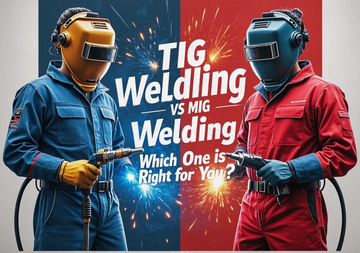
MIG and TIG welding are common types of welding. They both use an electric arc and a shielding gas. However, the two processes differ in several ways, including the welding electrodes used to create the arc. MIG uses a solid wire that is machine-fed to the weld area, while TIG uses a non-consumable electrode and a hand-held filler rod to form the weld.
MIG Process:
Metal Inert Gas (MIG) welding, or Gas Metal Arc Welding (GMAW), uses a semi-automatic or automatic arc with a consumable wire electrode and shielding gas, typically 75% argon and 25% CO2.
The welding gun feeds both the electrode and gas, with the electrode's composition and diameter varying by metal type and thickness. The wire feed speed (WFS) controls the electrode's feed rate to ensure sufficient weld material.
TIG Process:
Tungsten Inert Gas (TIG) welding, or Gas Tungsten Arc Welding (GTAW), uses a non-consumable tungsten electrode and a separate consumable filler rod manually added to the weld pool. This process requires both hands—one for the electrode and one for the filler.
TIG welding typically uses 100% argon as a shielding gas to avoid tungsten oxide contamination. It also features a foot pedal to control amperage and heat for precise adjustments during welding.
Advantages and Disadvantages
MIG Advantages and Disadvantages
MIG (Metal Inert Gas) welding is ideal for joining large, thick materials using a consumable wire that serves as both the electrode and filler. It is faster and easier to learn than TIG welding, resulting in shorter production times and lower costs, with welds that often require minimal cleaning. However, MIG welds are generally less precise, strong, and aesthetically pleasing compared to those made by skilled TIG welders.
TIG Advantages and Disadvantages
TIG (Tungsten Inert Gas) welding is a versatile method for joining small and thin materials, using a non-consumable tungsten electrode and an optional filler rod.
While TIG welding is slower and more challenging to learn than MIG welding, leading to higher production costs, it offers greater control. As a result, TIG welds are stronger, more precise, and more aesthetically pleasing than those made with MIG.
MIG vs TIG Comparison Table
Benefit | MIG | TIG |
Welding Speed |
√ |
X |
Welding Costs |
√ |
X |
Ease of Welding |
√ |
X |
Strength of Welds |
X |
√ |
Weld Precision |
X |
√ |
Weld Aesthetics |
X |
√ |
Thick Materials |
√ |
X |
Thin Materials |
X |
√ |
Applications
TIG Applications: TIG welding is harder to learn but provides greater precision than MIG welding. It excels at joining thinner materials and can weld aluminum, copper, steel, titanium, and more. Consequently, TIG is widely used in precision-required fields such as aerospace, motorsport, industrial structures, and production line manufacturing.
The Key Difference Between MIG and TIG Welding
MIG and TIG welding have key differences. MIG is easier to learn, faster, and better for thick materials. In contrast, TIG provides greater control and precision, making it ideal for thinner materials and producing cleaner welds.
Beyond these basics, distinctions can be categorized by properties, cost, and learning curve.
1. Weld Strength
TIG welds are generally stronger than MIG welds due to the narrow, focused arc that allows for better metal penetration and fewer defects. However, MIG can also produce strong welds by creating a V-shaped groove in the joint before welding and maintaining good travel speed and torch positioning to enhance penetration
2. Weld Speed
MIG welders operate faster in production because they automatically feed filler material and have a broader arc that dissipates heat, allowing for quicker movement. TIG welders are slower due to limited puddle movement and filler supply. Their air-cooled torches can overheat, necessitating cooling or costly water-cooled alternatives.
3. Shielding Gas
MIG and TIG welding use shielding gas to protect welds from reactive air gases. TIG typically uses pure argon, while MIG often uses a 75/25 argon-CO2 blend for better stability and penetration. TIG can also use argon with helium or nitrogen, and MIG can use 100% argon for aluminum or pure CO2 for cost savings. MIG has a higher gas flow rate (35-50 cubic feet per hour) than TIG (15-25 cubic feet per hour).
4. Weld Aesthetics
TIG welds offer better aesthetics than MIG welds, producing minimal spatter and requiring only light polishing. TIG "coin" stacks are especially attractive on unpainted surfaces. MIG welds, while often less visually appealing, are acceptable for applications where appearance is less important or when covered by coatings.
5. Process Difficulty
MIG welding is easier to learn than TIG due to its simpler operation. TIG requires two hands and a foot pedal for amperage control, while MIG uses an automatic filler feed, allowing welders to work with one hand.
6. Cost
TIG welding costs more per foot than MIG due to lower deposition rates, the need for more skilled welders, and greater preparation requirements. Additionally, MIG supplies and equipment are generally cheaper. These factors contribute to the higher cost of TIG welding.
Arccaptain is a leading manufacturer of high-quality welding and cutting machines, offering a wide range of exceptional equipment.
For MIG welding, we provide two excellent options:
· MIG200
For TIG welding, the TIG200P AC/DC stands out as the premier choice!
Explore our machines to find the perfect fit for your welding needs!