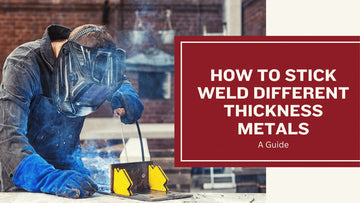
Stick welding is a popular welding method that has been around for a long time and is still used in various industrial applications, such as pipeline and structural welding. It is also a favorite among welders due to its ease of use, versatility, high deposition rates, and low expenses. This welding process is not limited to industry professionals but is also loved by hobbyists, DIY enthusiasts, and small shop owners.
However, welding different thickness metals can be challenging, especially for those less experienced. In this comprehensive guide, we will explain how Stick welding deals with thin, medium, and thick metals and what you will need to weld them successfully. We will also cover important safety equipment, such as welding helmets and gloves, as well as the cost and affordability of Stick welding.
Stick Welding Different Thickness Metals
Stick welding is an ideal process for welding medium-thick and thick metal, making it a popular choice for industrial manufacturing and construction projects. However, it is not commonly used to weld thin metal due to the lack of heat control.
Picking the Perfect Electrode
When stick welding different thickness metals, it is crucial to select the correct electrode size to ensure proper penetration and fusion. The most common stick welding rod sizes are 1/16, 5/64, and 3/32.
Pro Tip: Welding 1/8" metal? Grab a 3/32" rod. Remember, go a size thinner than your base metal to keep burn-through at bay.
Amps and Polarity - The Dynamic Duo
To weld different metals, it is necessary to adjust the amperage and polarity of the welding machine. DCEN (direct current electrode negative) is commonly used for stick welding carbon steel and mild steel, while DCEP (direct current electrode positive) is used for welding stainless steel and aluminum.
Remember Polarity Matters: DCEN for carbon and mild steel, DCEP for the shiny stuff like stainless steel and aluminum.
To start welding, connect the electrode holder to the welding machine and insert the stick electrode into the holder. Connect the ground clamp to the workpiece, ensuring a good connection. Strike an arc and maintain a consistent travel speed to prevent overheating and warping of the metal.
Stick welding is a versatile and cost-effective welding process that can be used to weld different thickness metals. With the right equipment, electrode selection, and technique, you can achieve high-quality welds on a variety of metals and metal thicknesses.
Stick Welding Thin Metal
Welding thin metal is a challenging task, and it requires precision and care. Stick welding, also known as Shielded Metal Arc Welding (SMAW), is a versatile welding technique that can be used for welding thin metals. However, the heat output of stick welding is rarely lower than 20-30 amps, making it difficult to weld thin metals without encountering issues such as burn-through, wrapping, or distortion. This section will provide practical advice on how to stick weld thin metal.
Stick Welding Equipment To Weld Thin Metal
To weld thin sheet metal, you won't need the most powerful stick welder. Instead, you can use The ARCCAPTAIN ARC160 is a 160 Amps dual voltage synergic stick welding machine, which supports 2 welding modes, including MMA and lift TIG. This feature can help you automatically matched the recommended current and voltage after diameter of welding electronic is selected.You can also adjust current manually. Professionals welder and beginners can use it easily when welding metal and repairing around the house.
