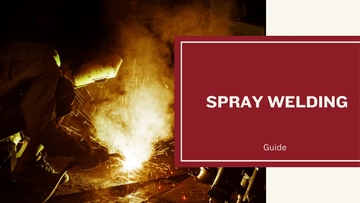
Spray welding is a welding process that involves spraying molten or semi-molten metal particles onto a surface to create a coating or build up a component. This process is commonly used in industries such as aerospace, automotive, and manufacturing, where the production of high-quality, durable components is essential.
The spray welding process involves the use of specialized equipment, including a spray gun and a power source, to heat and melt the metal particles. The molten metal is then sprayed onto the surface of the component, where it cools and solidifies to form a coating or build up the component. This process can be performed using a variety of metals, including aluminum, copper, nickel, and stainless steel, among others.
Spray welding offers a number of advantages over other welding processes, including the ability to create high-quality coatings with excellent adhesion and corrosion resistance. Additionally, the process can be used to repair worn or damaged components, extending their service life and reducing the need for costly replacements. With its versatility and numerous benefits, spray welding is a valuable tool for a wide range of industries and applications.
What is Spray Welding?
Spray welding is a type of thermal spray coating process that involves the deposition of a material onto a substrate using a spray gun. This process is commonly used in the repair and maintenance of machinery and equipment, as well as in the manufacturing of new components.
Types of Spray Welding
There are several types of spray welding techniques, including flame spray, arc spray, plasma spraying, cold spray, and HVOF (high-velocity oxy-fuel) spraying. Each technique has its own unique advantages and disadvantages, and the choice of technique will depend on the specific application.
Essential Spray Welding Equipment and Materials
Spray welding is a way to fix or make things using a special spray. Here's what you need and how it works, explained in easy words:
What You Need:
- Spray Gun: This is like a paint gun but for welding. It sprays hot material onto things.
- Heat Source: You need something hot, like a gas flame or electricity, to melt the material.
- Material to Spray: This can be wire, rod, or powder flame spray. You use this to coat or build up the thing you're fixing or making.
- What You're Spraying On (Substrate): This can be different stuff like metal, plastic, or even ceramics.
Other Stuff You Might Need:
- Masking Materials: These are like stencils or tape to cover parts you don’t want to spray.
- Cleaning Solutions: To clean the item before you spray weld it.
- Protective Coatings: To protect the spray-welded part or make it last longer.
Uses of Spray Welding:
Spray welding isn't just for one thing. You can use it to:
- Fix Stuff: Like repairing parts of machines that are worn out or broken.
- Make New Things: Creating parts with special features, like being really hard or not getting rusty.
Who Uses It?
It's super useful in many areas, like:
- Aerospace: For planes and spacecraft.
- Automotive: In cars and trucks.
- Manufacturing: Making all sorts of products.
So, spray welding is a cool, handy way to fix or make things, used in lots of different jobs. It's like giving an object a new skin or extra layer to make it better or to bring it back to life!
What is Thermal Spray Welding?
Thermal spray welding is a cool way to join materials using heat. Imagine a super-hot spray that can melt stuff. Here's how it works:
- Heat Source: It uses a heat source, kind of like a really intense flame, to melt materials.
- Spraying: This melted material is then sprayed onto a surface. It's like using a spray paint can, but with molten metal!
- Cooling Down: The molten material cools down and hardens on the surface. This creates a strong layer or coating.
Why use thermal spray welding? Well, it's great for:
- Fixing Things: It can repair worn-out parts, like in machines.
- Protection: It can make surfaces tougher and protect them from rust or wear.
- Special Coatings: It can add special properties to a surface, like making it resist heat or electricity.
In simple words, thermal spray welding is like giving a surface a new, strong, protective coat using a hot, melting spray. It's a clever way to make things last longer and work better!
