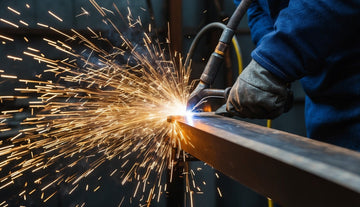
Deposition rate in welding measures how quickly metal is added to your weld joint, typically expressed in kg/hr or lb/hr. This critical metric directly impacts both productivity and weld quality. By optimizing deposition rate, you can significantly reduce project time and costs while maintaining structural integrity.
Multiple factors affect deposition rate—electrode type and size, current settings, and most importantly, your chosen welding process. While stick welding might deposit only 2-4 kg/hr, submerged arc welding can exceed 20 kg/hr under optimal conditions.
Want to maximize your welding efficiency? Read on to master deposition rate optimization techniques.
Welding Deposition Rate Basics

Deposition rate is one of the most important factors in welding efficiency. It affects how quickly you can complete projects and how much material you use.
What Deposition Rate Means In Welding
Deposition rate in welding is the amount of filler material that gets deposited onto the welded surface in a specific time period. Think of it as how fast you're adding metal to your weld joint.
It's usually measured in pounds or kilograms per hour.
Different welding processes have very different deposition rates. TIG welding has a lower deposition rate because you feed the rod slowly by hand. MIG and flux-cored welding deposit material much faster.
Your welding machine settings greatly affect this rate.
Higher amperage usually means a higher deposition rate. But be careful - going too fast can hurt weld quality.
How Deposition Rate Impacts Productivity
Deposition rate directly affects how quickly you can finish welding jobs. A higher rate means you can complete more work in less time.
When planning projects, knowing your deposition rate helps you estimate:
- How long jobs will take
- How much filler material you'll need
- Labor costs for the project
But there's always a trade-off. Higher deposition rates may lead to quality issues like poor penetration or increased spatter. Finding the right balance is key.
For large industrial projects, even small improvements in deposition rate can save thousands of dollars in labor and materials.
Standard Units For Measuring Weld Deposition
Weld deposition rate (WDR) is typically measured in these units:
- Pounds per hour (lbs/hr) - common in the US
- Kilograms per hour (kg/hr) - used internationally
The calculation for deposition rate is:
Deposition Rate = Wire Feed Speed × Wire Cross-sectional Area × Density × Efficiency
Your actual deposition efficiency is always less than 100%. Some material is lost to spatter and stub ends. Most processes have efficiency between 60-98%.
To measure real-world deposition rates, you can weigh completed welds and divide by the arc time. This gives you a practical measure for your specific setup and technique.
Key Factors That Affect Deposition Rate
Several elements impact how quickly you can deposit weld material. Understanding these factors helps you optimize your welding process for better efficiency and quality.
Wire Feed Speed And Diameter
Wire feed speed directly affects how much filler metal reaches your weld pool. Faster speeds mean more material deposited per hour.
For example, increasing from 200 to 300 inches per minute can boost deposition rates by 50%.
Wire diameter plays a crucial role too. Thicker wires deposit more material than thinner ones at the same feed speed.
Common Wire Diameters and Typical Deposition Rates:
- 0.030" (0.8mm): 2-5 lbs/hr
- 0.035" (0.9mm): 3-7 lbs/hr
- 0.045" (1.2mm): 5-10 lbs/hr
- 1/16" (1.6mm): 8-15 lbs/hr
You need to balance wire size with your welding requirements.
Thicker wires need more power but increase deposition rates. Thinner wires offer better control for detailed work but deposit material more slowly.
Current And Voltage Settings
Your amperage setting directly impacts deposition rate. Higher current means more wire melts faster, increasing deposition.
The relationship isn't perfectly linear though. Doubling current doesn't exactly double deposition rate due to efficiency factors.
Voltage affects how the arc transfers metal and the weld bead's shape. Higher voltage creates a wider, flatter bead with potentially more spatter.
Finding the sweet spot between current and voltage is key.
