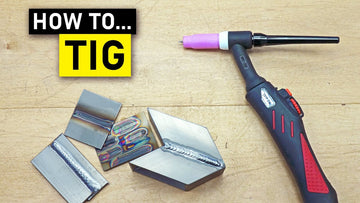
Introduction: Embarking on the journey of TIG welding can be both exciting and challenging. In this article, we'll delve into the essential basics that every novice welder should know to kickstart their TIG welding adventure. The primary focus will be on the use of an AC/DC TIG welder with a pulse function, emphasizing key steps and parameters for optimal results.
Choosing the Right Equipment: To commence your TIG welding journey, invest in an AC/DC TIG welder with a pulse function. This versatile tool will open up a world of possibilities for your welding projects. Ensure a seamless connection by linking your welder to a gas bottle, preferably filled with pure argon. A crucial detail is to incorporate a reducer valve between the gas bottle and the hose, guaranteeing an airtight connection to prevent any gas leaks that might compromise the weld quality.
Preparing the TIG Torch: A critical step in the preparation process is sharpening the tungsten electrode to a fine point. Assemble the TIG torch, ensuring that the tungsten slightly protrudes from the gas cup. Connect the torch to the negative terminal and the ground clamp to the positive terminal. Plug your welder into the electric grid, power it on, and set the gas flow between 8 to 10 liters per minute based on your gas cup size.
Understanding TIG Welding Modes: Before diving into the intricacies of TIG welding, grasp the basics of 2T and 4T modes. In 2T mode, the trigger must be held throughout the welding process, while in 4T mode, a single press initiates the arc, and another press concludes the weld. This fundamental knowledge sets the stage for further exploration.
Differentiating Between AC and DC TIG Welding: Discerning between direct current (DC) and alternating current (AC) TIG welding is crucial for successful welding projects. DC TIG welding, where electricity flows in one direction, is ideal for carbon steel and stainless steel welding. Conversely, AC TIG welding is essential for aluminum, as the alternating current aids in removing the oxide layer protecting the metal.
Exploring DC TIG Welding Functions: Delving into DC TIG welding, familiarize yourself with the key functions and parameters on your welder. The primary parameter is welding current, and for demonstration purposes, we'll set it to 150 amps. Understand pre-flow and post-flow, which determine the duration of argon gas flow before and after the welding arc, preventing oxidation of the tungsten electrode and the weld.
Mastering Up Slope and Down Slope: Up slope and down slope are crucial aspects of DC TIG welding. Up slope defines the duration it takes to transition from start current to main current, while down slope is the reverse. Setting these parameters ensures a smooth and controlled welding process. Practice is key to mastering these nuances.
Perfecting Your Weld: To create a flawless weld, clean the edges of both pieces, align them, and create tack welds. These tack welds secure the pieces together, allowing for welding in between. Maintain the proper torch angle, move in the direction of the filler wire, and master the art of TIG welding by practicing on a flat piece of steel with drawn lines.
Unlocking the Pulse Function: For thin sheet metal welding, the pulse function is invaluable in preventing burn-through. Adjust the pulse current, frequency, and duration to suit your material. Experiment with settings, starting with 90 amps, 1 Hertz, and 50% duration, and observe the impact on your welds. Fine-tune as needed for optimal results.
AC Welding on Aluminum: Transitioning to AC welding on aluminum introduces two additional parameters: AC frequency and AC balance. Higher AC frequency (150-250 Hz) is suitable for thin materials, providing a more accurate welding arc and faster travel speed. Lower AC frequency (80-120 Hz) is recommended for thicker materials. Strike a balance between the two for optimal welding performance.
Comparing AC Balance in Aluminum Welding: Finally, we explore the impact of AC balance on aluminum welding. Higher AC balance enhances surface cleaning but slightly erodes the tungsten electrode. Lower AC balance results in dirtier welds but preserves the electrode. A balance around 35% is commonly recommended for the best compromise.
Conclusion: Armed with these fundamental insights, you're well on your way to mastering TIG welding. Remember, practice and experimentation are key components of the learning process. As you progress, seek guidance from certified welding professionals to refine your skills further. Happy welding!