
Welding stringers are a key technique for creating clean, strong welds. A stringer bead is applied in a straight line without excessive side-to-side movement, ensuring uniform penetration and minimal distortion.
This method is commonly used in SMAW, GMAW, and FCAW processes.
Stringer beads help reduce heat input, porosity, and warping, making them ideal for structural welding, pipelines, and fabrication.
They offer better control and precision than weave beads, especially on thinner metals.
So, what are welding stringers, and when to use them? Keep reading to explore the benefits, best practices, and situations where stringer beads are the best choice for your welding projects.
What Are Welding Stringers?
Welding stringers are straight, narrow weld beads. Unlike weave beads, stringers are created without any side-to-side motion. This means the weld is laid in one single direction across the joint.
Stringers are important for achieving precise, clean welds.
They help create a smooth and strong connection between metal pieces. You often use stringer beads when you want to maintain the weld's shape and sharpness.
-
High-Strength Welds: Stringers are great for high-strength welds. Since they're straight, they allow for deep penetration, ensuring a solid connection.
-
Minimal Heat Distortion: The focused heat of stringers means less metal is exposed to high temperatures. This reduces the risk of distorting the metal due to excessive heat.
-
Better Control: You have more control over the welding process with stringers. This is important when working on projects that need precision.
Stringers are often chosen for projects where maintaining the original form and structure of the metal is crucial. They ensure the weld is both aesthetically pleasing and functionally strong, making them a popular choice in various metallic constructions.
When and Why to Use Welding Stringers
Welding stringers are a precise and controlled technique used in various applications. They are ideal for creating strong, clean welds while minimizing heat-related issues. Here’s when and why you should use them:
- For Thin Materials – Stringer beads help control heat input, preventing warping or burn-through. This is essential for materials that can’t handle high temperatures.
- For Deep Penetration – A straight-line motion allows for deeper weld penetration while keeping the width narrow, ensuring a strong joint.
- For Structural Strength – High-strength projects benefit from stringers because they improve fusion and penetration, maintaining structural integrity.
- For Efficiency and Cost-Effectiveness – Stringers are applied quickly, reducing welding time and material use, making them ideal for manufacturing and production work.
By using stringer beads, you get a strong, reliable weld with precision, making them an excellent choice for various welding applications.
📌 Also Read: How to Stick Weld Different Thickness Metals
Best Welding Processes for Stringer Beads
Stick Welding (SMAW) Stringer Beads
Use stick welding for tasks like structural and pipeline welding. It's ideal for heavy-duty applications. Keep the electrode at a 10-15° angle in the travel direction.
Ensure a steady travel speed to maintain a smooth bead. To avoid undercutting, manage the heat buildup carefully. This technique is reliable for strong, clean welds.
Related Product:
Arccaptain ARC205 Pro iControl Dual Voltage SYN Stick Welder
The ARC205 Pro Dual Voltage Stick Welder is ideal for stringer beads, offering Smart Synergy technology for precise SMAW welding. With dual voltage (110V/220V), hot start, and arc force, it ensures deep penetration, minimal spatter, and strong welds for structural and fabrication projects. |
MIG Welding (GMAW) Stringer Beads
MIG welding works well for sheet metal and automotive repairs. For the best results, use a short-circuit or spray transfer mode.
You should maintain a consistent wire speed to ensure even welds. Avoid weaving too much; keep a straight path to achieve the best penetration. This method suits general fabrication needs.
Related Product:
Arccaptain MIG205 Pro 6 IN 1 Multi Process MIG Welder
The ARC205 Pro Multi-Process MIG Welder is perfect for welding stringer beads, delivering smooth, controlled welds ideal for sheet metal and automotive repairs. With Synergic MIG, Lift TIG, and Stick welding capabilities, it ensures deep penetration and clean welds, making it a top choice for precision work in fabrication and auto body repairs. |
TIG Welding (GTAW) Stringer Beads
TIG welding is preferred for stainless steel and precision work. A sharp tungsten tip can help with better arc control.
Maintain a steady hand and slow travel speed for clean welds. Keeping a tight arc length helps improve penetration and prevents contamination.
