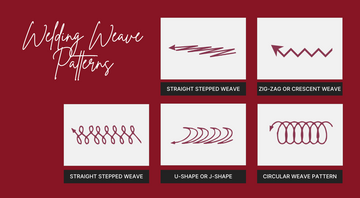
Welding weave patterns are important for making strong and good-looking welds.
They involve moving the welding torch in a certain way to shape the weld bead.
These patterns are commonly used in welding methods like TIG and MIG to help control the weld pool, making sure heat spreads evenly and the weld penetrates well.
Learning about weave patterns can help both beginners and experienced welders improve their skills and take on tougher projects.
But how do you know which weaving technique to use and when? Let’s dive into the different types of weaving and when to apply them!
What Are Welding Weave Patterns?
Welding weave patterns involve the movement of the welding torch or rod in side-to-side motions, creating wider welds by distributing the heat evenly across the joint.
This method allows for better control and filling of gaps in welding, resulting in a stronger and more uniform weld.
Stringer vs. Weave Beads
Stringer Beads:
- A stringer bead involves a straight-line motion along the weld seam.
- It requires less heat input and is useful for tasks demanding higher penetration or when working with thinner materials.
- Stringer beads are often preferred when precision and focused heat are necessary to prevent distortion.
Weave Beads:
- Weave beads cover a broader area with a side-to-side motion.
- They offer improved heat distribution, making them suitable for thicker materials that require more heat to penetrate.
Benefits of Weave Patterns:
- Better Control: Provides enhanced control over the weld pool and heat input.
- Wider Coverage: Allows for filling gaps in joints more effectively, creating wider, more stable welds.
- Heat Management: Ensures uniform heat distribution to prevent overheating and defects.
Understanding these differences helps welders choose the right technique for their specific needs, ensuring optimal performance and the best results for the materials they are working with.
Common Types of Welding Weave Patterns
Welding weave patterns help control the movement of the welding electrode, creating strong, smooth welds. Here are some common patterns and when to use them.
1. Straight Stepped Weave
The straight weave pattern is basic and often used when a clean and straightforward weld is needed. This pattern is ideal for thin materials or when working with steel, aluminum, or stainless steel.
✅ Best for: Vertical welding, and horizontal fillet welds.
🔧 How to do it: Move the electrode evenly from side to side across the weld area.
👍 Pros:
- Helps control penetration (how deep the weld goes).
- Prevents undercut (a groove along the edges of the weld that weakens it).
2. Zig-Zag or Crescent Weave
The zig-zag or crescent weave pattern involves a back-and-forth movement that helps fill wider joints effectively.
This pattern is particularly beneficial for vertical and horizontal welds where a large gap needs to be bridged.
By moving in a crescent shape, the welder ensures a large amount of filler material is deposited. This method provides excellent gap coverage and stability.
✅ Best for: Structural welding, horizontal & vertical-up welding.
🔧 How to do it: Move the electrode in a sharp, side-to-side zigzag motion.
👍 Pros:
- Controls bead width (how wide the weld is).
- Helps reinforce the weld for extra strength.
3. U-Shape or J-Shape Weave
The U-shape or J-shape weave pattern is known for its deep penetration, making it suitable for thicker materials.
This pattern is often used in pipe welding and structural welding where strong, robust joints are necessary.
This helps in reducing the risk of weak spots and ensures structural integrity. It’s frequently employed in high-pressure applications that demand tight and leak-proof joints.
✅ Best for: Vertical-up welding, groove welds, pipe welding.
🔧 How to do it: Move the electrode in a U or J shape, slightly pausing at the sides to ensure good fusion.
👍 Pros:
- Helps control the weld puddle, reducing drips in vertical welding.
- Ensures strong fusion at the edges, preventing weak spots.
- Provides good penetration without too much heat buildup.
4. Figure-Eight Weave Pattern
The figure-eight weave is complex yet highly effective for advanced welding projects. It is used when precision and strength are critical, such as in aerospace, automotive, or intricate fabrications.
This technique involves moving in a continuous figure-eight motion, which requires skill and practice to master.
✅ Best for: Thick plates, large fillet welds.
🔧 How to do it: Move the electrode in a figure-eight shape to evenly spread the heat.
👍 Pros:
- Prevents excess metal buildup.
- Reduces slag entrapment (when non-metal material gets trapped in the weld).
5. Circular Weave Pattern (Oscillation Weave)
✅ Best for: Overhead welding, flat positions.
🔧 How to do it: Move the electrode in small circles while moving forward.
👍 Pros:
- Creates smooth, even welds.
- Produces less spatter (small molten metal drops that fly off during welding).
Each weave pattern has a specific use, so choosing the right one depends on the welding position and material. Practicing different patterns will help you become a better welder
When is It Necessary to Use Weaving in Welding?
Weaving is essential for welding large or thick materials. It helps control the heat and secures the metal parts effectively.
For wide joints or large gaps, using a zigzag weave is beneficial. This technique allows for more filler material, which is vital to maintain consistent heat and bridge gaps successfully.
Photo Source: https://www.youtube.com/watch?v=rYebtimCTG8
In some areas, such as shipyards, weaving might not be allowed for critical joints due to specific safety standards. It's important to follow these guidelines and choose the correct method based on the situation.
Always consult the welding procedures or guidelines for the project to determine when weaving is appropriate.
Choosing the Right Welding Weave Pattern for Your Project
Material Type
- Steel: Supports most weave patterns, making it versatile.
