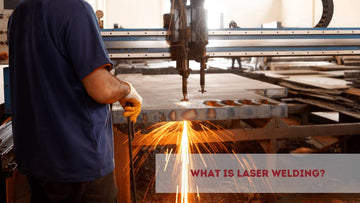
If you're interested in welding, you've probably heard of laser welding. But what exactly is it? Laser welding is a type of welding that uses a laser beam to join two pieces of material together. It's a relatively new technology, but it's quickly becoming one of the most popular methods of welding.
Laser welding is a precise and efficient way to join materials together. It's used in a variety of industries, from automotive to aerospace, and it's capable of welding a wide range of materials, including metals, plastics, and ceramics. But how does it work?
In the next section, we'll take a closer look at the technology behind laser welding and explore the different types of lasers used in the process.
Key Takeaways
- Laser welding is a type of welding that uses a laser beam to join two pieces of material together.
- Laser welding is a precise and efficient way to join materials together and is used in a variety of industries.
- In the next section, we'll explore the technology behind laser welding and the different types of lasers used in the process.
What Is Laser Welding
Laser welding is a modern and highly efficient welding technique that uses a high-energy laser beam to melt and fuse metal parts together. The laser beam heats the material to its melting point, creating a small, localized pool of molten metal that cools and solidifies to form a strong, durable weld joint.
Laser welding is widely used in the manufacturing industry for joining metal parts that require high precision and strength. It is particularly useful for welding thin materials, such as those used in the aerospace and medical industries, as it produces a narrow, focused beam that minimizes heat input and reduces the risk of warping or distortion.
Overall, laser welding is a versatile and effective welding technique that offers numerous benefits over traditional welding methods. Whether you are working on a small-scale project or a large-scale manufacturing operation, laser welding can help you achieve high-quality, precise welds quickly and efficiently.
How Does Laser Welding Technology Work?
Laser welding is a process that uses a high-energy beam of light to melt and fuse two pieces of metal together. The laser beam is focused onto the joint between the two pieces of metal, creating a small and precise weld. This process is widely used in the manufacturing industry due to its high precision and speed.
Materials Compatible with Laser Welding
Laser welding can be used to weld a variety of materials, including:
- Stainless steel
- Aluminum
- Titanium
- Copper
- Brass
- Gold
- Silver
- Nickel alloys
The process can also be used to weld dissimilar materials together, such as aluminum and copper.
The laser beam is generated by a laser source and directed through a series of mirrors and lenses to focus the beam onto the workpiece. The laser beam can be either continuous or pulsed, depending on the application.
The laser beam melts the surface of the metal, creating a small pool of molten metal. As the laser beam moves along the joint, the molten metal solidifies, creating a strong and precise weld.
In conclusion, laser welding is a highly precise and efficient welding process that is widely used in the manufacturing industry. It can be used to weld a variety of materials, including dissimilar materials, and offers precise control over the size and location of the weld.
Types of Lasers Used in Welding
When it comes to laser welding, there are two main types of lasers that are used: solid-state lasers and gas lasers.
Solid-State Lasers
Solid-state lasers are the most commonly used type of laser in welding. They are known for their high power output and their ability to produce a very precise beam. Solid-state lasers use a solid material as the active medium, which is usually a crystal or a glass. The most common types of solid-state lasers used in welding are neodymium-doped yttrium aluminum garnet (Nd) and fiber lasers.
Gas Lasers
Gas lasers are another type of laser that is used in welding. They are less common than solid-state lasers, but they still have their advantages. Gas lasers use a gas as the active medium, which is usually a mixture of helium and neon. The most common type of gas laser used in welding is the carbon dioxide (CO2) laser.
Both solid-state and gas lasers can be used for two main types of laser welding: heat conduction welding and keyhole welding.
Overall, the choice of laser and welding method will depend on the specific application and the materials being welded.
What is Heat Conduction Welding?
Heat conduction welding is a process in which the laser beam heats the surface of the material, causing it to melt and fuse together. This type of welding is commonly used for thin materials or materials with low melting points.
What is Keyhole Welding?
Keyhole welding, on the other hand, is a process in which the laser beam creates a hole in the material, which then fills up with molten material as the laser beam moves along the joint. This type of welding is commonly used for thicker materials or materials with higher melting points.
