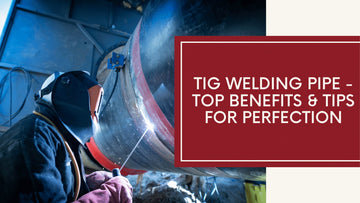
Exploring the world of TIG welding pipe reveals numerous benefits and essential tips for achieving perfection in your work. This article delves into the top advantages of TIG welding pipe, along with practical advice to help you refine your technique. Whether you're tackling intricate projects or aiming for high-quality finishes, our guide will assist you in mastering the art of TIG welding pipe.
Understanding TIG Welding Process
Tungsten Inert Gas (TIG) welding, also known as Gas Tungsten Arc Welding (GTAW), is a welding process that uses a non-consumable tungsten electrode to produce an arc that melts the base material and filler material. The process uses an inert gas, such as argon or helium, to shield the weld area from contamination.
TIG welding is a versatile process that can be used to weld a variety of metals, including stainless steel, aluminum, and copper. It is commonly used in applications where a high-quality weld is required, such as in the aerospace and automotive industries.
Components of TIG Welding
The components of a TIG welding system include a power source, a TIG torch, a tungsten electrode, a shielding gas, and filler material. The power source provides the electrical current that creates the arc, while the TIG torch holds the tungsten electrode and delivers the shielding gas.
The tungsten electrode is a non-consumable electrode that is used to create the arc. It is made of tungsten, which has a high melting point and is able to withstand the heat generated by the welding process.
The shielding gas is used to protect the weld area from contamination. Argon is the most commonly used shielding gas for TIG welding, but helium can also be used for certain applications.
Types of Tungsten Electrodes
There are several types of tungsten electrodes that can be used for TIG welding, including pure tungsten, thoriated tungsten, ceriated tungsten, and ArcCaptain lanthanated tungsten.
Pure tungsten electrodes are used for welding aluminum and magnesium alloys, while thoriated tungsten electrodes are used for welding steel and stainless steel. Ceriated tungsten electrodes are used for welding non-ferrous metals, such as copper and brass, and lanthanated tungsten electrodes are used for welding both ferrous and non-ferrous metals.
Understanding Pipe Welding Application
When it comes to pipe welding application, there are a few important factors to consider. The joint preparation and fit-up, as well as cleaning and material preparation, are crucial steps in ensuring a successful weld.
Joint Preparation and Fit-Up
The joint preparation and fit-up are critical to the success of the weld. The edges of the pipes must be prepared properly to ensure a good fit. The edges should be clean and free of any burrs or debris. Proper alignment of the pipes is also important to ensure that the weld is strong and consistent.
Cleaning and Material Preparation
Cleaning and material preparation are also important factors to consider when welding pipe. The surface of the pipe should be cleaned thoroughly to remove any contaminants, such as oil or grease, that could affect the quality of the weld. The material should also be prepared properly, taking into consideration the type of material being welded. For example, stainless steel requires a different approach than carbon steel or aluminum.
In conclusion, understanding pipe welding application is crucial to producing high-quality welds. Proper joint preparation and fit-up, as well as cleaning and material preparation, are essential steps to ensure a successful weld. By paying attention to these factors, welders can produce strong and consistent welds that will stand the test of time.
TIG Welding Techniques
TIG welding is a versatile welding process that can be used to weld various materials, including pipe. To achieve high-quality welds, it is important to use proper welding techniques. In this section, we will discuss some TIG welding techniques that can help improve your welding skills and produce better welds.
Welding Pipe Positions and Movements
When welding pipe, it is important to use the proper welding position and movement. The most common welding position for pipe welding is the 6G position, which is a combination of the 45-degree and horizontal positions. In this position, the pipe is fixed, and the welder must move around the pipe to complete the weld.
To achieve a high-quality weld, the welder should use a consistent speed and movement. Walking the cup technique is commonly used in pipe welding, where the cup is moved in a circular motion around the weld puddle. This technique helps to maintain consistent heat and penetration and produces a smooth weld bead.
