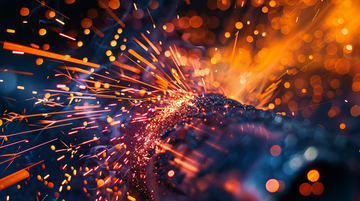
What does a good weld look like? If you’re new to welding or looking to improve, recognizing a quality weld is key to achieving strong and reliable results.
A good weld is more than just visually appealing; it ensures the strength, safety, and durability of the joint. Whether you’re working on small DIY projects or large industrial jobs, understanding the characteristics of a good weld, like consistency, smoothness, and proper penetration—is essential.
In this guide, we’ll break down what makes a weld successful and how to spot the difference between a strong weld and one that might fail.
Understanding Welding Fundamentals
In welding, your success hinges on knowing the basic techniques, the proper use of equipment, and understanding the materials you work with.
Basic Welding Techniques
Welding processes vary, but three primary techniques are fundamental:
- TIG Welding (GTAW): A high-skill method using a tungsten electrode for creating strong, clean welds on a variety of metals.
- MIG Welding (GMAW): Utilizes a consumable wire electrode and shielding gas, ideal for thick or long welds and more forgiving for beginners.
- Stick Welding (SMAW): Employs an electrode stick that melts to form the weld, suitable for outdoor use and robust materials.
Each technique requires a distinct skill set and understanding of welding principles.
Your choice depends on the base material, weld strength requirements, and desired finish.
Welding Equipment and Materials
Handling welder equipment competently is crucial:
- Electrode: Determines the type of weld. Selection depends on the welding process and the materials being joined.
- Filler Metal: Added during the process, it must be compatible with the base material to ensure a strong weld.
- Shielding Gas: Protects your weld from contaminants; varies with the welding method, whether it's TIG, MIG, or stick welding.
Safety equipment is non-negotiable to protect yourself from sparks, UV radiation, and fumes.
Always use appropriate safety gear like helmets, gloves, and aprons.
Especially for beginners, it’s important to familiarize yourself with the tools and materials necessary for the specific type of welding you'll be doing.
Understanding and respecting the welding safety protocols cannot be overstated.
It’s not only about the quality of the weld but also your well-being.
What Does a Good Weld Look Like: How To Identify
You can distinguish a high-quality weld by certain visual cues and through standardized inspection techniques. Mastery in these methods equips you with the ability to ensure the durability and strength of welded structures.
Characteristics of a Strong Weld
A strong weld is defined by a set of distinct features:
- Smoothness: The weld bead should be smooth without excessive spatter.
- Consistency: Look for a consistent weld bead width and height along the entire length of the weld.
- Uniformity: The color and texture of the weld metal should be uniform, indicating proper temperature control during welding.
- Penetration: Good penetration means the weld metal has adequately fused with the base metal, which is essential for strength.
The appearance of the weld is also a factor; a high-quality weld is often aesthetically pleasing.
However, focus primarily on the structural integrity, which includes tensile strength and durability.
Visual and Technical Inspection Techniques
For effective visual inspection, consider these techniques:
- Visual Observation: Examine the weld for smoothness, consistency, and lack of visible defects such as cracks or pores.
- Direct Measurement: Use tools to measure the weld bead size and check for uniformity.
Technical inspection methods extend beyond what the eye can see:
- X-ray Inspection: Reveals internal flaws such as cracks or voids in the weld.
- Ultrasonic Inspection: Uses high-frequency sound waves to detect discontinuities inside the weld.
- Magnetic Particle Inspection: Identifies surface and near-surface defects in ferromagnetic materials.
Each of these weld testing techniques has its place in ensuring the quality of a weld.
Your goal is to combine visual inspections with these technical methods to confirm the weld's overall strength and durability.
Recognizing Substandard Welds
In welding, the integrity and strength of the metalwork often hinge on the quality of its welds. Substandard welds can result in malfunction or failure, thus identifying these flaws is crucial for safety and function.
Common Welding Defects and Their Causes
Undercut: A groove that appears at the base of the weld bead may occur due to high voltage or high travel speed. It weakens the welding joint and could lead to cracking.
- Causes: Excessive heat, incorrect voltage or amperage, fast travel speed.
Spatter: Small droplets of molten material that scatter around the weld can occur when the settings of the welding torch are inappropriate.
- Causes: Inappropriate voltage or amperage, dirty material.
Porosity: Cavities or holes are caused by trapped gas in the solidified weld. This defect affects weld strength and can lead to premature failure.
- Causes: Contaminated surface, improper shielding gas, or incorrect welding technique.
Slag Inclusions: Non-metallic solid particles trapped in the weld metal occur if the slag is not removed after a pass.
- Causes: Improper cleaning between weld passes.
Cracking: Visible lines in or around the weld area can be the result of undue tension, inappropriate filler materials, or high heat.
- Causes: Rapid cooling, incompatible materials, excessive joint constraint.