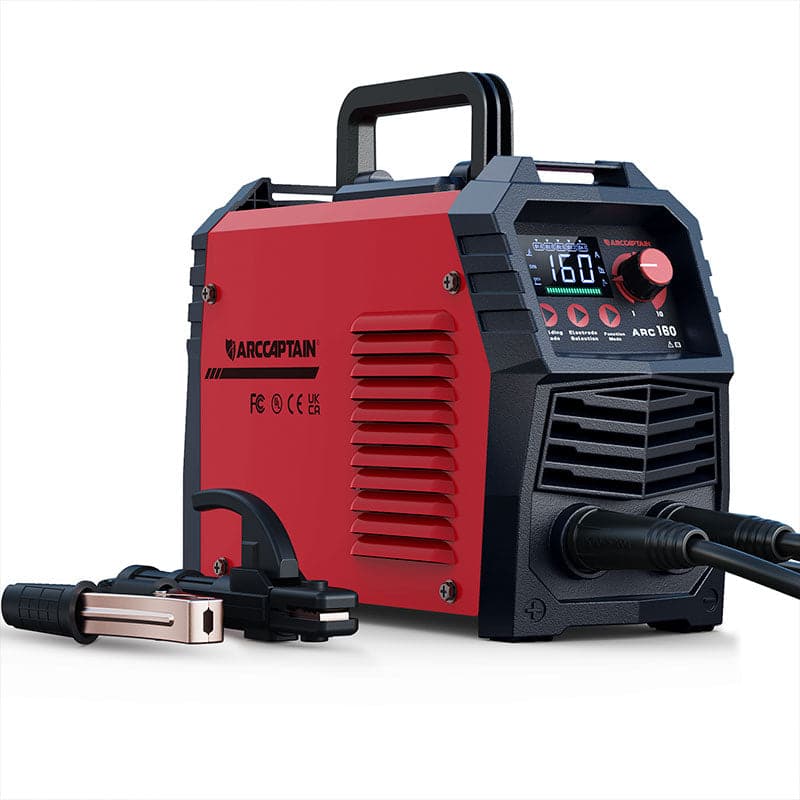
The next step is to select the right stick welding rod. You should not go higher than 1/8″ or 1/16″ diameter electrodes, as they will extend the heat-affected zone, leading to wrapping or distortion. E6011 or E6013 rods are the best options for welding thin metals. E6011 is more suitable when you don't need good-looking welding in thin or sheet metal and works well with painted, rusted, or dirty metal. However, E6013 rods show better results when the weld appearance is essential, but they require an adequately cleaned surface. In addition, 6013s offer a bit more shallow penetration compared to 6011s.
Choosing the right polarity is as important as matching filler metal. For thin metals, DCEN (Direct Current Electrode Negative or DC-) is the better choice as it offers lower penetration compared to DCEP. With DCEN, the electrode holder is connected to the negative side (-) connection of the welder.
Stick Welding Medium-Thickness Metal
Stick welding is an ideal and cost-effective method for welding medium-thickness mild steel. This process is commonly used for on-field repairs, maintenance, farm work, and hobbyist and DIY work.
Equipment For Medium-thickness Metal
- Welder: Meet the ARCCAPTAIN ARC160 110/220V SYN Portable Small Stick Welder - your new best friend for medium-thickness metal.
- Features: Portable, affordable, and packed with features of unique human-computer Interaction LED screen design, provides you accurate data display and make you read easier and more clear without taking off helmet. The mini arc welder only weight 11.73 lbs, easy to carry with handle or shoulder strap(included), very suitable for outdoor maintenance, farm, road equipment, home DIY. Plug it into a 110/220V outlet and you’re ready to tackle up to 5/32" steel.
Filler Metal (Electrode) Selection
The correct stick welding rod size is the largest one that fits in the joint, ensuring proper penetration and fusion. As the thickness of the base metal increases, you will need to use a larger diameter Stick electrode. The most common sizes are 1/16, 5/64, and 3/32. You want one step thinner electrode than the base metal.
Choosing Your Stick Electrode:
Size Matters: The golden rule? The biggest rod that fits the joint. Think 1/16, 5/64, and 3/32 inches.
Electrode Variety: From heat-packing E6010 to beginner-friendly E6013, there’s an electrode for every project.
Polarity Pointers: Remember, some rods like E6013 are picky about polarity. But no sweat, the ARCCAPTAIN ARC160 handles them like a champ.
Electrode Examples:
Electrode Type | Best For | Polarity | Amperage Setting |
---|---|---|---|
E6010 | Deep Penetration | DCEP Only | 85-110 amps |
E6013 | Beginners | AC/DC | 75-95 amps |
E7018 | Low-Hydrogen | AC/DC | 110-140 amps |
Stick Welding Thick Metal
When it comes to joining thicker metals, stick welding is one of the most widely used and suitable methods. This welding process is commonly used in farm and ranch, pipeline welding, plant maintenance and repair, shipbuilding, and other applications where thicker metals need to be joined. The high deposition and penetration with low costs make it an attractive option.