Controlling Heat and Penetration
Controlling heat and penetration is crucial to achieving a high-quality weld. The welder should use proper amperage settings and control the heat input to prevent overheating and distortion of the pipe. The welder should also maintain proper arc length to ensure proper penetration into the base metal.
To control penetration, the welder should watch the weld puddle and adjust the filler rod accordingly. The filler rod should be added to the leading edge of the weld puddle, and the welder should move the puddle forward to control the penetration.
Filling and Capping Techniques
Filling and capping techniques are used to complete the weld and produce a smooth and strong weld bead. The welder should use proper filler rod or wire and ensure that it is compatible with the base metal.
To achieve a smooth weld bead, the welder should use proper techniques to fill the joint. The fill pass should be made in a single motion and should overlap the previous pass slightly. The capping pass should be made with a slightly higher amperage setting to ensure proper fusion and produce a smooth and uniform weld bead.
In conclusion, using proper TIG welding techniques is crucial to producing high-quality welds on pipe. By using the proper welding position and movement, controlling heat and penetration, and using proper filling and capping techniques, the welder can achieve strong and smooth welds.
Benefits of Welding Pipe with TIG
TIG welding is a popular welding method used for welding pipe due to its precision and clean welds. Here are some benefits of using TIG welding for pipe welding projects.
Working with Different Pipe Materials
TIG welding is a versatile method that can be used to weld different types of pipe materials. Whether it is stainless steel pipe, magnesium, or inconel, TIG welding can produce high-quality welds on these materials. This makes it an ideal welding method for pipe welding projects that require welding different materials.
TIG Welding Thin Wall and Heavy Wall Pipe
TIG welding is also suitable for welding thin wall and heavy wall pipe. The precision and control offered by TIG welding make it possible to weld thin wall pipe without causing damage to the pipe. At the same time, TIG welding can also handle heavy wall pipe with ease, producing clean welds that are free from defects.
TIG welding is also known for its excellent thermal conductivity, which means that it can weld materials without causing distortion or warping. This is particularly important when welding thin wall pipe, as distortion can cause leaks or other defects in the weld.
In summary, TIG welding is an excellent method for welding pipe due to its precision, versatility, and ability to handle different materials and wall thicknesses. Whether you are welding stainless steel pipe, thin wall pipe, or heavy wall pipe, TIG welding is a reliable method that can produce clean and defect-free welds.
Choosing the right TIG Welding Equipment and Settings
When it comes to TIG welding, choosing the right welder is crucial. A good TIG welder should have a high-frequency start, adjustable amperage control, and a foot pedal for amperage control. It's also important to consider the type of material being welded and the thickness of the material. For example, a welder with a higher amperage range may be necessary for thicker materials.
Check out Best Selling ArcCaptain TIG Foot Pedal.
Tig Welder Adjusting Amperage and Gas Flow
Once the right TIG welder has been selected, it's important to adjust the amperage and gas flow settings for the specific project. The amperage setting will depend on the thickness of the material being welded, as well as the type of tungsten and cup size being used. A general rule of thumb is to use 1 amp for every 0.001 inch of material thickness.
The gas flow rate is also important to consider, as it affects the quality of the weld. Typically, a flow rate of 15-20 cubic feet per hour (CFH) of argon or helium gas is recommended. It's important to use a regulator to ensure consistent gas flow throughout the welding process.
In addition to amperage and gas flow settings, the size of the tungsten and cup used in the torch can also affect the quality of the weld. A larger tungsten size may be necessary for thicker materials, while a smaller cup size can provide better access to tight spaces.
Overall, selecting the right TIG welder and adjusting the amperage and gas flow settings for the specific project are crucial for achieving high-quality TIG welds.
