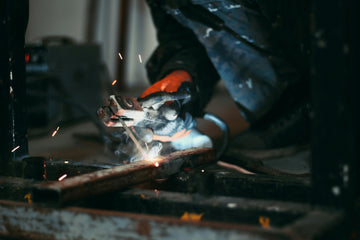
Welding rod types might sound like a small detail, but they can make a big difference in your welding results. Whether you're repairing, building, or just experimenting, using the right rod sets the stage for strong, clean welds. But with so many options out there, how do you know which one to choose?
In this blog, we’ll break down the most common welding rod types, what they’re best for, and how to pick the perfect one for your project. Read on to ensure your next weld is solid, precise, and built to last!
What Is a Welding Rod?

Welding rods, also known as electrodes, are welding materials that are melted and injected during stick welding operations.
To use a welding rod, first connect it to your welding equipment, which will create an electric arc between the base metal and the welding rod. The powerful electric arc quickly melts the metal, allowing it to be fused for welding.
What Are The Types of Welding Rods?
Picking the right welding rod is key to getting strong, clean welds. From the type of electrode to the material it’s made of, every choice matters. Let’s break it down.
Consumable vs. Non-Consumable Electrodes
When it comes to welding, understanding the difference between consumable and non-consumable electrodes is crucial. These two types serve distinct purposes and are used in different welding techniques, so knowing which one to choose can make all the difference in the quality of your welds.
-
Consumable Electrodes
These rods melt during welding, adding filler material to the joint as they burn away. They’re commonly used in shielded metal arc welding (SMAW) and are ideal for joining metals and creating strong, reliable bonds. -
Non-Consumable Electrodes
Unlike consumable rods, non-consumable electrodes don’t melt during the welding process. Instead, they generate the arc that melts the metal being joined while remaining intact. Tungsten electrodes are the most popular choice in this category because they can handle high temperatures without melting, making them perfect for precise welding jobs.
Welding Rod Materials
Each type of welding rod is made to work with specific metals. Matching the rod to the material ensures a strong bond and a quality weld.
- Carbon Steel & Mild Steel Rods: Great for structural welding and everyday repairs.
- Stainless Steel Rods: Ideal for corrosion-resistant projects like kitchen equipment or outdoor builds.
- Bronze Rods: Used for repairs, particularly on cast iron or bronze pieces.
- Aluminum Rods: Designed for lightweight, rust-proof welds on aluminum parts.
Why the Right Rod Matters
Choosing the wrong welding rod can lead to problems down the line. Weak welds are a common issue, which means your project may not hold up under stress.
In some cases, the wrong rod can damage the base material itself, creating more work or requiring costly fixes.
Taking the time to match the welding rod to the material ensures a stronger bond, better durability, and a more professional result. It’s a simple step that saves time and frustration in the long run.
Find the right welding rods for any project in our welding electrodes collection. With options suited for different materials and positions, you’ll always have the perfect match for your welding needs.
What Is The Welding Rod Number System?
Choosing the right welding rod also involves understanding numbers printed on the rod. They’re not just random codes—they tell you everything from strength to welding position and even the type of current to use. Let’s break it down so you can pick the perfect rod for your project with confidence.
What Do the Numbers Mean?
Every number on a welding rod has a purpose:
- First Two Digits: Tensile strength of the weld (measured in thousands of pounds per square inch).
- Third Digit: Welding position the rod works best for.
- Fourth Digit: Type of coating and the current it uses.
For example:
- 6010: Great for deep penetration and works with DC current.
- 7018: Perfect for low-hydrogen applications, producing smooth, strong welds.
Knowing these codes means you’re not guessing—you’re welding smarter.
Popular Welding Rod Types
Here’s a quick rundown of the most common rods and what they’re best for:
1. 6010/6011 (Fast-Freeze Rods)
- Use: Deep penetration on dirty/rusted steel, pipelines, and farm equipment.
- Power: DC-only (6010) or AC/DC (6011).
- Tip: Demands skill—strikes hot and splatters heavily.
2. 6013 (All-Position Generalist)
- Use: Sheet metal, auto repair, and DIY projects.
- Power: AC/DC.
- Tip: Smooth arcs, easy for beginners; less penetration than 6010.
3. 7018 (Low-Hydrogen, High-Strength)
- Use: Structural steel, bridges, and pressure vessels.
- Power: AC/DC (best on DC+).
- Tip: Keep rods oven-dried to prevent hydrogen cracking.
4. 7024 (Jet Rod)
- Use: High-speed horizontal fillets on thick steel.
- Power: AC/DC.
- Tip: Thick flux layer allows heavy deposition—ideal for flat joints.
5. Nickel-Based Rods (e.g., ENi-CI)
- Use: Cast iron repair, machining tools.
- Power: AC/DC.
- Tip: Preheat cast iron to 500°F to avoid cracks.
Why It Matters
Understanding welding rod numbers makes it easier to choose the right one for your job. Whether you need deep penetration, easy handling, or strong, clean welds, the right rod gets the job done better and faster. Keep this guide handy for your next project!