Too much of either can cause problems like:
- Excessive spatter
- Poor fusion
- Increased heat input
- Burnthrough on thin materials
A good starting point is following manufacturer recommendations for your specific wire type and diameter. Then make small adjustments to optimize for your specific project.
Electrode Type And Efficiency
Different electrodes have varying deposition efficiencies. This measures how much of the electrode actually becomes part of the weld.
Solid wires typically have 95-98% efficiency. This means almost all of what you feed becomes weld metal.
Flux-cored wires have lower efficiencies, usually 80-90%. The flux converts to slag rather than becoming part of the weld.
Metal-cored wires offer a good balance with 90-95% efficiency while still providing benefits like better penetration.
Your electrode choice should match your project needs:
- GMAW (MIG): Good efficiency, clean welds
- FCAW: Lower efficiency but better for outdoor work
- SMAW (Stick): Lowest efficiency (60-70%) but very portable
High-efficiency electrodes might cost more upfront but save money through reduced waste and faster completion times.
Shielding Gas Selection
Your shielding gas choice affects both weld quality and deposition rate.
Pure argon creates a narrower penetration profile while adding CO2 increases penetration and heat.
For MIG welding on steel, a mix of 75% argon and 25% CO2 offers good balance between deposition rate and spatter control.
Higher CO2 percentages (over 25%) can increase deposition rates but also increase spatter. Pure CO2 maximizes penetration and deposition but produces the most spatter.
For aluminum, pure argon is standard. Adding helium increases heat input and can boost deposition rates by 20-30%.
Gas flow rate matters too.
Too low and you get contamination; too high and you waste gas and might cause turbulence in the weld pool.
Duty Cycle And Operating Factor
Duty cycle refers to how long you can weld continuously before your equipment needs to cool down. A higher duty cycle means more arc-on time and greater overall deposition.
Operating factor is the percentage of time you're actually welding versus setup, cleaning, changing positions, etc. Most welders achieve 25-40% operating factors in real-world conditions.
To maximize deposition efficiency:
- Reduce repositioning time
- Plan your welds to minimize starts and stops
- Use fixtures to hold work pieces
- Keep your work area organized
Even the best welder with 100% duty cycle equipment rarely achieves more than 60% operating factor due to necessary non-welding tasks.
Investing in ergonomic equipment and proper planning can significantly increase your actual deposition rates by boosting your operating factor, even without changing any welding parameters.
Deposition Rates By Welding Process

Different welding processes offer varying deposition rates that impact productivity and project timelines. The deposition rate directly affects how quickly you can complete welding tasks and influences overall costs.
MIG/GMAW Deposition Rate Capabilities
MIG welding (Metal Inert Gas) or GMAW (Gas Metal Arc Welding) offers moderate to high deposition rates ranging from 2-12 pounds per hour. This process uses a continuously fed wire electrode and shielding gas.
The deposition rate in MIG welding depends on:
- Wire diameter (larger = higher deposition)
- Wire feed speed
- Voltage settings
- Shielding gas composition
For typical production welding, you can expect:
Wire Size |
Typical Deposition Rate |
0.035" |
3-5 lbs/hr |
0.045" |
5-8 lbs/hr |
0.052" |
7-12 lbs/hr |
MIG welding works well for medium-thickness materials. Its continuous wire feed allows for less stopping and starting compared to stick welding.
Flux-Cored Wire Deposition Advantages
FCAW (Flux-Cored Arc Welding) provides higher deposition rates than solid wire MIG, typically between 5-15 pounds per hour. The flux inside the tubular wire allows for deeper penetration.
Key advantages of FCAW include:
- Better performance on thicker materials
- Excellent weldability in outdoor conditions
- Higher tolerance for contaminants on base metals
Self-shielded flux-cored wire works well in windy conditions. Dual-shield flux-cored wire (using additional gas shielding) offers the highest deposition rates in the FCAW family.
You can boost FCAW deposition by using larger diameter wires and higher current settings. Many fabrication shops prefer FCAW when speed matters more than appearance.
