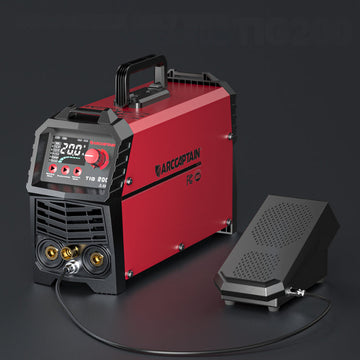
The decision between an inverter vs transformer welder can make or break your welding projects, affecting everything from your weld quality to your power bill.
As technologies evolve, many welders find themselves wondering if the extra cost of inverter models truly delivers better results or if traditional transformer units still offer the best value. What if the option that costs more upfront actually saves you thousands in the long run?
In this guide, we're cutting through the confusion to reveal which welder type delivers the best performance for your specific needs. We'll examine real-world power outputs, energy consumption differences, and the hidden costs most manufacturers don't advertise.
Understanding these crucial differences will help you avoid an expensive mistake and find the perfect welding partner for your projects.
After comparing options, browse our energy-efficient inverter welders that deliver the precision and portability advantages highlighted above.
Inverter vs Transformer Welder: Definitions and Comparison
When choosing between transformer and inverter welders, you can look at their differences in technology, weight, efficiency, and reliability. This section will explore how transformer welders use proven mechanical methods, while inverter welders bring modern innovations to welding technology.
Transformer Welders: Reliable and Proven Technology

Let's examine transformer welders - the time-tested foundation of welding technology that many professionals still depend on today.
- Built for longevity - Transformer welders have been the industry standard for decades, known primarily for exceptional durability and reliability in demanding environments
- Simple, effective design - These units use wire coils to step down voltage while increasing current, creating the ideal electrical conditions for strong welds
- Industrial-grade construction - The substantial weight comes from robust internal components designed to withstand continuous heavy-duty operation
- Low maintenance requirements - With fewer electronic components, transformer welders offer straightforward maintenance and often allow for DIY repairs without specialized knowledge
- Power stability advantages - These machines handle inconsistent power supplies and voltage fluctuations well, making them ideal for rural locations or job sites with unreliable electricity
Now that we understand the traditional approach, let's examine how inverter technology has changed the welding landscape...
Inverter Welders: Modern Machines
As welding technology evolved, inverter welders have emerged, offering several distinct advantages over their traditional counterparts.
- Advanced technology design - Inverter welders represent newer innovation, using sophisticated electronic components to convert power with significantly improved efficiency
- Remarkable portability - These units weigh considerably less than transformer models, making them ideal for welders who need to transport equipment between job sites
- Superior control precision - They offer more extensive adjustment capabilities, allowing for finer control over welding parameters and more consistent results across different materials
- Energy cost savings - By converting electricity more efficiently, inverter welders can substantially reduce power consumption and lower your operational expenses over time
- Improved work environment - They typically operate with noticeably less noise, creating a more comfortable setting for extended welding sessions
With these technological advantages in mind, let's examine how these differences translate to real-world performance and value...
Inverter vs Transfomer Welder: Core Differences
The fundamental distinction between these welding technologies comes down to how they process and deliver electrical power to create your welds. Let's compare their key operational characteristics:
Feature |
Transformer Welders |
Inverter Welders |
Power Conversion Method |
Heavy magnetic coils and laminated cores |
Advanced electronic circuits and microprocessors |
Current Type |
Primarily AC output (some with rectifiers for DC) |
Efficient AC-to-DC conversion with precise control |
Power Requirements |
Often need 220V+ outlets; may require special wiring |
Many models operate on standard 110V household outlets |
Weld Quality Control |
Basic adjustments with mechanical components |
Digital precision controls with extensive parameter options Digital precision controls with extensive parameter options |
Duty Cycle |
Excellent for continuous heavy-duty operation |
Improved in newer models, but typically better for intermittent use |
Power Characteristics: How Each Technology Delivers Welding Performance
The electrical power dynamics of your welder directly impact weld quality, versatility, and operational efficiency across different environments and applications.
Inverter Welder Power Performance
- Superior electrical efficiency - Inverters convert AC to DC power with remarkable precision, delivering up to 85-90% efficiency compared to transformers
- Exceptional arc stability - These units provide consistent, smooth arcs ideal for TIG and MIG welding where minor fluctuations can compromise weld quality
- Responsive power adjustment - Advanced electronics allow for microsecond adaptations to power output, virtually eliminating arc flickering during operation
- Voltage fluctuation tolerance - Many inverter models include built-in compensation for input voltage variations, maintaining stable output even with inconsistent power supplies
- Dual AC/DC capability - Integrated rectifiers allow flexible operation across both current types, expanding the range of materials and applications you can work with
Transformer Welder Power Performance
- Robust power delivery - Transformer technology provides reliable, consistent power output well-suited for demanding industrial environments
- Lower electrical efficiency - These units typically convert power at 60-70% efficiency, resulting in higher electricity consumption for equivalent output
- Stable arc in basic applications - While less precise, transformer welders deliver dependable performance for straightforward welding tasks without requiring complex adjustments
- Power supply sensitivity - Performance may be affected by voltage fluctuations, making them better suited for environments with consistent, reliable power
- Heavy-duty application advantage - Their simple, durable design excels in continuous operation scenarios where ruggedness outweighs precision requirements
The ideal choice depends heavily on your specific application requirements, with inverters generally preferred for precision work and transformers often better suited for heavy-duty industrial applications.
For those heavy-duty applications where transformer welders traditionally excel, our powerful 220V models provide the robust performance required for serious fabrication.