Different Spray Welding Procedures
When it comes to spray welding, there are several different procedures to choose from, each with its own unique benefits and drawbacks. Here are some of the most common spray welding procedures:
Flame Spraying Process
Flame spraying is a spray process that uses heat from a flame to melt and atomize a feedstock material, which is then sprayed onto a surface to form a coating. The heat input and deposition rate can be controlled by adjusting the fuel gas (acetylene, propane, or propylene) and oxygen levels. Flame spraying is commonly used for bonding materials such as metals, ceramics, and plastics.
Arc Spraying Process
Arc spraying is a spray process that uses an electric arc to melt and atomize a feedstock material, which is then sprayed onto a surface to form a coating. The spray arc welding process uses DC power to create the arc. Arc spraying is commonly used for bonding materials such as metals and alloys.
Plasma Spraying Process
Plasma spraying is a spray process that uses a plasma arc to melt and atomize a feedstock material, which is then sprayed onto a surface to form a coating. The plasma spray uses a mixture of argon and hydrogen gases to create high temperatures. Plasma spraying is commonly used for bonding materials such as ceramics, metals, and plastics.
High-Velocity Oxyfuel Spraying
High-velocity oxyfuel (HVOF) spraying is a spray process that uses a mixture of oxygen and fuel gases to create a high-velocity flame that melts and atomizes a feedstock material. The high-velocity flame produces high deposition rates and low gas cost. HVOF spraying is commonly used for bonding materials such as metals and alloys.
Cold Spray Process
Cold spray is a spray process that uses a high-pressure gas (such as nitrogen or helium) to accelerate a feedstock material to high velocities, which causes the particles to bond to a surface. The cold spray process produces high deposition rates and can be used to bond materials such as metals and ceramics.
Overall, each spray welding procedure has its own unique advantages and disadvantages. By understanding the differences between these procedures, you can choose the one that best suits your needs for your specific application.
Benefits of Spray Welding
Spray welding is a welding technique that offers several benefits over other welding techniques. Here are some of the advantages of spray welding:
1. High-quality welds
Spray welding produces high-quality welds with minimal distortion and excellent metallurgical properties. This is because the process uses a fine spray of molten metal droplets that are deposited onto the workpiece, resulting in a uniform and controlled buildup of material.
2. Versatility
Spray welding can be used to repair or build up a wide variety of materials, including steel, aluminum, and other alloys. It is also suitable for repairing worn or damaged parts, such as shafts, gears, and bearings.
3. Efficiency
Spray welding is an efficient process that can save time and money. It produces less waste than other welding techniques, and the buildup of material is precise and controlled, reducing the need for additional machining.
4. Durability
Spray welding produces welds that are highly resistant to wear, corrosion, and other forms of damage. This makes it an ideal choice for applications that require high durability and longevity.
5. Reduced Heat Input
Spray welding produces less heat input compared to other welding techniques, reducing the risk of heat distortion and warping. This makes it an ideal choice for repairing delicate or complex parts.
In summary, spray welding offers several benefits over other welding techniques, including high-quality welds, versatility, efficiency, durability, and reduced heat input. These advantages make it an ideal choice for a wide range of applications, from repairing worn or damaged parts to building up new components.
Steps on How Does Spray Welding Work?
Spray welding is a process that involves the use of a spray gun to deposit molten metal onto a surface. This process is commonly used for repairing or building up worn or damaged parts. If you're new to spray welding, don't worry, this step-by-step guide will help you get started.
Step 1: Preparation
Before you begin spray welding, you need to properly prepare the surface you'll be working on. This involves cleaning the surface and removing any rust, paint, or other contaminants. You should also ensure that the surface is completely dry before beginning.
Step 2: Set up the Equipment
Next, you'll need to set up the spray welding equipment. This typically involves connecting the spray gun to the air and power supply. You'll also need to select the appropriate nozzle size and adjust the air pressure and power settings.
Step 3: Begin Spray Welding
Once your equipment is set up and the surface is prepared, you can begin spray welding. Hold the spray gun at a 90-degree angle to the surface and maintain a consistent distance of 6-8 inches. Move the spray gun back and forth across the surface, overlapping each pass slightly.
