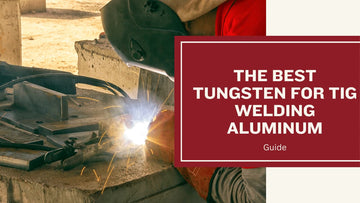
When it comes to TIG welding aluminum, selecting the right tungsten electrode is crucial for achieving optimal results. The tungsten electrode is responsible for conducting the electrical current that creates the arc necessary for welding. However, not all tungsten electrodes are created equal, and choosing the best one can make a significant difference in the quality of your welds.
To determine the best tungsten for TIG welding aluminum, several factors must be considered. These include the type of aluminum being welded, the thickness of the material, the amperage being used, and the type of shielding gas being used. Additionally, tungsten electrodes come in various sizes, shapes, and compositions, each with its own unique properties and benefits. By selecting the right tungsten for your specific application, you can achieve stronger, cleaner, and more precise welds.
Understanding TIG Welding and Aluminum
What is TIG Welding
Tungsten Inert Gas (TIG) welding is a popular welding technique that uses a non-consumable tungsten electrode to produce an electric arc. The arc is used to melt the metal and create a weld puddle that cools and solidifies to form a strong joint. TIG welding is known for its precision, cleanliness, and versatility, making it a popular choice for welding aluminum.
Characteristics of Aluminum
Aluminum is a lightweight and durable metal that is commonly used in various industries. However, it has unique characteristics that make it challenging to weld. Aluminum has a high thermal conductivity, which means it dissipates heat quickly. This makes it challenging to maintain a stable weld puddle, especially when using a high heat input. Additionally, aluminum forms an oxide layer when exposed to air, which can prevent proper fusion during welding.
Why Choosing the Right Tungsten is Important
Choosing the right tungsten is crucial when TIG welding aluminum. Tungsten is the electrode that creates the electric arc, and it must be able to withstand the high heat input required to weld aluminum. Pure tungsten is not ideal for welding aluminum because it has a low melting point and can easily contaminate the weld puddle. Instead, a tungsten alloy, such as 2% thoriated tungsten, is recommended. This type of tungsten has a higher melting point and better arc stability, making it ideal for welding aluminum.
In conclusion, understanding the basics of TIG welding and the characteristics of aluminum is crucial when welding aluminum. Choosing the right tungsten is also essential to ensure a strong and clean weld. By using the right techniques and equipment, you can produce high-quality welds on aluminum that are both strong and aesthetically pleasing.
Tungsten Electrodes Explained
Tungsten electrodes play a crucial role in TIG welding, as they are responsible for creating the electrical arc that melts and joins the aluminum pieces. Choosing the right tungsten electrode is crucial to achieve a high-quality weld. In this section, we will discuss the different types of tungsten electrodes and their properties.
Types of Tungsten Electrodes
There are different types of tungsten electrodes available in the market, including pure tungsten, thoriated, ceriated, and lanthanated. Each type has its unique properties that make it suitable for specific welding applications.
-
Pure Tungsten: This type of tungsten electrode is made of 100% tungsten and is suitable for welding aluminum alloys with a low electrical conductivity. It is not recommended for high amperage welding applications as it has a low current carrying capacity.
-
Thoriated Tungsten: Thoriated tungsten electrodes contain a small amount of thorium oxide, which makes them suitable for welding aluminum alloys with a higher electrical conductivity. They have a high current carrying capacity and are ideal for high amperage welding applications. However, thorium is a radioactive material, and the use of thoriated tungsten electrodes is regulated in some countries.
-
Ceriated Tungsten: Ceriated tungsten electrodes contain a small amount of cerium oxide, which makes them suitable for welding aluminum alloys with a higher electrical conductivity. They have a high current carrying capacity, similar to thoriated tungsten electrodes, but without the radioactive hazard. Ceriated tungsten electrodes are ideal for high amperage welding applications.
-
Lanthanated Tungsten: Lanthanated tungsten electrodes contain a small amount of lanthanum oxide, which makes them suitable for welding aluminum alloys with a higher electrical conductivity. They have a high current carrying capacity and are ideal for high amperage welding applications. Lanthanated tungsten electrodes are also non-radioactive, making them a safer alternative to thoriated tungsten electrodes.
Role of Tungsten in TIG Welding
Tungsten electrodes are classified based on their properties and the American Welding Society (AWS) classification. The AWS classification system is based on the tungsten electrode's composition, color code, and the type of welding application it is suitable for.
In TIG welding, the tungsten electrode is responsible for creating the electrical arc that melts and joins the aluminum pieces. The electrode must be sharpened to a specific point to create a stable arc and prevent contamination of the weld. The type of tungsten electrode used will depend on the aluminum alloy being welded, the amperage, and the welding application.
In conclusion, choosing the right tungsten electrode is crucial to achieve a high-quality weld. Understanding the properties and advantages of each type of tungsten electrode will help you select the right one for your welding application.