Efficiency Considerations: Maximizing Performance and Minimizing Waste
The efficiency profile of your welder affects not just power consumption but also productivity, mobility, and overall operational costs - making it a crucial factor in equipment selection.
Inverter Welder Efficiency

- Superior energy conversion - Inverters typically utilize 80-90% of input power for welding output, minimizing wasted electricity and reducing utility costs
- Enhanced duty cycles - Modern inverter models often feature duty cycles of 60% or higher at maximum amperage, allowing longer continuous operation without cooldown periods
- Thermal management advantages - Advanced cooling systems and efficient electronics generate less heat during operation, reducing overheating risks
- Compact, lightweight design - Most inverter welders weigh 20-50 pounds, enabling single-person transport and use in confined spaces or elevated work areas
- Space optimization - Their reduced footprint (often 70% smaller than transformers) conserves valuable workshop space and improves workspace organization
Transformer Welder Efficiency
- Lower power utilization - Transformer technology typically converts only 60-70% of input power to welding output, resulting in higher energy consumption
- Limited duty cycles - Many transformer models operate at 20-40% duty cycles at maximum settings, requiring more frequent breaks during intensive welding sessions
- Heat generation challenges - Their design produces more heat during operation, potentially creating uncomfortable working conditions and increasing cooling needs
- Substantial weight considerations - Averaging 75-200+ pounds, transformer welders often require equipment or multiple people for transport and positioning
- Significant space requirements - Their larger footprint demands more permanent installation space, potentially limiting workshop layout flexibility
Understanding these efficiency factors helps explain why many professional shops are transitioning to inverter technology despite higher initial costs, while others maintain transformer welders for specific high-volume applications.
Value Analysis: Determining True Return on Investment
Beyond simple price comparisons, understanding the complete value proposition of each welder type requires examining initial costs against long-term benefits and operational considerations.
Inverter Welder Value Proposition
- Premium initial investment - Expect to pay $800-$3,000+ for quality inverter welders, representing a 30-50% higher upfront cost than comparable transformer models
- Operational cost savings - Their superior efficiency typically reduces power consumption by 20-30%, potentially saving hundreds of dollars annually for frequent users
- Application versatility advantage - Single inverter units often handle TIG, MIG, and stick welding with precision control, potentially replacing multiple specialized machines
- Portability value - Their lightweight design (typically under 50 pounds) enables multi-site use without additional transportation equipment or assistance
- Component vulnerability - Circuit boards and electronic components may require professional repair if damaged, potentially increasing maintenance costs
Transformer Welder Value Proposition
- Cost-effective acquisition - With prices typically ranging from $500-$2,000, transformer welders offer lower barrier to entry for beginners and budget-conscious buyers
- Exceptional longevity - These units frequently remain operational for 15-20+ years, sometimes outlasting multiple generations of inverter technology
- Simplified maintenance - Basic mechanical design allows for straightforward repairs, often manageable without specialized technicians or proprietary parts
- Robust construction - Built to withstand harsh environments and rough handling, transformer welders typically endure conditions that might damage inverter electronics
- Specialized application focus - While less versatile, they excel at specific high-amperage applications where their durability provides consistent performance
The optimal value choice depends heavily on your specific usage patterns - with high-volume or mobile operations typically benefiting more from inverter technology despite higher initial investment, while occasional users might find better value in transformer models.
Whether you choose inverter or transformer technology, our advanced GMAW machines offer exceptional control for professional-quality welds in any setting.
Conclusion on Inverter vs Transformer Welders
When selecting between inverter and transformer welders, your specific needs should guide your decision.
Inverter welders offer superior efficiency, precision, and portability at a premium price point, making them ideal for professionals requiring versatility across multiple job sites. Meanwhile, transformer welders continue to provide unmatched durability and straightforward reliability at a lower initial cost, perfectly serving stationary workshops with consistent heavy-duty requirements.
Consider your priorities carefully - frequent users will likely recoup the higher investment in inverter technology through energy savings and increased productivity, while occasional welders might find better value in the simpler transformer design. Whichever technology you choose, proper maintenance and usage will maximize your investment's lifespan.
For additional guidance on selecting the right manufacturer for your needs, check out our guide to Welder Brands: Which Manufacturers Deliver Quality and Value.
Frequently Asked Questions
Inverter and transformer welders have unique benefits and uses. Inverters are modern, efficient, and versatile, while transformers are durable and reliable. This section will help clear up common questions about these welding machines.
What is the difference between inverter and transformer welders?
Inverter welders use newer technology, making them lightweight and energy-efficient. Transformer welders are heavier and known for their durability. Inverters offer smoother arc starts, while transformers are preferred for their robustness and reliability.
Do inverter welders last?
Inverter welders are durable and often last for years when properly maintained. Their lifespan can be affected by factors like usage, quality of components, and care. They require more attention to dust and moisture to ensure longevity.
Why would a welding company choose to use an inverter type of welder?
A welding company might opt for inverter welders due to their portability and efficiency. These machines are lighter, easier to transport, and consume less power. They are also capable of maintaining a stable arc, which leads to precise welding outcomes.
What can I weld with an inverter welder?
You can weld a variety of materials, including steel, stainless steel, and aluminum with inverter welders. They are versatile and can handle different welding processes like Stick, TIG, and MIG, making them useful for many projects and materials.
Do inverter welders use less power?
Yes, inverter welders are designed to be energy-efficient. They convert power efficiently and tend to consume less electricity than transformer welders. This efficiency can lead to cost savings, especially over extended use or in large-scale operations.
What are the advantages disadvantages of transformer type welding machines?
Transformer welders are highly reliable and robust, making them ideal for heavy-duty applications. They usually have a lower upfront cost. However, they are heavier and use more power, which may increase operational costs and reduce portability.