: A fillet weld joins two pieces of metal at a right angle to each other. It is triangular in shape and does not require the edges of the material to be shaped before welding.
- Applications: Widely used in metal fabrication for joining perpendicular pieces.
- Typical Use: Great for connections in metal frames, brackets, and various structural applications.
-
Lap Joint Weld
- Characteristics: In lap welding, two pieces of metal are overlapped and joined. The weld can be made on one or both sides of the overlapped region.
- Applications: Used in sheet metal work and to join overlapping components.
- Typical Use: Suitable for scenarios where metal pieces are of different thicknesses or where a butt weld is not feasible.
-
Corner Joint Weld
- Characteristics: This weld is used to join two metal parts at a corner. It's applied to the exterior or interior of the corner formed by the two pieces.
- Applications: Common in box, frame, and enclosure constructions.
- Typical Use: Ideal for creating boxes, frames, and similar structures where two pieces meet at a corner.
-
Edge Joint Weld
- Characteristics: Edge welds are used to join the edges of two or more metal parts. The weld is applied along the edge of each piece.
- Applications: Often seen in sheet metal fabrication.
- Typical Use: Useful when joining sheet metal pieces along their edges, especially in making tanks or panels.
-
T-Joint Weld
- Characteristics: This weld is used when two pieces of metal are perpendicular to each other, forming a 'T' shape.
- Applications: Common in structural frames and various metal assemblies.
- Typical Use: Applicable in constructing frameworks and structures where a perpendicular joint is required.
Each of these weld types serves a specific purpose and is chosen based on the requirements of the welding project. Understanding their individual characteristics helps in selecting the right type of weld to ensure strength, durability, and effectiveness of the joint.
Choosing the Right Type of Weld and Joint
Selecting the appropriate weld and joint type is a critical decision in any welding project. This choice can significantly impact the strength, durability, and appearance of the final product. Here are key considerations to guide you in "selecting weld types" and "joint selection in welding":
-
Material Type:
- Different materials require different welding approaches. For example, stainless steel often works best with TIG welding, while aluminum can be welded using MIG or TIG methods. The material thickness also plays a role; thinner materials might need careful TIG welding, while thicker materials could be more suited to MIG or stick welding.
-
Joint Configuration:
- The design of the joint determines the type of weld required. Butt joints are ideal for flat surfaces, whereas T-joints are necessary for perpendicular connections. Lap joints are useful for overlapping materials, and corner joints are used for box or frame constructions.
-
Load Conditions:
- Consider the mechanical stress and load the welded joint will endure. Structural projects, bearing heavy loads, need strong welds like butt or T-joints. Fillet welds in T-joints or lap joints can provide sufficient strength for less demanding applications.
-
Aesthetics:
- In projects where appearance is important, such as in furniture or decorative items, the neatness and precision of the weld are crucial. TIG welding is often preferred for its cleaner and more controllable welds.
-
Accessibility and Position:
- The location and accessibility of the joint affect the choice. Some welds and joints are easier to execute in tight or hard-to-reach spaces.
-
Welder’s Skill and Equipment:
- The complexity of the weld and the skill level of the welder should be considered. Beginners might find some types of welds and joints easier to handle than others. The available welding equipment also influences the choice of weld and joint type.
In conclusion, the selection of the right type of weld and joint is based on a combination of factors including the material, the joint's design, the load it will bear, aesthetic considerations, and the welder's skill level. Understanding these factors will help in making informed decisions, ensuring that your welding project is successful and meets all necessary requirements.
Advanced Welding Techniques
In addition to the more common groove welds and fillet welds, there are a number of advanced welding techniques that can be used in fabrication and construction.
One such technique is surfacing welding, which is used to add material to a surface to increase its strength or restore its original dimensions. This technique can be used to repair worn or damaged parts, or to add a layer of corrosion-resistant material to a surface.
Another advanced welding technique is bevel groove welding, which is used to create a strong joint between two pieces of metal that are at an angle to each other. This technique requires careful preparation of the joint, including beveling the edges of the metal to create a V-shaped groove that can be filled with filler material.
Overall, the selection of welding techniques and materials is a critical part of the fabrication and construction process. By carefully considering the materials being used and the requirements of the final weld, you can ensure a strong and durable joint that will stand up to the demands of its intended use.
Applications and Examples of 5 Basic Types of Weld
Understanding where and how the 5 basic types of welds and joints are applied in the real world can help grasp their practical importance. Here are some common applications and examples:
-
- Pipelines: Butt welds are frequently used in pipeline construction for transporting water, oil, and gas. They provide a smooth joint that doesn’t obstruct the flow.
- Shipbuilding: In shipbuilding, butt welds are used to join flat plates that form the ship's hull, ensuring a strong and watertight structure..
-
Lap Welds:
- Sheet Metal Work: In sheet metal fabrication, lap welds are used for joining overlapping sheets, such as in the construction of ducts or containers.