Selecting the Right Tungsten for Aluminum
When it comes to TIG welding aluminum, selecting the right tungsten is crucial for achieving high-quality welds. The tungsten electrode is the main heat source in TIG welding, and it needs to be able to withstand the high temperatures and electrical currents involved in the process. Here are two popular tungsten options for TIG welding aluminum:
Lanthanated Tungsten for Aluminum
Lanthanated tungsten is a popular choice for TIG welding aluminum due to its ability to maintain a stable arc and resist contamination. It is also known for its long lifespan, making it a cost-effective option in the long run. Lanthanated tungsten is ideal for AC TIG welding, which is commonly used for welding aluminum. It is available in various diameters, and its color-coded tip makes it easy to identify.
Zirconiated Tungsten for Aluminum
Zirconiated tungsten is another popular option for TIG welding aluminum. It is known for its ability to maintain a sharp and stable arc, making it ideal for precision welding. Zirconiated tungsten is also resistant to contamination, which helps to ensure high-quality welds. It is available in various diameters and is suitable for both AC and DC TIG welding.
When selecting the right tungsten for TIG welding aluminum, it is important to consider the type of welding you will be doing, the thickness of the aluminum, and the amperage you will be using. Lanthanated tungsten is a reliable option for general-purpose welding, while zirconiated tungsten is ideal for precision welding. Whichever option you choose, make sure to follow the manufacturer's recommendations for use and storage to ensure optimal performance.
The Best Tungsten for TIG Welding Aluminum
The best tungsten for TIG welding aluminum is one that can handle the high heat generated during the process while maintaining a stable arc.
Choosing the best running shoes for a marathon. You need something that can handle the heat and keep things steady.
The go-to choice is often pure tungsten. It's like the strong, heat-resistant athlete of the welding world, able to withstand temperatures up to 3422°C. But, just like a strong athlete might be a bit tricky to coach, pure tungsten can be tough to work with. Sometimes, it can even mix into your weld, which isn't great.
There's another team of players, though: tungsten alloys. Think of these as the versatile, all-round players. Alloys like ceriated tungsten or thoriated tungsten don't just handle heat better than pure tungsten, they also pass it along more efficiently. This means they're easier to use and less likely to mess up your weld.
When choosing your tungsten superhero, think about the aluminum you're welding. Is it thin? Go for a thinner tungsten. Is it thick? You'll need a thicker one. And don't forget about your welding machine – it's part of the team, too!
Overall, the best tungsten for TIG welding aluminum is one that can handle the heat generated during the process while maintaining a stable arc and minimizing the risk of contamination. By selecting the right tungsten for your specific welding needs, you can achieve high-quality welds with ease.
Tungsten Electrode Preparation and Maintenance
Sharpening Tungsten Electrodes
To achieve the best results when welding aluminum with TIG, it is essential to have a sharp tungsten electrode. A sharp edge on the electrode will help to direct the arc to the desired location and produce a clean and precise weld.
To sharpen the tungsten electrode, you can use a dedicated tungsten sharpener or a bench grinder. When using a bench grinder, it is important to ensure that the electrode is cooled regularly to prevent overheating.
When sharpening, it is recommended to grind the tungsten electrode at a 20 to 30-degree angle. The angle will depend on the type of welding and the thickness of the aluminum. A smaller angle is suitable for thinner aluminum, while a larger angle is better for thicker aluminum.
Maintaining Electrode Quality
To ensure the tungsten electrode lasts as long as possible, it is important to maintain its quality. One way to do this is to avoid touching the electrode with bare hands. The oil and dirt on your hands can contaminate the electrode and reduce its lifespan.
Another way to maintain the quality of the electrode is to store it in a dry and clean place. Moisture and dirt can also contaminate the electrode and affect its performance.
Finally, it is important to inspect the electrode regularly for signs of wear and tear. A damaged electrode can affect the quality of the weld and may need to be replaced.
In summary, preparing and maintaining the tungsten electrode is crucial to achieving high-quality TIG welds on aluminum. By sharpening the electrode correctly and taking care of its quality, you can ensure that it lasts longer and produces the best results.
Why Tungsten Choice Matters for Aluminum
Welding aluminum can be tricky. Why? Because aluminum heats up quickly and melts easily. This makes it tough to get just the right welding settings for a strong, steady weld. But, the good news is, using the right kind of tungsten can really help in TIG welding aluminum.
When welding aluminum, don't go for pure tungsten. It's not the best choice because it melts too easily. This can cause problems, like the tungsten mixing into your weld. Instead, tungsten alloys are the way to go. These are special mixes of tungsten, like 2% thoriated tungsten, 1.5% lanthanated tungsten, or zirconiated tungsten. They have a higher melting point and carry heat better. This means a more stable welding arc and better heat control on your aluminum piece.
The size of the tungsten matters too. If you're welding thin aluminum sheets, a thinner tungsten electrode is better. It gives a more focused arc and lets you manage the heat more precisely. But if you're working with thicker aluminum, a bigger tungsten electrode is your friend. It can handle more power and gives a broader arc, great for thicker pieces.
In short, picking the right tungsten – both the type and size – is a big deal in aluminum TIG welding. The right choice can really improve your welds, making them strong and reliable, even on this tricky metal.
