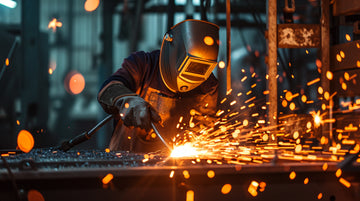
If you're interested in metalworking, you may have heard of a plasma cutter. It's a powerful tool that can cut through metal with remarkable precision.
But how does a plasma cutter work? In short, it uses a high-temperature, high-velocity stream of ionized gas, or plasma, to melt and cut through metal.
To understand how a plasma cutter works, it's helpful to understand the basics of plasma cutting. Plasma cutting is a process that involves creating an electrical channel of superheated, electrically ionized gas (plasma) from the plasma cutter itself, through the workpiece to be cut, and back to the plasma cutter through a grounding clamp. This creates a completed electric circuit that allows the plasma to cut through the metal.
The plasma cutter itself consists of a power supply, a plasma torch, and a ground clamp. The power supply generates a high-voltage, high-frequency electrical current that is fed to the plasma torch. The torch then ionizes the gas passing through it, creating the plasma that is used to cut through the metal. The ground clamp completes the electrical circuit, allowing the plasma to flow through the metal and cut it.
Fundamentals of Plasma Cutting
Understanding Plasma
Plasma is the fourth state of matter, which is created by ionizing a gas. When a gas is heated to a high temperature, the energy causes the atoms to become ionized, resulting in the formation of a plasma. Plasma is an incredibly hot and highly reactive gas that is capable of cutting through a variety of materials, including metals.
Components of a Plasma Cutter
A plasma cutter is a device used to cut through metal using a plasma torch. The components of a plasma cutter include a power supply, a pilot arc, a plasma torch, a nozzle, an electrode, a swirl ring, a shielding gas, and consumables.
The Plasma Cutting Process
The plasma cutting process begins with the power supply, which creates an electric circuit that sends an electric current through the pilot arc. The pilot arc ionizes the gas flowing through the torch, creating a plasma arc. The plasma arc then flows through the nozzle, which focuses the plasma and increases its velocity. The plasma arc then comes into contact with the workpiece, which causes the metal to heat up and melt. The high-velocity plasma then blows the molten material away from the cut, creating a clean, precise cut.
During the cutting process, the plasma arc generates a significant amount of heat, which can cause the metal to melt and create a kerf. The kerf is the width of the cut, which is determined by the size of the nozzle and the amount of airflow through the torch.
Overall, plasma cutting is an effective and efficient method for cutting through a variety of materials. With the right equipment and technique, you can create precise cuts with minimal heat distortion and minimal clean-up.
Types of Plasma Cutters
When it comes to plasma cutters, there are primarily two types of systems available: handheld plasma cutters and CNC plasma cutters. Each type has its own set of advantages and disadvantages, and the choice of which one to use will depend on your specific needs and requirements.
Handheld Plasma Cutters
Handheld plasma cutters are a popular choice for those who need a portable and versatile plasma cutting system. These systems are designed to be lightweight and easy to carry, making them ideal for use in remote locations or for on-site work.
One of the main advantages of handheld plasma cutters is their portability. You can easily move them from one location to another without the need for heavy lifting equipment. Additionally, handheld plasma cutters are highly versatile, allowing you to cut a wide range of materials with ease.
However, handheld plasma cutters may not be the best choice for precision cutting. If you require high precision cutting, you may need to consider a CNC plasma cutter.
CNC Plasma Cutters
CNC plasma cutters are designed for precision cutting and automation. These systems are typically used in industrial settings where high precision cutting is required. CNC plasma cutters are often integrated into a larger CNC machine or robotic arm, allowing for automated cutting.
One of the main advantages of CNC plasma cutters is their precision. These systems are capable of cutting complex shapes with high accuracy, making them ideal for use in manufacturing and fabrication.
However, CNC plasma cutters are typically more expensive than handheld plasma cutters, and they require a higher level of technological expertise to operate. Additionally, CNC plasma cutters are not as portable as handheld plasma cutters, and they may not be as versatile.
In conclusion, when choosing a plasma cutter, you need to consider your specific needs and requirements. If you require portability and versatility, a handheld plasma system may be the best choice. If you require precision and automation, a CNC plasma cutter may be the right choice.
Materials and Applications
Compatible Materials
Plasma cutters are versatile tools that can cut through a variety of materials, including steel, aluminum, copper, stainless steel, and brass. The key to cutting through these materials is that they must be conductive. Plasma cutters work by creating an electrically conductive channel of plasma through the material being cut, which is then blown away by a high-velocity jet of gas.
When it comes to steel, plasma cutters are particularly effective. They can cut through steel up to 6 inches thick, making them an ideal tool for construction and metal fabrication. Aluminum is another popular material for plasma cutting, as it is lightweight and easy to work with.
Industrial and Creative Use
Plasma cutters are used in a variety of industries, including construction, automotive, and metal fabrication. They are also popular among hobbyists and professionals who enjoy working with metal and creating custom pieces.
In the construction industry, plasma cutters are used to cut through metal beams and other materials. They are also used to create custom metal pieces for buildings and other structures. In the automotive industry, plasma cutters are used to cut through sheet metal and other materials to create custom parts and bodywork.
Metal fabrication is another industry where plasma cutters are commonly used. They are used to cut and shape metal into a variety of different forms, from simple brackets to complex sculptures. Plasma cutters are also popular among hobbyists who enjoy creating custom metal pieces and artwork.
Overall, plasma cutters are versatile tools that can be used to cut through a variety of materials. Whether you are a professional metalworker or a hobbyist, a plasma cutter can help you create custom pieces with precision and ease.