- Stainless Steel: Prefers a controlled heat input with a zig-zag weave.
- Aluminum: Best with stringer beads, but a circular weave can work.
Welding Position
- Flat: Zig-zag and circular weaves ensure even coverage.
- Vertical-Up: Crescent or side-to-side weaves help with upward motion.
- Overhead: Circular or figure-8 patterns offer better control.
Welding Method
- MIG Welding: Often uses weave patterns for wider weld beads.
- TIG Welding: More precise, suits narrower weaves.
- Stick Welding: Common with various patterns for different joint types.
Material Thickness and Joint Type
- Thickness: Thick materials require patterns for higher penetration. Thin materials benefit from narrower weaves to prevent burn-through.
-
Joint Type:
- Butt Joints: Typically use a straight or zig-zag weave.
- Lap Joints: Employ a crescent or side-to-side pattern.
- Corner Joints: Often use figure-8 or circular weaves.
Heat Input Considerations
Too much heat can cause excessive penetration and warping, while too little results in poor fusion. It's crucial to match the weave width to not exceed 2.5 times the electrode diameter to balance the heat input effectively.
Common Mistakes & How to Improve Welding Weave Patterns
❌ Overlapping & Excessive Reinforcement: This occurs when weld beads overlap too much or are excessively built up. It's important to maintain a consistent side-to-side motion. Avoid pausing too long at the edges.
❌ Undercutting Along the Weld Edges: Undercutting happens when there is a groove at the weld edges. To fix this, reduce your travel speed and avoid weaving too quickly to ensure proper coverage.
❌ Weave Pattern Produces Excess Spatter: Excessive spatter can be caused by incorrect voltage settings. Adjust the voltage and ensure proper shielding gas flow to minimize spatter effectively.
❌ Lack of Penetration or Fusion: Insufficient penetration can weaken the weld. It can be improved by increasing heat input and slowing down the travel speed slightly.
Tips for Improvement
- Consistent Technique: Practice consistent motion to avoid irregularities.
- Equipment Settings: Regularly check equipment settings for voltage and gas flow.
- Material Preparation: Ensure the materials are clean and properly prepared to avoid contamination.
Implementing these suggestions can help enhance weld quality and reduce common mistakes in weave patterns.
Safety Tips for Using Welding Weave Patterns
Controlling heat input is crucial to prevent material warping during welding. Minimize overheating by using controlled weave motions. This helps maintain structural integrity and improves the quality of the weld.
Proper protective equipment is essential when welding. An auto-darkening welding helmet protects against the intense arc light that can damage vision. Heat-resistant gloves safeguard hands from high temperatures.
It is important to avoid fume exposure to ensure a safe working environment. Using fume extractors or welding in well-ventilated spaces can significantly reduce the risk of inhaling harmful fumes.
In confined areas, wearing a respirator provides additional protection.
Implementing these safety measures can greatly enhance both the safety and effectiveness of using welding weave patterns.
Check out Related Products 🔥
14 Inch Goatskin Tig Welding Gloves
Arccaptain Goat leather Tig Welding Gloves provide superior protection and grip compared to other types of welding gloves. They are made from highly durable and heat-resistant material, making them ideal for a variety of welding tasks.
|
|
Arccaptain MIG200 Multi Process MIG Welder Novice/Professional Friendly Welder
The MIG200 is ARCCAPTAIN's best-selling multi-process All in 1 MIG Welder. Whether you're a beginner or a professional welder, this machine meets all your welding project needs.
|
|
Arccaptain TIG200P AC DC Multi Process Pulse TIG Aluminum Welder
The AC DC TIG200P is our most powerful, best-selling, and top-rated high-performance Pulse Aluminum TIG Welder, highly recognized for its exceptional performance in aluminum welding and thin plate welding projects.
|
Frequently Asked Questions
Welding weave patterns can affect strength, width, and technique. Understanding these aspects is vital for choosing the right method and tools for different welding tasks.
What is the strongest weave welding method?
The strongest weave welding method is often considered to be the "zigzag" or "weave" pattern. This method ensures thorough fusion between the weld metal and the base metal, providing a strong and durable joint. The weave pattern helps distribute heat evenly, reducing the risk of defects.
How wide can you weave a weld?
The width of a weave weld typically ranges from 2 to 3 times the diameter of the electrode or filler rod. Going wider can lead to issues like excessive heat input, which can weaken the weld. It's important to follow guidelines to ensure a strong and stable weld.
What is the difference between stringer and weave beads?
Stringer beads are straight and narrow, applied by moving the electrode or torch in a straight line. Weave beads, on the other hand, involve a side-to-side motion, creating a wider weld. Stringer beads are often used for deeper penetration, while weave beads are used for covering larger areas and improving weld appearance.
Is Weaving Necessary for All Welds?
Weaving is not necessary for all welds. It depends on the specific requirements of the welding job. For instance, stringer beads may be more suitable for deep penetration, while weaving is useful for filling wider gaps and ensuring better coverage.
What Is the Best Welding Machine for Weave Patterns?
The best welding machine for weave patterns is typically a MIG or TIG welder. These machines offer precise control over the welding process, making it easier to perform consistent weave patterns. Look for machines with adjustable settings to fine-tune the weld.
Why should a weaving motion be used when making horizontal welds?
A weaving motion should be used when making horizontal welds to ensure even heat distribution and better control of the molten pool. This helps prevent sagging and improves the overall strength and appearance of the weld. It also allows for better fusion between the weld metal and the base metal.