Advantages of Laser Welding
One of the advantages of laser welding is its precision. The laser beam can be focused onto a small area, allowing for precise control over the size and location of the weld. This precision also allows for minimal heat input, reducing the risk of distortion or damage to the workpiece.
Benefits of Laser Welding
Laser welding is a highly efficient and precise welding technique that offers a number of advantages over traditional welding methods.
Here are some of the key benefits of laser welding:
-
High Precision: Laser welding is extremely precise and can be used to weld even the smallest of components with high accuracy. This is because the laser beam can be focused to a very small point, allowing for precise control over the welding process.
-
Minimal Heat Affected Zone (HAZ): Laser welding produces a very small HAZ, which means that there is minimal distortion or damage to the surrounding material. This is particularly important when welding delicate or thin materials, as it minimizes the risk of warping or deformation.
-
High Speed: Laser welding is a very fast process, which means that it can be used to weld large volumes of components quickly and efficiently. This makes it ideal for use in high-volume manufacturing environments.
-
Versatility: Laser welding can be used to weld a wide range of materials, including metals, plastics, and ceramics. This makes it a versatile welding technique that can be used in a variety of different applications.
-
Reduced Welding Costs: Laser welding is a cost-effective welding technique, as it requires less material and produces less waste than traditional welding methods. This can help to reduce overall welding costs and improve profitability.
-
Improved Weld Quality: Laser welding produces high-quality welds that are strong, durable, and aesthetically pleasing. This is because the laser beam produces a narrow, deep weld that penetrates the material more effectively than other welding techniques.
In summary, laser welding offers a number of advantages over traditional welding methods, including high precision, minimal HAZ, high speed, versatility, reduced costs, and improved weld quality. These benefits make it an attractive option for a wide range of welding applications.
Disadvantages of Laser Welding
Laser welding is a highly precise and efficient welding method, but it also has some disadvantages that you should be aware of. In this section, we will discuss the limitations and considerations of laser welding.
Limitations and Considerations
Higher Cost
One of the main disadvantages of laser welding is its higher cost compared to other welding methods. The equipment and maintenance costs for laser welding are significantly higher than those of traditional welding methods. This makes it a less viable option for small-scale projects or those with limited budgets.
Limited Thickness
Laser welding is not suitable for welding thick materials. The thickness of the material that can be welded using laser welding is limited, and it varies depending on the type of laser used. This means that if you need to weld thick materials, you may need to use a different welding method.
Limited Joint Access
Laser welding requires direct line-of-sight access to the joint being welded. This means that if the joint is in a hard-to-reach or confined area, laser welding may not be possible. In addition, the laser beam must be aligned accurately with the joint, which can be challenging in some cases.
Material Sensitivity
Laser welding can also be sensitive to the material being welded. Some materials, such as copper and aluminum, can be difficult to weld using laser welding. In addition, some materials may require additional preparation or post-weld treatment to ensure the quality of the weld.
In conclusion, laser welding has many advantages, but it also has some limitations and considerations that you should be aware of. By understanding these disadvantages, you can make an informed decision about whether laser welding is the right welding method for your project.
Applications of Laser Welding in Different Industries
Due to its high precision, faster processing time, wide material tolerance, and consistent quality, laser welding has many applications.
Here's a list of its applications in different sectors, each with a brief description:
Automotive Industry:
- Body Components: Laser welding is used for joining thin sheets in car bodies, providing high strength with minimal distortion.
- Powertrain Components: Used in the welding of gear components and engine parts, laser welding ensures high-quality joins essential for these critical components.
Aerospace Industry:
- Engine Components: Laser welding is crucial for components like turbine blades, offering precision and strength in high-stress environments.
- Structural Elements: Used in the welding of airframe components, it ensures lightweight and strong joints, essential for aircraft performance and safety.
Electronics:
- Microelectronics: It's used in the joining of small electronic components, where precision and minimal thermal impact are critical.
- Battery Manufacturing: Laser welding helps in creating reliable connections in battery cells and packs, crucial for performance and safety.
