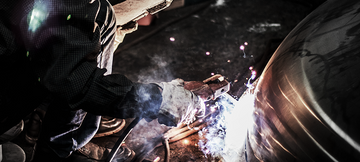
You may be looking for the suitable parameters to refer for mig 200, the simple wizard will help you with some mig 200 basic setup.
The suitable parameters for ARCCAPTAIN MIG 200 depend on several factors such as the type of material you will weld, the thickness of the material, the welding position, and the wire size being used.
Here are some general guidelines to help you get started with setting up suitable parameters for ARCCAPTAIN MIG 200:
-
Determine the type and thickness of the material you will weld. This information will help you choose the appropriate wire size and shielding gas.
-
Select the appropriate wire size and drive roller type based on the thickness of the material. For example, for welding thin sheet metal, you might use a 0.023 inch wire, while for thicker material, you might use a 0.035 inch wire.
-
Choose the appropriate shielding gas for the material being welded. For mild steel, you might use a mix of 75% Argon and 25% CO2. For stainless steel, you might use a mix of 98% Argon and 2% CO2.
-
Set the voltage and wire feed speed based on the wire size and material thickness. You can see the guide image to choose suitable WFS.
-
Test your settings on a scrap piece of material before welding on the actual workpiece.
-
Adjust the settings as necessary based on the welding position, joint type, and other variables.
It's important to note that the best parameters for ARCCAPTAIN MIG 200 may vary based on the specific application and welding conditions. Therefore, always follow the recommendations and adjust the settings based on your own experience and testing.
The following setting guide image can help you better set related parameters.
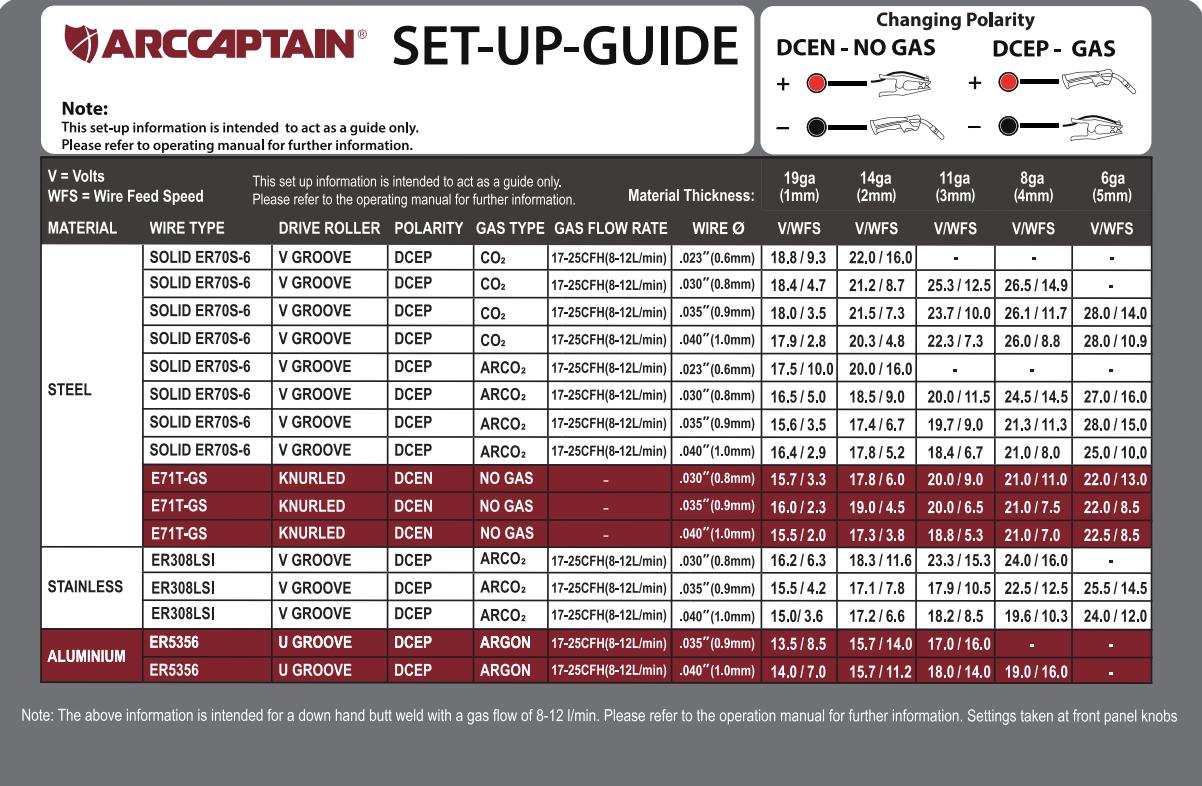