Tig Welding Safety and Best Practices
Tig welding is a process that requires a high level of safety measures to be followed to prevent injuries and accidents. Here are some safety measures that should be followed when tig welding:
- Always wear proper personal protective equipment (PPE) such as ArcCaptain welding gloves, helmet, and clothing.
- Keep the work area clean and free of any flammable materials.
- Make sure the welding machine is grounded properly.
- Use a welding curtain or shield to protect others from the welding arc.
- Ensure proper ventilation in the work area to prevent inhaling harmful fumes.
Tips for Efficient and Effective Welding
Tig welding requires precision and control, which can be achieved through proper practice and technique. Here are some tips for efficient and effective tig welding:
- Use a foot pedal or fingertip control to adjust the amperage while welding.
- Maintain a consistent travel speed and work angle to ensure proper penetration and fusion.
- Keep the tungsten electrode sharp and clean to prevent contamination and improve arc stability.
- Use torch-mounted amperage control to adjust the amperage while welding.
- Take breaks when needed to prevent fatigue and maintain focus.
Following these safety measures and tips will not only ensure a safe work environment but also improve the quality and efficiency of your tig welding.
Applications of TIG Welding Pipe
Tungsten Inert Gas (TIG) welding is a highly versatile welding process that is widely used in various industries for welding pipes. It is a clean and precise welding process that produces high-quality welds with minimal spatter and distortion. Here are some of the applications of TIG welding pipe:
Industry-Specific Applications
TIG welding is commonly used in the power generation industry for welding pipes in power plants. It is also widely used in the nuclear industry for welding pipes in nuclear power plants. In addition, TIG welding is used in the food industry for welding pipes in food processing plants due to its clean and precise welding process.
TIG Welding for Repair and Maintenance
TIG welding is also used for repair and maintenance of pipes in various industries. It is commonly used for repairing pipes that have been damaged due to oxidation or corrosion. TIG welding can be used to repair small cracks or holes in pipes, which can help extend the lifespan of the pipes.
In conclusion, TIG welding is a highly versatile welding process that is widely used in various industries for welding pipes. It is a clean and precise welding process that produces high-quality welds with minimal spatter and distortion. TIG welding is commonly used in the power generation, nuclear, and food industries, and it is also used for repair and maintenance of pipes that have been damaged due to oxidation or corrosion.
Frequently Asked Questions
What is the difference between TIG and MIG welding when it comes to pipe fabrication?
TIG welding is a more precise and controlled process that produces high-quality welds suitable for critical applications. MIG welding, on the other hand, is faster and more suitable for thicker materials where appearance is not a primary concern.
How do you select the appropriate amperage for TIG welding an exhaust pipe?
The appropriate amperage for TIG welding an exhaust pipe depends on the thickness of the pipe, the type of material, and the desired welding speed. Generally, a lower amperage is suitable for thinner materials, while thicker materials require higher amperage.
What factors determine the best TIG cup size for walking the cup on pipe welds?
The best TIG cup size for walking the cup on pipe welds depends on the diameter of the pipe, the thickness of the material, and the welding position. A larger cup size is suitable for larger diameter pipes, while a smaller cup size is suitable for smaller diameter pipes.
Can you describe the process for performing a root pass with TIG on pipes?
To perform a root pass with TIG on pipes, the welder must first clean the joint and prepare the edges for welding. Then, the welder must set the appropriate amperage and use a filler rod to melt the base metal and form a root pass. The welder must ensure that the root pass is free from defects and has good penetration.
What are the challenges associated with TIG welding aluminum pipes compared to other materials?
TIG welding aluminum pipes can be challenging due to the material's high thermal conductivity and low melting point. The welder must use a lower amperage and faster welding speed to prevent the material from overheating and warping.
Which TIG welding torch is most suitable for pipe welding applications?
A TIG welding torch with a flexible head and a small diameter is most suitable for pipe welding applications. The flexible head allows the welder to access tight spaces and awkward angles, while the small diameter allows for precise control and maneuverability.