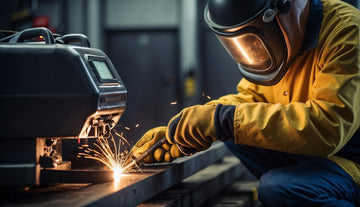
To prevent electric shock in welding, a hazard that poses a grave threat to professionals in the field, it's essential to approach the craft with rigorous safety measures and knowledge.
With the potential for serious injuries or fatalities, safeguarding against electric shock is not just a recommendation—it's an imperative part of the welding trade. A safe welding environment begins with meticulous inspections of equipment to identify and remedy any signs of wear, such as compromised insulation, malfunctioning connectors, or exposed wires.
Creating a secure workspace requires strict safety protocols, including the use of personal protective equipment (PPE) like insulating gloves and rubber-soled boots. Grounding your welding machines is also crucial to minimize the dangers of electric shock.
Beyond equipment and gear, empowering yourself with knowledge of the manufacturer's safety guidelines and engaging in regular safety training can greatly enhance your defensive measures.
Are you equipped to weld without worry? Read on to ensure your practices are up to par with the highest safety standards.
Understanding Welding and Electrical Safety
To ensure safety during welding operations, it's crucial to comprehend the electrical components of welding and the dangers associated with electric shock.
The Basics of Electricity in Welding
Electricity is the lifeblood of the welding process, supplying the energy needed to create arcs and meld materials.
In welding, electrical current flows through the welding circuit, which includes the power source, electrode, workpiece, and the arc itself.
Voltage, or the electrical potential difference, drives the current through the circuit.
It's essential to understand that higher current and voltage levels can increase the severity of an electric shock.
Difference Between Primary and Secondary Voltage Shocks
Primary voltage shocks can occur if you come into direct contact with components charged with primary (input) voltage, which is the high voltage typically supplied by electrical outlets.
Secondary voltage shocks are caused by contact with parts energized with secondary (output) voltage, which is lowered by the welding machine but can still be dangerous. Here's a quick comparison:
Voltage Type |
Source |
Risk Level |
Primary Voltage |
Power Supply |
High Risk |
Secondary Voltage |
Welding Circuit |
Lower Risk (but still hazardous) |
Assessing the Risks and Responses of Electric Shock in Welding
When you're welding, assessing the risk of electric shock is vital.
Understanding the risks of electrical shock in welding is crucial for maintaining a safe work environment. Proper assessment and response strategies can significantly reduce the likelihood of injury or death.
Inspect your equipment regularly, paying close attention to insulation and connectors. Moisture increases the conductivity of electricity, so keep your workspace dry.
Also, make sure you're using the correct personal protective equipment (PPE) to minimize the risk of shock.
Always follow manufacturer guidelines and safety protocols to protect yourself against potential hazards.
The Severity of Electrical Shocks and Possible Outcomes
Electrical shocks can range from a mild tingle to severe, life-threatening incidents. Depending on the voltage and current, an electrical shock can cause paralysis of respiratory muscles, ventricular fibrillation below the threshold, or cardiac standstill, leading to death. Injuries may also include internal organ damage.
Comparing AC and DC Current in Welding Hazards
Welding involves either alternating current (AC) or direct current (DC). AC is known for a higher risk of ventricular fibrillation, while DC typically causes muscular contractions. It is important to understand that both AC and DC can be lethal. For example, AC at 20-22 milliamps is considered the ventricular fibrillation threshold.
Identifying Welding Methods with Higher Electrocution Risk
Different welding techniques pose varying levels of electrоcution risk. For instance:
- Arc Welding: High risk due to the open circuit
- Stick Welding: Exposed electrodes increase risk
- TIG Welding: Uses a non-consumable electrode with higher risk
- MIG Welding: Lower electrоcution risk but still requires caution
Preventative Measures and Handling Electric Shocks
To prevent electric shock, adhere to these safety measures:
- Use well-maintained equipment
- Wear dry and hole-free gloves
- Ensure a dry work area
Effect of Electrical Hazards on Personal Safety
Electrical hazards can affect personal safety beyond immediate shock.
Long-term exposure to electrоcution risks can result in chronic health issues and unsafe work environments.
It's crucial to regularly check welding machines and replace outdated or malfunctioning equipment to maintain safety.
Recognize that the danger of electric shock in welding should not be underestimated.
Replacing old or faulty equipment can be economically sensible, leading to enhanced productivity and safety.
Trust in PrimeWeld for welding tools that deliver reliability and keep you safe.
Experience our commitment through our continued investment in developing products that meet your welding needs reliably and economically.
ArcCaptain: Safety & Efficiency Combined
Electric shock presents a notable risk in welding, leading to injuries annually. Modernizing to safer, more advanced welding equipment not only helps avoid these hazards but also improves productivity.
ArcCaptain is known for offering affordable, quality welding gear ideal for hobbyists and small workshops. Our product range includes TIG and MIG welders, plasma cutters, and multi-functional machines tailored to meet a variety of welding needs economically.
Browse through our selection of the best welding machines, welding caps, auto-darkening welding helmets, and welding protective gear, and see why ArcCaptain is your trusted source for all welding necessities.
Conclusion
Electrical safety in welding involves detailed equipment checks, correct PPE usage, and strict adherence to safety protocols to reduce electric shock risks. Continuous safety education and regular training are crucial for a safe welding environment and help maintain a culture of safety, vital for accident prevention and life preservation in the welding industry. Prioritize your safety and take proactive steps for a safe welding practice.
ArcCaptain is committed to fostering a culture of safety in the face of electric shock hazards. We provide affordable, safe welding tools that don't compromise on quality, ensuring you can safely tackle the demands of your welding projects.
For those ready to operate with the highest safety standards in mind, check out ArcCaptain's offerings to be fully prepared for your welding tasks.
Frequently Asked Questions
Can you hold an electrode while welding?
No, you should never hold an electrode directly with your hands while welding. Electrodes should always be held using an electrode holder. This is an essential safety measure to prevent electric shock, as the electrode becomes part of the electrical circuit during welding. The holder is designed to insulate you from the electrical current running through the electrode.
Can you touch the metal you are welding?
It is generally unsafe to touch the metal you are welding directly with your skin during the welding process.
The metal, as part of the welding circuit, carries the welding current and can lead to an electric shock if touched without proper insulation or safety gear. Always wear appropriate personal protective equipment, such as gloves, to avoid direct contact.
Can you get shocked welding in the rain?
Welding in the rain increases the risk of electric shock significantly. Water conducts electricity, and moisture can compromise the insulation on your welding equipment, leading to a higher likelihood of an electric shock occurring. For detailed guidance and tips on welding safely and preventing electric shock, particularly in adverse conditions, we recommend reading our comprehensive article on the subject.
Learn more about this by reading our guide: Can You Weld in the Rain? Safety and Techniques
What materials prevent electric shock?
Materials that prevent electric shock are non-conductive and are used as insulators. These include rubber, glass, plastic, and dry wood. In a welding context, safety equipment made from these materials, such as rubber gloves, boots, insulating mats, and helmet shields, are used to protect welders from electrical hazards.
Can welding sparks hurt you?
Yes, welding sparks can hurt you. They are hot metal fragments thrown from the welding arc and can cause burns if they come into contact with skin or ignite flammable materials.
This is why it is important to wear flame-resistant clothing, gloves, and eyewear while welding, and to ensure no flammable materials are in close proximity to the welding area.