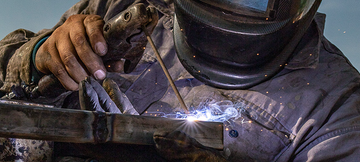
Summary of Welding Types
Welding is the process of joining two metal pieces by heating, pressure or both of them with or without use of filler metal. There are number of welding processes, each has its own pros and cons, hence selection of suitable welding process for a particular task is very important. A list of important arc welding processes is given below
- Shield Metal Arc Welding (SMAW)
- Gas Metal Arc Welding (GMAW)
- Gas Tungsten Arc Welding (GTAW)
- Submerged Arc Welding (SAW)
- Flux Cored Arc Welding (FCAW)
Next we will introduce each welding type in a few short sentences.Let's drive in.
1.Gas Metal Arc Welding (GMAW)
GMAW is an arc welding process that utilizes the arc between the filler metal electrode and the base metal, in the presence of externally supplied shielding gas to produce weld. This process can be further divided into following two types
- Metal Inert Gas (MIG)
- Metal Active Gas (MAG)
2. Gas Tungsten Arc Welding (GTAW)
GTAW is an arc welding process that utilizes the arc between the tungsten electrode (non-consumable) and the base metal, in the presence of externally supplied shielding gas to produce the weld. This process can be further divide into following two types
- Tungsten Inert Gas (TIG)
- Tungsten Active Gas (TAG)
We will focus on mig welding and tig welding types, they are currently the most widely used, most common and most practical welding types. Whether it is home welding repairs, diy projects, or shipbuilding, we can see their use scenarios.
3.MIG Welding

Metal inert gas welding process is in use since 1948 and is most widely used welding process in the industry. This process employs the automatic wire feeder as consumable electrode that is shielded by the externally supplied inert gas. A typical arrangement for MIG welding is given below
3.1 Power Source
MIG power source is DC power source which is essentially a constant voltage power source, whereas current is determined by wire feed speed.
3.2 Torch
MIG welding torch serves as a mean to deliver the welding filler wire that acts as electrode, and the shielding gas to the point where weld is being produced. Choice of the torch depends upon the thickness of the material and amount of current required to produce weld. Torch can be water cooled or air cooled, water cooled torches can offer 100% duty cycle while they can withstand current ranging from 250A to 600A.
3.3 Gases Used
Gas that is commonly used in this process are Argon (Ar), Carbon dioxide (CO2), Helium (He) or mixture of these. Choice of the gas depends upon the metal that is being welding, if they are not compatible a weak/ no weld will produce.
3.4 Wire/ Electrode
choice of wire/ electrode for the MIG welding depends upon the type of material to be welded. other factors include position and type of transfer during welding. typical MIG welding electrode is solid wire heaving thickness ranging from 0.02 to 0.45. some industrial applications may require thicker electrode. manufacturer of these electrodes use a standard code for identification purposes that usually starts with ER.
3.5 Process Advantages
- Consumable electrode welding process that is mostly used in industry to weld various metals including Mild steel, Stainless steel, Aluminum etc.
- Process is easy to learn
- Welding can be done in all positions, which is not possible in case of Submerged Arc Welding process
- Deposition rates are higher as compared to Shield Metal Arc Welding
- Welding speed are higher
- Long welds can be deposited without the need of stop and start over
- Minimal post weld cleaning is required
- Process can be easily automated
3.6 Process Limitations
- Overcomes the rustication of limited electrode length
- Welding equipment is more complex
- Difficult to weld in hard to reach areas due to the size of welding torch
- Welding arc needs to be protected with shielding gas, which makes it difficult to use this process in open air
4.TIG Welding

Tungsten inert gas welding process produces fine quality welds, in this process filler wire is externally fed to the arc that is created between the metal to be welded and the tungsten tip electrode (non consumable) of the welding torch. A typical arrangement for TIG welding is given below
4.1 TIG Power Source
TIG welding source can be either AC or DC however its characteristic are of constant current power source. For the welding of materials that develop rigid layer of oxide AC power source must be used, however care must be exercised to clean the surface prior to use the DC power source.
4.2 Torch
TIG welding torch utilizes a non-consumable electrode to produce arc while also serves as a mean to deliver the shielding gas to the point where weld is being produced. choice of the torch deepens upon the amount of current that is required to produce weld or the thickness of the material. Torch can be water cooled or air cooled usually for the current range up to 200A air cooled torches are used while for the current ranging from 200A to 500A water cooled torches are used.
4.3 Gases Used
Shielding gases are used to protect the weld form environmental contaminations, during TIG welding process inert gases like Argon (Ar) and Helium (He) are used and the Choice of particular gas depends upon the metal that is being weld.
4.4 Wire/ Electrode
TIG welding process utilizes the externally fed wire during the process and the choice of wire depends upon the various factors including composition of the material that is required to be welded. size of TIG welding wire for typical applications range from .062 to 0.15
4.5 Process Advantages
- It produces high quality welds
- Spatter free welds are produced, which is not the case for most welding processes
- Depending upon the material type and thickness, welds can be produced with or without the use of filler wire
- It allows excellent control of welding variables
- It can be used to weld virtually all metals, including dissimilar metal
- Post cleaning of weld is not required
4.6 Process Limitations
- Deposition rate is lower as compared to consumable electrode welding process
- More steady hand is requiring to produce good quality weld
- It is less economical for welding of thick metal
- Welding arc needs to be protected with shielding gas, which makes it difficult to use this process in open air
About the author
Muhammad Zeshan
Electrical Engineer with specialization in Electronics from University of Engineering and Technology, Pakistan and registered with Pakistan Engineering Council. Since 2012, Working as Maintenance and Support Engineer in reputed organization where welding/ fabrication is primary means of production, this lead my interest in welding and acquiring the welding inspector course from Pakistan Welding Institute. Since then I am writing reports and articles about welding.