Operating a Plasma Cutter
If you want to use a plasma cutter, there are certain things you need to know. This section will cover the basics of operating a plasma cutter. We'll discuss setting up the equipment, cutting techniques and precision, and safety measures.
Setting Up the Equipment
Before you can use a plasma cutter, you need to set up the equipment. This includes connecting the plasma cutter to the appropriate air compressor and power source. Make sure you plug in the ground lead or earth lead into your plasma cutter. You also need to ensure that the cutting tip is properly installed and the cutting amperage is set correctly.
Cutting Techniques and Precision
Once you have set up the equipment, you can start using the plasma cutter. The precision plasma torch narrows down the stream of plasma, which helps create precise cuts in metal. You can adjust the cutting speed and precision by changing the cutting tip and adjusting the cutting amperage.
Safety Measures
When using a plasma cutter, it is important to take safety measures. Make sure you wear gloves, boots, goggles, and a shield cap to protect yourself from the heat and light produced by the plasma cutter. Keep the work area clean and free of clutter to avoid tripping hazards. Always follow the manufacturer's instructions and safety guidelines.
In conclusion, operating a plasma cutter requires setting up the equipment, using cutting techniques and precision, and taking safety measures. With the right equipment and safety measures in place, you can use a plasma cutter to create precise cuts in metal.
Gas and Airflow in Plasma Cutting
Plasma cutting is a process that uses a high-temperature, high-velocity jet of ionized gas to cut through metal. The gas used in plasma cutting is typically compressed air, nitrogen, argon, or oxygen. The gas is forced through a small nozzle at high pressure, which creates a plasma arc that melts and vaporizes the metal.
Types of Gases Used
The gas used in plasma cutting can affect the quality of the cut and the speed of the process. Compressed air is the most common gas used in plasma cutting because it is readily available and affordable. Nitrogen is also commonly used because it produces a high-quality cut and is less likely to react with the metal being cut. Argon is used for cutting non-ferrous metals such as aluminum, copper, and brass. Oxygen is used for cutting thicker metals, as it produces a faster cut speed and can be used at higher amperages.
Airflow Management
Airflow management is an important aspect of plasma cutting. The flow of gas through the nozzle affects the shape and quality of the plasma arc. The nozzle has a series of vent holes that control the flow of gas and create a vortex that helps to stabilize the arc. The pressure and flow rate of the gas must be carefully controlled to ensure a clean and accurate cut.
In addition to the gas used for cutting, a shielding gas is also used to protect the cut from oxidation and regulate the unpredictable nature of plasma. The cutter nozzle has a second set of channels that release a constant flow of shielding gas around the cutting area. The pressure of this gas flow effectively controls the radius of the plasma beam.
In summary, the gas and airflow management are critical components of the plasma cutting process. The type of gas used and the flow rate must be carefully chosen to ensure a high-quality cut. The use of a shielding gas is also important to protect the cut and regulate the plasma beam.
Technical Specifications
Electrical Requirements
To operate a plasma cutter, you will need an electrical power source. The plasma power supply converts single or three-phase AC line voltage into a smooth, constant DC voltage ranging from 200 to 400VDC. This DC voltage is responsible for maintaining the plasma arc throughout the cut. It also regulates the current output required based on the material type and thickness being processed.
Performance Metrics
The cutting speed of a plasma cutter depends on various factors, such as the thickness and type of metal, the cutting amperage, and the arc starting console. The plasma arc can reach speeds of up to 20,000 feet per second, which makes it a very efficient cutting tool.
The cutting amperage is another important factor that determines the performance of a plasma cutter. The higher the cutting amperage, the thicker the material that can be cut. For instance, a plasma cutter with a cutting amperage of 40A can cut through 1/8 inch steel, while a 60A plasma cutter can cut through 1/4 inch steel.
Overall, the technical specifications of a plasma cutter are essential to consider when selecting the right tool for your cutting needs. Understanding the electrical requirements and performance metrics will help you make an informed decision and ensure that you get the most out of your plasma cutter.
Frequently Asked Questions
What is the working principle of a plasma cutting machine?
A plasma cutter uses an electrical arc and compressed gas to create plasma. This plasma is then used to cut through metal quickly and accurately. The electrical arc is created between the electrode and the workpiece, which ionizes the gas and creates plasma. The plasma is then directed through a nozzle and onto the workpiece, which melts the metal and allows for precise cutting.
Can a plasma cutter operate without gas, and if so, how?
No, a plasma cutter cannot operate without gas. The gas is necessary to create the plasma that is used to cut through metal. Typically, compressed air or nitrogen is used as the gas source for plasma cutting machines.
What type of gas is typically used in a plasma cutting process?
Compressed air or nitrogen is typically used as the gas source for plasma cutting machines. Compressed air is the most common gas used in plasma cutting because it is readily available and inexpensive. Nitrogen is also used for plasma cutting, but it is more expensive than compressed air.
Are air compressors necessary for the operation of a plasma cutter?
Yes, air compressors are necessary for the operation of a plasma cutter. The compressed air is used to create the plasma that is used to cut through metal. The air compressor must be able to deliver a consistent flow of compressed air to ensure that the plasma cutter operates properly.
What are the common limitations or drawbacks of using plasma cutting technology?
One of the main limitations of plasma cutting technology is that it is not suitable for cutting thicker materials. Additionally, plasma cutting can produce a lot of noise and smoke, which can be a safety hazard if proper ventilation is not used. Finally, plasma cutting can be expensive, and the cost of the equipment and consumables can be prohibitive for some users.