This process is excellent for achieving high-quality, precise welds.
Related Product:
Arccaptain TIG200P AC DC Multi Process Pulse TIG Aluminum Welder
The ARC TIG200 AC/DC Multi-Process Welder is ideal for TIG welding (GTAW) stringer beads, offering precise arc control for clean, smooth welds. With pulse and AC/DC functions, it ensures steady, controlled welding on aluminum and stainless steel, making it perfect for precision work and automotive repairs. |
How to Create a Perfect Welding Stringer Bead
Step 1 – Choosing the Right Electrode or Wire
For stick welding, choose E6010 or E7018 electrodes. These provide deep penetration and smooth welds. In MIG welding, ER70S-6 wire is ideal for carbon steel applications. If you are TIG welding, use pure tungsten for aluminum and thoriated tungsten for steel.
Step 2 – Setting the Correct Amperage & Voltage
Setting the correct amperage and voltage is crucial. Too much heat can lead to undercutting and weak welds. Not enough heat causes poor penetration.
Adjust these settings based on the thickness of the material and the welding process you are using.
Step 3 – Mastering Travel Speed & Arc Control
Keep your movement steady and continuous to avoid excessive buildup. Maintain a close distance between the electrode and the workpiece to achieve better penetration.
A short arc length results in cleaner and more controlled welds.
Following these steps will help you create a strong and visually appealing welding stringer bead.
Common Mistakes & How to Fix Them
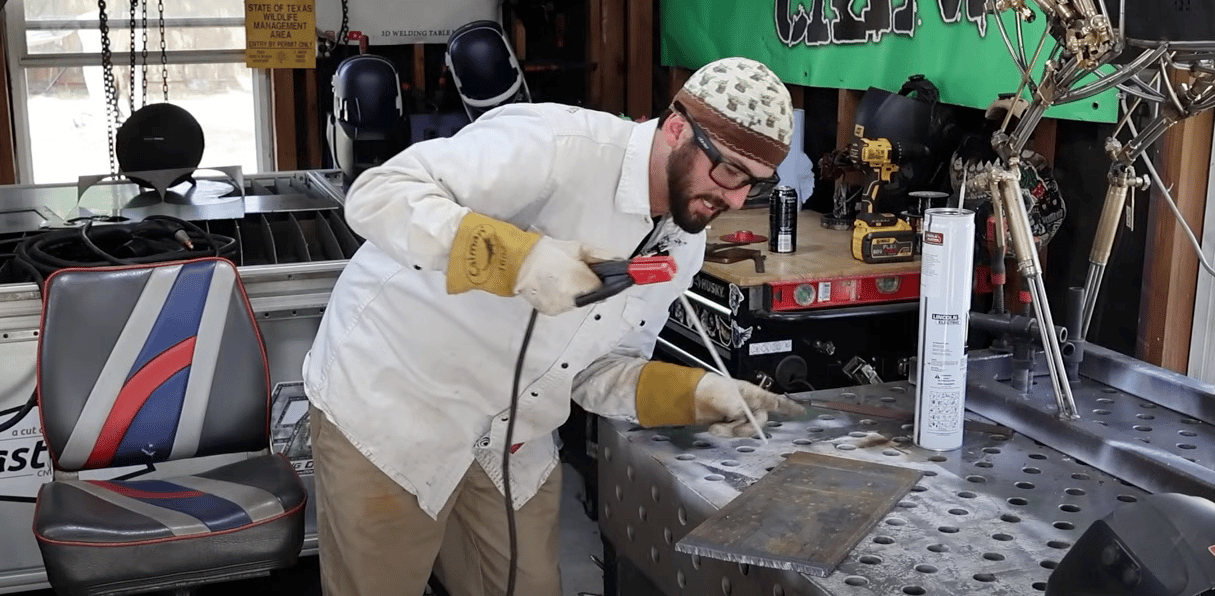
1. Undercutting Along the Weld Bead
Cause: Moving too fast or using too high amperage.
Solution: Slow down your travel speed and adjust the heat settings properly. Reducing the amperage will help minimize undercutting issues. (Read more: What Is Undercut in Welding?)