Stick Welding Deposition Limitations
Stick welding (SMAW or Shielded Metal Arc Welding) has relatively low deposition rates, usually between 0.4-5.5 pounds per hour. This process requires frequent electrode changes.
Factors limiting stick welding deposition:
- Electrode length (typically 14" or less)
- Duty cycle (time spent changing electrodes)
- Available amperage from welding machine
Stick welding actually deposits only about 65% of the electrode weight. The rest becomes slag or is lost as spatter.
Despite these limitations, stick welding remains valuable for repairs and field work.
You can maximize stick welding deposition by:
- Using larger diameter electrodes when possible
- Selecting high-efficiency electrode types
- Minimizing time spent changing electrodes
Submerged Arc Welding's High Deposition
SAW (Submerged Arc Welding) delivers the highest deposition rates among common welding processes, reaching 16-60 pounds per hour. The process buries the arc beneath granular flux, allowing extremely high current levels.
SAW systems can use:
- Single wire setups (3-16 lbs/hr)
- Twin wire configurations (up to 30 lbs/hr)
- Multiple wire arrangements (exceeding 60 lbs/hr)
The high deposition comes with limitations.
SAW typically works only in flat or horizontal positions. Equipment is bulky and not portable.
You'll find SAW in shipbuilding, pressure vessel manufacturing, and heavy equipment fabrication. The process provides deep penetration while maintaining excellent weld quality at high speeds.
Hot Wire TIG For Improved Deposition
Traditional GTAW/TIG welding has very low deposition rates (0.5-2 lbs/hr).
Hot Wire TIG solves this problem by preheating the filler wire electrically before it enters the weld pool.
This modification can increase TIG deposition rates by 3-5 times.
The system uses a secondary power source to heat the wire while maintaining the excellent control TIG offers.
Benefits of Hot Wire TIG include:
- Higher deposition while keeping TIG quality
- Less heat input to the base material
- Reduced distortion compared to other high-deposition methods
You'll see Hot Wire TIG in applications requiring high quality and faster speeds, like pipe fabrication and aerospace components. The process costs more than standard TIG but significantly improves productivity where precision matters.
Deposition Rate vs. Deposition Efficiency
When welding, knowing the difference between how fast metal is deposited and how much of your filler material actually becomes part of the weld is crucial for productivity and cost control.
Understanding The Critical Difference
Deposition rate is how much weld metal you can put down in a given time. It's usually measured in pounds per hour (lbs/hr). Think of it as your welding speed.
When you need to finish a big job quickly, you want a high deposition rate.
Deposition efficiency is different. It tells you what percentage of your filler metal actually ends up in the weld joint. The rest is lost to spatter, slag, or fumes.
For example, if you use 10 pounds of welding rod and 6.5 pounds ends up in your weld, your efficiency is 65%.
Higher efficiency means less waste and more value from your welding materials.
Efficiency Percentages By Process
Different welding processes have very different efficiency levels:
Welding Process |
Typical Efficiency |
GTAW (TIG) |
99% |
SAW |
99% |
GMAW (MIG) |
92-98% |
FCAW |
87% |
SMAW (Stick) |
65% |
TIG and submerged arc welding are the champions of efficiency, wasting almost no material. MIG welding with solid or metal-cored wire is also quite efficient, especially with the right shielding gas.
Stick welding has the lowest efficiency, with about 35% of your electrode not making it into the weld. This is mostly due to stub loss, slag coverage, and spatter.
Ways To Increase Deposition Rate

Improving deposition rate can significantly boost your welding productivity. The right equipment, materials, and techniques can help you lay down more weld metal in less time.
Equipment Upgrades For Higher Deposition
Switching to a higher-capacity power source can instantly increase your deposition rate. Modern inverter-based welders offer better control at higher amperage levels. This lets you push more wire without losing stability.
For MIG welding, consider upgrading to a machine with higher wire feed speeds. Some advanced units can deliver up to 800 inches per minute of wire. This translates directly to more pounds per hour of deposited metal.