Need more than just rods? Stock up on welding consumables to ensure your projects run smoothly. From essential supplies to specialty items, we’ve got you covered.
How To Choose the Right Welding Rod
Picking the right welding rod isn’t just about grabbing what’s on the shelf—it’s about understanding your project and its specific needs. Factors like metal type, weld appearance, strength, and welding position all play a role. Let’s break it down so you can make the best choice.
Key Considerations
Are you welding heavy-duty materials, or do you need a clean finish for a smaller repair? Each factor—from the type of metal to the welding position—plays a crucial role in determining the right rod for the job.
- Metal Type: The material you’re welding determines the rod you need. Different metals, like steel or aluminum, require specific rods for optimal results.
- Weld Appearance: Want a clean, smooth finish or something heavy-duty? The welding rod you choose affects how the final weld looks.
- Strength Requirements: If your weld needs to handle heavy loads, make sure the rod you select can deliver the necessary strength.
- Welding Position: Are you welding flat, vertical, or overhead? Some rods are better suited for specific positions.
Each of these factors ensures your project turns out just the way you want—strong, clean, and reliable.
Safety Tips for Handling Welding Rods
Welding rods are the heart of your project, but they need to be handled with care. Improper handling can lead to poor weld quality, damaged materials, or even personal injury.
Before you get started, make sure you’re following these safety precautions to keep yourself and your project safe.
- Keep your hands and rods dry to prevent contamination or electric shock.
- Always wear welding gloves to protect your hands during handling.
- Store rods in a dry, safe place to avoid damage or corrosion.
- Inspect each rod for defects before use—damaged rods can ruin weld quality and create safety hazards.
Don’t forget safety while working with welding rods. Keep your hands protected with our heat-resistant welding gloves. Designed for durability and comfort, they’re a must-have for any welder.
Taking proper safety precautions is just as important as choosing the right welding rod. Now that you know how to handle rods safely, let’s dive into understanding the welding rod number system to help you decode the numbers and choose with confidence.
Welding Rod Number System
Every welding rod has a cryptic code printed on it—like E6010 or E7018—but these aren’t random digits. They’re a cheat sheet telling you exactly how the rod performs. Here’s how to crack the code:
Example: E 60 1 0
(Breaking down "E6010")
-
First Letter: Electrode Type
- E = Electrode (the standard “stick” welding rod).
-
First Two Numbers: Tensile Strength
- 60 = 60,000 psi (pounds per square inch).
- Example: An E7018 rod = 70,000 psi (stronger than most steels).
-
Third Number: Welding Positions
- 1 = All positions (flat, horizontal, vertical, overhead).
- 2 = Flat + horizontal only (e.g., E7024 for production welding).
-
Fourth Number: Coating + Current Type
- 0 = Cellulose-sodium coating, DC+ only (great for deep penetration).
- 8 = Low-hydrogen iron powder, AC/DC+ (smooth, strong welds).
Common Rods Decoded
- E6010: Deep-penetration beast for dirty metal (DC+ only).
- E6013: Easy-going all-rounder (AC/DC, thin metals).
- E7018: The “strong & steady” choice for critical joints (AC/DC+).
Pro Tip: Rods ending in “8” (like 7018) are moisture-sensitive—store them in a rod oven!
Conclusion on Welding Rod Types
Selecting the right welding rod isn’t just about technical specs—it’s about understanding how each choice impacts the strength, appearance, and durability of your welds
Consider factors like metal type, tensile strength, and welding position to set yourself up for success. Pair that with safe handling practices, and you’ll ensure both quality results and a safer work environment.
As a recommendation, always keep a variety of commonly used rods like 6010, 6013, and 7018 on hand for versatility. Regularly inspect your welding rods and store them properly to avoid defects or contamination. When in doubt, refer to welding rod numbers and material compatibility to guide your decision-making.
If you’re ready to take your welding expertise further, understanding MIG wire sizes is the next step to mastering your craft.
heck out our guide on MIG wire sizes to learn more about choosing the right wire for your welding projects. Keep refining your skills and make every weld count!
Frequently Asked Questions on Welding Rod Types
What are the 5 common welding rods?
The five most common welding rods are 6010, 6011, 6013, 7018, and 7024. Each is designed for specific applications, such as deep penetration, versatility, or smooth finishes. These rods are widely used across various welding projects for their reliability and performance.
What is the best welding rod for everything?
There isn’t a single “best” rod for all projects, but the 7018 is often considered versatile due to its strength, smooth finish, and low-hydrogen properties. It works well on a wide range of metals and positions. However, always consider the specific requirements of your project before choosing.
What welding rod to use for mild steel?
For mild steel, the 6013 and 7018 rods are popular choices. The 6013 is great for thin metals and low-amp machines, while the 7018 offers high strength and a smooth finish. Both provide reliable welds for mild steel applications.
How do I know what welding rod to use?
To choose the right welding rod, consider the type of metal, welding position, and required strength or finish. The welding rod number provides key information, like tensile strength and current type. Matching the rod to your project ensures strong, quality welds.