2. Lack of Fusion (Cold Welds)
Cause: Low heat input or poor electrode angle.
Solution: Increase the amperage to provide adequate heat. Ensure you maintain the correct torch or electrode angle to improve fusion.
3. Uneven Bead Appearance
Cause: Inconsistent travel speed or arc length.
Solution: Keep a steady, controlled motion throughout the welding process. Practice maintaining a uniform pace to produce even beads.
4. Excessive Spatter in MIG Welding
Cause: Poor voltage settings or incorrect gas mixture.
Solution: Adjust to higher voltage settings and use the proper shielding gas, such as a CO2/argon mix. Ensure workpieces are clean to minimize spatter. (Read more: What Is Weld Spatter?)
Use this table for a quick reference:
Mistake |
Cause |
Solution |
Undercutting |
Fast speed/high amperage |
Slow down and reduce amperage |
Lack of Fusion |
Low heat/poor angle |
Increase amperage, correct angle |
Uneven Bead |
Inconsistent speed/arc length |
Steady and controlled motion |
Excessive Spatter |
Poor voltage/gas mixture |
Higher voltage, proper gas, clean workpiece |
Paying attention to these aspects will enhance the quality of your welding stringers. Address each issue systematically, and you'll achieve better results in your projects.
Welding Stringers vs. Weave Patterns: Which Should You Use?
Choosing between stringer beads and weave patterns in welding depends on your project needs. Each has its advantages and uses.
Stringer Beads
- Precision: Offers straight and precise welds.
- Heat Distortion: Less likely to cause distortion due to focused heat.
- Speed: Faster travel speed, making it time-efficient.
Weave Patterns
- Weld Coverage: Provides wider coverage, useful for filling gaps or covering large areas.
- Heat Distribution: Distributes heat more evenly, reducing the risk of burn-through.
- Thickness: Better suited for thicker materials.
Feature |
Stringer Bead |
Weave Pattern |
Precision |
High precision with a straight line weld. |
Less precision, wider coverage. |
Travel Speed |
Faster travel speed, which saves time. |
Slower, as it involves more elaborate movement. |
Heat Distortion |
Causes less distortion due to less heat spread. |
Spreads heat more evenly, reducing burn-through risk. |
Material Use |
Ideal for thin materials and situations requiring precision. |
Suitable for thicker materials and filling gaps. |
When deciding, consider the material thickness and the level of precision you need. Stringer beads are ideal for tasks requiring straight welds and reduced heat effects.
Weave patterns offer better results for covering larger areas or handling thicker material. Use the right technique to ensure high-quality welds for your project.
Watch Related Video 🎬:
FAQs About Welding Stringers 💬
Understanding how to properly work with welding stringers can improve the quality and strength of your welds. Here are some key points about techniques, materials, and best practices for welding stringers.
What Is the Ideal Travel Speed for Welding Stringers?
The ideal travel speed for welding stringers is typically between 6 to 10 inches per minute. This speed ensures proper penetration and fusion of the weld metal with the base metal. Adjusting the speed based on the material thickness and type can help achieve the best results.
Can Stringer Beads Be Used in All Welding Positions?
Yes, stringer beads can be used in all welding positions, including flat, horizontal, vertical, and overhead. They are versatile and provide good control over the weld pool, making them suitable for various applications. However, the technique may need slight adjustments depending on the position.
Can I Use Stringers on Thick Materials?
Yes, you can use stringers on thick materials. Stringer beads are effective for deep penetration, which is essential for welding thicker sections. Multiple passes may be required to ensure a strong and complete weld.
How Do You Avoid Undercut When Welding Stringers?
To avoid undercut when welding stringers, maintain a consistent travel speed and proper electrode angle. Keep the arc length short and ensure even heat distribution. Using the correct welding parameters and techniques will help prevent undercut and ensure a smooth weld.
What Is the Best Electrode for Stringer Beads?
The best electrode for stringer beads is typically an E7018 for steel welding. This electrode provides good arc stability and produces strong, high-quality welds. For other materials, choose an electrode that matches the base metal and desired weld characteristics.