Welding Equipment For Thick Stock
Welding thicker metals with SMAW requires beveling the pieces and using multiple passes. Stick and Flux core (Dual Shielded flux core) are the most cost-efficient processes to do so. To weld thicker pieces successfully, you can use a typical 160-200 amp rated small stick welder, but most industrial-grade stick welders don't have a high-rated output like MIG or TIG machines. Nonetheless, home-repair applications that include welding thick stock will be more than manageable with the 60% duty cycle that ARC-205 offers.
Electrode Choice
Stick welding thick plates requires a manageable size of electrodes since you are bringing the root at a reasonable thickness. For the first, initial, or root pass, you will need a 1/8-inch or 5/8-inch rod, and a 5/32 or a 3/16-inch rod for filler and cap passes. An all-position cellulose E-XX10 welding electrode is used (6010, 7010, 8010) to weld the root pass.
The standard travel speed is 12 inches per minute, with reverse (DC+) polarity. This approach creates a strong foundation for the upcoming welds with slag that easily falls off. Upcoming fill and cap passes are usually done with E-7018 low-hydrogen electrodes. This is because 7018s produce strong, ductile welds that fill the opening nicely, making them the backbone of structural welding.
Weld Preparation For Thicker Pieces
Weld preparation for thicker piece welding is nearly as important as welding itself. For plates up to 3/16" thick, you should use a V-bevel to prepare the pieces. 1/2" to 3/4" pieces will require a U-bevel, which can take more filler metal to ensure stronger welds. Finally, pieces thicker than 3/4 inch will need a double V or U-bevel joint configuration. The gap should be even along the entire piece of plate or pipe, and aligning the parts is crucial. Once aligned, you can use tack welds to keep everything in place, so you can start welding.
Multi-pass Stick Welding Technique
Thicker pieces now have a larger gap between them, so you will have to use a weaving manipulation with a pushing technique for 3/16"-1/2" V bevels or a pull technique for U bevels larger than 1/2" to fill it correctly and get the solid weld bead. The weaving procedure requires more time and practice to perform. You can practice by clamping a pen in your electrode holder and drawing on a piece of paper. Cleaning the slag thoroughly before performing any other passes is crucial. Any leftover slag can cause slag inclusions that can interfere with the integrity of the weld, and they are hardly noticed without x-ray or ultrasonic testing.
After a root pass, you can opt to put a hot pass, performed within 5 minutes after completing the initial weld. The hot pass is used to correct some imperfections noticed in the root pass, taking 5-10% more heat to penetrate the first pass. The filler pass is done with smaller diameter E7018 rods, but you can use any convenient electrode manipulation method. Highly skilled welders usually use weaving techniques for cap weld to produce high-aesthetic TIG-like welds. However, you will be more than fine with a simple finish with 7018s.
Final Thoughts
Stick welding is an extremely versatile process that will allow you to weld various thickness metals. The biggest advantage is that you can do it cheaply and quickly. As a result, modern repair and maintenance and structural steel welding would be impossible with it. For you as a hobbyist, that means you can weld mild steel of various thicknesses, but as long as it is not thin. MIG welding sheet metal is significantly easier, while TIG welding provides the highest quality welds. Still, they cannot compete with Stick welding when it comes to the thick stock.
Frequently Asked Questions
How to Adjust the Technique to Weld Materials of Varying Thicknesses?
When stick welding materials of varying thicknesses, it is important to adjust the technique to ensure a proper weld. The key is to strike a balance between amperage and travel speed. For thicker materials, higher amperage and slower travel speed are required. For thinner materials, lower amperage and faster travel speed are recommended.
Recommended Electrode Types for Welding Thin Materials Using Stick Welding
When welding thin materials using stick welding, it is recommended to use electrodes with a high deposition rate and good penetration. The 6011 and 6013 electrodes are commonly used for thin materials. The 6011 is more forgiving when welding surfaces with rust or paint, while the 6013 is more versatile and can be used on a variety of materials.
Can Stick Welding Be Effectively Used for Both Thick and Thin Materials, and How?
Stick welding can be effectively used for both thick and thin materials with the proper technique and electrode selection. For thicker materials, higher amperage and slower travel speed are required, while for thinner materials, lower amperage and faster travel speed are recommended.