Factors to Consider When Choosing Tungsten for Aluminum
When it comes to TIG welding aluminum, selecting the right tungsten electrode is crucial for achieving high-quality welds. Here are some factors you should consider when choosing tungsten for aluminum welding:
1. Electrode Size
The diameter of the tungsten electrode you use will depend on the thickness of the aluminum you are welding. A general rule of thumb is to use an electrode that is equal to or slightly smaller than the thickness of the material you are welding. Using too large of an electrode can cause excessive heat buildup, leading to warping or burn-through.
2. Electrode Shape
There are different electrode shapes to choose from, including pointed, truncated, and rounded. Pointed electrodes are ideal for welding thin aluminum, while truncated or flat electrodes are better suited for thicker materials. Rounded electrodes are a good choice for welding joints with tight angles.
3. Electrode Material
Tungsten electrodes can be made from different materials, including pure tungsten, thoriated tungsten, lanthanated tungsten, and ceriated tungsten. Each material has its own unique properties that can affect the quality of your weld. Pure tungsten is suitable for welding aluminum, while thoriated tungsten is ideal for welding steel. Lanthanated and ceriated tungsten are versatile and can be used for welding various materials.
Choosing the right tungsten electrode size, shape, and material is essential for achieving high-quality welds when TIG welding aluminum. By taking these factors into consideration, you can ensure that your welds are strong, durable, and visually appealing.
Welding Equipment for Aluminum
When it comes to TIG welding aluminum, having the right equipment is crucial. Here are some of the best welding equipment for aluminum and their descriptions:
-
TIG Welding Machine: A TIG welding machine is required for TIG welding aluminum. It should have a high-frequency start and a pulsing feature to ensure a clean and precise weld.
-
Tungsten Electrodes: Tungsten is the most commonly used electrode for TIG welding aluminum. It is available in various diameters and lengths. You should choose a tungsten electrode with a pointed tip for better arc stability.
-
Filler Rods: Filler rods are used to add material to the weld joint. For welding aluminum, you should use filler rods made from the same material as the base metal.
-
Gas Lens: A gas lens helps to distribute shielding gas evenly around the weld joint. This is important for welding aluminum as it is more prone to contamination.
-
Gas Flowmeter: A gas flowmeter is used to regulate the flow of shielding gas. It should be set to the recommended flow rate for the specific welding application.
-
Welding Helmet: A welding helmet is necessary to protect your eyes and face from the intense light and heat produced during welding. It should have a clear lens to provide a clear view of the weld joint.
-
Welding Gloves: Welding gloves protect your hands from the heat and sparks produced during welding. They should be made from heat-resistant materials such as leather.
-
Welding Apron: A welding apron protects your clothing from sparks and debris produced during welding. It should be made from flame-resistant materials.
By using the right welding equipment for aluminum, you can ensure a clean and precise weld. Make sure to choose equipment that is appropriate for the specific welding application.
Conclusion
After reviewing the various tungsten options for TIG welding aluminum, you should have a clear understanding of which tungsten is best suited for your welding needs.
If you are looking for a tungsten that provides excellent arc stability and works well with AC welding, then the 2% thoriated tungsten might be the best option for you. However, if you are looking for a tungsten that can withstand high temperatures and is great for welding thin aluminum, then the 2% ceriated tungsten might be the better choice.
It is important to note that each tungsten option has its own unique advantages and disadvantages. Therefore, it is essential to consider your specific welding needs before making a final decision.
No matter which tungsten you choose, always make sure to follow proper safety precautions and use appropriate welding techniques to achieve the best results.
Frequently Asked Questions
What is the best tungsten for aluminum TIG welding?
The best tungsten for aluminum TIG (Tungsten Inert Gas) welding is typically a Green Tip (Pure Tungsten) or a Blue Tip (2% Lanthanated). Pure tungsten, represented by a green-colored tip, was traditionally used for aluminum welding due to its ease of forming a balled tip which is beneficial in TIG welding aluminum. However, 2% Lanthanated tungsten (blue tip) is also a popular choice as it offers a good balance between longevity and ease of use and can be used for both AC (alternating current) and DC (direct current) processes.
What color tungsten to use for aluminum?
For aluminum welding, you should use a Green Tip (Pure Tungsten) or a Blue Tip (2% Lanthanated). The green tip is the traditional choice for aluminum due to its suitability for AC welding, which is commonly used for aluminum. The blue tip is a more modern choice that also works well and can be easier to find.
Which type of tungsten is not recommended for welding?
Thoriated tungsten (Red Tip) is generally not recommended, especially for aluminum TIG welding. While thoriated tungsten is effective in DC applications for materials like steel or stainless steel, it's not ideal for AC processes used in aluminum welding. Moreover, thoriated tungsten contains Thorium, a radioactive element, which poses health and environmental concerns.
What tungsten tip for aluminum welding?
The tungsten tip for aluminum welding should ideally be a balled tip. When using a green tip (pure tungsten) for AC welding aluminum, the tip naturally forms into a ball when heated. This balled tip provides a more stable arc and better heat control, which is important for the softer and more sensitive nature of aluminum.