Submerged arc welding (SAW) equipment provides some of the highest deposition rates.
SAW systems can achieve up to 40 pounds per hour with single wire setups. For even higher rates, look into:
- Tandem arc systems (multiple wires in one weld pool)
- Multi-wire feeders
- Twin-arc torches
Water-cooled systems also allow longer duty cycles at higher amperages.
Advanced Filler Metals And Consumables
Metal-cored wires offer deposition rates 30% higher than solid wires at the same amperage. They provide better arc stability and less spatter too.
Larger diameter filler metals deposit more material per pass. Moving from a 0.035" wire to a 0.045" wire can increase your deposition rate by 25-30%. For high production, consider these options:
- Flux-cored wires (4-15 pounds per hour)
- Large diameter SMAW electrodes (3-10 pounds per hour)
- SAW wires up to 5/32" (10-40 pounds per hour)
Special alloy formulations optimize conductivity. Some newer consumables contain elements that improve electrical conductivity and melting efficiency.
Hot-wire additions for TIG welding can boost deposition rates from 1-2 pounds per hour to 4-8 pounds per hour.
Technique Adjustments For Faster Deposition
Adjusting your welding technique can significantly increase deposition rates.
Try using a drag angle instead of a push angle when possible. This keeps more heat in the weld pool.
Reducing your travel speed sometimes allows higher wire feed rates. This creates a larger, more stable weld pool that can accept more filler material.
For stick welding, use a shorter arc length. This increases the electrode burn-off rate and puts more metal into the joint.
Position matters too.
Flat position welding typically allows 15-20% higher deposition rates than vertical or overhead positions. When possible, rotate parts to weld in the flat position.
Preheating the base metal can also help. Warmer base metal needs less energy from the arc to form a stable weld pool.
Pulsed And Waveform Technologies
Modern pulsed power sources alternate between high and low current levels. This creates a stable arc at higher average wire feed speeds. Pulsed MIG can boost deposition rates by 10-30% over conventional MIG.
Advanced waveform control technology optimizes the electrical characteristics of your arc. Some systems offer specialized programs for high-deposition welding. These maintain arc stability while pushing more wire through the contact tip.
Synergic welding systems automatically adjust parameters as you increase wire feed speed. This makes it easier to achieve maximum deposition rates without defects.
For thick materials, try:
-
Surface tension transfer (STT) for root passes
-
Rapid-X for fill passes
-
RapidArc or other high-speed programs for cap passes
These technologies can increase your kilograms per hour while maintaining weld quality.
Troubleshooting Deposition Rate Issues

When your welding projects face deposition challenges, knowing how to fix them quickly saves time and money. The right solutions will help you maintain weld quality while meeting production goals.
Solving Common Deposition Problems
Low deposition rates often result from incorrect parameter settings. Check your current and voltage levels first. If they're too low, gradually increase them while monitoring your weld quality.
Wire feed issues can seriously hurt your deposition rate. Look for:
- Kinked or damaged feed lines
- Worn drive rolls
- Improper tension settings
- Clogged contact tips
Electrode selection matters too.
Larger diameter electrodes typically deposit more material but may not work for all positions. Try rutile or basic flux-cored wires if you need higher deposition in vertical or overhead positions.
Environmental factors like wind can reduce your arc stability. Use shields or windbreaks in outdoor settings to protect your arc and improve deposition consistency.
Managing Quality At Higher Deposition Rates
Higher deposition rates can lead to quality problems if not managed properly. Watch for excessive spatter, which wastes filler material and reduces your effective deposition rate. Adjust your stick-out length and travel speed to find the sweet spot.
Overheating is a common issue with high deposition welding. You might need to:
- Use pulsed welding techniques
- Apply interpass cooling times
- Reduce overall heat input
Porosity problems often appear as you push for more speed. Make sure your shielding gas coverage is adequate by checking for:
- Proper flow rates (15-25 CFM typical)
- No drafts near the welding area
- Clean base materials
Slag inclusions become more likely at higher deposition rates. Slow down slightly if needed and use proper weaving techniques to allow slag to float to the surface.