Step 4: Build Up the Weld
As you spray weld, you'll need to build up the weld by adding additional layers. Allow each layer to cool before adding the next. Continue building up the weld until it is the desired thickness.
Step 5: Finish the Weld
Once the weld is complete, you'll need to finish it by grinding or sanding the surface to smooth it out. You may also need to apply a protective coating to prevent corrosion.
Spray welding can be a challenging process, but with practice and patience, you can achieve great results. Remember to always follow safety procedures and wear appropriate protective gear when spray welding.
Safety Tips and Best Practices
Spray welding can be a hazardous process if proper safety measures are not taken. Here are some safety tips and best practices to follow during spray welding:
- Always wear appropriate personal protective equipment (PPE), including eye protection, gloves, and a respirator. Make sure that your PPE is properly fitted and in good condition.
- Ensure that your work area is well-ventilated to prevent the buildup of toxic fumes. If necessary, use exhaust fans or ventilation systems to remove fumes from the area.
- Before beginning the spray welding process, inspect your equipment and make sure that it is in good working condition. Replace any damaged or worn parts before starting.
- Follow all manufacturer's instructions and guidelines for the equipment and materials you are using. Do not exceed recommended settings or use equipment in ways that it was not designed for.
- Keep a fire extinguisher nearby and know how to use it in case of an emergency.
- Do not spray weld on surfaces that are painted, coated, or contaminated with grease or oil. These substances can create toxic fumes when heated.
- If you are not experienced with spray welding, it is recommended that you receive training from a qualified instructor before attempting the process on your own.
By following these safety tips and best practices, you can help ensure that your spray welding process is safe and successful.
Conclusion
In conclusion, spray welding is a reliable and efficient method for repairing and restoring damaged metal surfaces. By using a combination of heat and a powdered metal coating, spray welding can restore surfaces to their original condition without the need for costly replacements.
One of the most significant benefits of spray welding is its versatility. It can be used on a wide range of materials, including aluminum, stainless steel, and cast iron. Additionally, it is an excellent method for repairing complex shapes and surfaces that would be difficult to repair with traditional welding methods.
ArcCaptain is one of the leading providers of welding equipment and supplies. Their products are designed to provide high-quality results while being easy to use. Whether you are a professional welder or a DIY enthusiast, ArcCaptain has the right equipment for your needs.
By exploring the Shopify store, you can find a wide range of related products, including welding machines, metal powders, and accessories. Whether you need to repair a damaged part or restore an antique piece of machinery, ArcCaptain has everything you need to get the job done.
Overall, spray welding is a reliable and efficient method for repairing and restoring damaged metal surfaces. By using high-quality equipment and supplies from ArcCaptain, you can achieve professional results with ease.
Frequently Asked Questions
What is welding spray?
Welding spray, also known as spray welding or thermal spraying, is a process of applying a metal coating onto a surface using a high-velocity flame or arc. The metal is heated until it melts and is then propelled onto the surface to be coated. The result is a durable and corrosion-resistant coating that can protect the surface from wear and tear.
What are the disadvantages of spray welding?
Although spray welding has many advantages, it also has some disadvantages. One of the main disadvantages is that it can be expensive compared to other welding methods. Additionally, the process can produce high levels of heat and noise, which can be dangerous if proper safety precautions are not taken. It can also be difficult to achieve a uniform coating thickness, which can affect the overall quality of the coating.
What machine does spray welding use?
Spray welding uses a specialized machine called a thermal spray gun or spray torch. The gun or torch is connected to a power source and a supply of metal wire or powder. The metal is heated and melted in the gun or torch, and then sprayed onto the surface to be coated.
What voltage is needed for spray welding?
The voltage needed for spray welding can vary depending on the type of machine and the type of metal being used. Typically, a voltage of between 20 and 40 volts is needed for spray welding. However, it is important to consult the manufacturer's instructions and follow proper safety procedures when using any welding equipment.