- Automotive Bodywork: Car body panels are often joined using lap welds for repair or modification work.
-
Corner Joints:
- Furniture Making: In metal furniture making, corner joints are used to create frames for tables, chairs, or shelves.
- Metal Boxes and Enclosures: These joints are essential in fabricating metal boxes, cabinets, or electrical enclosures, providing a neat corner connection.
-
Edge Joints:
- Panel Fabrication: Edge joints are used in fabricating larger panels from smaller sheets, as in metal roofing or siding.
- Decorative Metalwork: For creating large decorative pieces, edge joints offer a seamless way to join metal sheets along their edges.
-
T-Joints:
- Structural Frameworks: T-joints are vital in constructing metal frameworks for buildings, bridges, and industrial structures, offering a strong connection at perpendicular intersections.
- Automotive Chassis: The chassis of vehicles often utilizes T-joints for assembling various structural components.
Each type of weld and joint has its specific use, influenced by factors like the required strength, aesthetics, and accessibility. Understanding these applications can give a clearer perspective on how welding impacts everyday structures and objects, underscoring the importance of selecting the right type of weld and joint for each project.
Welding Challenges and Best Practices
Achieving quality results in welding involves adhering to certain best practices, regardless of the type of weld or joint configuration. These practices ensure not only the strength and durability of the weld but also the safety of the welder.
Preventing Weld Defects
Weld defects can significantly affect the strength and quality of your welds. Here are some common welding defects and how to prevent them:
-
Porosity: This occurs when gas becomes trapped in the weld. To prevent it, make sure to clean your workpiece thoroughly and use the correct shielding gas.
-
Cracking: This can happen when the weld cools too quickly or when there is too much stress on the joint. To prevent it, use preheat and post-weld heat treatment, and make sure to properly align and clamp your workpiece.
-
Lamellar tearing: This is a type of cracking that occurs in rolled steel plates. To prevent it, use proper joint design and welding techniques, and avoid welding in areas with high residual stress.
Addressing Welding Joint Failures
Welding joint failures can occur due to a variety of reasons, including inadequate reinforcement, poor joint design, and insufficient mechanical strength. Here are some solutions to common joint failures:
-
Insufficient reinforcement: This can happen when the weld bead is too small or when there is not enough penetration. To address it, increase the size of the weld bead, use a larger electrode, or adjust your welding parameters.
-
Poor joint design: This can lead to stress concentration and joint failure. To address it, use proper joint design and make sure to properly prepare and fit your workpiece.
-
Insufficient mechanical strength: This can occur when the weld is not strong enough to handle the load or resistance placed on it. To address it, use the correct welding technique and parameters, and make sure to properly test and inspect your welds.
By following these tips and techniques, you can prevent common welding challenges and ensure the strength and quality of your welds.
Conclusion
In summary, understanding different types of welds and joints is crucial in the welding process. Each type has its own set of applications and requirements that dictate the overall quality of a welding project. By following best practices, from preparation to post-weld inspection, welders can ensure strong, effective, and safe welds.
Whether it's a simple repair or a complex fabrication, the right welding technique, paired with safety and precision, can lead to successful project outcomes. Recognizing the importance and applications of various types of welds and joints not only enhances a welder’s skill set but also contributes significantly to the overall success and integrity of welding projects.
Frequently Asked Questions
What are the 5 types of weld joints?
The five basic types of weld joints are:
- Butt Joint: Joining two pieces of metal end-to-end or edge-to-edge.
- Corner Joint: Joining two pieces of metal at a corner, either internally or externally.
- Lap Joint: Overlapping two pieces and joining them at the edges.
- T-Joint: Joining two pieces of metal at a right angle, forming a 'T' shape.
- Edge Joint: Joining the edges of two or more pieces lying in the same plane.
What are the 4 types of welding?
The four most common types of welding are:
- MIG Welding (Metal Inert Gas Welding): Uses a wire feeding gun that feeds wire at an adjustable speed and sprays an argon-based shielding gas over the weld puddle to protect it from contamination.
- TIG Welding (Tungsten Inert Gas Welding): Uses a non-consumable tungsten electrode to produce the weld and is known for its precision.
- Stick Welding (Shielded Metal Arc Welding): Uses an electrode that has flux around it to protect the weld puddle. It's versatile and can be used in various environments.
- Flux-Cored Arc Welding: Similar to MIG welding, but it uses a special tubular wire filled with flux.
How many types of standard weld joints are there?
There are five standard types of weld joints: butt, corner, lap, T-joint, and edge joint. These joints are fundamental in various welding applications and are chosen based on the design, structural requirements, and material of the pieces being welded.
What are the 3 types of weld joints that require a fillet weld?
Three types of weld joints that commonly require a fillet weld are:
- T-Joint: Where two pieces are perpendicular to each other.
- Lap Joint: Where two pieces overlap and the weld is made at the edges of the top piece.
- Corner Joint: Typically in sheet metal work, where the edges of two pieces meet at a corner.