Jewelry Making:
- Fine Detail Work: Ideal for delicate tasks like repairing or resizing jewelry, laser welding offers precision without damaging heat-sensitive materials.
Shipbuilding:
- Structural Welding: Used in the construction of ships, laser welding provides strong, deep welds for large steel sections.
Rail Industry:
- Rail Component Fabrication: For the construction of rail cars and components, laser welding offers high-strength joins essential for durability and safety.
Construction Equipment:
- Heavy Machinery: In the fabrication of construction equipment, laser welding is used for its strength and efficiency in joining heavy materials.
Energy Sector:
- Solar Panels and Wind Turbines: Laser welding is employed in the manufacturing of solar panel components and wind turbine parts, where precision and strength are key.
Consumer Products:
- Home Appliances: Used in the manufacturing of various household items, offering aesthetic and strong welds.
Laser welding's precision, speed, and versatility make it a valuable technique in these industries, enhancing product quality, durability, and performance.
Step-by-Step Process to Laser Welding
Laser welding is a high-precision welding technique that uses a laser beam to melt and join two metal parts. The process is highly efficient and produces a strong, clean weld. Here are the steps to process laser welding:
-
Preparation: Before starting the laser welding process, the metal parts to be joined must be cleaned thoroughly to remove any dirt, oil, or debris. The parts should also be clamped securely in place to ensure they do not move during welding.
-
Alignment: The laser beam must be precisely aligned with the joint to be welded. This is done using a laser alignment system that ensures the beam is focused on the correct spot.
-
Welding Parameters: The laser welding parameters must be set correctly according to the type and thickness of the metal parts being welded. This includes the laser power, welding speed, and pulse duration.
-
Welding: Once the laser beam is properly aligned and the welding parameters are set, the welding process can begin. The laser beam is directed at the joint, melting the metal and forming a bond between the two parts. The beam moves along the joint, creating a continuous weld.
-
Inspection: After the welding is complete, the joint should be inspected to ensure the weld is of the desired quality. This includes checking for any defects or irregularities in the weld, such as cracks or voids.
Laser welding is a complex process that requires a high level of skill and expertise. However, by following these steps and using the right equipment, you can produce high-quality welds that are strong, clean, and precise.
Laser Welding Equipment
Laser welding equipment is a highly specialized tool that utilizes laser technology to join two or more pieces of metal together. This process is widely used in various industries, including automotive, aerospace, and medical. A laser welding machine consists of several key components that work together to create a precise and efficient welding process.
Key Components of a Laser Welding Machine
The primary components of a laser welding machine include the laser source, optics, power supply, robot or torch, and the focal point. The laser source is the heart of the welding machine, producing the high-intensity beam of light that is used to melt and join the metal pieces. The optics help to focus the laser beam onto the weld joint, ensuring that the energy is concentrated at the right location.
The power supply provides the necessary electrical power to operate the laser source and other components of the welding machine. The robot or torch is used to move the laser beam along the weld joint, while the focal point determines the size and shape of the weld.
Maintenance and Safety Measures
Proper maintenance and safety measures are essential for ensuring the longevity and safety of the laser welding equipment. Regular maintenance of the laser source, optics, and power supply is necessary to keep the machine operating at peak performance. It is also important to follow safety guidelines to prevent accidents and injuries.
Safety measures include wearing appropriate personal protective equipment, ensuring proper ventilation, and following safe operating procedures. Additionally, regular inspections and testing of the equipment can help identify potential issues before they become major problems.
In conclusion, laser welding equipment is a sophisticated tool that requires careful maintenance and safety measures to ensure optimal performance and safety. Understanding the key components of a laser welding machine can help you choose the right equipment for your needs and operate it safely and efficiently.
Materials Can be Welded Using Laser Welding
Laser welding is a versatile process that can be used to join a wide range of materials. Here are some of the materials that can be welded using laser welding:
-
Metals: Laser welding can be used to join a variety of metals, including steel, aluminum, copper, brass, titanium, and nickel. Laser welding is particularly useful for welding thin sheets of metal, as it produces a narrow, precise weld that minimizes heat distortion.
-
Plastics: Laser welding can be used to join thermoplastics, which are plastics that can be melted and reformed. This includes materials such as polycarbonate, acrylic, and nylon. Laser welding is particularly useful for joining small, delicate plastic parts, as it produces a clean, precise weld that minimizes damage to the surrounding material.