Uneven Weld Bead: Fluctuations in height and width of the weld bead weaken the joint and are often a result of an unsteady hand or incorrect travel speed.
- Causes: Inconsistent welding technique, improper travel speeds.
Lack of Fusion: The failure to properly melt and fuse the base metal or previous pass layers can result in a weak bond.
- Causes: Low heat input, improper angle or speed of the welding torch.
Burn-through: Excessive penetration can cause holes in the base metal, often due to too much heat.
- Causes: Very high amperage, slow travel speed, thin materials.
Holes/Burnout: Unwanted perforations in or through the metal can compromise the structure.
- Causes: Typically too much heat input or insufficient filler metal.
Avoiding Errors in the Welding Process
To prevent the occurrence of bad welds, consider the following:
- Use correct settings: Ensure that your welding torch's voltage and amperage are adjusted according to the material and type of welding.
- Clean the area before welding: Remove any contaminants to avoid porosity and poor adhesion.
- Choose the right filler metal: The filler metal should be compatible with the base metal to prevent cracking and poor weld quality.
- Control your speed: Maintain a steady travel speed to avoid uneven beads and undercut.
- Apply sufficient heat: Heat input should be adequate to ensure proper fusion but not too high to cause burnouts or holes.
- Practice your technique: A consistent and skillful welding technique contributes to quality welds and minimizes defects.`
Welding Across Different Metals
When welding different metals, you must consider the unique properties of each type, alongside appropriate techniques and solutions for common challenges.
Techniques for Specific Metals
Aluminum: For aluminum, you typically use TIG welding (Tungsten Inert Gas) or MIG welding (Metal Inert Gas).
TIG is preferred for its finer control and cleaner weld bead, which is essential due to aluminum’s thermal conductivity and sensitivity to heat.
-
TIG Welding:
- Gas: Argon
- Electrode: Tungsten
- Filler Material: Aluminum Alloy
-
MIG Welding:
- Gas: Argon or a mix of Argon and Helium
- Filler Material: Match to base aluminum alloy
Stainless Steel: Stainless steel is best handled with TIG or MIG welding. The key is to maintain the steel’s corrosion resistance by preventing carbon contamination.
-
TIG Welding:
- Gas: Argon
- Filler Material: Match stainless steel grade
-
MIG Welding:
- Gas: Argon with some Carbon Dioxide
- Filler Material: Match stainless steel grade
Carbon Steel: The most versatile for carbon steel is SMAW (Shielded Metal Arc Welding) or stick welding.
Carbon steel is forgiving and the process is cost-effective.
- Stick Welds:
- Electrode: Mild steel or low-hydrogen electrodes
- Shielding: Flux coating
Challenges and Solutions
Metals Like Iron and Nickel: These metals can be more challenging due to their melting points and brittleness. It's crucial to preheat them to reduce the risk of cracking.
- Challenge: High Melting Points
- Solution: Use controlled heat input - proper preheating and post-weld heat treatment.
Base Metal Preparation: Regardless of the metal, proper preparation of the base metal is critical. Clean the metal to remove any contaminants and ensure a strong adhesion and smooth weld pattern.
- Pre-Weld Action:
- Clean thoroughly to avoid contamination.
- Apply correct preheat to align with metal's properties.
Filler Material Incompatibility: Always match the filler material to the base metal to prevent weak welds. For instance, using the incorrect filler for aluminum can result in porosity and a weak joint.
- Filling Correctly:
- Select the right filler material.
- Confirm compatibility with base metal alloy.
Using precise techniques tailored to each metal type and addressing their respective welding challenges ensures strong, durable, and effective joints that meet your project's specific needs.
Also read: Different Types of Metal Used in Welding
Safety and Best Practices in Welding
Before operating any welding equipment, it is crucial to understand the safety measures and best practices. These ensure not only your safety but also the quality of your work.
Welding Safety Equipment
Helmet and Eye Protection: Your eyes and face are at risk from sparks, spatter, and intense light.
Always wear a welding helmet, such as an auto-darkening helmet with the correct shade number for the type of welding you are doing. Supplement that with safety glasses or goggles to safeguard against debris.
Protective Clothing: Heat and spatters can also burn skin and ignite clothing.
Wear fire-resistant clothing, heat-resistant welding gloves, and welding aprons to protect exposed skin and your regular clothes.
Ensure the clothing is clean and free from any flammable substances like paint or oil.
Respiratory Protection: Shielding gases and welding fumes can be hazardous.
Use an appropriate respirator, especially when welding in confined spaces or where natural ventilation is insufficient.
Maintaining a Safe Working Environment
Ventilation: Adequate ventilation is crucial to disperse harmful welding fumes.
Either work in a well-ventilated area or use local exhaust systems to capture fumes at the source.
Equipment Maintenance: Regular maintenance of your welding equipment is paramount.
Inspect hoses, regulators, and torches for wear and damage before use to prevent leaks and malfunctions.
Cleanliness: Maintain a clean welding area to reduce contamination of your weld and the risk of fire.