Equipment Limitations And Solutions
Your welding machine has built-in limits. Standard machines may not handle high deposition demands. For serious production work, consider upgrading to:
- Inverter-based power sources with higher duty cycles
- Specialized high-deposition GMAW or FCAW equipment
- Synergic welding systems that automatically adjust parameters
Heat management becomes critical with higher deposition rates. Water-cooled guns help prevent equipment overheating during extended welding sessions.
Automated systems can boost your deposition capabilities. Semi-automatic options like oscillators or simple carriages cost less than robots but still improve consistency. They help maintain steady travel speeds even during long welds.
Your consumables might limit deposition too.
Standard contact tips wear faster under high-amperage conditions. Look for heavy-duty alternatives made from copper-chromium alloys that last longer in production environments.
Conclusion
Ready to supercharge your welding productivity? Mastering deposition rate is your ticket to faster projects and bigger profits!
By dialing in the perfect current settings, choosing the right electrodes, and refining your technique, you'll lay down more metal in less time—without cutting corners on quality. It's fascinating how processes vary—from stick welding's modest 65% efficiency to submerged arc's impressive 99%!
Finding your sweet spot means balancing speed with your project's unique demands. Once you've got deposition rate in your toolbox, you'll tackle jobs with newfound confidence and precision.
Curious about what your perfect welds should look like? Read our guide: What Do Good Welds Look Like: Characteristics of High-Quality Welding!
Frequently Asked Questions
What factors influence the deposition rate in various welding techniques?
Electrode or filler wire diameter greatly affects deposition rate. Larger diameters typically deposit more material per hour.
Current settings play a crucial role too.
Higher current typically means higher deposition rates, but may impact weld quality.
Travel speed, electrode type, and shielding gas choice also influence how much material you can deposit.
Some gases improve arc stability, allowing faster deposition.
The welder's skill level matters as well. Experienced welders maintain better arc time and positioning.
How do deposition rates differ between SMAW and GTAW?
SMAW (Stick Welding) generally offers moderate deposition rates between 2-5 pounds per hour. It's limited by electrode length and frequent changes.
GTAW (TIG Welding) provides lower deposition rates, typically 1-2 pounds per hour. This process focuses on precision rather than speed.
The difference exists because GTAW requires manual filler addition, while SMAW incorporates the filler in the electrode coating. This makes SMAW faster but less precise.
Which formulas are utilized to estimate welding deposition rates?
For wire-based processes, you can use this formula:
WDR = 13.1 × D² × FS × (EE/100)
WDR is the Weld Deposition Rate in pounds per hour D is the electrode diameter in inches FS is the feed speed in inches per minute EE is the electrode efficiency percentage
For stick welding, a simpler formula works:
Deposition Rate = Weight of electrode × Deposition efficiency × 60 ÷ Arc time in minutes
Deposition efficiency varies by electrode type, typically 60-70% for most stick electrodes.
In what ways do high deposition rate welding processes benefit industrial applications?
High deposition welding reduces labor costs by finishing jobs faster. This is vital for large projects like shipbuilding.
It lowers energy consumption per weld, saving on power costs in manufacturing settings.
Projects with tight deadlines benefit from faster completion times. This can prevent costly penalties for delays.
Heavy fabrication industries like construction and pipeline work save money with high deposition techniques like SAW or FCAW.
What determines the maximum deposition rate achievable in a given welding operation?
Power supply limitations set a ceiling on your maximum current, directly affecting deposition rate.
Industrial machines typically allow higher rates. Heat input restrictions based on material type matter too.
Some metals can't handle excessive heat without warping or property changes. Position limitations affect your maximum rate.
Overhead welding typically requires lower deposition rates than flat position welding.
Equipment capabilities play a role. Advanced power sources with pulse capabilities can achieve higher rates while maintaining quality.
Joint design also matters. Deep grooves require multiple passes, limiting effective deposition rates.