-
Ceramics: Laser welding can be used to join ceramics, including materials such as alumina, zirconia, and silicon carbide. Laser welding is particularly useful for joining ceramics that are difficult to weld using traditional methods, as it produces a precise, localized heat source that minimizes thermal stress.
-
Composites: Laser welding can be used to join composite materials, which are materials made up of two or more different materials. This includes materials such as carbon fiber reinforced plastic (CFRP) and glass fiber reinforced plastic (GFRP). Laser welding is particularly useful for joining composite materials that are difficult to weld using traditional methods, as it produces a precise, localized heat source that minimizes damage to the surrounding material.
Overall, laser welding is a versatile process that can be used to join a wide range of materials. Whether you are working with metals, plastics, ceramics, or composites, laser welding can provide a precise, reliable, and efficient way to join your materials together.
Safety Considerations in Laser Welding
Laser welding is a highly precise and efficient method of joining materials. However, it also poses some potential hazards that require proper safety measures. Here are some safety considerations that you should keep in mind when performing laser welding:
Protective Equipment
When using laser welding equipment, you should wear appropriate protective gear to prevent any potential injuries. The following are some of the essential safety equipment that you should use:
- Laser safety glasses or goggles
- Protective clothing, including gloves, aprons, and sleeves
- Respirators or dust masks to prevent inhalation of fumes or gases
- Earplugs or earmuffs to protect against noise
Proper Ventilation
Laser welding produces fumes and gases that can be hazardous to your health. Proper ventilation is essential to maintain a safe working environment. Ensure that your workspace has adequate ventilation to remove any harmful fumes or gases.
Electrical Safety
Laser welding equipment uses high voltage and current, which can be dangerous if not handled correctly. Always follow the manufacturer's instructions and guidelines when operating the equipment. Ensure that the equipment is grounded and that all electrical connections are secure.
Fire Safety
Laser welding generates intense heat that can cause fires. Keep flammable materials away from the welding area and ensure that you have a fire extinguisher nearby in case of an emergency.
Conclusion
In conclusion, laser welding is a highly precise and efficient welding technique that uses a laser beam to join two pieces of metal. It offers several advantages over traditional welding methods, including faster welding speeds, minimal distortion, and the ability to weld a wide range of materials.
One of the key benefits of laser welding is its ability to produce high-quality welds with minimal heat input. This reduces the risk of warping or distortion, making it ideal for precision welding applications.
Another advantage of laser welding is its versatility. It can be used to weld a wide range of materials, including metals, plastics, and ceramics. This makes it an ideal choice for a variety of industries, including automotive, aerospace, and medical.
Overall, laser welding is a highly effective welding technique that offers several advantages over traditional welding methods. If you are looking for a precise, efficient, and versatile welding solution, laser welding is definitely worth considering.
Frequently Asked Questions
Is laser welding as strong as MIG welding?
Yes, laser welding can be just as strong as MIG welding. Laser welding produces a narrow, deep weld that can have high strength and quality. The strength of the weld depends on the materials being welded and the welding parameters used. However, laser welding can be more precise and accurate than MIG welding, which can result in stronger welds.
Is laser welding better than welding?
Laser welding has some advantages over traditional welding methods like MIG welding, TIG welding, and arc welding. Laser welding can be more precise, faster, and produce a smaller heat-affected zone. Laser welding can also be done remotely, which can improve safety and accessibility. However, laser welding can be more expensive and require more specialized equipment and training.
Does laser welding really work?
Yes, laser welding is a proven welding technique that has been used in various industries for decades. Laser welding uses a high-energy laser beam to melt and fuse materials together. The laser beam can be precisely controlled to produce high-quality welds with minimal distortion and defects. Laser welding can be used on a wide range of materials, including metals, plastics, and ceramics.
Where is laser welding used?
Laser welding is used in various industries, including automotive, aerospace, medical, and electronics. Laser welding is commonly used to weld components with complex geometries or thin walls, where traditional welding methods may not be suitable. Laser welding can also be used for precision welding and micro-welding applications, such as in the production of electronic components.