A wire brush is a vital tool; use it to clean away slag, paint, or rust before you start welding.
Fire Safety: Devices like fire-resistant blankets and screens can help contain sparks and prevent accidental fires.
Keep a fire extinguisher readily available, and remain in the work area for at least 30 minutes after completing the weld to ensure no smoldering fires start.
Practice: Consistently producing quality welds requires practice.
As a professional welder, honing your skill minimizes the safety risks associated with improper technique.
Ensure proper torch angle and heat control through practice to maintain a consistent weld seam and reduce errors.
Advancing Your Welding Skills
To rise above the level of a novice, your journey in becoming a professional welder hinges on perfecting your technique and dedication to ongoing improvement.
Developing Technique and Mastery
When it comes to welding, technique is pivotal. You must ensure control over the welding torch and the wire electrode to produce welds with consistent weld penetration. Make sure to avoid common issues such as dips and craters.
- Consistent practice: Regularly weld different joints and positions to build muscle memory.
- Precision handling: Learn to hold the torch steadily to maintain a consistent angle and distance from the workpiece.
Continuous Learning and Improvement
The field of welding is continuously evolving, with advancements in welding machines and techniques.
Even if you're not working with the latest equipment, avoid the trap of becoming a "cheap welder" by skimping on your skill development:
- Educational resources: Keep up-to-date with new practices and welding machines by studying instructional guides and tutorials.
- Integrity: Strive for structural integrity in your welds, as it ensures safety and longevity of the projects you work on.
Preparation and Aftercare of Welds
Good welding outcomes hinge on meticulous preparation and thorough aftercare, ensuring structural integrity and longevity of the weld.
Setting Up for a Successful Weld
Before initiating a welding project, you need to consider several key factors to set the stage for quality work.
Your preparation should involve selecting the correct filler metal and equipment, ensuring the base metal is free from contaminants like rust, and confirming the cleanliness of all materials involved. This approach reduces the possibility of weld defects.
- Cleanliness: Remove oils, dirt, and any other contaminants on the surface of the metal, as these can cause porosity and other weld quality issues.
- Correct Filler Metal: Match the filler metal closely with the base metal to ensure compatibility and thereby enhance the strength of the weld.
- Equipment Check: Verify that all welding equipment, including your welder, is in good condition and appropriate for the welding technique you plan to use.
- Welding Technique: Familiarize yourself with the specific welding technique you intend to employ. Each technique requires a certain skill set and set of conditions to be used effectively.
Post-Weld Treatment and Analysis
After completing a weld, inspect and treat the weld to promote its durability and functionality.
Post-weld activities include visual inspection and, if necessary, stress-relieving treatments.
- Visual Inspection: Look closely at the weld bead; it should be uniform, without cracks or signs of incomplete fusion.
- The consistent weld bead indicates proper technique and filler material usage.
- Uniformity: Assess for consistent bead width, smoothness, and the absence of defects such as porosity or undercutting.
- Stress-Relieving: Depending on the metal and the project's requirements, you might need to perform post-weld heat treatment to alleviate residual stresses that can cause distortions or weaken the weld over time.
Conclusion
If you want to achieve good welds, start with the right equipment, which lays the foundation for quality workmanship. Smooth, even, and thoroughly penetrating welds are signs of high-quality results that ensure project safety and longevity.
By mastering the core principles of welding and continuously applying best practices, your welds will reflect your commitment to excellence. For the best results, equip yourself with ArcCaptain's trusted welding tools, designed to help you achieve precision and craftsmanship on every job.
Frequently Asked Questions about What Does a Good Weld Look Like
What creates the strongest weld?
The strongest weld is created through proper preparation of materials, correct selection and application of welding techniques, and the use of compatible filler materials. Factors like clean workpieces, precise control of welding parameters, and adequate heat input ensure deep penetration and strong fusion between the base metals.
How do you test a good weld?
A good weld can be tested using both non-destructive and destructive methods. Non-destructive tests include visual inspection, ultrasonic testing, and radiography, which identify external and internal imperfections without damaging the weld. Destructive testing, like bend tests or tensile tests, assesses the weld's mechanical properties but destroys the weld in the process.
How should welds look?
Welds should look smooth and uniform in appearance, with consistent width and height along the joint. There should be no visible defects such as cracks, porosity, or undercutting. The weld should show good fusion along the toe of the weld, where it meets the base metal, and the weld bead should have a uniform texture and color.
How is weld quality measured?
Weld quality is measured against predefined standards that assess characteristics like bead shape, depth of penetration, and the absence of defects. Tools such as welding gauges can measure bead size and check for concavity or convexity, while more advanced methods include metallurgical analysis and non-destructive testing to detect internal flaws.
Can you fix a bad weld?
Yes, a bad weld can often be repaired, but the approach depends on the nature and severity of the defects. Minor issues may be fixed by grinding down the irregularities and re-welding, while more serious flaws like deep cracks might require removing the entire weld and starting over. Repair work must ensure complete penetration and fusion to restore the weld's strength.